طرق ضمان الجودة للبرامج. تختلف طرق ضمان جودة المنتج عن طرق ضمان الجودة الحديثة
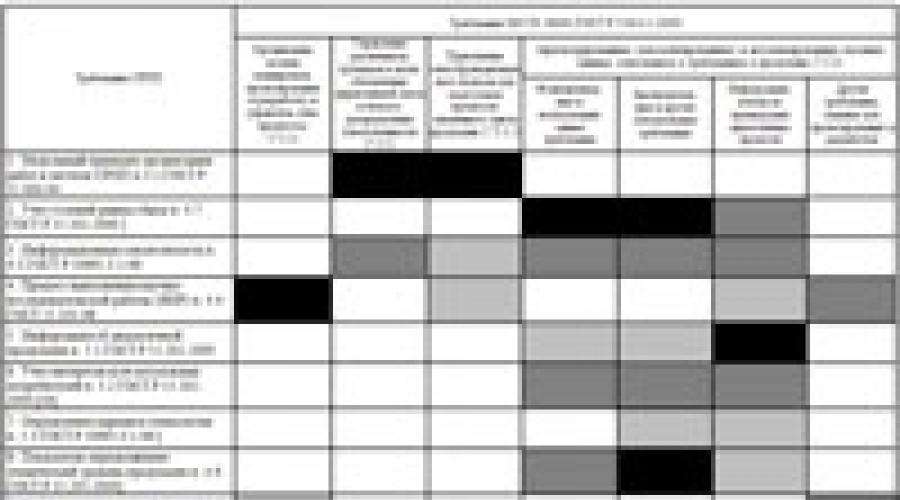
في السنوات الأخيرة ، تحتاج مؤسسات بناء الآلات بشكل متزايد إلى إنشاء أنظمة إدارة لا تتوافق مع المعيار الأساسي ISO 9001 ، ولكن مع معايير محسنة (محدثة وفقًا لمتطلبات الوقت وخصائص صناعة معينة) لأنظمة إدارة الجودة (على سبيل المثال ، معايير شركة غازبروم ، والسكك الحديدية الروسية ، وما إلى ذلك). P.).
على الرغم من أن غالبية الشركات الروسية قد أدخلت منذ فترة طويلة وتعمل بنجاح كبير نظامًا لتطوير المنتجات وإطلاقها (SRPP) ، والذي يتوافق مع المعايير الوطنية للاتحاد الروسي ، فإن العديد من المستهلكين يطلبون اليوم من الموردين تنفيذ أنظمة إدارة الجودة الحديثة تركز على المعايير التي تأخذ بعين الاعتبار خصوصيات الصناعة (على سبيل المثال ، المعيار الدولي ISO / TU 16949 ، AS 9100 وما شابه).
عند تنفيذ هذه المعايير ، من الضروري تكرار العديد من الإجراءات الحالية والقائمة في المؤسسة التي تنفذ متطلبات معايير SRPP. مما لا شك فيه أن هذا يؤدي إلى إهدار إضافي لجميع أنواع الموارد.
إن مهمة تقليل الوقت والموارد البشرية والمالية لتنفيذ متطلبات المعايير الدولية لأساليب وإجراءات ضمان الجودة باستخدام تجربة المعايير الوطنية الحالية للاتحاد الروسي هي مهمة ملحة للغاية اليوم.
على الرغم من الاختلافات الواضحة في ميزات إنتاج المباني في صناعة السيارات وفي الفروع الأخرى للهندسة الميكانيكية ، فإن السمة المشتركة هي الاستخدام الواسع النطاق لإمدادات المكونات إلى مصانع التجميع الرئيسية من قبل المؤسسات الصغيرة نسبيًا.
تم تطوير مبادئ تنظيم الإنتاج بشكل جيد في جميع مصانع السيارات تقريبًا (المحلية والأجنبية) ، دون استثناء ، يتم استخدامها أيضًا في هندسة النفط والغاز - في المصانع التي تنتج أنظمة تكنولوجية معقدة: منصات الحفر ، والمجمعات لتطوير الحقول البحرية ، إلخ. يمكن العثور على أمثلة مماثلة في صناعات أخرى أيضًا.
نظرًا لحقيقة أن السيارات هي نتاج طلب جماعي أوسع بكثير ، فقد كان على الشركات المصنعة في هذه الصناعة أن تولي اهتمامًا خاصًا لإنشاء أنظمة إدارة الجودة التي يمكن أن تتوافق مع المبادئ الحديثة لتنظيم الإنتاج ، علاوة على ذلك ، يمكن في نفس الوقت تساهم في تحسين جودة المنتج .... بالإضافة إلى ذلك ، أنشأت صناعة السيارات نظام معايير جودة الصناعة الخاص بها في وقت أبكر بكثير من الحاجة إليه في مجالات أخرى.
في هذا السياق ، فإن العمل في مجال تشكيل نظام إدارة الجودة ، والذي يتم تنفيذه حاليًا في مؤسسات السيارات ، له أهمية لا شك فيها. من الأرجح أنه ، مع مراعاة التعديلات الطفيفة ، يمكن أن تجد النتائج المحققة عليها تطبيقًا في أي مصانع لبناء الآلات.
من المعروف أنه من أجل توضيح للمستهلك كيف تراقب الشركة جودة منتجاتها ولضمان هذه الجودة ، يقوم المصنعون بإنشاء أنظمة إدارة الجودة التي تلبي متطلبات ISO 9001 و ISO / TU 16949 ، وتطبيق الأساليب الموضحة هناك.
في روسيا ، هناك اتجاه الآن للانتقال من المعايير الوطنية إلى المعيار الدولي ISO / TU 16949 ، والذي يتم تطبيقه على صناعة السيارات والمنظمات التي تنتج قطع الغيار المقابلة. نظرًا لحقيقة أن ISO / TU 16949 تم إصداره في وقت واحد مع معيار أنظمة إدارة الجودة ، فإن له الكثير من القواسم المشتركة مع الأخير ، ولكن له أيضًا خصائصه الخاصة ، حيث تم تطوير ISO / TU 16949 بواسطة صناعة السيارات الدولية فرقة العمل (IATF) ورابطة مصنعي السيارات اليابانية ، وهي شركة مسجلة (JAMA) بدعم من اللجنة الفنية ISO / TC 176 ، إدارة الجودة وضمان الجودة.
يقوم كبار مصنعي السيارات بالفعل باعتماد أو التخطيط للتصديق على أنظمة إدارة الجودة الخاصة بهم وفقًا للمعيار الدولي ISO / TU 16949 ، ويطلبون ذلك من مورديهم. على سبيل المثال ، طرح ممثلو "الثلاثة الكبار" - DaimlerChrysler و General Motors و Ford ، مثل هذه المتطلبات لمورديهم.
تجدر الإشارة إلى أن تنفيذ معيار ISO / TS 16949 يتطلب استخدام طرق خاصة لتنظيم العمل - APQP (خطة متقدمة لتخطيط ومراقبة جودة المنتج) ، PPAP (عملية الموافقة على جزء الإنتاج) الموافقة على إنتاج مكونات السيارات ) ، وكذلك استخدام بعض أدوات ضمان الجودة باستخدام طرق التحليل الإحصائية - FMEA (طريقة لتحليل وضع الفشل المحتمل وآثاره - طريقة تحليل أنواع ونتائج العيوب المحتملة) ، MSA (تحليل أنظمة القياس - تحليل أنظمة القياس ) ، SPC (طرق التحكم في العمليات الإحصائية) و QSA (تحليل أنظمة جودة الإدارة).
إن أخطر الصعوبات التي تواجه المؤسسات المحلية ناتجة عن إدخال طريقة تنظيم العمل APQP (التخطيط المتقدم لجودة المنتج) ، في الواقع - عملية التخطيط والتطوير والإعداد لإنتاج مكونات السيارات ، مما يجعل من الممكن ضمان ذلك بشكل مطلق. جميع متطلبات وتوقعات المستهلك بالفعل في مرحلة إعداد الإنتاج ، عندما تكون هناك فرص أساسية للوقاية من العيوب ، تنشأ الصعوبات بسبب حقيقة أن هذه العملية تؤثر تقريبًا على جميع الإدارات وجميع العمليات في المنظمة ويجب تنفيذها في جميع المراحل من دورة حياة المنتج - من التخطيط لإنشاء وتصميم وتطوير أحد مكونات السيارات إلى إنتاجه التسلسلي.
يوجد في روسيا نظام مشابه من حيث الغرض لنظام APQP - وهو نظام لتطوير وإطلاق المنتجات (SRPP).
كما تعلم ، فإن SRPP عبارة عن مجموعة معقدة من معايير الحالة الفنية التنظيمية والمنهجية والعامة الأساسية المترابطة التي تحدد الأحكام والقواعد والمتطلبات الرئيسية التي تضمن الوحدة الفنية والتنظيمية للعمل المنجز في مراحل دورة حياة المنتج (LCP) ) ، بما في ذلك البحث والتبرير لتطوير منتج أو مشروع ، في الواقع التطوير والإنتاج والتشغيل (التطبيق والتخزين) للمنتجات والإصلاح (للمنتجات التي تم إصلاحها) ، وكذلك تفاعل الأطراف المعنية.
يرتبط SRPP بمعايير الأنظمة الفنية العامة الأخرى ومجموعات المعايير: النظام الموحد لتوثيق التصميم (ESKD) ، والنظام الموحد للتوثيق التكنولوجي (ESTD) ، والنظام الموحد لتوثيق البرامج (ESPD) ، ونظام الدولة لضمان توحيد القياسات ، والدعم التكنولوجي لإنشاء المنتج.
في الوقت الحالي ، يشعر العديد من المتخصصين في المؤسسات بالقلق إزاء المشكلة التالية - لقد نفذت الشركات بالفعل نظامًا لتطوير وإطلاق المنتجات وفقًا للمعايير الوطنية للاتحاد الروسي بنجاح. ولكن يأتي وقت يطلب فيه المستهلك - صانع سيارات معين - من مورده تنفيذ نظام إدارة الجودة وفقًا للمعيار الدولي ISO / TU 16949 ، بما في ذلك ، بالطبع ، إدخال طريقة APQP كجزء لا يتجزأ من مثل نظام إدارة الجودة. يفهم الخبراء أنه يتعين عليهم تكرار العديد من العمليات الجارية بالفعل ، والتي تكون مصحوبة بتكاليف إضافية غير منطقية.
تمت مناقشة هذا الوضع بوضوح من قبل الخبراء الذين واجهوه. صحيح ، في معظم الحالات ، يتكهن الخبراء فقط حول مدى اهتمام متطلبات المنظمات الدولية (فرقة العمل الدولية لصناعة السيارات (IATF)) التي تتوافق مع متطلبات معاييرنا الوطنية القديمة طويلة الاستخدام ، والتي تم تطويرها مرة أخرى في الثمانينات والتسعينات من القرن الماضي.
إذن ، هناك مشكلة - كيفية تنفيذ متطلبات معيار ISO / TU 16949 بأقل تكلفة ، بما في ذلك طريقة APQP ، التي لا تزال غريبة بالنسبة لنا ، في مؤسسة لديها SRPP مطبق ويعمل بنجاح.
كان الغرض من دراستنا هو تطوير خوارزمية لتطوير أنظمة إدارة الجودة الدولية في الشركات الروسية ، مع مراعاة خصوصيات الخبرة السابقة المتراكمة في تشغيل الأنظمة المحلية وفي نفس الوقت تحسين تكاليف أنواع مختلفة من الموارد: العمالة ، المالية ، الوقت ، إلخ.
قام المؤلف بتحليل درجة توافق متطلبات معيار ISO / TU 16949 وطريقة APQP مع متطلبات المعايير الوطنية لـ SRPP. لهذا الغرض ، تم بناء مصفوفات الامتثال لمتطلبات النظامين المذكورين أعلاه ، حيث يفي 45 صفًا بمتطلبات SRPP ، ويلبي 49 عمودًا متطلبات ISO / TU 16949 و APQP. تم تحليل كل عنصر من عناصر تقاطع الصفوف والأعمدة بشكل أكبر من خلال مجموعة من أحكام الخبراء وطرق تحليل الانحدار.
لفهم أكثر دقة لما كانت درجة تعميم المتطلبات ، وكيف تم تصنيف متطلبات طريقة APQP إلى مجموعات ، وأي متطلبات من SRPP تم النظر فيها لتوافقها مع متطلبات عملية APQP ، سننظر في جزء صغير من المصفوفة بشكل أكبر. يتم عرض جزء من المصفوفة في الجدول 2.
الجدول 2 - جزء من مصفوفة التوافق لمتطلبات SRPP و ISO / TU 16949
نتيجة للتحليل ، تم الكشف عن وجود توافق (كامل أو جزئي) في بعض الحالات مع متطلبات ISO / TU 16949 و APQP مع متطلبات SRPP والعكس صحيح. لذلك ، علاوة على ذلك ، تم إجراء تقييم كمي لدرجة توافق متطلبات ISO / TU 16949 وطريقة APQP ، والتي أظهرت أن التطابق الكامل للمتطلبات تم العثور عليه في 15 ٪ من الحالات ، والتزامن الجزئي للمتطلبات - في 13٪ من الحالات. بالإضافة إلى ذلك ، تم تحديد المواقف التي يمكن أن تكون فيها المتطلبات بمثابة أساس لتنفيذ المعايير الدولية: لا تتوافق مجموعة المتطلبات ISO / TU 16949 و APQP بشكل مباشر مع متطلبات SRPP ، ولكن إذا تم استكمال هذه الأخيرة بطريقة ما ، ثم تحدث مصادفة كاملة أو جزئية ... كان هناك حوالي 22٪ من هذه الحالات. أخيرًا ، بلغ عدد الحالات ذات المطابقة الضئيلة 12٪ ، ولم يتم العثور على تطابق في 38٪ من الحالات.
على سبيل المثال ، تنص الفقرة 5.2 من GOST R 15.201-2000 على ما يلي: "يوصى بمراعاة مصالح جميع المستهلكين المحتملين في الاختصاصات". في المقابل ، كمدخل في المرحلة الأولى من طريقة APQP ، من الضروري الحصول على "معلومات من مستهلكين محددين". وجدت الدراسة أن هناك تداخلًا تامًا في المتطلبات.
مثال آخر: في الفقرة 4.6 من GOST R 15.201-2000 ، هناك مطلب مفاده أن مطور المنتج ، عند إجراء البحث والتطوير والعمل التكنولوجي ، يجب أن يولي اهتمامًا خاصًا لضمان ، على وجه الخصوص ، متطلبات محاسبة مؤشرات المنتج التي تحدد ذلك.المستوى التقني. تتعامل عملية APQP مع معايير منتجات / عمليات المنافسين. في هذه الحالة ، تم الاعتراف بوجود تداخل في المتطلبات. يتشابه الموقف مع متطلبات مثل التطوير التكنولوجي الإلزامي للمنتجات وفقًا للبند 5.2.6 من GOST R 50995.3.1-96 والحاجة إلى "افتراض المنتج والعملية" وفقًا لمتطلبات طريقة APQP.
بناءً على نتائج هذا العمل ، يمكن استخلاص الاستنتاج التالي - عند تنفيذ ISO / TU 16949 وطريقة تنظيم عمل APQP في المؤسسات مع تنفيذ SRPP ويعمل بنجاح ، من الممكن تقليل تكاليف الموارد بشكل كبير.
يمكن تحقيق خفض التكلفة بسبب حقيقة أن عناصر التحكم في عملية ما قبل الإنتاج التي تم تنفيذها بالفعل في المؤسسة وفقًا لمتطلبات معايير SRPP لا تحتاج إلى إعادة التنفيذ إذا تم توفيرها في تطبيق ISO / TU 16949 و APQP. سيكون كافيا لتوضيح الاختلاف في المصطلحات في توثيق المؤسسة. نتفهم جميعًا تمامًا أن مثل هذا النهج يمكن أن يوفر بشكل كبير الوقت لتنفيذ ISO / TU 16949 وطريقة APQP ، ويقلل من الموارد البشرية والمادية المطلوبة للتنفيذ.
وتجدر الإشارة إلى أنه تم إجراء تحليل سطحي إلى حد ما للوضع الحالي. على وجه الخصوص ، تم تقسيم متطلبات معايير SRPP إلى 45 مجموعة فقط ، ومتطلبات ISO / TU 16949 وطريقة APQP - إلى 49 مجموعة ، والتي ربما لا تكون كافية لإجراء تقييم كامل لتوافق متطلبات ISO / TU 16949 و APQP مع متطلبات معايير SRPP ؛ وتجدر الإشارة أيضًا إلى أنه تم استخدام مقياس من 5 فئات فقط لتقييم توافق المتطلبات ، والذي يعطي أيضًا فقط تقييمًا تقريبيًا لتوافق المتطلبات.
وتجدر الإشارة أيضًا إلى أنه وفقًا لخصائص المؤسسة والاتجاه العام لأنشطتها ، قد تختلف إجراءات تنفيذ المتطلبات المختلفة لمعايير SRPP ومتطلبات ISO / TU 16949 و APQP. ولكن ، في الوقت نفسه ، ينبغي ألا يغيب عن البال أن بعض المتطلبات قد تكون مترابطة ومن ثم هناك ترتيب لا جدال فيه في تنفيذها. يجب أن يؤخذ هذا الوضع في الاعتبار عند التنفيذ المشترك لمعايير SRPP و ISO / TU 16949.
مع الأخذ في الاعتبار ما سبق ، تم تطوير مخطط تنظيم الإنتاج ، والذي أطلقنا عليه "النموذج التنظيمي" (الشكل 1). يتيح لك النموذج التنظيمي تحديد تسلسل الإجراءات في مرحلة التصميم ، وتطوير المنتجات وإطلاقها في الإنتاج وأثناء إنتاج المنتجات ، وتحديد الاختناقات وتوطينها ، واتخاذ إجراءات محددة للقضاء عليها ، وتوزيع المسؤولية والسلطة داخل كل من الوحدة مسؤول عن إصدار المنتج وفي جميع أنحاء المنظمة.
الشكل 1 - النموذج التنظيمي "إدارة الإنتاج والخدمات"
النموذج التنظيمي المطور ينطبق على أي مؤسسة صناعية. يمكن استخدام النموذج التنظيمي لتحديد ترتيب التنفيذ وتوزيع العمل عند إدخال الأساليب الحديثة لإدارة الجودة في مؤسسة بناء الآلات التي لديها نظام إدارة تشغيل يعتمد على المعايير المطبقة للنظام الوطني لـ SRPP.
لم يأخذ التحليل أيضًا في الاعتبار عامل مثل بعض عدم الدقة والمصطلح في ترجمة النص الذي يصف طريقة APQP. في مثل هذه الحالة ، قد يكون من الصعب جدًا مراعاة المرادفات عند تحديد المتطلبات - بعد كل شيء ، قد تتطابق بعض المتطلبات تمامًا ، ولكن في نفس الوقت يتم التعبير عنها بكلمات مختلفة تمامًا.
تسمح لنا نتائج التحليل بتطوير خوارزمية محددة لتنفيذ متطلبات المعايير الدولية ، مع مراعاة نظام PSPP العامل في المؤسسات ، والذي يمكن أن يقلل بشكل كبير من الوقت والموارد البشرية والمالية وفي نفس الوقت استخدام أمتعة ضخمة تركها لنا أسلافنا - المهندسين السوفيت - مطورو المعايير الوطنية. سيتم وصف هذه الخوارزمية في المنشور التالي للمؤلف.
ناتاليا فاششينكو- رئيس قسم إصدار الشهادات وتنظيم العمل ، مركز تنسيق ANO "ATOMVOENCERT"
قائمة المصادر المستخدمة
1 كودرياشوف أ. طاوله دائريه الشكل. APQP: المشاكل وتجربة التنفيذ // طرق إدارة الجودة. - 2012. - رقم 6.
2 Kershenbaum V.Ya.، Vaschenko N.V. منهجية لتقييم مدى توافق المتطلبات التنظيمية للممارسات المحلية والأجنبية في بناء أنظمة إدارة الجودة // إدارة الجودة في مجمع النفط والغاز. - 2013. - رقم 1. - مع. 17 - 21.
3 Vaschenko N.V. حول ملاءمة إجراء موثق في إطار تنفيذ متطلبات القسم السابع من ISO 9001: 2008 // إدارة الجودة في مجمع النفط والغاز. - 2013. - رقم 2. - مع. 14 - 18.
تشير العديد من الإحصائيات حول الجودة إلى أن عيب المنتجات هو ما يقرب من 85-90٪ ناتج عن عوامل بشرية. ضع في اعتبارك الأسباب المرتبطة بالعامل التي يمكن أن تؤثر على عدم الامتثال للوثائق الفنية ، بما في ذلك المنتجات المعيبة. من بينها ، يمكن للمرء أن يلاحظ: المؤهلات المنخفضة ، والخبرة العملية القصيرة ، وسوء الحالة الصحية ، وعدم الانتباه عند التعرف على الرسومات أو التقنيات أو التعليمات ، وإعداد مكان العمل بجودة رديئة.
يجب التأكيد على أن أسباب الزواج يمكن أن ترتبط ليس فقط بالشخص ، ولكن أيضًا بأداة ، ومعدات تكنولوجية ، وأدوات. هذا صحيح ، ولكن في أغلب الأحيان لا يحدث هذا كثيرًا بسبب أوجه القصور في الأداة أو المعدات أو الأدوات نفسها ، ولكن نظرًا لإهمالها في شحذها أو ضعف الإصلاحات أو التصنيع والتجميع غير الدقيقين اللذين يقوم بهما العمال. إذا "وصلت إلى الجزء السفلي" من المتسبب في الخلل ، ففي الغالبية العظمى سيكون الشخص الذي لا يعمل بالضرورة في شركتك ، ولكن ربما في شركة المورد.
أين يجب أن تبدأ في تحسين الجودة؟ ينصح الخبراء اليابانيون بالبدء بالجودة في مكان العمل. علاوة على ذلك ، فقد طوروا نظامًا متماسكًا لتحسين الجودة في مكان العمل ، والذي يسمونه "5S" (الممارسات الجيدة لصيانة المنزل). يأتي الاسم من خمس كلمات يابانية تبدأ بالحرف "C": seiri (الفرز) ، seiso (التنظيف) ، seiton (المنظمة) ، seiketsu (التوحيد القياسي) ، shitsuke (الاختبار الذاتي). تعطي الترجمة الروسية لهذه الكلمات ، إن لم تكن واضحة تمامًا ، فكرة كافية تمامًا عن المحتوى التقريبي للتدابير الرامية إلى تحسين الجودة في مكان العمل. إذا وصفنا هذا النظام بإيجاز ، فيمكننا القول أنه "قبل بدء العمل ، وحتى المسؤول ، تحتاج إلى فهم الترتيب في مكان عملك."
دعونا نعطي محتوى أوضح لكل مرحلة من مراحل نظام "5S". قبل الشروع في تنفيذه ، من الضروري أن تصف بالتفصيل ، وإذا أمكن ، قم بتصوير منطقة العمل (أو مكان العمل) الذي يحتاج إلى إعادة تنظيم. يمكن أن يكون لمقارنة أوصاف مناطق العمل (الأماكن) قبل التحول وبعده انطباع إيجابي على الإدارة ، مما ينشط العمل في المؤسسة من أجل الجودة.
المرحلة 1. الفرز.ضع الأشياء (أو الأشياء) التي يتم استخدامها يوميًا في مكان واحد. يجب وضع العناصر التي يتم استخدامها مرة واحدة في الأسبوع في مكان آخر ، شهريًا - في الثلث ، وتلك التي نادرًا ما تكون مطلوبة - في مكان رابع. قم بتنفيذ هذا الإجراء لكل منطقة من مكان العمل. ثم ، من كل موقع تخزين ، حدد واترك نسخة واحدة من كل نوع من العناصر ، وانقل الباقي إلى الخزانة لتخزين قطع الغيار.
المرحلة 2. التنظيف.نظف جميع أسطح العمل قبل وضع أي شيء عليها مرة أخرى. تأكد من وجود حاويات مناسبة لجمع النفايات بالقرب من منطقة العمل. ضع جميع قطع الغيار في مستودع مشترك. قم بعمل قائمة بالعناصر التي تم إرجاعها إلى المستودع حتى تتمكن من إبلاغ إدارة الورشة بها. تنظيم ووضع جميع المستندات اللازمة في مكان واحد وتنظيف جميع الأدوات. وضع معايير (قواعد) للنظافة يجب على كل عامل مراعاتها.
المرحلة 3. التنظيم.رتب جميع الأوراق والمجلدات بدقة. يجب أن تكون العناصر التي يتم استخدامها على أساس يومي في متناول اليد للعامل. يمكن وضع العناصر المستخدمة مرة واحدة في الأسبوع على مسافة خطوة واحدة ، والعناصر المستخدمة مرة واحدة في الشهر على مسافة 2-3 خطوات. يمكن تحديد موقع كل شيء آخر على بعد خطوات قليلة من مكان العمل. من الضروري تحديد مكان كل عنصر بوضوح.
المرحلة 4. التوحيد.قم بتعريف جميع الموظفين المرتبطين بمكان العمل هذا بمعايير النظافة وانشر صورًا للإعداد القياسي "الصحيح". عند الاقتضاء ، قم بتزويد المعدات والأدوات بأغطية غبار شفافة. إذا كانت هذه الأغطية معتمة ، فمن المرجح أن يقوم العمال بتخزين عناصر خارج مساحة العمل تحتها.
المرحلة 5. الاختبار الذاتي.بعد حوالي شهر ، قم بفحص حالة مكان العمل بعناية لمعرفة ما إذا كان يمكن تحسينها. إذا وجدت عناصر إضافية ، أرسلها إلى المستودع العام. مراجعة معايير النقاء ومراجعتها إذا لزم الأمر. كرر هذه الخطوة بعد شهر.
يمكنك أيضًا التوصية بإجراءات إضافية للحفاظ على النظام في مكان العمل. لذلك ، على سبيل المثال ، يمكنك إنشاء لوحات متحركة بأدوات لوظائف محددة ، أو رسم الخطوط العريضة للأدوات على اللوحات بحيث تتضح على الفور الأداة المفقودة.
يعتقد الباحثون اليابانيون أنه إذا لم يتمكن مديرو الشركة من تنفيذ مفهوم 5S ، فلن يتمكنوا من الإدارة بشكل فعال. على العكس من ذلك ، إذا كان بإمكانك إتقان النظام ، فهذا يعني أنه يمكنك تنفيذ أنظمة أخرى أكثر تعقيدًا بنجاح. والسبب في هذا الاستنتاج هو أن نظام "5S" لا يتطلب أي موظفين خاصين من المديرين لتنفيذه ولن يصبح ساري المفعول حتى يشارك فيه جميع الموظفين ويبدأوا في التفكير في نجاح هذا النظام. ولكن إذا تم تنفيذ نظام 5S بالفعل ، فيمكننا افتراض أن الأنظمة الأخرى متقنة نصف تقريبًا (من حيث استعداد الموظفين لتنفيذ التغييرات).
منذ منتصف الثمانينيات. القرن العشرين في الشركات اليابانية ، كان نظام 5S محوريًا في التفكير الإداري والفلسفة. لقد توصلت إدارة الشركات في كل مكان إلى رأي مفاده أن هذا النظام هو الطريقة الرئيسية للإدارة في أي مجال ، حتى في أكثر مجالات النشاط عالية التقنية.
في السنوات الأخيرة ، أصبح نظام 5S معروفًا على نطاق واسع في الشركات الروسية. من الممارسة المحلية لإدخال هذا النظام ، يمكن استخلاص الاستنتاجات التالية:
- - قابل للتطبيق ويمكن تنفيذه بنجاح في المؤسسات والمنظمات المحلية من مختلف أشكال الملكية إذا كانت القيادة مهتمة بذلك ؛
- - أن محتوى مبادئ النظام وتكنولوجيا تنفيذه تتطلب تكيفاً كبيراً مع خصائص الاقتصاد المحلي وطرق تنظيم الإنتاج وعقلية العاملين ؛
- - إمكانية التنفيذ الناجح للنظام تعتمد بشكل مباشر على الظروف الاجتماعية والاقتصادية للعمل في مكان العمل ، أي مستوى وانتظام دفع الأجور ، وعبء العمل المنتظم والمنتظم للإنتاج ، وامتثال الإدارة للمتطلبات الأساسية على الأقل لظروف العمل الآمنة.
وقد بذلت محاولات لتحديث هذا النظام ، مع مراعاة مبادئ التنظيم العلمي للعمل وممارسة تحسين الجودة. النظام الجديد ، الذي أدمج عناصر نظام "5S" وتكييفه مع ظروف الإنتاج المحلية ، سُمي "الترتيب" (الجدول 2.4). المبادئ الأساسية لهذا النظام هي كما يلي:
- - قم بإزالة كل ما هو غير ضروري ؛
- - إجراء تنظيف شامل بانتظام والتحقق من صلاحية المعدات والمخزون ؛
- - لوضع كل شيء في مكان العمل بالطريقة الأكثر ملاءمة ؛
- - وضع معايير (قواعد) للتخزين والاستخدام والتنظيف والتفتيش ؛
- - اتباع القواعد المقبولة بشكل مستمر وواعي.
الجدول 2.4
مقارنة بين مبادئ النظم "5S" و "الترتيب"
1. مشاركة الفريق بأكمله.مثلما يستحيل "غلي الماء في زاوية واحدة من البركة" ، فلا يمكن تطبيق هذا النظام بشكل فعال في مكان عمل واحد أو في قسم واحد بأمر من شخص واحد. يتطلب النظام الجديد تصميم وتماسك الفريق بأكمله.
كل قاعدة من قواعد النظام التي يجب الوفاء بها ليست صعبة في حد ذاتها. تكمن الصعوبة في عدم التوقف عن فعل ذلك. وهذا يتطلب المثابرة والتعاون ، وهذا بدوره يخلق إحساسًا بالانتماء إلى فريق ويحسن مناخ الشركة.
2. سهولة التعلم - على ما يبدو.للوهلة الأولى ، تبدو مبادئ نظام "التسلسل" واضحة جدًا وسهلة التنفيذ. لكن لماذا يصعب تنفيذها؟
ترجع السهولة الظاهرة في تنفيذ هذه المبادئ إلى حقيقة أن الموظفين لا يفهمون تمامًا ما هو نظام "الترتيب". هذا ليس تنظيفًا عامًا لمرة واحدة ، وليس نقل أداة من مكان إلى آخر ، ولكنه أسلوب جديد جوهريًا في الموقف تجاه بيئة العمل ، وتنظيمها وسلامتها ، وأسلوب الحفاظ باستمرار على مكان عمل نظيف عالي التنظيم.
3. من التصحيحات إلى المنع.يمكنك في كثير من الأحيان ملاحظة مقدار الوقت الذي يقضيه المديرون في إصلاح الخطأ الذي تم فعله في الوقت المناسب. يتفاعلون مع المتاعب بعد وقوعها. لكن عندما نتعرف على المشكلات ، يتضح أن أسباب العديد منها غالبًا ما تكون أشياء بسيطة جدًا.
يمكن للمخالفات التي لوحظت في الوقت المناسب في تشغيل المعدات أو الأعطال المحددة للمعدات أو المخزون أن تمنع الخسائر الكبيرة والحوادث. حتى أي "أشياء صغيرة" في مجموعة من الظروف غير المواتية يمكن أن تجلب مشاكل كبيرة.
- 4. من إدارة النتائج - لمعالجة السيطرة.في كثير من الأحيان ، يميل المديرون إلى رؤية نتائج الأنشطة فقط والحكم على فعالية عملهم. عند تنفيذ نظام "الترتيب" ، من الضروري معرفة الأسباب التي تؤدي إلى نتائج معينة ، لرؤية العملية برمتها ، ونقاط قوتها وضعفها.
- 5. التأكيد على تلبية المتطلبات الأساسية.يجب أن يعتاد الموظفون على الوفاء المستمر بالمتطلبات الأساسية. على سبيل المثال ، التحقق من وجود جميع النقوش والملصقات على العناصر أو الأشياء المهمة.
- 6. تعزيز مسؤولية كل موظف عن نتائج عمله.قال السيد فورد ذات مرة أنه "حتى أكثر العمال غباءً يمكنهم إيجاد مائة طريقة لخداع أكثر العمال المؤهلين". وهذا يؤكد أن فقط عامل المسؤولية الشخصية للعامل واهتمامه بالعمل يمكن أن يلعب دورًا إيجابيًا كبيرًا في الإنتاج ، وليس التنظيم المستمر للعمل والرقابة الصارمة. هناك حاجة إلى جو حيث يساعد الناس بعضهم البعض ويحاول الجميع القيام بالمهمة بشكل جيد.
- 7. فهم التعليمات واتباع متطلباتها.في كثير من الأحيان ، لا يتم اتباع التعليمات والمتطلبات ، ليس بسبب إهمال الموظفين لها ، ولكن لأنهم إما لا يعرفون أو لا يفهمون تمامًا جوهر المتطلبات أو التوصيات التي تحتوي عليها.
يسمح نظام "الترتيب" للموظفين بتطوير قواعد وتعليمات محددة بشكل مستقل فيما يتعلق بأماكن عملهم.
8. نهج تدريجي (خطوة بخطوة).من الواضح أن نظام "الانسياب" ، الذي يركز بشكل أساسي على تغيير الصور النمطية السلوكية للعمال ، لا يمكن تنفيذه بسرعة وعلى الفور بعد بدء تنفيذه ، وتحقيق نتائج ملموسة. النظام الجديد هو الخطوة الأولى نحو برنامج استرداد طويل الأجل للمؤسسة.
تفترض تقنية تنفيذ النظام إتقانًا منهجيًا وتدريجيًا خطوة بخطوة لمبادئها وتقييم وتوحيد نتائج كل خطوة.
9. النظام "الترتيب» - هذا هو الطريق الصعب.النظام الجديد ، مثل نظام 5S الياباني ، يعمل وفقًا لمبدأ: "الأفعال تتحدث بصوت أعلى من الكلمات". أي عمل كبير يبدأ بشيء صغير ، بفهم تدريجي لجوهر المشكلة ، بالأخطاء والتصحيحات. يجب ألا ترفض أبدًا المساعدة والمشورة والدعم من الزملاء والموظفين الهندسيين. التقدم الحقيقي ، التدريجي ، حتى بخطوات صغيرة ، مفيد أكثر بكثير من المناقشات العالمية حول مشروع كبير يمكنه قلب هيكل الإنتاج في مكان عمل معين.
الأساليب المنهجية المذكورة أعلاه لا تكشف كثيرًا عن محتوى وتكنولوجيا تنفيذ مبادئ نظام "الترتيب" ، ولكنها تشرح العقبات والصعوبات والصعوبات التي ستواجه في طريقة تنفيذ كل من هذا النظام و "5S" النظام.
إذا كان الموظف الياباني ، فإن ثقة إدارة الشركة في أن إدخال نظام 5S سيكون ذا فائدة كبيرة ليس فقط للشركة ، ولكن أيضًا للموظف نفسه ، يكفي تمامًا ، بحيث يكون الدافع طويل الأجل لتنفيذ العناصر يتم تنفيذ هذا النظام من الناحية العملية ، ومن الواضح أن هذا لا يكفي لموظف في شركة روسية ... هناك حاجة إلى آليات فعالة من شأنها أن تحفز على تحسين الوظائف وتحسين جودة المنتجات والعمل في كل مكان عمل. كما هو الحال دائمًا ، في المؤسسات الروسية ، كل ما يتعلق بالتحسين والترشيد ، بما في ذلك الوظائف ، لا يعتمد عمليًا على النظام ، وليس على الحوافز الفعالة ، ولكن على المبادرة الشخصية فقط. مثل هذه المسألة الخطيرة مثل تنفيذ أنظمة 5S أو Streamlining لا يمكن إلقاء اللوم عليها على هواة المصانع وحدهم.
هناك رأي مفاده أنه إذا كان بالإمكان إنجاز كل الأعمال "في حالة الطوارئ" ، فلن يكون لروسيا منافسون هنا ، في حين أن العمل المرتبط بالعمل الشاق اليومي المتمثل في ترتيب الأمور والنظافة لا يتوافق مع عقليتنا. ومن هنا تأتي الحاجة إلى شرح مطوّل باستخدام مناهج منهجية حول كيفية أداء عمل بسيط إلى حد ما بشكل أساسي ، وهي مبادئ نظام "الترتيب".
إذا أردنا أن نعيش بطريقة حضارية ، على سبيل المثال ، في اليابان أو أوروبا ، فيجب على المديرين الجدد إلهام العمال بأن جودة العمل لا تعتمد على عقلية الأمة ، ولكن على القدرة والرغبة في ذلك. الامتثال لجميع المتطلبات المسجلة في كل من المواصفات الفنية للمنتجات وفي المواصفات الدولية ISO 9000. وليس فقط لغرس ، ولكن أيضًا ضمانًا تنظيميًا وماديًا لتطبيق المعايير اللازمة.
نتيجة دراسة المادة في هذا الفصل يجب على الطالب:
أعرف
- سبع أدوات لمراقبة جودة المنتج ؛
- الأساليب الإحصائية لمراقبة جودة المنتج ؛
- تحليل التكلفة الوظيفية
- تقنيات إدارة الجودة الحديثة (مفهوم ستة سيجما ، طريقة QFD ، إلخ) ؛
يكون قادرا على
- بناء مخطط إيشيكاوا السببي ومخطط باريتو لإدارة جودة السلع والخدمات ؛
- تطبيق طريقة QFD لتتبع متطلبات العملاء في جميع مراحل دورة حياة المنتج ؛
- تطبيق التحليل الوظيفي والتكلفة من أجل تحقيق الخصائص الاستهلاكية الضرورية لمنتج (خدمة) بأقل تكاليف لتوفيرها ؛
ملك
- المهارات في استخدام سبع أدوات لمراقبة جودة السلع التي تدخل التجارة ؛
- الأساليب الإحصائية لإدارة جودة السلع الداخلة للتجارة.
أهمية الأساليب وتصنيفها
كما هو مذكور أعلاه ، في الفصل. 2 ، أحد مبادئ SM K هو أن أساس اتخاذ القرار يجب أن يكون فقط الحقائق وليس الحدس. أحد أسباب أخطاء إدارة الجودة هو الخلط بين الحقائق والأحكام الذاتية. لمنع الأخطاء ، يجب تنظيم عملية البحث عن الحقائق ، أي مواد إحصائية.
تتعامل الإحصاءات الرياضية ، التي تتضمن عددًا كبيرًا من الأساليب المختلفة ، مع جمع النتائج ومعالجتها وتحليلها. اختار العلماء اليابانيون (بشكل أساسي البروفيسور ك. إيشيكاوا) من هذه المجموعة سبع أدوات أساسية لمراقبة الجودة(الشكل 4.1). لعبت دوائر الجودة دورًا مهمًا في إتقان الأساليب الإحصائية في اليابان.
أرز. 4.1
مع نمو أحجام الإنتاج أثناء الإنتاج الضخم والمتسلسل للمنتجات ، يحتاج المستهلك (ككيان قانوني) والشركة المصنعة نفسها إلى معلومات حول الجودة الحقيقية للمنتجات التي يتم إنتاجها وشرائها. ومع ذلك ، نظرًا للكم الكبير من مجموعات المنتجات المصنعة ، كان من الصعب إجراء مراقبة كاملة للجودة ، وكانت موثوقيتها منخفضة. من أجل تقليل كثافة اليد العاملة وزيادة الموثوقية ، بدأوا في الاستخدام الأساليب الإحصائية لمراقبة جودة أخذ العينات.معناها بسيط للغاية: بعد دراسة جزء صغير من المنتجات (العينة) ، يمكنك التوصل إلى استنتاجات موثوقة حول جودة الدفعة بأكملها.
في أواخر السبعينيات وأوائل الثمانينيات. طور تحالف العلماء والمهندسين اليابانيين مجموعة أكثر تطوراً من أدوات مراقبة الجودة. استندت هذه الأدوات إلى كل من أساليب الإحصاء الرياضي وأساليب العلوم الأخرى: التحليل التشغيلي ، ونظرية التحسين ، إلخ. كأدوات أكثر دقة ، تم توجيهها إلى فريق الهندسة. تسمى هذه الأساليب أدوات إدارة الجودة.يغطي هذا البرنامج التعليمي بعض أدوات إدارة الجودة: البرنامج "ستة غرابيل" ، تكنولوجيا نشر وظيفة الجودة ، تحليل التكلفة الوظيفية.
يتم وصف ثلاث مجموعات من الأساليب أدناه:
- 1) أدوات مراقبة الجودة الأساسية ؛
- 2) الأساليب الإحصائية لمراقبة جودة أخذ العينات ؛
- 3) أدوات إدارة الجودة.
أدوات مراقبة الجودة الأساسية
أدوات مراقبة الجودة الرئيسية هي طرق التحليل الإحصائي للظروف والعوامل التي تؤثر على جودة المنتج. يتضمن التحليل الإحصائي تحليلاً لأنواع الزواج وأسبابه ، وتحليل تأثير العوامل الفردية للعملية التكنولوجية على مؤشرات الجودة. في التحليل ، يوصى باستخدام طرق رسومية خاصة (تسمى أحيانًا الإحصائيات الوصفية) لتصور بيانات الجودة. تتضمن هذه الطرق سبع أدوات لمراقبة الجودة (انظر الشكل 4.1).
قائمة التحقق (ورقة)- أداة لجمع وتنظيم البيانات لتسهيل الاستخدام الإضافي للمعلومات التي تم جمعها.
في التين. 4.1 ليس من قبيل المصادفة أن تكون ورقة التحكم موجودة في المركز ، وتحيط بها الأجهزة الستة الأخرى. إنها تلعب دورًا خاصًا ، لأن تنفيذ أي مهمة لتحليل الجودة يبدأ بجمع البيانات الأولية.
القائمة المرجعية عبارة عن نموذج ورقي تُطبع عليه مسبقًا أنواع العيوب الخاضعة للرقابة (في حالتنا ، باستخدام مثال العيوب في منتجات الزخرفة الخزفية) ، والتي وفقًا لتكرار حدوثها يشار إليها في شكل رموز بسيطة.
يتم حساب عدد المنشورات المختلفة في المؤسسة بالمئات ، ولكل غرض محدد ، في الجوهر ، يمكن تطوير المنشور الخاص بها. لكن مبدأ تصميمها لم يتغير: يجب أن يكون شكل الورقة بسيطًا ومفهومًا (بدون تفسيرات إضافية) ؛ من الضروري الإشارة إلى من قام بجمع البيانات وفي أي مرحلة وإلى متى.
من الواضح أن جودة المنتجات هي المؤشر الرئيسي لنشاط أي مؤسسة. للحفاظ على القدرة التنافسية للسلع والخدمات ، يتم استخدام تطوير نظام إدارة سلامة الأغذية ، ومجموعة متنوعة ، معظمها اقتصادية ورياضية ، اليوم. على سبيل المثال ، البرمجة الديناميكية والخطية وغير الخطية ونمذجة المحاكاة وتخطيط التجربة ونظرية قائمة الانتظار ونظرية اللعبة وتحليل القيمة الوظيفية وطريقة تاجوشي وطريقة هيكلة الجودة.
اترك طلب للحصول على استشارة مجانية
نشر وظيفة الجودة (QFD)). إنه نهج منظم لتحديد متطلبات العملاء يساعد المؤسسة على فهم ودمج تحديد المتطلبات في خطط تقديم خدمة محددة. على عكس الطرق الأخرى ، يعد QFD طريقة لضمان الجودة تفترض تلبية احتياجات العميل في بناء المصفوفات المتعرجة ، والتي تسمى فيما بعد "منازل الجودة" ، والتي يتم من خلالها تسجيل المعلومات حول جودة الخدمة والقرارات المتخذة. هذه الطريقة هي تقنية لتصميم المنتجات والعمليات التي تسمح بتحويل رغبات المستهلك إلى متطلبات فنية للمنتجات ومعايير عمليات الإنتاج الخاصة بها. طريقة QFD هي طريقة متخصصة تستخدم طريقة مجدولة لعرض البيانات ، وبنموذج محدد من الجداول ، والتي تسمى "بيوت الجودة". الفكرة الرئيسية لتكنولوجيا QFD هي فهم أن هناك فرقًا كبيرًا بين خصائص المستهلك ("مؤشرات الجودة الفعلية") ومعايير المنتج المحددة في المعايير ("مؤشرات الجودة المساعدة"). تعتبر مقاييس الجودة الإضافية مهمة للمصنع ، ولكنها ليست ضرورية دائمًا للمستهلك. ستكون الحالة المثالية عندما يمكن للشركة المصنعة التحكم في جودة المنتجات مباشرة من المؤشرات الفعلية ، ولكن هذا عادة ما يكون مستحيلًا ، لذلك يستخدم مؤشرات مساعدة.
تقنية QFD هي سلسلة من الإجراءات التي تتخذها الشركة المصنعة لتحويل مؤشرات الجودة الفعلية للمنتج إلى متطلبات فنية للمنتجات والعمليات والمعدات. الأداة الرئيسية لتكنولوجيا QFD هي جدول خاص يسمى "منزل الجودة". يوضح هذا الجدول العلاقة بين مؤشرات الجودة الفعلية (خصائص المستهلك) والمؤشرات المساعدة (المتطلبات الفنية):
يتيح لك تطبيق طريقة QFD مراعاة متطلبات المستهلك في جميع مراحل إنتاج المنتجات النهائية لجميع عناصر نظام الجودة في المؤسسة ، وبالتالي زيادة درجة رضا العملاء وتقليل تكلفة التصميم و تحضير المنتجات للإنتاج.
طريقة FSAهي تقنية لتحليل تكاليف منتج يؤدي وظائفه ؛ يتم تنفيذ FSA للمنتجات والعمليات الحالية من أجل تقليل التكاليف ، وكذلك للمنتجات قيد التطوير من أجل تقليل تكلفتها. تم استخدام طريقة FSA بنشاط في الصناعة منذ الستينيات ، بشكل أساسي في الولايات المتحدة. جعل استخدامه من الممكن تقليل تكلفة العديد من أنواع المنتجات دون تقليل جودتها وتحسين تكاليف التصنيع. يعد FSA الآن أحد أكثر أنواع تحليل المنتجات والعمليات شيوعًا. FSA هي إحدى طرق التحليل الوظيفي للأشياء والأنظمة التقنية ؛ تتضمن هذه المجموعة من الطرق FFA (التحليل الفيزيائي الوظيفي) وتحليل FMEA. عند إجراء تحليل التكلفة الوظيفية ، يتم تحديد وظائف عناصر كائن أو نظام تقني ويتم تقييم تكاليف تنفيذ هذه الوظائف من أجل تقليل هذه التكاليف. يشمل FSA المراحل الرئيسية التالية:
1. البناء المتتالي لنماذج كائن FSA (مكون ، هيكلي ، وظيفي) ؛ عادة ما يتم بناء النماذج في شكل جدول (مصفوفة) ؛ 2. بحث النماذج ووضع مقترحات لتحسين موضوع التحليل.
مخطط إيشيكاوا(الرسم البياني السببي ، "هيكل السمكة") - أداة جودة تعمل على التمثيل المرئي لعلاقات السبب والنتيجة بين موضوع التحليل والعوامل التي تؤثر عليه.
يقع المؤثر أو المشكلة في نهاية السهم الأفقي كما هو موضح ؛ سيتم عرض الأسباب المحتملة على شكل أسهم معنونة مضمنة في سهم السبب الجذري. قد يكون لكل سهم أسهم أخرى تعرض الأسباب أو العوامل الأساسية المضمنة فيه ، والتي تقل أولويتها مع المسافة من السهم الرئيسي.

تحليل باريتو- يمكن استخدامها لتحليل الأفكار من جلسات العصف الذهني. يتم استخدامه لتحديد العديد من المشاكل الحيوية أو أسباب هذه المشاكل التي لها أكبر الأثر. يعرض مخطط باريتو بيانياً البيانات في شكل مخطط مبني بترتيب تنازلي لتكرار حدوث العناصر. عادةً ، يُظهر مخطط باريتو أن 80٪ من التأثير قد تم تفسيره بنسبة 20٪ من الأسباب ، ومن ثم يطلق عليه أحيانًا قاعدة 80/20.
التحكم في العمليات الإحصائية (SPC)- عبارة عن مجموعة من الأدوات لإدارة العمليات. بالإضافة إلى ذلك ، فهي أيضًا أداة إستراتيجية لتقليل تنوع المنتجات وتوريد المواد والمعدات والعلاقات والعمليات التي تسبب معظم مشاكل الجودة. SPCسيوضح ما إذا كانت العملية "تحت السيطرة" - أي سواء كانت مستقرة مع اختلافات عشوائية فقط ، أو "خارج نطاق السيطرة" وتتطلب الانتباه. علاوة على ذلك، SPCيحذر تلقائيًا عندما تنخفض إمكانية التحكم ويمكن أن يساعد في التخفيضات طويلة الأجل في معدلات العيوب ، وتحديد الأسباب الخاصة ، وتقليل أسباب التباين أو القضاء عليها ، وتحقيق مستويات إمكانية التحكم في أقرب وقت ممكن من الهدف. في SPC ، تشكل الأرقام والمعلومات الأساس للقرارات والإجراءات من خلال نظام صارم لتسجيل البيانات. بالإضافة إلى الأدوات اللازمة لتسجيل البيانات ، هناك أيضًا مجموعة من الأدوات لتحليل البيانات وتفسيرها ، والتي تمت مناقشة بعضها في الصفحات التالية. لا يتطلب فهم الأدوات وكيفية استخدامها معرفة مسبقة بالإحصاءات.
بطاقة التحكم.يتم استخدامه لمراقبة العمليات الخاضعة للرقابة باستخدام القيم والنطاقات. قائمة المراجعة هي بيانات مرتبة ترتيبًا زمنيًا ، مثل المبيعات والحجم وشكاوى العملاء ، وتوضح كيف تتغير القيم بمرور الوقت. في مخطط التحكم ، تتوافق كل نقطة مع قيمة فردية. فوق وتحت المتوسط ، يوجد خط تحذير علوي وسفلي وخطوط عمل (UWL ، LWL ، UAL ، LAL). تعمل هذه الحدود كإشارات وقواعد لاتخاذ القرارات ، كما تزود المشغلين بمعلومات حول العملية وحالة سيطرتها. الخريطة مفيدة كحساب تاريخي للعملية ، ومسارها ، وكأداة لتحديد التغييرات والتنبؤ بها.