Metode osiguranja kvalitete prema. Metode osiguranja kvalitete proizvoda se razlikuju Suvremene metode osiguranja kvalitete
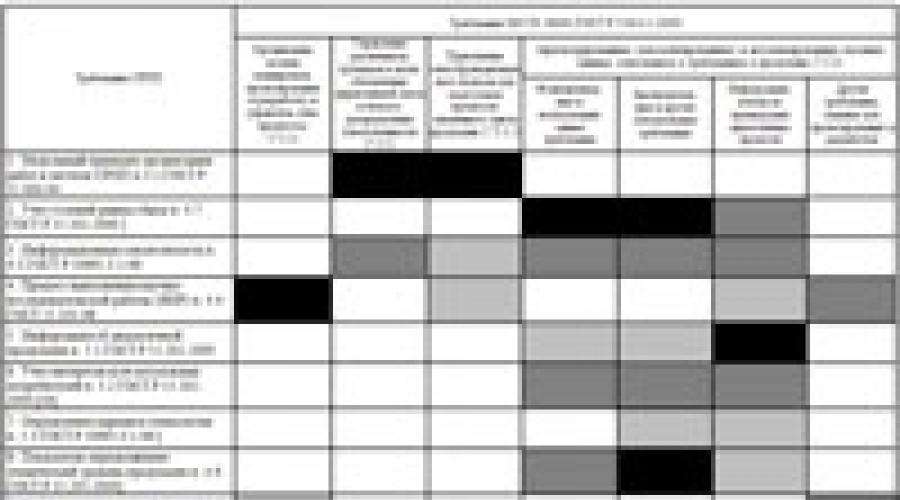
U poduzećima strojarstva posljednjih se godina sve više javlja potreba za stvaranjem sustava upravljanja koji ne odgovaraju temeljnom standardu ISO 9001, već se poboljšavaju (moderniziraju u skladu sa zahtjevima vremena i specifičnostima određene industrije) standardi za sustave upravljanja kvalitetom (na primjer, standardi Gazproma, Ruskih željeznica itd.). P.).
Iako je većina ruskih poduzeća već dugo uvela i uspješno upravlja sustavom za razvoj i puštanje proizvoda u proizvodnju (SRPP), koji zadovoljava nacionalne standarde Ruske Federacije, mnogi potrošači danas zahtijevaju od dobavljača implementaciju modernih sustava upravljanja kvalitetom usmjerenih na standarde koji uzeti u obzir specifičnosti industrije (na primjer, međunarodne norme ISO/TS 16949, AS 9100 i sl.).
Prilikom implementacije ovih standarda potrebno je duplicirati mnoge postupke koji već postoje i djeluju u poduzeću koji implementiraju zahtjeve SRPP standarda. Nema sumnje da to dovodi do dodatnih neracionalnih troškova svih vrsta resursa.
Zadatak smanjenja vremena, ljudskih i financijskih resursa za provedbu zahtjeva međunarodnih standarda za metode i postupke za osiguranje kvalitete korištenjem iskustava postojećih nacionalnih standarda Ruske Federacije danas je iznimno aktualan.
Unatoč naizgled očitim razlikama u specifičnostima građevinske proizvodnje u automobilskoj industriji i drugim granama strojarstva, zajednička je značajka raširenost opskrbe komponentama glavnim montažnim pogonima od strane relativno malih poduzeća.
Takvi principi organizacije proizvodnje dobro su razvijeni u gotovo svim automobilskim tvornicama bez iznimke (i domaćim i stranim), koriste se i za naftno i plinsko inženjerstvo - u pogonima koji proizvode složene tehnološke sustave: bušaće platforme, komplekse za razvoj pučinskih polja itd. Slični primjeri mogu se naći i u drugim industrijama.
Zbog činjenice da su automobili proizvod znatno šire masovne potražnje, upravo su u ovoj industriji proizvođači morali obratiti posebnu pozornost na stvaranje sustava upravljanja kvalitetom koji bi mogli odgovarati suvremenim principima organizacije proizvodnje i, štoviše, mogli bi istovremeno poboljšati proizvod. kvaliteta.. Osim toga, automobilska industrija je uspostavila vlastiti sustav industrijskih standarda kvalitete mnogo ranije nego što se potreba za tim pojavila u drugim područjima.
U tom kontekstu nedvojbeno je zanimljiv rad na području formiranja sustava upravljanja kvalitetom koji se trenutno provodi u automobilskim poduzećima. Više je nego vjerojatno da će se, uzimajući u obzir manje prilagodbe, rezultati postignuti na njima moći koristiti u bilo kojem strojogradnji.
Poznato je da kako bi potrošaču pokazali kako tvrtka prati kvalitetu svojih proizvoda i jamči tu kvalitetu, proizvođači kreiraju sustave upravljanja kvalitetom koji zadovoljavaju zahtjeve ISO 9001, ISO/TU 16949, primjenjuju tamo opisane metode.
U Rusiji je sada prisutan trend prelaska s nacionalnih standarda na međunarodni standard ISO / TU 16949, koji se primjenjuje na automobilsku industriju i organizacije koje proizvode odgovarajuće rezervne dijelove. Zbog činjenice da je ISO/TS 16949 objavljen u isto vrijeme kad i standard za sustave upravljanja kvalitetom, on ima mnogo zajedničkog s ovim potonjim, ali ima i svoje karakteristike, budući da je ISO/TS 16949 razvio Međunarodni Radna skupina za automobilsku industriju (IATF) i Japansko udruženje proizvođača automobila registrirani su kao korporacija (JAMA) uz potporu Tehničkog odbora ISO/TC 176 Upravljanje kvalitetom i osiguranje kvalitete.
Veliki proizvođači automobila već certificiraju ili planiraju certificirati svoje sustave upravljanja kvalitetom prema ISO/TU 16949 i zahtijevaju od svojih dobavljača da to učine. Na primjer, predstavnici "velike trojke" - DaimlerChrysler, General Motors, Ford postavili su takve zahtjeve svojim dobavljačima.
Treba napomenuti da implementacija standarda ISO / TS 16949 zahtijeva korištenje posebnih metoda organizacije rada - APQP (Advanced Product Quality Planning and Control Plan - Napredno planiranje kvalitete proizvoda i razvoj plana upravljanja), PPAP (Production Part Approval Proces - Proces za koordinaciju proizvodnje dijela, tj. odobravanje proizvodnje automobilskih komponenti), kao i korištenje nekih alata za osiguranje kvalitete proizvoda pomoću statističkih metoda analize - FMEA (Metoda za mogući način kvara i analiza učinaka - Metoda za analizu vrsta i posljedica potencijalnih nedostataka), MSA (Analiza mjernih sustava - Analiza mjernih sustava), SPC (Metode statističke kontrole procesa - Metode statističke kontrole procesa) i QSA (Analiza sustava kvalitete upravljanja - Procjena sustavi upravljanja kvalitetom).
Najozbiljnije poteškoće u domaćim poduzećima su uvođenje APQP (Advanced Product Quality Planning) metode organizacije rada, odnosno procesa planiranja, razvoja i pripreme proizvodnje automobilskih komponenti, što omogućuje ispunjavanje apsolutno svih zahtjeva. i očekivanja potrošača već u predproizvodnoj fazi, kada postoje osnovne mogućnosti Prevencija nedostataka.Poteškoće nastaju zbog činjenice da ovaj proces zahvaća gotovo sve odjele i sve procese u organizaciji i mora se implementirati u svim fazama životni ciklus proizvoda - od planiranja stvaranja, dizajna i razvoja automobilske komponente do njezine masovne proizvodnje.
U Rusiji postoji sustav sličan namjeni APQP - sustav za razvoj i stavljanje proizvoda u proizvodnju (SRPP).
Kao što znate, SRPP je skup međusobno povezanih temeljnih organizacijskih, metodoloških i općih tehničkih državnih standarda koji utvrđuju glavne odredbe, pravila i zahtjeve koji osiguravaju tehničko i organizacijsko jedinstvo posla koji se obavlja u fazama životnog ciklusa proizvoda (LCP) , uključujući istraživanje i opravdanje razvoja proizvoda ili projekta, zapravo razvoj, proizvodnju, rad (primjena, skladištenje) proizvoda i popravak (za popravljene proizvode), kao i interakciju dionika.
SRPP je međusobno povezan sa standardima drugih općih tehničkih sustava i skupova standarda: Jedinstveni sustav projektne dokumentacije (ESKD), Jedinstveni sustav tehnološke dokumentacije (ESTD), Jedinstveni sustav programske dokumentacije (ESPD), Državni sustav za Osiguravanje ujednačenosti mjerenja, Tehnološka podrška za izradu proizvoda.
Trenutno su mnogi stručnjaci poduzeća zabrinuti zbog sljedećeg problema - poduzeća su već implementirala i uspješno upravljaju sustavom za razvoj i puštanje proizvoda u proizvodnju u skladu s nacionalnim standardima Ruske Federacije. No dolazi vrijeme kada potrošač - određeni proizvođač automobila - zahtijeva od svog dobavljača implementaciju sustava upravljanja kvalitetom prema međunarodnoj normi ISO / TU 16949, uključujući, naravno, implementaciju APQP metode kao sastavnog dijela takve sustav upravljanja kvalitetom. Stručnjaci shvaćaju da moraju duplicirati mnoge od već provedenih procesa, što je popraćeno dodatnim neracionalnim troškovima.
O ovoj situaciji aktivno raspravljaju stručnjaci koji su se s njom susreli. Istina, stručnjaci u većini slučajeva govore samo o tome koliko su zanimljivi zahtjevi međunarodnih organizacija (međunarodna radna skupina za automobilsku industriju (IATF) i zahtjevi naših starih, dugo korištenih nacionalnih standarda, razvijenih još osamdesetih i devedesete godine prošlog stoljeća, poklapaju se.
Dakle, postoji problem - kako implementirati zahtjeve standarda ISO / TU 16949 uz najnižu cijenu, uključujući još uvijek egzotičnu metodu organizacije APQP rada za nas u poduzeću s implementiranim i uspješno funkcionirajućim SRPP-om.
Svrha našeg istraživanja bila je razviti algoritam za ovladavanje međunarodnim sustavima upravljanja kvalitetom u ruskim poduzećima, uzimajući u obzir specifičnosti akumuliranog prethodnog iskustva u funkcioniranju domaćih sustava i, istovremeno, optimizirajući troškove resursa različitih vrste: radni, financijski, vremenski itd.
Autor je analizirao stupanj usklađenosti zahtjeva norme ISO/TU 16949 i metode APQP sa zahtjevima nacionalnih SRPP normi. Za to su izgrađene matrice usklađenosti sa zahtjevima gornja dva sustava u kojima 45 redaka ispunjava zahtjeve SRPP-a, a po 49 stupaca ispunjava zahtjeve ISO/TU 16949 i APQP. Svaki element sjecišta redaka i stupaca dodatno je analiziran kombinacijom metoda stručne prosudbe i regresijske analize.
Za točnije razumijevanje koliki je bio stupanj generalizacije zahtjeva, kako su zahtjevi APQP metode razvrstani u grupe i koji su zahtjevi iz SRPP-a uzeti u obzir za njihovu kompatibilnost sa zahtjevima APQP procesa, razmotrimo mali dio matrice u većem obliku. Fragment matrice prikazan je u tablici 2.
Tablica 2 - Fragment matrice kompatibilnosti zahtjeva SRPP i ISO/TU 16949
Kao rezultat analize, otkriveno je da u nekim slučajevima postoji usklađenost (potpuna ili djelomična) zahtjeva ISO/TU 16949 i APQP sa zahtjevima SRPP-a i obrnuto. Stoga je nadalje provedena kvantitativna procjena stupnja kompatibilnosti zahtjeva ISO/TS 16949 i APQP metode, koja je pokazala da je potpuna podudarnost zahtjeva utvrđena u 15% slučajeva, a djelomična podudarnost zahtjeva. zahtjevi - u 13% slučajeva. Osim toga, identificirane su situacije kada zahtjevi mogu poslužiti kao temelj za implementaciju međunarodnih normi: skupina zahtjeva ISO / TU 16949 i APQP ne podudara se izravno sa zahtjevima SRPP-a, ali ako se potonji nekako dopune , tada će se dogoditi potpuna ili djelomična podudarnost . Takvih je situacija bilo oko 22%. Konačno, broj slučajeva s manjim podudaranjem je 12%, a nije pronađeno podudaranje u 38% slučajeva.
Na primjer, klauzula 5.2 GOST R 15.201-2000 kaže sljedeće: "Preporučuje se da projektni zadaci uzmu u obzir interese svih mogućih potrošača." Zauzvrat, u prvoj fazi APQP metode kao ulazne informacije potrebno je imati „informacije od određenih potrošača“. Tijekom istraživanja uočeno je da postoji potpuna podudarnost zahtjeva.
Drugi primjer: u odredbi 4.6 GOST R 15.201-2000 postoji zahtjev da programer proizvoda, kada provodi istraživanje, razvoj i tehnološki rad, treba obratiti posebnu pozornost na osiguranje, posebno zahtjeva za računovodstvenim pokazateljima proizvoda koji ga određuju tehnička razina. APQP proces odnosi se na mjerila za proizvode/procese konkurenata. U ovom slučaju je uočeno da je došlo do djelomičnog preklapanja zahtjeva. Slična je situacija s takvim zahtjevima kao što su obvezni tehnološki razvoj proizvoda u skladu s točkom 5.2.6 GOST R 50995.3.1-96 i potreba za "pretpostavkom o proizvodima i procesima" u skladu sa zahtjevima metode APQP .
Na temelju rezultata ovog rada može se izvesti sljedeći zaključak – primjenom ISO/TU 16949 i APQP metode organizacije rada u poduzećima s implementiranim i uspješno funkcionirajućim SRPP-om, troškovi resursa se mogu značajno smanjiti.
Smanjenje troškova može se postići činjenicom da one elemente kontrole predproizvodnog procesa koji su već implementirani u poduzeću u skladu sa zahtjevima SRPP standarda nije potrebno ponovno implementirati ako su predviđeni prilikom primjene. ISO / TS 16949 i APQP. Bit će dovoljno razjasniti razliku u terminologiji u dokumentaciji poduzeća. Svi smo svjesni da takav pristup može značajno uštedjeti i vrijeme za implementaciju ISO/TS 16949 i APQP metode te smanjiti ljudske i materijalne resurse potrebne za implementaciju.
Valja napomenuti da je provedena prilično površna analiza postojećeg stanja. Konkretno, zahtjevi standarda SRPP podijeljeni su u samo 45 skupina, zahtjevi ISO/TU 16949 i APQP metode - u 49 grupa, što vjerojatno nije dovoljno za potpunu procjenu kompatibilnosti zahtjeva ISO/TU 16949. i APQP sa zahtjevima standarda SRPP; Također treba napomenuti da je za ocjenu usklađenosti zahtjeva korištena ljestvica koja se sastoji od samo 5 kategorija, a koja također daje samo približnu ocjenu kompatibilnosti zahtjeva.
Također treba napomenuti da, ovisno o specifičnostima poduzeća i općem smjeru njegovih aktivnosti, postupak implementacije različitih zahtjeva kako standarda SRPP, tako i zahtjeva ISO / TU 16949 i APQP može biti različit. No, u isto vrijeme treba imati na umu da neki zahtjevi mogu biti međusobno povezani i tada postoji neporeciv red za njihovu provedbu. Ova se situacija mora uzeti u obzir u zajedničkoj provedbi standarda SRPP i ISO/TU 16949.
S obzirom na navedeno, razvijena je shema organizacije proizvodnje koju smo nazvali “organizacijski model” (slika 1.). Organizacijski model omogućuje vam da odredite slijed radnji u fazi projektiranja, razvoja i stavljanja proizvoda u proizvodnju iu proizvodnji proizvoda, identificirate i lokalizirate uska grla, poduzmete specifične radnje za njihovo uklanjanje, dodijelite odgovornost i ovlasti unutar obje jedinice. odgovoran za proizvodnju proizvoda i u cijeloj organizaciji.
Slika 1 - Organizacijski model "Upravljanje proizvodnjom i uslugama"
Razvijeni organizacijski model primjenjiv je na svako industrijsko poduzeće. Organizacijski model može se koristiti za određivanje redoslijeda implementacije i raspodjele poslova pri uvođenju suvremenih metoda upravljanja kvalitetom u strojograditeljskom poduzeću koje ima operativni sustav upravljanja temeljen na implementiranim standardima nacionalnog SRPP sustava.
Analiza također nije uzela u obzir faktor kao što su neke netočnosti i konvencije u prijevodu teksta koji opisuje APQP metodu. U takvoj situaciji može biti vrlo teško uzeti u obzir sinonime prilikom predstavljanja zahtjeva - uostalom, neki zahtjevi mogu se čak i potpuno poklapati, ali u isto vrijeme biti izrečeni potpuno različitim riječima.
Rezultati analize omogućuju razvoj specifičnog algoritma za implementaciju zahtjeva međunarodnih standarda, uzimajući u obzir SRPP sustav koji djeluje u poduzećima, što može značajno smanjiti vrijeme, ljudske i financijske resurse, a istovremeno koristiti ogromna prtljaga koju su nam ostavili naši prethodnici - sovjetski inženjeri - programeri nacionalnih standarda. Ovaj algoritam će biti opisan u sljedećoj publikaciji autora.
Natalia Viktorovna VASHCHENKO— voditelj Odjela za certifikaciju i organizaciju rada Koordinacijskog centra ANO "ATOMVOENSERT"
Popis korištenih izvora
1 Kudryashov A.V. Okrugli stol. APQP: problemi i iskustvo implementacije // Metode upravljanja kvalitetom. - 2012. - Broj 6.
2 Kershenbaum V.Ya., Vashchenko N.V. Metodologija procjene usklađenosti regulatornih zahtjeva domaće i strane prakse u izgradnji sustava upravljanja kvalitetom // Upravljanje kvalitetom u naftno-plinskom kompleksu. - 2013. - Broj 1. - Sa. 17 - 21 (prikaz, stručni).
3 Vashchenko N.V. O izvedivosti dokumentiranog postupka u okviru provedbe zahtjeva sedmog odjeljka ISO 9001:2008 // Upravljanje kvalitetom u naftnom i plinskom kompleksu. - 2013. - Broj 2. - Sa. 14 - 18 (prikaz, stručni).
Brojni statistički podaci o kvaliteti pokazuju da je nedostatak proizvoda u otprilike 85-90% uzrokovan ljudskim faktorom. Razmotrimo koji razlozi vezani uz radnika mogu utjecati na nepoštivanje tehničke dokumentacije, sve do braka proizvoda. Među njima se može primijetiti: niska kvalifikacija, kratko radno iskustvo, loše zdravlje, nepažnja pri čitanju crteža, tehnologija ili uputa, loša priprema radnog mjesta.
Treba naglasiti da se uzroci braka mogu povezati ne samo s osobom, već i s alatom, tehnološkom opremom, opremom. To je točno, ali najčešće se to događa ne toliko zbog nedostataka samog alata, opreme ili opreme, koliko zbog njihovog nepažljivog oštrenja, loših popravaka ili netočne izrade i montaže koju obavljaju radnici. Ako "kopate" do krivca kvara, onda će to u velikoj većini biti osoba koja ne radi nužno u vašem poduzeću, ali i, eventualno, u poduzeću dobavljača.
Gdje treba započeti poboljšanje kvalitete? Japanski stručnjaci savjetuju početi s kvalitetom na radnom mjestu. Štoviše, razvili su koherentan sustav poboljšanja kvalitete na radnom mjestu, koji su nazvali "5S" ("Good Housekeeping Practices"). Ime dolazi od pet japanskih riječi koje počinju slovom "C": "seiri" (razvrstavanje), "seiso" (čišćenje), "seiton" (organizacija), "seiketsu" (standardizacija), "shitsuke" (samopregled ). Ruski prijevod ovih riječi daje, ako ne sasvim jasnu, onda sasvim dovoljnu ideju o približnom sadržaju mjera za poboljšanje kvalitete na radnom mjestu. Ako ukratko okarakteriziramo ovaj sustav, možemo reći da “prije početka rada, pa čak i odgovornog rada, morate shvatiti red na svom radnom mjestu”.
Navedimo jasniji sadržaj svake od faza "5S" sustava. Prije nego što se pristupi njegovoj provedbi, potrebno je detaljno opisati, te po mogućnosti fotografirati radno područje (ili radno mjesto) koje je potrebno preurediti. Usporedba opisa radnih područja (mjesta) prije i nakon transformacije može menadžmentu ostaviti povoljan dojam koji aktivira kvalitetan rad u poduzeću.
Faza 1. Razvrstavanje. Stavite stvari (ili predmete) koje se svakodnevno koriste na jedno mjesto. Predmete koji se koriste jednom tjedno treba staviti na drugo mjesto, mjesečno - na treće, a ono što je potrebno vrlo rijetko - na četvrto. Učinite ovaj postupak za svaku zonu radnog mjesta. Zatim sa svake skladišne lokacije odaberite i ostavite po jedan primjerak svake vrste artikla, a ostatak prebacite u ormar za pohranu rezervnih dijelova.
Faza 2. Čišćenje. Očistite sve radne površine prije ponovnog stavljanja bilo čega na njih. Pobrinite se da u blizini radnog mjesta postoje odgovarajući spremnici za otpad. Sve rezervne dijelove smjestite u opće skladište. Napravite popis artikala vraćenih u skladište kako biste ih mogli prijaviti upravi trgovine. Organizirajte i stavite na jedno mjesto sve potrebne dokumente i očistite sav alat. Uspostaviti standarde (norme) čistoće koje svaki zaposlenik mora poštivati.
Faza 3. Organizacija. Uredno organizirajte sve papire i mape. Predmeti koji se svakodnevno koriste trebaju biti na dohvat ruke radnika. Predmeti koji se koriste jednom tjedno mogu se postaviti na udaljenosti od jednog koraka, a oni koji se koriste jednom mjesečno - na udaljenosti od 2-3 koraka. Sve ostalo može se nalaziti unutar nekoliko koraka od radnog mjesta. Potrebno je jasno definirati mjesto svake stavke.
Faza 4. Standardizacija. Upoznati sve zaposlenike povezane s ovim radnim mjestom sa standardima čistoće i objaviti fotografije s "ispravnim" standardnim okruženjem. Gdje je potrebno, osigurajte opremu i alate s prozirnim poklopcima otpornim na prašinu. Ako su takvi poklopci neprozirni, radnici će vjerojatno ispod njih pohraniti predmete koji nisu povezani s radnim mjestom.
Faza 5. Samotestiranje. Nakon otprilike mjesec dana pažljivo pregledajte stanje radnog mjesta kako biste ga poboljšali. Ako ima dodatnih artikala - pošaljite ih u opće skladište. Pregledajte standarde čistoće i po potrebi ih revidirajte. Ponovite ovaj korak nakon mjesec dana.
Također možete preporučiti dodatne mjere za održavanje reda na radnom mjestu. Tako, na primjer, možete izraditi pokretne ploče s alatima za određene poslove ili nacrtati obrise alata na pločama tako da odmah bude jasno koji alat nedostaje.
Japanski istraživači vjeruju da ako menadžeri tvrtke ne mogu implementirati "5S", onda ne mogu učinkovito upravljati. Suprotno tome, ako možete svladati ovaj sustav, to znači da jednako uspješno možete implementirati i druge, složenije sustave. Razlog za ovakav zaključak je da 5S sustav ne zahtijeva nikakav poseban menadžerski kadar za njegovu implementaciju i neće postati učinkovit sve dok se u njega ne uključe svi zaposleni i ne počnu razmišljati o uspjehu ovog sustava. No, ako je sustav 5S već implementiran, onda možemo pretpostaviti da su ostali sustavi gotovo napola asimilirani (u smislu spremnosti osoblja za provedbu promjena).
Od sredine 80-ih. 20. stoljeće u japanskim tvrtkama, sustav 5S bio je središnji za razmišljanje i filozofiju upravljanja. Uprava poduzeća posvuda je došla do zaključka da je ovaj sustav ključna metoda upravljanja u bilo kojem, pa i najvisokotehnološkom području djelatnosti.
Sustav 5S posljednjih je godina stekao veliku popularnost u ruskim poduzećima. Iz domaće prakse implementacije ovog sustava mogu se izvući sljedeći zaključci:
- - primjenjiv je i može se uspješno implementirati u domaćim poduzećima iu organizacijama različitih oblika vlasništva s interesom menadžmenta u tome;
- - sadržaj principa sustava i tehnologija njegove provedbe zahtijevaju značajnu prilagodbu osobitostima domaćeg gospodarstva, metodama organiziranja proizvodnje i mentalitetu osoblja;
- - mogućnost uspješne implementacije sustava izravno ovisi o socio-ekonomskim uvjetima rada na radnom mjestu, t.j. razina i redovitost isplate plaća, sustavno i ritmično opterećenje proizvodnje, poštivanje od strane administracije barem osnovnih zahtjeva za sigurne radne uvjete.
Pokušava se modernizirati ovaj sustav, uzimajući u obzir načela znanstvene organizacije rada i praksu poboljšanja kvalitete. Novi sustav, koji je apsorbirao elemente sustava "5S" i prilagodio se uvjetima domaće proizvodnje, nazvan je "Naručivanje" (tablica 2.4). Glavni principi ovog sustava su sljedeći:
- - ukloniti sve nepotrebno;
- - redovito provoditi temeljito čišćenje i provjeru ispravnosti opreme i inventara;
- - sve postavite na radno mjesto na najprikladniji način;
- - izraditi standarde (pravila) za skladištenje, korištenje, čišćenje i inspekciju;
- - stalno i svjesno slijediti prihvaćena pravila.
Tablica 2.4
Usporedba principa sustava "5S" i "Naručivanje".
1. Sudjelovanje cijelog tima. Kao što je nemoguće “zakuhati vodu u jednom kutu bazena”, tako se ovaj sustav ne može učinkovito implementirati na jednom radnom mjestu ili u jednoj jedinici voljom jedne osobe. Novi sustav zahtijeva odlučnost i koherentnost djelovanja cijelog tima.
Svako pravilo sustava koje treba izvršiti nije samo po sebi teško. Poteškoća je u tome da se ne zaustavi njegova provedba. To zahtijeva upornost i suradnju, što zauzvrat stvara osjećaj pripadnosti timu i poboljšava korporativnu klimu.
2. Lakoća razvoja - prividna. Principi sustava "Naručivanje" na prvi pogled izgledaju tako jasni i jednostavni za implementaciju. Ali zašto ih je tako teško implementirati?
Očigledna lakoća provedbe ovih načela posljedica je činjenice da zaposlenici ne razumiju u potpunosti što je sustav "Naručivanje". Ovo nije jednokratno generalno čišćenje, ne premještanje alata s jednog mjesta na drugo, već temeljno novi stil odnosa prema radnom okruženju, njegovoj organizaciji i sigurnosti, stilu stalnog održavanja visoko organiziranog, čistog radnog prostora.
3. Od korekcije do prevencije.Često možete vidjeti koliko vremena menadžeri provode ispravljajući ono što je učinjeno pogrešno ili izvan vremena. Na nedaće reagiraju naknadno. No, kada se upoznamo s problemima, postaje jasno da su uzroci mnogih od njih često vrlo jednostavne stvari.
Pravovremeno uočeni prekršaji u radu opreme, utvrđeni kvarovi opreme ili inventara mogu spriječiti velike gubitke i nesreće. Čak i neke "sitnice" pod nepovoljnim spletom okolnosti mogu donijeti velike nevolje.
- 4. Od upravljanja temeljenog na rezultatima - za kontrolu procesa. Menadžeri su vrlo često skloni vidjeti samo rezultate aktivnosti i procijeniti učinkovitost svog rada. Pri implementaciji sustava "Naručivanje" potrebno je naučiti vidjeti razloge koji dovode do određenih rezultata, sagledati cijeli proces u cjelini, njegove prednosti i slabosti.
- 5. Naglasak na ispunjavanju elementarnih zahtjeva. Osoblje se mora naviknuti na stalno ispunjavanje elementarnih zahtjeva. Na primjer, provjera prisutnosti svih natpisa i oznaka na važnim predmetima ili objektima.
- 6. Jačanje odgovornosti svakog zaposlenika za rezultate svoga rada. G. Ford je jednom rekao da "čak i najgluplji radnik može pronaći stotinu načina da prevari najvještijeg majstora". To potvrđuje da samo faktor osobne odgovornosti radnika i njegov interes za rad može imati veliku pozitivnu ulogu u proizvodnji, a ne stalno reguliranje rada i stroga kontrola. Trebamo atmosferu u kojoj ljudi pomažu jedni drugima i svi se trude raditi dobar posao.
- 7. Razumijevanje uputa i praćenje njihovih zahtjeva. Vrlo često se upute i zahtjevi ne poštuju, ne zato što ih zaposlenici zanemaruju, već zato što ili ne znaju ili ne razumiju u potpunosti bit zahtjeva ili preporuka sadržanih u njima.
Sustav naručivanja omogućuje zaposlenicima da samostalno razvijaju specifična pravila i upute u odnosu na svoja radna mjesta.
8. Postupni (korak po korak) pristup. Očito je da se sustav "Naručivanje", koji je prvenstveno usmjeren na promjenu stereotipa ponašanja zaposlenika, ne može implementirati brzo i odmah nakon početka implementacije donijeti opipljive rezultate. Novi sustav prvi je korak prema dugoročnom programu oporavka poduzeća.
Tehnologija implementacije sustava uključuje metodično, postupno, postupno svladavanje njegovih principa, evaluaciju i konsolidaciju rezultata svakog koraka.
9. Sustav "Naručivanje» - to je težak put. Novi sustav, poput japanskog "5S", funkcionira po principu: "Djela govore više od riječi". Svaki veliki posao počinje malim djelom, postupnim razumijevanjem suštine problema, greškama i ispravcima. Nikada ne smijete odbiti pomoć, savjet, podršku kolega i inženjerskog osoblja. Stvarni napredak u postupnim, čak i malim koracima, puno je korisniji od globalnih rasprava o velikom projektu koji može promijeniti strukturu proizvodnje na danom radnom mjestu.
Gore navedeni metodološki pristupi ne samo da otkrivaju sadržaj i tehnologiju implementacije principa "Naručivanje" sustava, već objašnjavaju prepreke, poteškoće i poteškoće koje će naići na putu implementacije i ovog sustava i "5S" sustava. .
Ako je japanskom zaposleniku sasvim dovoljno biti siguran menadžmentu tvrtke da će uvođenje “5S” sustava donijeti velike koristi ne samo kompaniji, već i samom zaposleniku, kako bi se dugoročna motivacija nosila da implementira elemente ovog sustava u praksi, onda to očito nije dovoljno za zaposlenika ruskog poduzeća. Potrebni su učinkoviti mehanizmi koji bi potaknuli unapređenje radnih mjesta i poboljšanje kvalitete proizvoda i rada na svakom radnom mjestu. Kao i uvijek, u ruskim poduzećima sve što se tiče poboljšanja, racionalizacije, uključujući i radna mjesta, praktički se ne temelji na sustavu, ne na učinkovitim poticajima, već isključivo na osobnoj inicijativi. Tako ozbiljna stvar kao što je uvođenje sustava "5S" ili "Naručivanje" ne može se "brbljati" samo tvorničkim entuzijastima.
Postoji mišljenje da kada bi se sav posao mogao obaviti "hitno", onda Rusija ovdje ne bi imala konkurenciju, dok posao povezan s svakodnevnim mukotrpnim radom na uspostavljanju reda i čistoće ne odgovara našem mentalitetu. Otuda i potreba za opširnim objašnjenjem, koristeći metodološke pristupe, kako izvesti u biti prilično jednostavan posao, što je načelo sustava "Naručivanje".
Ako želimo živjeti civilizirano, kao na primjer u Japanu ili Europi, onda novi menadžeri moraju uvjeriti radnike da kvaliteta rada ne ovisi o mentalitetu nacije, već o sposobnosti i želji da se udovoljava svim zahtjevima zabilježenim kako u tehničkim specifikacijama za proizvode tako iu međunarodnim normama ISO 9000. I ne samo da inspirira, već i organizacijski i financijski osigurava provedbu potrebnih standarda.
Kao rezultat proučavanja gradiva iz ovog poglavlja, student bi trebao:
znati
- sedam alata za kontrolu kvalitete proizvoda;
- statističke metode kontrole kvalitete proizvoda;
- funkcionalna analiza troškova;
- suvremene tehnologije upravljanja kvalitetom (koncept šest sigma, QFD metoda itd.);
biti u mogućnosti
- izgraditi kauzalni Ishikawa dijagram i Pareto dijagram kako bi se upravljalo kvalitetom robe i usluga;
- primijeniti QFD metodu kako bi se pratili zahtjevi potrošača u svim fazama životnog ciklusa proizvoda;
- primijeniti funkcionalnu analizu troškova kako bi se postigla potrebna potrošačka svojstva robe (usluga) uz minimalne troškove za njihovo pružanje;
vlastiti
- vještine primjene sedam alata za kontrolu kvalitete robe koja ulazi u promet;
- statističke metode upravljanja kvalitetom robe koja ulazi u promet.
Značenje i klasifikacija metoda
Kao što je gore navedeno, u pogl. 2, jedno od načela SM K je da temelj za donošenje odluke trebaju biti samo činjenice, a ne intuicija. Jedan od razloga za pogreške u upravljanju kvalitetom je to što se činjenice brkaju sa subjektivnim prosudbama. Kako bi se spriječile pogreške, potrebno je organizirati proces traženja činjenica, t.j. statistički materijal.
Problemima prikupljanja, obrade i analize rezultata bavi se matematička statistika koja uključuje veliki broj različitih metoda. Japanski znanstvenici (prvenstveno profesor K. Ishikawa) birali su iz ovog skupa sedam osnovnih alata za kontrolu kvalitete(slika 4.1). Krugovi kvalitete odigrali su važnu ulogu u razvoju statističkih metoda u Japanu.
Riža. 4.1.
S rastom obujma proizvodnje u serijskoj i masovnoj proizvodnji proizvoda, potrošaču (kao pravnoj osobi) i samom proizvođaču bili su potrebni podaci o stvarnoj kvaliteti proizvedenih i kupljenih proizvoda. Međutim, zbog velikog volumena proizvedenih serija proizvoda, potpunu kontrolu kvalitete bilo je teško izvesti, a pouzdanost niska. Kako bi se smanjio intenzitet rada i povećala pouzdanost, počeli su se primjenjivati statističke metode selektivne kontrole kvalitete. Njihovo značenje je krajnje jednostavno: proučavanjem malog dijela proizvoda (uzorka), moguće je izvući pouzdane zaključke o kvaliteti cijele serije.
Krajem 1970-ih i početkom 1980-ih. Unija japanskih znanstvenika i inženjera razvila je sofisticiraniji skup alata za kontrolu kvalitete. Ti su se alati temeljili i na metodama matematičke statistike i na metodama drugih znanosti: operativnoj analizi, teoriji optimizacije itd. Kao suptilniji alati, bili su upućeni inženjerskom osoblju. Ove metode se nazivaju alati za upravljanje kvalitetom. Ovaj vodič pokriva neke od alata za upravljanje kvalitetom: „Šest sita“, tehnologija implementacije funkcije kvalitete, analiza troškova.
U nastavku su opisane tri grupe metoda:
- 1) osnovni alati za kontrolu kvalitete;
- 2) statističke metode selektivne kontrole kvalitete;
- 3) alati za upravljanje kvalitetom.
Osnovni alati za kontrolu kvalitete
Glavni alati kontrole kvalitete su metode statističke analize uvjeta i čimbenika koji utječu na kvalitetu proizvoda. Statistička analiza uključuje analizu vrsta i uzroka braka, analizu utjecaja pojedinih čimbenika tehnološkog procesa na pokazatelje kvalitete. Prilikom analize preporuča se korištenje posebnih grafičkih metoda (ponekad nazvanih deskriptivna statistika) za vizualizaciju kvalitetnih podataka. Ove metode uključuju sedam alata za kontrolu kvalitete (vidi sliku 4.1).
Kontrolni list (list)- alat za prikupljanje i organiziranje podataka kako bi se olakšalo daljnje korištenje prikupljenih informacija.
Na sl. 4.1, kontrolni list nije slučajno smješten u sredini, okružen s ostalih 6 alata. Ona ima posebnu ulogu, jer provedba bilo kojeg zadatka analize kvalitete počinje prikupljanjem početnih podataka.
Kontrolni list - papirnati obrazac na kojem su prethodno ispisane kontrolirane vrste nedostataka (u našem slučaju, na primjeru nedostataka u dekoraciji keramičkih proizvoda), koji u obliku jednostavnih simbola označavaju učestalost njihova pojavljivanja.
Broj različitih letaka u poduzeću se kreće stotinama, a za svaku konkretnu namjenu, zapravo, može se izraditi vlastiti letak. Ali princip njihovog dizajna ostaje nepromijenjen: oblik lista trebao bi biti jednostavan i razumljiv (bez dodatnih objašnjenja); potrebno je naznačiti tko je, u kojoj fazi i koliko dugo prikupljao podatke.
Očito, kvaliteta proizvoda je glavni pokazatelj aktivnosti svakog poduzeća. Kako bi se održala konkurentnost roba i usluga, razvoj sustava upravljanja sigurnošću hrane danas se koristi raznim, uglavnom ekonomskim i matematičkim. Na primjer, dinamičko, linearno i nelinearno programiranje, simulacijsko modeliranje, dizajn eksperimenta, teorija čekanja i igara, analiza funkcionalnih troškova, Taguchi metoda i metoda strukturiranja kvalitete.
Ostavite zahtjev za besplatno savjetovanje
Metoda implementacije funkcije kvalitete - QFD (Quality Function Deployment). To je sustavni pristup identificiranju zahtjeva kupaca koji pomaže poduzeću razumjeti i integrirati otkrivanje zahtjeva u specifične planove isporuke usluga. Za razliku od ostalih metoda, QFD je metoda osiguranja kvalitete koja uključuje zadovoljavanje potreba korisnika u izgradnji kovrčavih matrica, kasnije nazvanih "kuće kvalitete", unutar kojih se bilježe podaci o kvaliteti usluge i donesenim odlukama. Ova metoda je tehnologija za dizajniranje proizvoda i procesa koja vam omogućuje pretvaranje želja potrošača u tehničke zahtjeve za proizvode i parametre njihovih proizvodnih procesa. QFD metoda je ekspertna metoda koja koristi tablični način prikaza podataka, a sa specifičnim oblikom tablica, koje se nazivaju "kuće kvalitete". Glavna ideja QFD tehnologije je shvaćanje da postoji velika razlika između potrošačkih svojstava ("stvarnih pokazatelja kvalitete") i parametara proizvoda utvrđenih u standardima ("pomoćni pokazatelji kvalitete"). Pomoćni pokazatelji kvalitete važni su za proizvođača, ali nisu uvijek bitni za potrošača. Idealan slučaj bi bio kada bi proizvođač mogao kontrolirati kvalitetu proizvoda izravno iz stvarnih pokazatelja, ali to obično nije moguće, pa koristi pomoćne indikatore.
QFD tehnologija je slijed radnji proizvođača za pretvaranje stvarnih pokazatelja kvalitete proizvoda u tehničke zahtjeve za proizvode, procese i opremu. Glavni alat QFD tehnologije je stol posebne vrste, nazvan "kuća kvalitete". Ova tablica prikazuje odnos između stvarnih pokazatelja kvalitete (potrošačka svojstva) i pomoćnih pokazatelja (tehnički zahtjevi):
Primjena QFD metode omogućuje uvažavanje zahtjeva potrošača u svim fazama proizvodnje gotovih proizvoda, za sve elemente sustava kvalitete organizacije i na taj način povećava stupanj zadovoljstva kupaca, smanjuje troškove. procesa projektiranja i pripreme proizvoda za proizvodnju.
FSA metoda je tehnologija analize troškova kako bi proizvod obavljao svoje funkcije; FSA se provodi za postojeće proizvode i procese kako bi se smanjili troškovi, kao i za proizvode u razvoju kako bi se smanjila njihova cijena. FSA metoda se aktivno koristi u industriji od 1960-ih, prvenstveno u SAD-u. Njegova uporaba omogućila je smanjenje troškova mnogih vrsta proizvoda bez smanjenja njihove kvalitete i optimizaciju troškova proizvodnje. Sada je FSA jedna od najpopularnijih vrsta analiza proizvoda i procesa. FSA je jedna od metoda funkcionalne analize tehničkih objekata i sustava, u istu skupinu metoda spadaju FFA (funkcionalna fizička analiza) i FMEA analiza. Prilikom provođenja funkcionalne troškovne analize utvrđuju se funkcije elemenata tehničkog objekta ili sustava i procjenjuju troškovi provedbe tih funkcija kako bi se ti troškovi smanjili. Provođenje FSA uključuje sljedeće glavne faze:
1. Dosljedna konstrukcija modela FSA objekta (komponentni, strukturni, funkcionalni); modeli se obično grade u tabličnom (matričnom) obliku; 2. Proučavanje modela i izrada prijedloga za poboljšanje objekta analize.
Ishikawa dijagram(uzročno-posljedični dijagram, "riblja kost") - kvalitetan alat koji služi za vizualizaciju uzročno-posljedičnih veza između objekta analize i čimbenika koji na njega utječu.
Faktor utjecaja ili problem nalazi se, kao što je prikazano, na kraju vodoravne strelice; mogući uzroci bit će prikazani kao označene strelice koje su uključene u strelicu glavnog uzroka. Svaka strelica također može imati druge strelice koje prikazuju glavne uzroke ili čimbenike uključene u nju, čiji se prioritet smanjuje s udaljenosti od glavne strelice.

Pareto analiza- Može se koristiti za analizu ideja iz brainstorminga. Koristi se za identificiranje nekoliko vitalnih problema ili uzroka onih problema koji imaju najveći utjecaj. Pareto dijagram vizualno predstavlja podatke u obliku dijagrama izgrađenog silaznim redoslijedom učestalosti pojavljivanja elemenata. Općenito, Pareto grafikon pokazuje da je 80% utjecaja posljedica 20% uzroka, stoga se ponekad naziva pravilom 80/20.
Statistička kontrola procesa (SPC)- je skup alata za upravljanje procesima. Osim toga, to je i strateški alat za smanjenje varijabilnosti proizvoda, opskrbe materijalom, opremom, odnosima i procesima koji su uzrok većine problema s kvalitetom. SPCće pokazati je li proces "pod kontrolom" - t.j. je li stabilan samo sa slučajnim varijacijama, ili je "van kontrole" i treba mu obratiti pozornost. Štoviše, SPC automatski upozorava kada upravljivost opada i može pomoći u dugoročnom smanjenju stope kvarova, identificiranju posebnih uzroka, smanjenju ili eliminaciji uzroka varijacija i postizanju razine upravljivosti što bliže ciljnoj. U SPC-u brojke i informacije čine osnovu za donošenje odluka i djelovanje putem rigoroznog sustava za evidentiranje podataka. Osim alata potrebnih za bilježenje podataka, postoji i skup alata za analizu i interpretaciju podataka, od kojih su neki razmotreni na sljedećim stranicama. Razumijevanje alata i načina njihove uporabe ne zahtijeva prethodno poznavanje statistike.
Kontrolna kartica. Koristi se za praćenje kontroliranih procesa pomoću vrijednosti i raspona. Kontrolni grafikon je podatak kao što su prodaja, količina, pritužbe kupaca prikazani kronološkim redoslijedom i pokazuje kako se vrijednosti mijenjaju tijekom vremena. U kontrolnoj karti svaka točka odgovara pojedinačnoj vrijednosti. Iznad i ispod prosjeka prolaze gornja i donja linija upozorenja i akcije (UWL, LWL, UAL, LAL). Ove granice djeluju kao znakovi i pravila za odlučivanje i pružaju operaterima informacije o procesu i njegovom statusu kontrole. Karta je korisna kao povijesni zapis procesa, kako je napredovao i kao sredstvo za prepoznavanje i predviđanje promjena.