Metodi di garanzia della qualità secondo. I metodi di assicurazione della qualità del prodotto variano I moderni metodi di assicurazione della qualità
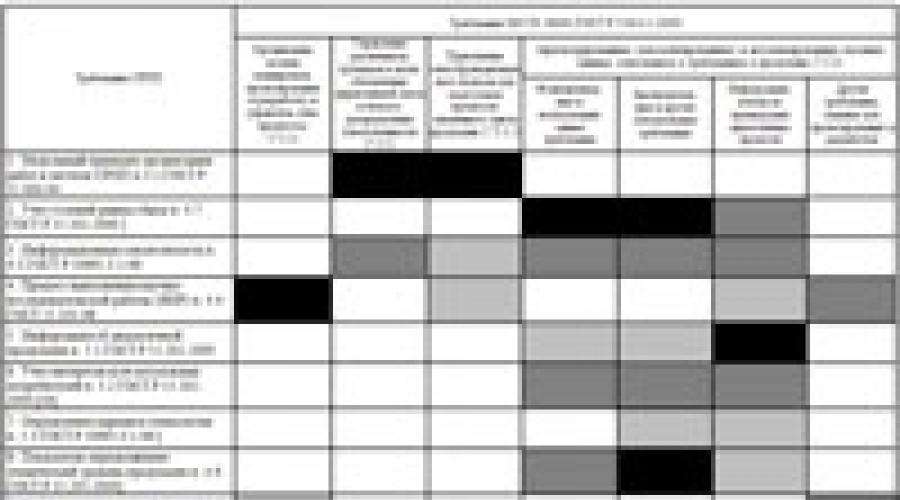
Nelle imprese di ingegneria meccanica, negli ultimi anni, è emersa una crescente esigenza di creare sistemi di gestione che non corrispondano alla norma fondamentale ISO 9001, ma che siano migliorati (ammodernati secondo le esigenze del tempo e le specificità di un particolare industria) standard per i sistemi di gestione della qualità (ad esempio gli standard di Gazprom, Ferrovie Russe, ecc.). P.).
Sebbene la maggior parte delle imprese russe abbia introdotto da tempo e gestisca con successo un sistema per lo sviluppo e la messa in produzione dei prodotti (SRPP), che soddisfi gli standard nazionali della Federazione Russa, molti consumatori oggi richiedono ai fornitori di implementare moderni sistemi di gestione della qualità incentrati su standard che tenere conto delle specificità del settore (ad esempio, lo standard internazionale ISO/TS 16949, AS 9100 e simili).
Quando si implementano questi standard, è necessario duplicare molte procedure già esistenti e operative presso l'impresa che implementano i requisiti degli standard SRPP. Non c'è dubbio che ciò comporti costi aggiuntivi irrazionali per tutti i tipi di risorse.
Il compito di ridurre il tempo, le risorse umane e finanziarie per l'attuazione dei requisiti degli standard internazionali per i metodi e le procedure per l'assicurazione della qualità utilizzando l'esperienza degli standard nazionali esistenti della Federazione Russa è oggi estremamente rilevante.
Nonostante le differenze apparentemente evidenti nelle specificità della produzione edilizia nell'industria automobilistica e in altri rami dell'ingegneria, una caratteristica comune è l'uso diffuso della fornitura di componenti ai principali impianti di assemblaggio da parte di imprese relativamente piccole.
Tali principi di organizzazione della produzione sono ben sviluppati in quasi tutti gli stabilimenti automobilistici senza eccezioni (sia nazionali che esteri), sono utilizzati anche per l'ingegneria petrolifera e del gas - in impianti che producono sistemi tecnologici complessi: impianti di perforazione, complessi per lo sviluppo di giacimenti offshore , ecc. Esempi simili possono essere trovati anche in altri settori.
A causa del fatto che le automobili sono un prodotto di una domanda di massa molto più ampia, è in questo settore che i produttori hanno dovuto prestare particolare attenzione alla creazione di sistemi di gestione della qualità che potessero corrispondere ai moderni principi di organizzazione della produzione e, inoltre, potessero contemporaneamente migliorare il prodotto qualità. . Inoltre, l'industria automobilistica ha stabilito il proprio sistema di standard di qualità del settore molto prima di quanto fosse necessario in altre aree.
È in questo contesto che il lavoro nel campo della formazione di un sistema di gestione della qualità attualmente in corso presso le imprese automobilistiche è di indubbio interesse. È più che probabile che, tenendo conto di piccoli aggiustamenti, i risultati ottenuti su di essi possano essere utilizzati in qualsiasi impianto di costruzione di macchine.
È noto che per mostrare al consumatore come l'azienda controlla la qualità dei suoi prodotti e garantisce questa qualità, i produttori creano sistemi di gestione della qualità che soddisfano i requisiti della ISO 9001, ISO / TU 16949, applicano i metodi ivi descritti.
In Russia c'è ora una tendenza al passaggio dagli standard nazionali allo standard internazionale ISO / TU 16949, che viene applicato all'industria automobilistica e alle organizzazioni che producono i pezzi di ricambio corrispondenti. Poiché ISO/TS 16949 è stato rilasciato contemporaneamente allo standard per i sistemi di gestione della qualità, ha molto in comune con quest'ultimo, ma ha anche caratteristiche proprie, poiché ISO/TS 16949 è stato sviluppato dall'International Automotive Industry Task Force (IATF) e Japan Automobile Manufacturers Association registrate come società (JAMA) con il supporto del Comitato tecnico ISO/TC 176 Gestione della qualità e assicurazione della qualità.
Le principali case automobilistiche certificano già o intendono certificare i loro sistemi di gestione della qualità secondo lo standard internazionale ISO/TU 16949 e lo richiedono ai loro fornitori. Ad esempio, i rappresentanti dei "Tre Grandi" - DaimlerChrysler, General Motors, Ford hanno presentato tali requisiti ai loro fornitori.
Va notato che l'implementazione dello standard ISO / TS 16949 richiede l'uso di metodi speciali di organizzazione del lavoro - APQP (Advanced Product Quality Planning and Control Plan - Advanced product quality planning and development of a management plan), PPAP (Production Part Approval) Processo - Processo per il coordinamento della produzione di un pezzo, ovvero l'approvazione della produzione di componenti automobilistici), nonché l'utilizzo di alcuni strumenti per garantire la qualità del prodotto mediante metodi statistici di analisi - FMEA (Metodo per la modalità di guasto potenziale e analisi degli effetti - Metodo per l'analisi dei tipi e delle conseguenze di potenziali difetti), MSA (Analisi dei sistemi di misura - Analisi dei sistemi di misura), SPC (Metodi di controllo statistico di processo - Metodi di controllo statistico di processo) e QSA (Analisi dei sistemi di gestione della qualità - Valutazione di sistemi di gestione della qualità).
Le difficoltà più gravi nelle imprese nazionali sono l'introduzione del metodo di organizzazione del lavoro APQP (Advanced Product Quality Planning), infatti, il processo di pianificazione, sviluppo e preparazione della produzione di componenti automobilistici, che consente di soddisfare assolutamente tutti i requisiti e aspettative del consumatore già nella fase di pre-produzione, quando ci sono opportunità di base Prevenzione dei difetti Le difficoltà sorgono dal fatto che questo processo interessa quasi tutti i reparti e tutti i processi dell'organizzazione e deve essere implementato in tutte le fasi della ciclo di vita del prodotto - dalla pianificazione della creazione, progettazione e sviluppo di un componente automobilistico alla sua produzione in serie.
In Russia esiste un sistema simile a quello di APQP, un sistema per lo sviluppo e la messa in produzione dei prodotti (SRPP).
Come sapete, SRPP è un insieme di norme fondamentali organizzative, metodologiche e tecniche generali interconnesse che stabiliscono le principali disposizioni, regole e requisiti che garantiscono l'unità tecnica e organizzativa del lavoro svolto nelle fasi del ciclo di vita del prodotto (LCP) , comprese la ricerca e la giustificazione per lo sviluppo di prodotti o un progetto, di fatto lo sviluppo, la produzione, il funzionamento (applicazione, immagazzinamento) dei prodotti e la riparazione (per i prodotti riparati), nonché l'interazione delle parti interessate.
SRPP è interconnesso con gli standard di altri sistemi tecnici generali e serie di standard: il Sistema unificato per la documentazione di progettazione (ESKD), il sistema unificato per la documentazione tecnologica (ESTD), il sistema unificato per la documentazione del programma (ESPD), il sistema statale per Garantire l'uniformità delle misure, supporto tecnologico per la creazione dei prodotti.
Attualmente, molti specialisti delle imprese sono preoccupati per il seguente problema: le imprese hanno già implementato e gestiscono con successo un sistema per lo sviluppo e la messa in produzione di prodotti in conformità con gli standard nazionali della Federazione Russa. Ma arriva il momento in cui un consumatore - una certa casa automobilistica - richiede al proprio fornitore di implementare un sistema di gestione della qualità secondo lo standard internazionale ISO/TU 16949, inclusa, ovviamente, l'implementazione del metodo APQP come parte integrante di tale sistema di gestione della qualità. Gli specialisti capiscono che devono duplicare molti dei processi già implementati, il che è accompagnato da costi irrazionali aggiuntivi.
Questa situazione è attivamente discussa dagli esperti che l'hanno incontrata. È vero, nella maggior parte dei casi, gli esperti parlano solo di quanto siano interessanti i requisiti delle organizzazioni internazionali (la task force internazionale dell'industria automobilistica (IATF) e i requisiti dei nostri vecchi standard nazionali di lunga data, che sono stati sviluppati negli anni ottanta e anni novanta del secolo scorso, coincidono.
Quindi, c'è un problema: come implementare i requisiti dello standard ISO / TU 16949 al costo più basso, incluso il metodo ancora esotico di organizzare il lavoro APQP per noi in un'impresa con un SRPP implementato e funzionante con successo.
Lo scopo del nostro studio era sviluppare un algoritmo per padroneggiare i sistemi internazionali di gestione della qualità presso le imprese russe, tenendo conto delle specifiche dell'esperienza precedente accumulata nel funzionamento dei sistemi domestici e, allo stesso tempo, ottimizzando il costo delle risorse di vari tipi: lavoro, finanziario, tempo, ecc.
L'autore ha analizzato il grado di compatibilità dei requisiti della norma ISO/TU 16949 e del metodo APQP con i requisiti delle norme nazionali SRPP. Per fare ciò, sono state costruite le matrici di conformità ai requisiti dei due sistemi precedenti, in cui 45 righe soddisfano i requisiti dell'SRPP e 49 colonne ciascuna soddisfano i requisiti ISO / TU 16949 e APQP. Ciascun elemento dell'intersezione di righe e colonne è stato ulteriormente analizzato mediante una combinazione di giudizio di esperti e metodi di analisi di regressione.
Per una comprensione più accurata di quale fosse il grado di generalizzazione dei requisiti, come i requisiti del metodo APQP sono stati classificati in gruppi e quali requisiti del SRPP sono stati considerati per la loro compatibilità con i requisiti del processo APQP, consideriamo un piccola parte della matrice in una forma più ingrandita. Un frammento della matrice è presentato in Tabella 2.
Tabella 2 - Frammento della matrice di compatibilità dei requisiti di SRPP e ISO/TU 16949
Come risultato dell'analisi, è emerso che in alcuni casi vi è compatibilità (totale o parziale) dei requisiti della ISO/TU 16949 e APQP con i requisiti dell'SRPP e viceversa. Pertanto, ulteriormente, è stata effettuata una valutazione quantitativa del grado di compatibilità dei requisiti della ISO/TS 16949 e del metodo APQP, che ha mostrato che la completa corrispondenza dei requisiti è stata riscontrata nel 15% dei casi, e la parziale corrispondenza di requisiti - nel 13% dei casi. Inoltre, sono state individuate situazioni in cui i requisiti possono fungere da base per l'implementazione di standard internazionali: il gruppo di requisiti di ISO / TU 16949 e APQP non coincide direttamente con i requisiti dell'SRPP, ma se questi ultimi sono in qualche modo integrati , allora si verificherà una coincidenza totale o parziale . C'era circa il 22% di tali situazioni. Infine, il numero di casi con una corrispondenza minore è del 12% e nessuna corrispondenza è stata trovata nel 38% dei casi.
Ad esempio, la clausola 5.2 di GOST R 15.201-2000 afferma quanto segue: "Si raccomanda che i termini di riferimento tengano conto degli interessi di tutti i possibili consumatori". A sua volta, è necessario disporre di "informazioni da consumatori specifici" come informazioni di input nella prima fase del metodo APQP. Durante lo studio, è stata riconosciuta una completa coincidenza dei requisiti.
Un altro esempio: nella clausola 4.6 di GOST R 15.201-2000 è richiesto che uno sviluppatore di prodotti, quando conduce attività di ricerca, sviluppo e tecnologia, debba prestare particolare attenzione a garantire, in particolare, i requisiti per la contabilizzazione degli indicatori di prodotto che lo determinano livello tecnico. Il processo APQP fa riferimento a benchmark per prodotti/processi concorrenti. In questo caso è stata riconosciuta una parziale sovrapposizione dei requisiti. La situazione è simile con requisiti come lo sviluppo tecnologico obbligatorio dei prodotti in conformità con la clausola 5.2.6 di GOST R 50995.3.1-96 e la necessità di un "assunto su prodotti e processi" in conformità con i requisiti del metodo APQP .
Sulla base dei risultati di questo lavoro, si può trarre la seguente conclusione: quando si implementa ISO / TU 16949 e il metodo di organizzazione del lavoro APQP nelle imprese con un SRPP implementato e funzionante con successo, i costi delle risorse possono essere notevolmente ridotti.
La riduzione dei costi può essere ottenuta grazie al fatto che quegli elementi del controllo del processo di pre-produzione che sono già implementati nell'impresa in conformità con i requisiti degli standard SRPP non devono essere nuovamente implementati se previsti al momento dell'applicazione ISO/TS 16949 e APQP. Basterà chiarire la differenza terminologica nella documentazione dell'impresa. Siamo tutti ben consapevoli che un tale approccio può far risparmiare significativamente sia il tempo per l'implementazione della ISO / TS 16949 che del metodo APQP, e ridurre le risorse umane e materiali necessarie per l'implementazione.
Si segnala che è stata effettuata un'analisi piuttosto superficiale della situazione attuale. In particolare, i requisiti delle norme SRPP sono stati suddivisi in soli 45 gruppi, i requisiti della ISO/TU 16949 e il metodo APQP - in 49 gruppi, il che probabilmente non è sufficiente per valutare appieno la compatibilità dei requisiti della ISO/TU 16949 e APQP con i requisiti degli standard SRPP; Si segnala inoltre che per valutare la compatibilità dei requisiti è stata utilizzata una scala composta da sole 5 categorie, che fornisce anche solo una valutazione approssimativa della compatibilità dei requisiti.
Va inoltre notato che, a seconda delle specificità dell'impresa e della direzione generale delle sue attività, la procedura per l'attuazione di vari requisiti sia degli standard SRPP che dei requisiti ISO / TU 16949 e APQP può essere diversa. Ma, allo stesso tempo, va tenuto presente che alcuni requisiti possono essere interconnessi e quindi c'è un ordine innegabile per la loro attuazione. Questa situazione deve essere presa in considerazione nell'attuazione congiunta degli standard SRPP e ISO / TU 16949.
Alla luce di quanto sopra, è stato sviluppato uno schema di organizzazione della produzione, che abbiamo chiamato “modello organizzativo” (Figura 1). Il modello organizzativo consente di determinare la sequenza delle azioni nella fase di progettazione, sviluppo e messa in produzione dei prodotti e nella produzione dei prodotti, identificare e localizzare i colli di bottiglia, intraprendere azioni specifiche per eliminarli, allocare responsabilità e autorità all'interno di entrambe le unità responsabile della produzione dei prodotti e di tutta l'organizzazione.
Figura 1 - Modello organizzativo "Gestione della produzione e del servizio"
Il modello organizzativo sviluppato è applicabile a qualsiasi impresa industriale. Il modello organizzativo può essere utilizzato per determinare l'ordine di attuazione e per la distribuzione del lavoro quando si introducono moderni metodi di gestione della qualità in un'impresa di costruzione di macchine che dispone di un sistema di gestione operativo basato sugli standard implementati del sistema nazionale SRPP.
L'analisi, inoltre, non ha tenuto conto di un fattore come alcune imprecisioni e convenzioni nella traduzione del testo che descrive il metodo APQP. In una situazione del genere, può essere molto difficile prendere in considerazione i sinonimi quando si presentano i requisiti: dopotutto, alcuni requisiti possono anche coincidere completamente, ma allo stesso tempo essere espressi con parole completamente diverse.
I risultati dell'analisi consentono di sviluppare un algoritmo specifico per l'implementazione dei requisiti degli standard internazionali, tenendo conto del sistema SRPP operante presso le imprese, che può ridurre significativamente i tempi, le risorse umane e finanziarie e allo stesso tempo utilizzare l'enorme bagaglio lasciatoci dai nostri predecessori - ingegneri sovietici - sviluppatori di standard nazionali. Questo algoritmo sarà descritto nella prossima pubblicazione dell'autore.
Natalia Viktorovna VASHCHENKO— Capo del Dipartimento di Certificazione e Organizzazione del Lavoro del Centro di Coordinamento ANO "ATOMVOENSERT"
Elenco delle fonti utilizzate
1 Kudryashov AV Tavola rotonda. APQP: problemi ed esperienza di implementazione // Metodi di gestione della qualità. - 2012. - N. 6.
2 Kershenbaum V.Ya., Vashchenko N.V. Metodologia per valutare la compatibilità dei requisiti normativi della prassi nazionale ed estera nella costruzione di sistemi di gestione della qualità // Gestione della qualità nel complesso petrolifero. - 2013. - N. 1. - Con. 17 - 21.
3 Vashchenko N.V. Sulla fattibilità di una procedura documentata nell'ambito dell'attuazione dei requisiti della settima sezione della ISO 9001:2008 // Gestione della qualità nel complesso del petrolio e del gas. - 2013. - N. 2. - Con. 14 - 18.
Numerose statistiche sulla qualità indicano che la difettosità dei prodotti è circa l'85-90% causata dal fattore umano. Consideriamo quali ragioni legate al lavoratore possono pregiudicare la non conformità alla documentazione tecnica, fino al matrimonio dei prodotti. Tra questi, si possono notare: scarsa qualificazione, breve esperienza lavorativa, cattiva salute, disattenzione nella lettura di disegni, tecnologie o istruzioni, scarsa preparazione del posto di lavoro.
Va sottolineato che le cause del matrimonio possono essere associate non solo a una persona, ma anche a uno strumento, attrezzature tecnologiche, attrezzature. Questo è vero, ma molto spesso ciò accade non tanto a causa delle carenze dello strumento, dell'attrezzatura o dell'attrezzatura stessa, ma a causa della loro affilatura incurante, riparazioni scadenti o produzione e assemblaggio imprecisi eseguiti dai lavoratori. Se "scavi" il colpevole del difetto, nella stragrande maggioranza sarà una persona che non lavora necessariamente nella tua impresa, ma anche, possibilmente, presso l'impresa del fornitore.
Da dove dovrebbe iniziare il miglioramento della qualità? Gli esperti giapponesi consigliano di iniziare con la qualità sul posto di lavoro. Inoltre, hanno sviluppato un sistema coerente di miglioramento della qualità sul posto di lavoro, che hanno chiamato "5S" ("Buone pratiche di pulizia"). Il nome deriva da cinque parole giapponesi che iniziano con la lettera "S": "seiri" (smistamento), "seiso" (pulizia), "seiton" (organizzazione), "seiketsu" (standardizzazione), "shitsuke" (autoesame). ). La traduzione russa di queste parole fornisce, se non un'idea abbastanza chiara, abbastanza sufficiente del contenuto approssimativo delle misure per migliorare la qualità sul posto di lavoro. Se caratterizziamo brevemente questo sistema, possiamo dire che "prima di iniziare il lavoro, e anche il lavoro responsabile, è necessario occuparsi dell'ordine sul posto di lavoro".
Diamo un contenuto più chiaro di ciascuna delle fasi del sistema "5S". Prima di procedere alla sua realizzazione, è necessario descrivere in dettaglio e, se possibile, fotografare l'area di lavoro (o luogo di lavoro) che necessita di essere riorganizzata. Il confronto delle descrizioni delle aree di lavoro (luoghi) prima e dopo la trasformazione può fornire al management un'impressione favorevole che attiva il lavoro di qualità nell'impresa.
Fase 1. Ordinamento. Metti le cose (o gli oggetti) che vengono utilizzati quotidianamente in un unico posto. Gli oggetti usati una volta alla settimana dovrebbero essere collocati in un altro posto, mensilmente - nel terzo, e ciò che è necessario molto raramente - nel quarto. Eseguire questa procedura per ciascuna zona del posto di lavoro. Quindi, da ogni luogo di stoccaggio, seleziona e lascia una copia di ogni tipo di articolo e trasferisci il resto nell'armadio per conservare i pezzi di ricambio.
Fase 2. Pulizia. Pulisci tutte le superfici di lavoro prima di riapplicare qualsiasi cosa. Assicurarsi che vi siano contenitori per rifiuti idonei vicino al luogo di lavoro. Collocare tutti i pezzi di ricambio nel magazzino generale. Fare un elenco degli articoli restituiti al magazzino per poterli segnalare alla direzione dell'officina. Organizza e metti in un unico posto tutti i documenti necessari e pulisci tutti gli strumenti. Stabilire standard di pulizia (norme) che devono essere osservati da ciascun dipendente.
Fase 3. Organizzazione. Organizza ordinatamente tutti i documenti e le cartelle. Gli articoli che vengono utilizzati quotidianamente dovrebbero essere a portata di mano del lavoratore. Gli oggetti usati una volta alla settimana possono essere posizionati a una distanza di un gradino e quelli usati una volta al mese a una distanza di 2-3 gradini. Tutto il resto può essere localizzato a pochi passi dal posto di lavoro. È necessario definire chiaramente il luogo di ogni articolo.
Fase 4. Standardizzazione. Familiarizzare tutti i dipendenti associati a questo luogo di lavoro con gli standard di pulizia e pubblicare foto con l'ambiente standard "corretto". Ove necessario, dotare attrezzature e strumenti di coperture trasparenti antipolvere. Se tali coperture sono opache, è probabile che i lavoratori ripongano sotto di esse articoli che non sono correlati al luogo di lavoro.
Fase 5. Autotest. Dopo circa un mese, ispezionare attentamente le condizioni del luogo di lavoro per migliorarlo. Se ci sono articoli extra, inviali al magazzino generale. Rivedere gli standard di purezza e rivederli se necessario. Ripetere questo passaggio dopo un mese.
Puoi anche raccomandare misure aggiuntive per mantenere l'ordine sul posto di lavoro. Così, ad esempio, puoi creare tavole mobili con strumenti per lavori specifici, oppure disegnare i contorni degli strumenti sulle tavole in modo che sia subito chiaro quale utensile manca.
I ricercatori giapponesi ritengono che se i manager di un'azienda non possono implementare le "5S", non possono gestirla in modo efficace. Al contrario, se riesci a padroneggiare questo sistema, significa che puoi implementare altrettanto con successo altri sistemi più complessi. La ragione di questa conclusione è che il sistema 5S non richiede personale speciale di manager per la sua attuazione e non diventerà effettivo fino a quando tutto il personale non sarà coinvolto e inizierà a pensare al successo di questo sistema. Ma se il sistema 5S è già stato implementato, allora possiamo presumere che altri sistemi siano quasi per metà assimilati (in termini di disponibilità del personale ad attuare le modifiche).
Dalla metà degli anni '80. 20 ° secolo nelle aziende giapponesi, il sistema 5S è stato centrale nel pensiero e nella filosofia del management. Il management delle aziende ovunque è giunto alla conclusione che questo sistema è un metodo di gestione chiave in qualsiasi campo di attività, anche il più high-tech.
Il sistema 5S ha guadagnato ampia popolarità nelle imprese russe negli ultimi anni. Dalla prassi interna di attuazione di questo sistema si possono trarre le seguenti conclusioni:
- - è applicabile e può essere implementato con successo nelle imprese nazionali e nelle organizzazioni di varie forme di proprietà con l'interesse della direzione in questo;
- - il contenuto dei principi del sistema e la tecnologia della sua attuazione richiedono un adattamento significativo alle peculiarità dell'economia domestica, ai metodi di organizzazione della produzione e alla mentalità del personale;
- - la possibilità di una corretta attuazione del sistema dipende direttamente dalle condizioni socio-economiche di lavoro sul luogo di lavoro, ad es. il livello e la regolarità del pagamento dei salari, il carico sistematico e ritmico della produzione, il rispetto da parte dell'amministrazione di almeno i requisiti fondamentali per condizioni di lavoro sicure.
Sono stati fatti tentativi per modernizzare questo sistema, tenendo conto dei principi dell'organizzazione scientifica del lavoro e della pratica del miglioramento della qualità. Il nuovo sistema, che incorporava elementi del sistema “5S” e si adattava alle condizioni di produzione nazionale, è stato denominato “Ordinazione” (Tabella 2.4). I principi fondamentali di questo sistema sono i seguenti:
- - rimuovere tutto ciò che non è necessario;
- - effettuare regolarmente un'accurata pulizia e controllare la funzionalità delle attrezzature e dell'inventario;
- - posizionare tutto sul posto di lavoro nel modo più conveniente;
- - sviluppare standard (regole) per lo stoccaggio, l'uso, la pulizia e l'ispezione;
- - seguire costantemente e consapevolmente le regole accettate.
Tabella 2.4
Confronto dei principi dei sistemi "5S" e "Ordering".
1. Partecipazione di tutta la squadra. Così come è impossibile "far bollire l'acqua in un angolo della piscina", così questo sistema non può essere implementato efficacemente in un posto di lavoro o in un'unità a volontà di una sola persona. Il nuovo sistema richiede determinazione e coerenza delle azioni di tutta la squadra.
Ogni regola del sistema che deve essere eseguita non è di per sé difficile. La difficoltà sta nel non fermarne l'attuazione. Ciò richiede tenacia e cooperazione, che a loro volta creano un senso di appartenenza al team e migliorano il clima aziendale.
2. Facilità di sviluppo - apparente. I principi del sistema "Ordinazione", a prima vista, sembrano così chiari e facili da implementare. Ma perché sono così difficili da implementare?
L'apparente facilità di attuazione di questi principi è dovuta al fatto che i dipendenti non comprendono appieno cosa sia il sistema di "Ordinazione". Questa non è una pulizia generale una tantum, non lo spostamento di strumenti da un luogo all'altro, ma uno stile fondamentalmente nuovo di atteggiamento nei confronti dell'ambiente di lavoro, della sua organizzazione e sicurezza, lo stile di mantenere costantemente uno spazio di lavoro altamente organizzato e pulito.
3. Dalla correzione alla prevenzione. Spesso puoi vedere quanto tempo dedicano i manager a correggere ciò che è stato fatto di sbagliato o fuori tempo. Reagiscono alle avversità dopo il fatto. Ma quando conosciamo i problemi, diventa chiaro che le cause di molti di loro sono spesso cose molto semplici.
Violazioni tempestivamente rilevate nel funzionamento delle apparecchiature, malfunzionamenti identificati delle apparecchiature o dell'inventario possono prevenire grandi perdite e incidenti. Anche alcune "piccole cose" in una serie di circostanze sfavorevoli possono portare grossi problemi.
- 4. Dalla gestione basata sui risultati - per elaborare il controllo. Molto spesso, i manager tendono a vedere solo i risultati delle attività ea giudicare l'efficacia del loro lavoro. Quando si implementa il sistema "Ordinazione", è necessario imparare a vedere le ragioni che portano a determinati risultati, a vedere l'intero processo nel suo insieme, i suoi punti di forza e di debolezza.
- 5. Enfasi sul rispetto dei requisiti elementari. Il personale deve abituarsi al costante adempimento dei requisiti elementari. Ad esempio, verificando la presenza di tutte le iscrizioni e le etichette su oggetti o oggetti importanti.
- 6. Rafforzare la responsabilità di ciascun dipendente per i risultati del proprio lavoro. G. Ford una volta disse che "anche il lavoratore più stupido può trovare cento modi per ingannare l'artigiano più abile". Ciò conferma che solo il fattore della responsabilità personale del lavoratore e del suo interesse per il lavoro può svolgere un ruolo molto positivo nella produzione, e non una regolamentazione costante del lavoro e un controllo rigoroso. Abbiamo bisogno di un'atmosfera in cui le persone si aiutino a vicenda e tutti cerchino di fare un buon lavoro.
- 7. Comprendere le istruzioni e seguire i loro requisiti. Molto spesso, le istruzioni e i requisiti non vengono seguiti, non perché i dipendenti li trascurino, ma perché non conoscono o non comprendono appieno l'essenza dei requisiti o delle raccomandazioni in essi contenuti.
Il sistema di ordinazione consente ai dipendenti di sviluppare autonomamente regole e istruzioni specifiche in relazione ai propri luoghi di lavoro.
8. Approccio graduale (passo dopo passo).È ovvio che il sistema "Ordering", che è principalmente incentrato sul cambiamento degli stereotipi comportamentali dei dipendenti, non può essere implementato rapidamente e subito dopo l'inizio della sua attuazione, porta risultati tangibili. Il nuovo sistema è il primo passo verso un programma di ripristino aziendale a lungo termine.
La tecnologia di implementazione del sistema prevede la padronanza metodica, graduale e graduale dei suoi principi, la valutazione e il consolidamento dei risultati di ogni fase.
9. Sistema "Ordinazione» - è un percorso difficile. Il nuovo sistema, come il giapponese "5S", funziona secondo il principio: "Le azioni parlano più delle parole". Ogni grande lavoro inizia con un piccolo atto, con una comprensione graduale dell'essenza del problema, con errori e correzioni. Non dovresti mai rifiutare aiuto, consigli, supporto da parte di colleghi e personale tecnico. Avanzamenti reali a passi graduali, anche piccoli, sono molto più utili delle discussioni globali su un grande progetto che può trasformare la struttura della produzione in un determinato luogo di lavoro.
Gli approcci metodologici sopra discussi non solo rivelano il contenuto e la tecnologia per l'attuazione dei principi del sistema "Ordinazione", ma spiegano piuttosto gli ostacoli, le difficoltà e le difficoltà che si incontreranno nel percorso di attuazione sia di questo sistema che del sistema "5S" .
Se per un dipendente giapponese basta avere la certezza del management aziendale che l'introduzione del sistema "5S" porterà grandi benefici non solo all'azienda, ma anche al dipendente stesso, in modo che venga trasportata la motivazione a lungo termine per implementare nella pratica gli elementi di questo sistema, questo chiaramente non è sufficiente per un dipendente di un'impresa russa. . Occorrono meccanismi efficaci che stimolino il miglioramento dei posti di lavoro e il miglioramento della qualità dei prodotti e della manodopera in ogni luogo di lavoro. Come sempre, nelle imprese russe, tutto ciò che riguarda il miglioramento, la razionalizzazione, compresi i posti di lavoro, si basa praticamente non sul sistema, non su incentivi efficaci, ma esclusivamente sull'iniziativa personale. Una questione così seria come l'introduzione dei sistemi "5S" o "Ordering" non può essere "spifferata" solo dagli appassionati di fabbrica.
C'è un'opinione secondo cui se tutto il lavoro potesse essere svolto "urgentemente", la Russia non avrebbe concorrenti qui, mentre il lavoro associato al lavoro scrupoloso quotidiano per ristabilire l'ordine e la pulizia non corrisponde alla nostra mentalità. Da qui la necessità di una spiegazione dettagliata, attraverso approcci metodologici, di come svolgere essenzialmente un lavoro abbastanza semplice, che sono i principi del sistema "Ordinazione".
Se vogliamo vivere in modo civile, come, ad esempio, in Giappone o in Europa, allora i nuovi dirigenti devono convincere i lavoratori che la qualità del lavoro non dipende dalla mentalità della nazione, ma dalla capacità e dalla voglia di rispettare tutti i requisiti registrati sia nelle specifiche tecniche dei prodotti che nelle norme internazionali ISO 9000. E non solo per ispirare, ma anche per garantire dal punto di vista organizzativo e materiale l'attuazione delle norme necessarie.
Come risultato dello studio del materiale in questo capitolo, lo studente dovrebbe:
sapere
- sette strumenti per il controllo della qualità del prodotto;
- metodi statistici di controllo della qualità del prodotto;
- analisi dei costi funzionali;
- moderne tecnologie di gestione della qualità (concetto six sigma, metodo QFD, ecc.);
essere in grado di
- costruire un diagramma causale di Ishikawa e un diagramma di Pareto per gestire la qualità di beni e servizi;
- applicare il metodo QFD per tenere traccia delle esigenze dei consumatori in tutte le fasi del ciclo di vita del prodotto;
- applicare l'analisi dei costi funzionali al fine di ottenere le necessarie proprietà di consumo dei beni (servizi) con costi minimi per la loro fornitura;
possedere
- abilità nell'applicazione di sette strumenti per il controllo della qualità delle merci che entrano nel commercio;
- metodi statistici di gestione della qualità delle merci che entrano in commercio.
Significato e classificazione dei metodi
Come notato sopra, nel cap. 2, uno dei principi di SM K è che la base per prendere una decisione dovrebbe essere solo i fatti, non l'intuizione. Una delle ragioni degli errori nella gestione della qualità è che i fatti sono confusi con i giudizi soggettivi. Per prevenire errori, è necessario organizzare il processo di ricerca dei fatti, ad es. materiale statistico.
I problemi di raccolta, elaborazione e analisi dei risultati sono affrontati dalla statistica matematica, che include un numero enorme di metodi diversi. Scienziati giapponesi (principalmente il professor K. Ishikawa) hanno scelto da questo set sette strumenti di base per il controllo della qualità(Fig. 4.1). I circoli di qualità hanno svolto un ruolo importante nello sviluppo di metodi statistici in Giappone.
Riso. 4.1.
Con la crescita dei volumi di produzione nella produzione in serie e in serie dei prodotti, il consumatore (in quanto persona giuridica) e lo stesso produttore avevano bisogno di informazioni sulla reale qualità dei prodotti fabbricati e acquistati. Tuttavia, a causa dell'elevato volume di lotti di prodotti fabbricati, il controllo qualità completo era difficile da eseguire e la sua affidabilità era bassa. Al fine di ridurre l'intensità del lavoro e aumentare l'affidabilità, hanno iniziato ad applicare metodi statistici di controllo selettivo della qualità. Il loro significato è estremamente semplice: dopo aver studiato una piccola parte dei prodotti (campione), si possono trarre conclusioni attendibili sulla qualità dell'intero lotto.
Tra la fine degli anni '70 e l'inizio degli anni '80. L'Unione degli scienziati e degli ingegneri giapponesi ha sviluppato una serie più sofisticata di strumenti di controllo della qualità. Questi strumenti erano basati sia sui metodi della statistica matematica che sui metodi di altre scienze: analisi operativa, teoria dell'ottimizzazione, ecc. In quanto strumenti più sottili, erano rivolti allo staff tecnico. Questi metodi sono chiamati strumenti di gestione della qualità. Questo tutorial copre alcuni degli strumenti di gestione della qualità: "Six setacci", tecnologia di implementazione delle funzioni di qualità, analisi dei costi.
Di seguito sono descritti tre gruppi di metodi:
- 1) strumenti di base per il controllo della qualità;
- 2) metodi statistici di controllo selettivo della qualità;
- 3) strumenti di gestione della qualità.
Strumenti di base per il controllo della qualità
I principali strumenti di controllo della qualità sono metodi di analisi statistica delle condizioni e dei fattori che influenzano la qualità del prodotto. L'analisi statistica include un'analisi dei tipi e delle cause del matrimonio, un'analisi dell'influenza dei singoli fattori del processo tecnologico sugli indicatori di qualità. Durante l'analisi, si consiglia di utilizzare metodi grafici speciali (a volte chiamati statistiche descrittive) per visualizzare i dati di qualità. Questi metodi includono sette strumenti di controllo della qualità (vedi Figura 4.1).
Foglio di controllo (foglio)- uno strumento per la raccolta e l'organizzazione dei dati per facilitare l'ulteriore utilizzo delle informazioni raccolte.
Sulla fig. 4.1, il foglio di controllo non si trova accidentalmente al centro, circondato dagli altri 6 utensili. Svolge un ruolo speciale, perché l'implementazione di qualsiasi attività di analisi della qualità inizia con la raccolta dei dati iniziali.
Foglio di controllo - un modulo cartaceo su cui sono prestampati tipi controllati di difetti (nel nostro caso, sull'esempio dei difetti nella decorazione dei prodotti ceramici), che indicano sotto forma di semplici simboli la frequenza del loro verificarsi.
Il numero di diversi volantini nell'impresa è di centinaia, e per ogni scopo specifico, infatti, è possibile sviluppare un proprio volantino. Ma il principio del loro design rimane invariato: la forma del foglio dovrebbe essere semplice e comprensibile (senza ulteriori spiegazioni); è necessario indicare chi, in quale fase e per quanto tempo i dati raccolti.
Ovviamente, la qualità dei prodotti è l'indicatore principale dell'attività di qualsiasi impresa. Per mantenere la competitività di beni e servizi, lo sviluppo di un sistema di gestione della sicurezza alimentare oggi utilizza una varietà di, per lo più economici e matematici. Ad esempio, la programmazione dinamica, lineare e non lineare, la modellazione della simulazione, la progettazione di esperimenti, la teoria delle code e dei giochi, l'analisi dei costi funzionali, il metodo Taguchi e il metodo di strutturazione della qualità.
Lascia una richiesta per una consulenza gratuita
Metodo di distribuzione della funzione di qualità - QFD (Distribuzione della funzione di qualità). Si tratta di un approccio sistematico all'identificazione dei requisiti dei clienti che aiuta un'azienda a comprendere e integrare l'individuazione dei requisiti in specifici piani di erogazione dei servizi. A differenza di altri metodi, QFD è un metodo di assicurazione della qualità che prevede di soddisfare le esigenze del cliente nella costruzione di matrici ricci, in seguito chiamate "case di qualità", all'interno delle quali vengono registrate informazioni sulla qualità del servizio e sulle decisioni prese. Questo metodo è una tecnologia per la progettazione di prodotti e processi che consente di convertire i desideri del consumatore in requisiti tecnici per prodotti e parametri dei loro processi produttivi. Il metodo QFD è un metodo esperto che utilizza un modo tabulare di presentare i dati e con una forma specifica di tabelle, che vengono chiamate "case di qualità". L'idea principale della tecnologia QFD è la comprensione dell'esistenza di una grande differenza tra le proprietà del consumatore ("indicatori di qualità effettivi") e i parametri del prodotto stabiliti negli standard ("indicatori di qualità ausiliari"). Gli indicatori di qualità ausiliari sono importanti per il produttore, ma non sempre essenziali per il consumatore. Il caso ideale sarebbe quando il produttore potrebbe controllare la qualità del prodotto direttamente dagli indicatori effettivi, ma questo di solito non è possibile, quindi utilizza indicatori ausiliari.
La tecnologia QFD è una sequenza di azioni da parte di un produttore per convertire gli indicatori di qualità del prodotto effettivi in requisiti tecnici per prodotti, processi e apparecchiature. Lo strumento principale della tecnologia QFD è un tavolo di tipo speciale, chiamato "casa della qualità". Questa tabella mostra la relazione tra indicatori di qualità effettivi (proprietà del consumatore) e indicatori ausiliari (requisiti tecnici):
L'applicazione del metodo QFD consente di tenere conto delle esigenze del consumatore in tutte le fasi della produzione dei prodotti finiti, per tutti gli elementi del sistema qualità dell'organizzazione e, quindi, aumentare il grado di soddisfazione del cliente, ridurre i costi dei processi di progettazione e preparazione dei prodotti per la produzione.
Metodo FSAè una tecnologia di analisi dei costi per consentire al prodotto di svolgere le sue funzioni; La FSA viene eseguita per prodotti e processi esistenti al fine di ridurre i costi, nonché per prodotti in fase di sviluppo al fine di ridurne i costi. Il metodo FSA è stato utilizzato attivamente nell'industria sin dagli anni '60, principalmente negli Stati Uniti. Il suo utilizzo ha permesso di ridurre il costo di molte tipologie di prodotti senza ridurne la qualità e di ottimizzare i costi di fabbricazione. Ora FSA è uno dei tipi più popolari di analisi di prodotti e processi. FSA è uno dei metodi di analisi funzionale di oggetti e sistemi tecnici, lo stesso gruppo di metodi include FFA (analisi fisica funzionale) e analisi FMEA. Quando si esegue un'analisi dei costi funzionali, vengono determinate le funzioni degli elementi di un oggetto tecnico o di un sistema e vengono valutati i costi di implementazione di tali funzioni al fine di ridurre tali costi. La conduzione della FSA comprende le seguenti fasi principali:
1. Costruzione coerente di modelli dell'oggetto FSA (componente, strutturale, funzionale); i modelli sono generalmente costruiti in forma tabulare (matrice); 2. Studio di modelli e sviluppo di proposte per il miglioramento dell'oggetto di analisi.
Diagramma di Ishikawa(diagramma di causa ed effetto, "lisca di pesce") - uno strumento di qualità che serve a visualizzare le relazioni di causa ed effetto tra l'oggetto di analisi ei fattori che lo influenzano.
Il fattore o il problema influente si trova, come mostrato, alla fine della freccia orizzontale; le possibili cause verranno visualizzate come frecce etichettate che sono incluse nella freccia della causa principale. Ogni freccia può avere anche altre frecce che mostrano le principali cause o fattori in essa inclusi, la cui priorità diminuisce con la distanza dalla freccia principale.

Analisi Paretiana- Può essere utilizzato per analizzare le idee del brainstorming. Viene utilizzato per identificare alcuni problemi vitali o le cause di quei problemi che hanno il maggiore impatto. Il grafico di Pareto rappresenta visivamente i dati sotto forma di un grafico costruito in ordine decrescente della frequenza di occorrenza degli elementi. In generale, il grafico di Pareto mostra che l'80% dell'influenza è dovuto al 20% delle cause, quindi a volte viene chiamata regola 80/20.
Controllo statistico di processo (SPC)- è un insieme di strumenti per la gestione dei processi. Inoltre, è anche uno strumento strategico per ridurre la variabilità dei prodotti, l'approvvigionamento dei materiali, le attrezzature, le relazioni ei processi che sono la causa della maggior parte dei problemi di qualità. SPC mostrerà se il processo è "sotto controllo" - ad es. se è stabile con solo variazioni casuali o "fuori controllo" e necessita di attenzione. Inoltre, SPC avverte automaticamente quando la controllabilità sta diminuendo e può aiutare con la riduzione del tasso di difetto a lungo termine, identificando le cause speciali, riducendo o eliminando le cause di variazione e raggiungendo livelli di controllabilità il più vicino possibile all'obiettivo. In SPC, i numeri e le informazioni costituiscono la base per il processo decisionale e l'azione attraverso un accurato sistema di registrazione dei dati. Oltre agli strumenti necessari per registrare i dati, esiste anche una serie di strumenti per l'analisi e l'interpretazione dei dati, alcuni dei quali sono discussi nelle pagine seguenti. Comprendere gli strumenti e come utilizzarli non richiede una conoscenza preliminare delle statistiche.
Carta di controllo. Viene utilizzato per monitorare i processi controllati utilizzando valori e intervalli. Un grafico di controllo presenta dati come vendite, volume, reclami dei clienti presentati in ordine cronologico e mostra come i valori cambiano nel tempo. Nella carta di controllo, ogni punto corrisponde a un valore individuale. Al di sopra e al di sotto della media, la linea di avviso superiore e inferiore e le linee di azione (UWL, LWL, UAL, LAL) passano. Questi confini fungono da spunti e regole decisionali e forniscono agli operatori informazioni sul processo e sul suo stato di controllo. La mappa è utile come registrazione storica di un processo, come è progredito e come mezzo per identificare e prevedere il cambiamento.