Совершенствование ремонта легковых автомобилей с разработкой приспособления для окраски кузовных элементов. Совершенствование процесса технического обслуживания и ремонта оборудования (торо)
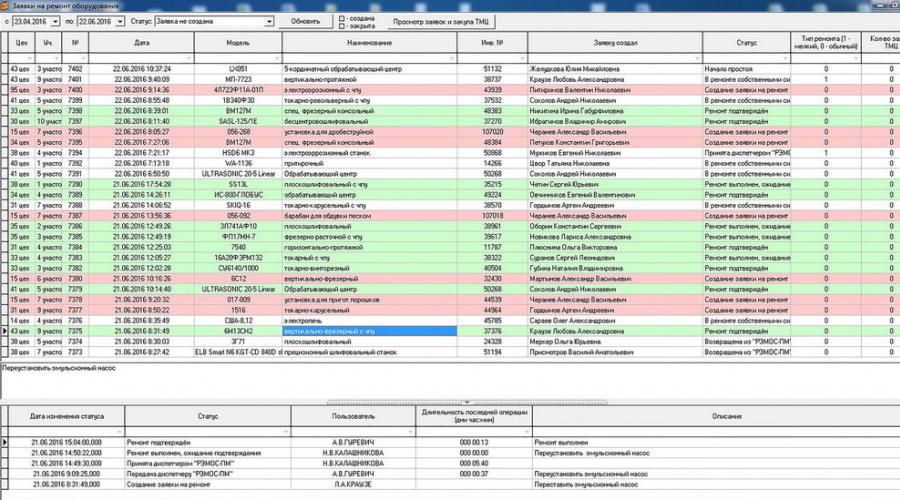
Читайте также
1. Основные аспекты планирования и анализа производства в ремонтно-механических цехах
1.1 Общая характеристика ремонтно-механических цехов и содержание выполняемых ими работ
Цехом называется организационно и технологически обособленное звено предприятия, выполняющее определенную часть производственного процесса, либо изготовляющее какой-либо вид продукции завода. В соответствии с назначением производственных процессов, выполняемых цехами, различают основные, вспомогательные и обслуживающие хозяйства.
К основным относятся те цехи, в которых выполняются основные производственные процессы, т.е. связанные с изготовлением продукции и производственных услуг, составляющих программу завода. К вспомогательным относят инструментальные, модельные, ремонтно-механические и др.; к обслуживающим хозяйствам складское, транспортное хозяйство и др.
Таким образом, ремонтно-механический цех является вспомогательным цехом основной задачей которого, является поддержание всего оборудования в рабочем состоянии, своевременный его ремонт и модернизацию. В цехе осуществляется ремонт основного и вспомогательного, подъёмно-транспортного и другого оборудования, которым располагает завод.
В деятельности ремонтного цеха техническое обслуживание (ТО) оборудования должно стоять на первом месте, а ремонт, на который нельзя смотреть как на самоцель, на втором.
Формы организации ремонтных работ
Большое значение для действующего производства имеет форма организации ремонтных работ. Все виды ремонтов за исключением капитального выполняются на месте установки ремонтируемого оборудования. Для капитального ремонта станки массой до 2,5 т перевозятся в ремонтно-механический цех, более тяжелые ремонтируются на месте. Для сокращения простоя оборудования в среднем и капитальном ремонтах применяют узловой метод ремонта, при котором узлы с оборудования снимают и устанавливают на него ранее отремонтированные с другого аналогичного оборудования. Весь объем ремонтных работ распределяется между ремонтно-механическим цехом и ремонтными базами производственных цехов. В зависимости от типа производства, размера завода и характера оборудования применяется централизованная, децентрализованная и смешанная формы организации ремонтных работ.
При централизованной форме организации ремонтных работ все работы по ремонту и модернизации оборудования выполняются только в ремонтно-механическом цехе. Ремонтные базы цехов выполняют лишь работы, связанные с проведением осмотров и межремонтного обслуживания. Такая форма организации применяется, на заводах с небольшими цехами в основном мелкосерийного производства (в частности на ФГУП «Калугаприбор»). При децентрализованной форме организации ремонтных работ почти все работы по ремонту и модернизации оборудования выполняются ремонтными базами производственных цехов. В ремонтно-механическом цехе изготовляют запасные части и производят капитальный ремонт наиболее сложных узлов и агрегатов. Данная форма организации применяется на заводах с крупными цехами в основном в массовом и крупносерийном типах производств.
При смешанной форме организации ремонтных работ в ремонтно-механическом цехе производят капитальный ремонт, а остальные виды ремонта выполняются цеховыми ремонтными базами. Подобная форма организации ремонта применяется, на заводах серийного производства и в тяжелом машиностроении.
Виды технического обслуживание и ремонта подразделяются на следующие:
Техническое обслуживание и ремонт (ТОР), выполняемые ремонтным персоналом службы главного механика;
Техническое обслуживание, выполняемое производственным персоналом.
Виды ТО: регламентированное (РТО), ежедневное (ТОед), периодическое.
РТО включает:
ТО 1 - техническое обслуживание первого вида;
ТО 2 - техническое обслуживание второго вида;
ТО 3 - техническое обслуживание третьего вида.
При ТО 1 должны быть проведены работы ТО есм (ежемесячное техническое обслуживание) и дополнительно - контроль за выполнением правил технической эксплуатации, проверка устройств техники безопасности, правильности функционирования систем смазки и механизмов, неисправность которых может вызвать крупные поломки или преждевременный износ оборудования.
ТО 2 предусматривает выполнение работ ТО 1 , а также проверку и регулировку ременных и цепных передач, органов управления, тяг, ходовых винтов и маточных гаек, крепежных деталей и т.д. с частичным снятием кожухов и крышек, проверку состояния рабочих поверхностей, плавность перемещения механизмов.
ТО 3 предусматривает выполнение работ TO 2 , а также более трудоемких работ с частичной или полной разборкой отдельных сборочных единиц и применением контрольно - измерительных инструментов и приборов, замену смазки и изношенных деталей (сборочных единиц), регулировку узлов и механизмов.
Ежедневное техническое обслуживание (ТО ед) проводиться ремонтно- механическим цехом по заявкам производственного персонала, сменных слесарей и электриков с целью устранения неисправностей и причин, порождающих отказы.
Периодическое техническое обслуживание подразделяется на следующие операции:
1) проверка на точность как самостоятельная операция;
2) консервация (расконсервация).
Виды ремонта
Ремонт может быть плановым (ПР) и неплановым (НР).
Плановый ремонт (ПР) - ремонт, постановка на который осуществляется в соответствии с требованиями нормативно-технической документации (технических условий на изготовление оборудования, требованиями отрасли). По составу и объему работ предусматривается три вида плановых ремонтов:
· капитальный (КР);
· средний (СР);
· текущий (ТР).
Капитальный ремонт - это ремонт, выполняемый для восстановления исправности и полного или близкого к полному восстановлению ресурса изделия с заменой или восстановлением любых его частей, включая базовые. При капитальном ремонте производится полная разборка оборудования, мойка, дефектация, замена или восстановление всех деталей и узлов, сборка оборудования, его комплексное регулирование проверка, испытание на холостом ходу и под нагрузкой, окраска, а также проверка состояния и ремонт фундамента.
Средний ремонт - ремонт, выполняемый для восстановления исправности и частичного восстановления ресурса изделий с заменой или восстановлением составных частей ограниченной номенклатуры и контролем технического состояния составных частей, выполняемый в объеме, установленном в нормативно-технической документации.
При среднем ремонте производится полная (до 65%) разборка сборочных единиц оборудования и частичная остальных, дефектация деталей и узлов, капитальный ремонт отдельных узлов, замена или восстановление ответственных изношенных деталей, в том числе базовых, сборка оборудования, его комплексное регулирование, проверка, испытание на холостом ходу и под нагрузкой, окраска, а также проверка состояния и ремонт фундамента.
Текущий ремонт - ремонт, выполняемый для обеспечения или восстановления работоспособности изделия и состоящий в замене и (или) восстановлении отдельных его частей. При текущем ремонте производится частичная разборка оборудования, полная разборка некоторых узлов, дефектация, замена или восстановление быстро изнашивающихся деталей и узлов и необходимые для этого сборочные и регулировочные работы.
Неплановый ремонт (НР) - ремонт, постановка изделий на который осуществляется без предварительного назначения.
Аварийный ремонт (АВ), связанный с внезапной остановкой оборудования, вызванной дефектами конструкции или изготовления, дефектами ремонта нарушением правил технической эксплуатации и требований техники безопасности, также является неплановым.
1.2 Сущность и эффективность системы планово-предупредительного ремонта (ППР) оборудования
Сущность планово-предупредительной системы
Основные работы по ремонту оборудования на заводе «Калугаприбор» производятся по планово-предупредительной системе, основные положения которой принимаются из «Единой системы планово-предупредительных ремонтов и рациональной эксплуатации технологического оборудования машиностроительных предприятий».
При этой системе ремонт станков выполняется в заранее установленные сроки, после проработки станком определенного количества часов, не ожидая какой-либо поломки. Конечно, такая система не исключает и необходимость ремонта, носящего случайный характер, например, неожиданная поломка станка из-за неправильного пользования им или недостатков, допущенных при изготовлении.
Ежедневное техническое обслуживание проводят во время перерывов в работе оборудования или в нерабочие смены.
Периодическое техническое обслуживание выполняется через установленные в технической документации интервалы времени.
Регламентированное техническое обслуживание выполняется с периодичностью и в объёмах, установленных отраслевой системой или руководством по эксплуатации на данное оборудование.
Все виды работ по плановому (регламентированному) ТО и ремонту выполняются в определенной последовательности, образуя повторяющиеся циклы.
Ремонтный цикл
Ремонтный цикл (Ц р) - это наименьшие повторяющиеся интервалы времени или наработка оборудования, в течение которых выполняется: в определенной последовательности в соответствии с требованиями Системы все установленные виды ремонта. Наработка оборудования определяется количеством часов оперативного времени его работы. Ремонтный цикл завершается капитальным ремонтом и характеризуется структурой и продолжительностью.
Структура ремонтного цикла (С ц.р.) - это перечень и последовательность выполнения плановых ремонтов в период 1 между капитальными ремонтами или между вводом в эксплуатацию оборудования и первым капитальным ремонтом.
Структура ремонтного цикла оговаривается стандартами предприятия для каждой группы станков. Например, структура ремонтного цикла для металлорежущих станков нормальной точности весом до 10 тонн, состоящего из четырех текущих, одного среднего и капитального ремонтов, выглядит следующим образом:
КР - ТР 1 - ТР 2 - СР - ТР 3 - ТР 4 - КР (1.1)
Продолжительность ремонтного цикла (Т ц.р.) - это количество часов оперативного времени работы оборудования на протяжении которого, выполняются все запланированные ремонтные работы, входящие в состав цикла. В продолжительность ремонтного цикла не входят простои оборудования, связанные с выполнением плановых и неплановых ремонтов и ТО, а также по другим организационно-техническим причинам. Продолжительность ремонтного цикла изображают размерной линией между обозначениями капитальных ремонтов, которыми начинается и завершается цикл. Над размерной линией указывают продолжительность цикла в отработанных часах.
Межремонтный период (Т мр) - это период оперативного времени работы оборудования между двумя последовательно выполняемыми плановыми ремонтами. Продолжительность межремонтного периода равна продолжительности ремонтного цикла, деленной на количество плановых ремонтов в цикле, включая капитальный ремонт.
Продолжительность ремонтного цикла и межремонтный период определены для каждого станка по заводу и сведены в таблицы как нормативные.
Цикл технического обслуживания
Цикл технического обслуживания (Ц т.о.) - это наименьшие повторяющиеся интервалы времени или наработка оборудования, в течение которых выполняются в определенной последовательности в соответствии с требованиями данной Системы все установленные виды планового регламентированного технического обслуживания.
Наработка оборудования определяется количеством часов оперативного времени его работы. Цикл технического обслуживания характеризуется структурой и продолжительностью ТО 1 , ТО 2 , ТО 3 образуют цикл технического обслуживания (Ц то). В зависимости от продолжительности межремонтного периода между плановыми ремонтами может быть проведено 1-8 циклов ТО.
Структура цикла технического обслуживания (С ц.то.) - это перечень видов РТО, входящих в состав цикла. Виды ТО, выполняемые неремонтным персоналом (станочниками, уборщицами), а такие операции периодического технического обслуживания (П р,К) в структуру С ц.то. не включают. В отраслевой системе условно принята следующая структура цикла технического обслуживания:
ПР -ТО 1 - ТО 1 - ТО 1 - ТО 2 -
ТО 1 - ТО 1 - ТО 1 - ТО 2 - C ц.то (1.2)
ТО 1 - ТО 1 - ТО 1 - ТО 3 -
ТО 1 - ТО 1 - ТО 1 - ТО 2 -...,
т.е. цикл технического обслуживания
С ц.то. = 9ТО 1 + 2ТО 2 + Т0 3 . (1.3)
Продолжительность цикла технического обслуживания (Т ц.т.о.) в отработанных часах оперативного времени работы оборудования определяется по формуле
где Т мр - продолжительность межремонтного периода, ч.
Т ц.р. - продолжительность ремонтного цикла, ч;
n c - количество средних ремонтов в ремонтном цикле;
n Т - количество текущих ремонтов в ремонтном цикле;
n о - количество циклов регламентированного технического обслуживания в межремонтном периоде.
Межоперационный период обслуживания (Т то) - это период оперативного времени работы оборудования между двумя последовательно выполненными одноименными видами РТО
Межоперационные периоды технического обслуживания для проведения ТО 1 ,ТО 2 определяют по формулам:
где Т ц.то - продолжительность цикла технического обслуживания, ч.
Продолжительность ремонтных циклов, межремонтных периодов и количество циклов РТО в межремонтном периоде для металлорежущего и литейного оборудования, эксплуатируемого в условиях, отличных от условий, указанных в таблицах, рассчитывают как произведение их значений, приведенных в таблицах, на поправочные коэффициенты.
где Т ц.р. - расчетная продолжительность ремонтного цикла, ч.;
Т ц.р. - табличное значение продолжительности ремонтного цикла, ч.;
К о.м. - коэффициент обрабатываемого материала;
К т.с. - коэффициент класса точности станка (оборудование классов точности П, В, А, С);
К к.с. - коэффициент категории станка (по массе);
К в - коэффициент возраста.
Числовые значения коэффициентов К с.м. , К к.с. , К в, К т.с. приведены в таблицах.
Межремонтный период Т мр рассчитывают по формуле:
где - количество средних ремонтов в ремонтном цикле;
Количество текущих ремонтов в ремонтном цикле.
Затем корректируют количество циклов РТО в межремонтном периоде по формуле:
округляют до ближайшего целого числа.
1.3 Техническая подготовка системы планово-предупредительных ремонтов
Техническая и материальная подготовка системы планово-предупредительных ремонтов состоит из конструкторской и технологической подготовки. Конструкторская подготовка включает составления альбомов чертежей деталей, определение номенклатуры и нормализации (унификации) сменных деталей и сборочных единиц.
Альбомы чертежей деталей оборудования используются при планировании, разработке технологии и изготовлении сменных и запасных деталей, установлении ремонтных размеров, нормализации и унификации сменных деталей и заготовок для них, внедрении заменителей дефицитных материалов и модернизации оборудования.
Составляется альбом чертежей на каждый типоразмер оборудования, который содержит паспорт и схемы (кинематическую, гидравлическую, пневматическую, электрическую и смазки), чертежи общего вида сборочных единиц, сменных деталей, спецификации подшипников качения, ремней, нормалей, покупных деталей и аппаратуры и т.п. Чертежи деталей должны составляться при разборке агрегата для плановых ремонтов.
Детали, заменяемые при ремонте оборудования новыми, называются сменными. Нормализация (унификация) сменных деталей позволяет сократить число их типоразмеров и тем самым снизить расходы, связанные с их изготовлением.
Технологическая подготовка заключается в составлении типовых технологических процессов сборки, разборки агрегатов и изготовления наиболее трудоемких и сложных деталей, а также составлении дефектной ведомости.
Дефектная ведомость является исполнительной технологической ведомостью и должна составляться обязательно при капитальном ремонте, а также при среднем ремонте с периодичностью свыше одного года. Предварительная дефектная ведомость составляется за 2-3 месяца до остановки агрегата для ремонта в один из плановых осмотров, а окончательная - при разборке агрегата для капитального или среднего ремонта техником или мастером по ремонту.
Материальная подготовка должна обеспечить создание постоянно возобновляемого запаса (парка) сменных деталей, хранимых в кладовых. Такие детали называются запасными.
К запасным относятся детали:
а) со сроком службы, не превышающим межремонтного периода;
б) расходуемые в больших количествах независимо от срока службы;
в) крупные, сложные и трудоемкие, требующие для своего изготовления сложных и крупных поковок или отливок;
г) изготовляемые на стороне;
д) все сменные детали уникального, особо ответственного или лимитирующего объем производства оборудования.
Детали со значительным сроком службы (1,5-2 года и более) не хранят в кладовой, а заказывают заблаговременно с учетом длительности производственного цикла их изготовления и сроков начала ремонта.
Запас покупных деталей, сборочных единиц и аппаратуры, потребляемых в больших количествах, определяется по аналогии с запасами материалов и покупных полуфабрикатов для основного производства.
В кладовой хранятся детали полностью обработанные, которые могут быть установлены без всякой доделки и подгонки, и в предварительно обработанном виде, если они устанавливаются во время ремонта с доделкой и подгонкой, или в виде заготовки, если не известны точные размеры детали.
Нормативный запас деталей в кладовых в денежном выражении устанавливается по видам оборудования на одну ремонтную единицу в зависимости от типа производства. Нормативы запаса приведены в «Единой системе планово-предупредительных ремонтов».
Расход материала h-го типоразмера на все виды ремонтных работ за год определяется по формуле:
где - расход h-го вида материала на капитальный ремонт оборудования на ремонтную единицу за год;
Коэффициент, учитывающий расход материала при осмотрах и межремонтном обслуживании;
Сумма ремонтных единиц агрегатов, подвергающихся соответственно капитальному, среднему и малому ремонтам в течение года;
Коэффициенты, характеризующие соотношения между количеством материала, расходуемым соответственно при среднем и капитальном, малом и капитальном ремонтах.
Величины устанавливаются для каждого вида оборудования и по подгруппам материала опытно-статистическим методом на основе анализа фактического расхода материалов на ремонт оборудования на заводах.
Для хранения запасных деталей и ремонтных материалов организуется заводская кладовая, подчиненная ОГМ, и цеховые кладовые - в крупных цехах. В цеховой кладовой хранятся запасные детали для агрегатов, имеющихся только в данном цехе или расходуемые в этом цехе в большом количестве.
1.4 Планирование ремонта оборудования в ремонтно-механическом цехе
Годовой план ремонта оборудования составляется ОГМ завода при участии цехового механика на каждую единицу оборудования. Календарные сроки ремонта определяют на основании данных журнала учета работы оборудования и других материалов об агрегате, исходя из фактически отработанных часов за период от последнего ремонта и результатов ежегодного технического осмотра в октябре - ноябре месяце.
В годовой план ремонтов включаются осмотры и плановые ремонты. Месяц, в котором должен производиться очередной ремонт (осмотр) по плану, определяется путем прибавления к месяцу предыдущего ремонта длительности межремонтного (межосмотрового) периода в месяцах. Вид очередного ремонта устанавливается по структуре ремонтного цикла в зависимости от видов предыдущих ремонтов.
Трудоемкость слесарных и станочных работ находят путем умножения трудоемкости одной ремонтной единицы по соответствующему виду ремонта на категорию сложности.
Система ППР предусматривает установление норм простоя оборудования в ремонте. Так, в настоящее время принято, что при работе ремонтной бригады в одну смену простой в рабочих днях на ремонтную единицу не должен превышать при малом ремонте 0,25, среднем - 0,6 и капитальном - 1,0.
Ускорение проведения ремонта достигается:
а) сокращением трудоемкости слесарных работ за счет их большей механизации, применения прогрессивной технологии ремонта, предварительной подготовки сменных деталей и сборочных единиц и расширения их номенклатуры, упрощения конструкции оборудования (снижения ремонтной сложности);
б) увеличением числа рабочих в бригаде (расширением фронта работ) или сменности их работы;
в) большей специализацией ремонтных слесарей, лучшей организацией труда и рабочего места ремонтных бригад и бесперебойным обеспечением их всем необходимым (чертежами, материалами, сменными деталями и др.).
Потребное количество рабочих для выполнения плановых ремонтов S п.р. определяется по формуле:
где - нормативы времени на 1 ремонтную единицу, подлежащих соответственно капитальному, среднему и малому ремонту;
F р - годовой эффективный фонд времени работы одного ремонтного рабочего, ч/чел;
Р в - средний процент выполнения норм ремонтными рабочими.
Суммарное количество ремонтных единиц оборудования.
Трудоемкость всех ремонтов в каждом месяце по плану должна быть примерно одинаковой, чтобы не было недостатка или излишка ремонтных рабочих в отдельные месяцы.
Годовой план ремонта оборудования подписывается главным механиком завода, начальником и механиком цеха и утверждается директором завода.
Учет выполнения плана ремонтов ведется в том же плане-графике, в нижней строке, по каждому агрегату.
На основании годового плана и его фактического выполнения за предыдущие месяцы, а также количества фактически отработанных агрегатом часов с момента последнего ремонта, фактического состояния оборудования, выявленного при проведении осмотра, и обеспеченности ремонта запасными деталями и материалами составляют по каждому цеху месячный план ремонта. Месячный план ремонта оборудования должен быть согласован с планом основного производства. Составляется он ОГМ совместно с механиком цеха.
Если агрегат на начало ремонта окажется исправным или очередной ремонт может быть заменен другим, меньшим по объему, то отмена данного вида ремонта или замена другим производится с разрешения главного механика завода. Межосмотровый период не может быть удлинен. Учет и контроль выполнения планов ведется планово-производственным бюро.
2. Анализ организации действующего производства в ремонтно-механическом цехе ФГУП «Калугаприбор»
2.1. Характеристика ремонтно-механического цеха ФГУП «Калугаприбор»
Организационная структура ремонтно-механического цеха на ФГУП «Калугаприбор» имеет следующий вид:
Рис. 2.1. Производственная структура ремонтно-механического цеха на ФГУП «Калугаприбор»
Производственная структура цеха - это состав его производственных участков, других внутрицеховых подразделений и формы их взаимосвязи.
Формирование цехов предприятия идет в основном по двум направлениям специализации: по однородности выполняемых ими технологических процессов (технологическая специализация) и по характеру изготовляемых в них изделий (предметная и подетальная специализация).
При технологической специализации в цехе выполняется часть технологического процесса, состоящая из одной или нескольких операций при весьма широкой номенклатуре деталей (изделий). При этом в цехе устанавливается главным образом однотипное оборудование. Такая форма специализации цехов имеет свои преимущества и недостатки. При небольшом разнообразии операций и оборудования облегчается техническое руководство, и создаются более широкие возможности регулирования загрузки оборудования, организации обмена опытом. Однако при технологической специализации обрабатывающих цехов складываются сложные, удлиненные маршруты движения предметов труда с неоднократным их возвращением в одни и те же цехи. Это нарушает принцип прямоточности, затрудняет согласование работы цехов и приводит к увеличению производственного цикла.
В цехах предметной специализации полностью осуществляется соответствующий этап (частичный процесс) изготовления закрепленных за ним деталей относительно узкой номенклатуры. Для этих цехов характерно разнообразное оборудование и оснастка, но узкая номенклатура обрабатываемых деталей (узлов). Согласование работы цехов в этом случае значительно проще, так как все операции обработки сосредоточены в одном цехе. Это ведет к устойчивой повторяемости процесса, упрощает оперативно календарное планирование, территориально сближает операции и отдельные стадии процесса и, в конечном счете, сокращает производственный цикл.
Одним из направлений совершенствования производственной структуры предприятия является замена технологической формы специализации цехов предметной.
Для данного ремонтно-механического цеха характерна многопредметная специализация. Здесь используется разнообразное оборудование и оснастка. Виды работ: преимущественно механическая обработка, слесарно-ремонтные работы (сборка и другие) восстановление, сварка. Точные виды работ, выполняемые в данном цехе, описаны ниже.
Участки цеха технологически специализированы и оснащены однородным оборудованием для выполнения отдельных операций. Они формируются по группам однотипных станков.
В состав отделений входят:
Токарное отделение;
Фрезерное отделение;
Сверлильное отделение;
Строгальное отделение;
Отделение зубофрезерных станков.
Вспомогательными являются отделения:
Заточное;
Инструментально-раздаточная кладовая;
Кладовая приспособлений.
Структурным звеном участка является рабочее место. Рабочим местом называют часть производственной площади, оборудованную и оснащенную техническими средствами и устройствами соответственно характеру выполняемых работ. Разнообразие выполняемых работ на рабочих местах находится в связи с характером и уровнем специализации цеха и участка. В ремонтно-механическом цехе ФГУП «Калугаприбор» доминирует технологическая специализация рабочего места, т.е. производится множество деталеопераций в пределах технологической возможности оборудования. Планировка цеха представлена в приложении 1.
2.2 Определение объёмов работ, выполняемых в ремонтно-механическом цехе ФГУП «Калугаприбор»
Система определения объемов работ для ремонтно-механического цеха, используемая на ФГУП «Калугаприбор»
Планирование работ для ремонтного цеха начинают с учета наличия, движения и использования оборудования в производственных цехах. Выбытие и поступление отражаются в бухгалтерской отчетности.
Для определения потребности проведения необходимых видов ремонта необходимо располагать данными о времени, фактически отработанном станком с момента ввода в эксплуатацию или от последнего планового ремонта (является составляющей частью календарного времени ремонта).
Календарное время смены Т см, равное для предприятий отрасли восьми часам, состоит из:
Т р.о. - оперативного времени работы оборудования;
Т пз - подготовительно - заключительного времени;
Т пн - времени простоя для поддержания или восстановления работоспособности;
Т п.о. - времени простоя по организационно-техническим причинам.
Учет оперативного времени может быть также организован с помощью счетчиков времени работы оборудования.
Счетчики времени работы оборудования, обеспечивающие точный результат, подключают к каждому станку. Ежемесячно работник ОГМ заготавливает «Ведомости показаний счетчиков», в которые записывают оборудование, оснащенное счетчиками времени, по цехам и участкам. Данный способ требует определенных затрат и на предприятии «Калугаприбор» не используется. Данные об оперативном времени работы оборудования получают из нормировочных подразделений производственных цехов.
Основным документом, в котором отражается планирование ремонтных работ, является план-график (план-график составляется с учетом межремонтных периодов). Реальный план-график ремонта оборудования составляется лишь на год. За шесть месяцев до начала планируемого года по всей номенклатуре оборудования, находящегося на предприятии «Калугаприбор» производиться расчет потребности во всех видах ремонта. Затем осуществляют свод необходимых ремонтов по каждому станку за год в Форму 1 «Годовой план ремонта оборудования по цеху», где указывается инвентарный номер, наименование оборудования, модель, категория сложности, а также сменность, вид и дата последнего ремонта, вид ремонтных операций за каждый месяц.
Весь определенный объем работ распределяется по месяцам в зависимости от вида и продолжительности ремонта каждой единицы оборудования.
Расчет месячной трудоёмкости работ для ремонтно-механического цеха на 2009 г.
Месячную трудоёмкость работ (в часах), выполняемых ремонтно-механическим цехом определяют следующим образом.
В месячном плане ремонта оборудования цеху устанавливают:
1. наименование и инвентарный номер оборудования;
2. модель станка;
4. плановую трудоёмкость работ в нормо-часах.
Механическая часть станков и машин в общем случае состоит из кинематической и гидравлической частей, ремонтосложность которых соответственно обозначают Р к и Р г.
Следовательно,
За единицу ремонтосложности механической части принято 0,09 трудоёмкости капитального ремонта станка 1К62.
Трудоемкость работ по ремонту механической части подсчитывают по каждому виду ремонта отдельно.
Т км =Т к.слес.+Т к.стан. ; (2.2)
Т см =Т с.слес.+Т с.стан. ; (2.3)
Т тм =Т т.слес.+Т т.стан. ; (2.4)
где Т км - трудоемкость капитального ремонта механической части;
Т см - трудоемкость среднего ремонта механической части;
Т тм - трудоемкость текущего ремонта механической части;
Т к.слес. - трудоемкость капитального ремонта слесарных работ;
Т с.слес. - трудоемкость среднего ремонта слесарных работ;
Т т.слес. - трудоемкость текущего ремонта слесарных работ;
Т к.стан. - трудоемкость капитального ремонта станочных работ;
Т с.стан. - трудоемкость среднего ремонта станочных работ;
Т т.стан. - трудоемкость текущего ремонта станочных работ.
Таким образом, трудоемкость каждого вида ремонта, в свою очередь, состоит из трудоёмкости станочных и слесарных работ. Трудоемкость слесарных и станочных работ находится по формулам:
где t к.слес. - норма трудоемкости капитального ремонта единицы ремонтосложности слесарных работ;
t к.стан. - норма трудоемкости капитального ремонта единицы ремонтосложности станочных работ;
t с.слес. - норма трудоемкости среднего ремонта единицы ремонтосложности слесарных работ;
t с.стан. - норма трудоемкости среднего ремонта единицы ремонтосложности станочных работ;
t т.слес. - норма трудоемкости текущего ремонта единицы ремонтосложности слесарных работ;
t т.стан. - норма трудоемкости текущего ремонта единицы ремонтосложности станочных работ;
(R м) к - суммарная ремонтосложность механической части оборудования, проходящего капитальный ремонт;
(R м) с - суммарная ремонтосложность механической части оборудования, проходящего средний ремонт;
(R м) т - суммарная ремонтосложность механической части оборудования, проходящего текущий ремонт.
Таким образом,
где Т рм - общая трудоемкость (суммарная трудоемкость работ по ремонту механической части оборудования);
0.1 - коэффицент, учитывающий непредвиденный ремонт.
В «Отраслевой системе технического обслуживания и ремонта металлообрабатывающего оборудования» приведена таблица трудоемкости плановых ремонтов (см. приложение 2), по которой определяют норму времени на 1 ЕРС в часах. Норма времени находится с учётом видов ремонта и работ (слесарные или станочные).
Трудоемкость технического обслуживания находится аналогично трудоемкости ремонта, с использованием нормативов времени на одну ремонтную единицу (см. приложение 3).
В «Отраслевой системе технического обслуживания и ремонта металлообрабатывающего оборудования» приведена таблица нормативов времени в часах на одну ремонтную единицу (см. приложение 3) по которому находится норма времени с учетом зависимости трудоемкости ремонта от получения запасных деталей со стороны.
Расчет трудоемкости работ ремонтно-механического цеха проведем на примере июля 2009г. (июль выбран как самый загруженный месяц года) (см. табл. 2.1, табл. 2.2, табл. 2.3).
Таблица 2.1. Расчет трудоемкости работ РМЦ
Используемые формулы:
Т с.стан. =(t с.стан. -t с.ум.стан.)(R м) с; (2.7)
Т с.слес. =(t с.слес. -t с.ум.слес.)(R м) с; (2.8)
Т к.стан. =(t к.стан. -t к.ум.стан.)(R м) к; (2.9)
Т к.слес. =(t к.слес. -t к.ум.слес.)(R м) к; (2.10)
Т т.стан. =(t т.стан. -t т.ум.стан.)(R м) т; (2.11)
Т т.слес. =(t т.слес. -t т.ум.слес.)(R м) т; (2.12)
где t ум. - величина уменьшения трудоемкости, зависящая от поставки запасных частей со стороны. Определяется по таблице (см. приложение 4).
Общая трудоемкость станочных работ при проведении ремонта (Т общ.стан.рем.).
Т общ.стан.рем. =Т с.стан. +Т к.стан. +Т т.стан. ; (2.13)
Т общ.стан.осм. =Т о.стан. ; (2.14)
Т общ.стан. = Т общ.стан.рем. +Т общ.стан.осм. (2.15)
Аналогично для слесарных работ, за исключением полученных по нормативным данным.
Т общ.слес.осм. =Т о.слес. 1,1; (2.16)
т.е. трудоемкость увеличится на 10% в связи с проведением работ в разных цехах (табл. 2.2).
Таблица 2.2. Ремонты
Наименование агрегата |
Место нахождения станка |
Вид ремонта |
Общая трдоемкость, н-ч. |
||||||
Кран-балка |
|||||||||
Строгальный |
|||||||||
Сверлильный |
|||||||||
Кран-штабелер |
|||||||||
Фрезерный |
|||||||||
Полировальный |
|||||||||
Вертикально сверлильный |
|||||||||
Вертикально сверлильный |
|||||||||
Электроталь |
|||||||||
Кромкообрезной |
В связи с отсутствием поставки в цех запасных частей со стороны, на июль 2009 г. коэффициент их учета общую трудоемкость ремонтов не уменьшает и равен 1.
Таблица 2.3. Осмотры
Наименование агрегата |
Место нахождения станка |
Трудоемкость слесарных работ, н-ч. |
Трудоемкость станочных работ, н-ч. |
Общая трудоемкость, н-ч. |
||||
«Пионер» |
||||||||
Подъемник |
||||||||
Подъемник |
Котельная |
|||||||
«Пионер» |
||||||||
Электроталь |
||||||||
Электроталь |
||||||||
Электроталь |
||||||||
Подъемник |
||||||||
Электроталь |
||||||||
Штабелер |
||||||||
Штабелер |
Т общ.слес. =3065 н-ч.; Т общ.стан. =1037 н-ч; Т общ. =3065+1037 =4102 н-ч.
Трудоемкость ремонтных работ для других месяцев года рассчитана аналогично (см. табл. 2.4). На основе этих данных строится суммарный график изменения трудоемкости ремонтных работ, планируемых в ремонтно-механическом цехе на 2009г. Построение осуществляется с учетом возможной переструктуризации планов ремонта по месяцам, т.е. с наиболее загруженных месяцев определенное количество капитальных ремонтов переносилось на предыдущий месяц. Данный график имеет следующий вид:
Рис. 2.2. Диаграмма трудоемкости плановых ремонтов на 2009 год
Таблица 2.4
Тобщ(час) |
сентябрь |
|||||||
Тобщ(час) |
3. Предлагаемые мероприятия по совершенствованию организации производства и их экономическая эффективность
3.1 Построение календарного графика продолжительности ремонтных работ
Для выполнения всех работ по ремонту и техническому обслуживанию оборудования и других видов основных фондов необходима рациональная организация и четко спланированная работа ремонтно-механического цеха. Таким образом, для оптимизации руководства и управления организацией работ целесообразно планирование продолжительности ремонта.
Плановая продолжительность ремонта оборудования зависит от трудоемкости ремонтных работ, ремонтной сложности оборудования, численности ремонтной бригады. Имея эти данные можно построить календарный график продолжительности ремонтов. Такой график в данном цехе, к сожалению, не используется. Однако с его помощью можно более точно определить дни поставки оборудования на ремонт, загруженность рабочих в течение дня, возможность расширения работ.
Диаграмма плановых ремонтов показывает, что июль является самым загруженным месяцем года.
Построение календарного графика работ для ремонтно-механического цеха на июль необходимо начать с группировки необходимых осмотров по объектам.
С 21 по 39 - номенклатурные номера объектов обслуживания.
Таблица 3.1. Группировка осмотров по объектам
КОТЕЛЬНАЯ |
||
БЮРО СБЫТА |
||
Общая трудоемкость осмотров и обслуживания в каждом цехе и отделе определяется как сумма трудоемкости работ по обслуживанию объектов отдельно для станочников и слесарей. Осуществление осмотров может происходить в свободное от плановых ремонтов время. Для построения календарного графика продолжительности ремонтов произведем расчет продолжительности ремонтов по формуле:
где Т n - плановая продолжительность ремонта единицы оборудования, ч.;
t- норма трудоемкости, соответствующего вида ремонта единицы ремонтной сложности;
R м - единицы ремонтной сложности;
Ч р - численность ремонтной бригады, чел.;
Коэффициент переработки норм.
Нельзя точно определить чередование работы слесарей и станочников в цехе во времени, поэтому внутри бригады необходимо самостоятельно определять объем и время проведения отдельных видов работ (слесарных и станочных).
С учетом подсчитанной выше численности работающих и категорий сложности производственных ремонтов, в бригаде должно быть 16 человек. При построении календарного графика берем во внимание, что общее время проведения работы делится на 16 работников бригады (из них 11 слесарей, 5 станочников).
Таблица 3.2. Расчет продолжительности плановых ремонтов
Номер объекта ремонта |
Наименование оборудования |
Местонахождение оборудования |
Плановая продолжительность ремонта |
|
Кран-балка |
(88+202,4)/1,9516=9,07 |
|||
(66+151,8)/1,9516=6,8 |
||||
Строгальный |
(297+683,1)/1,9516=30,1 |
|||
Сверлильный |
(55+126)/1,9516=5,6 |
|||
Кран-штабелер |
(23,1+52,8)/1,9516=2,37 |
|||
Фрезерный |
(100,1+288,8)/1,9516=12 |
|||
Полировальный |
(33+75,9)/1,9516=3,4 |
|||
Вертикально-сверлильный |
(46,2+105,6)/1,9516=4,7 |
|||
Вертикально-сверлильный |
(42,35+96,8)/1,9516=4,3 |
|||
Электроталь |
(15,4+35,2)/1,9516=3,5 |
|||
Кромкообрезной |
(38,5+88)/1,9516=3,9 |
|||
Электроталь |
(4,4+8,8)/1,9516=0,4 |
|||
Электроталь |
(4,4+8,8)/1,9516=0,4 |
Исходя из полученных данных, строим график, руководствуясь следующими принципами:
1. Для ремонта каждого станка необходимо оставлять время, превышающее продолжительность планового ремонта на случай возникновения необходимости в ремонте с большей трудоемкостью, чем нормативная. Это время называется резервным временем.
2. Каждый новый станок начинают обслуживать сначала следующей смены или с ее второй половины (это необходимо для того, чтобы рабочий видел результат выполнения своей работы, и площадь цеха излишне не загружалась).
3. Если по плановым расчетам время ремонта станка заканчивается среди смены, но не превышает ее половину, то за резервное время принимают количество оставшихся часов этого дня.
4. Если время ремонта станка заканчивается среди смены и превышает ее половину, то за резервное время принимаются оставшиеся часы дня и первая половина следующей смены.
5. Если непредвиденный ремонт не происходит, этот день используется для технического обслуживания, чтобы рабочие не простаивали.
На основе данных принципов было произведено построение календарного графика продолжительности плановых ремонтов на июль 2009 года (см. рис. 3.1).
Итак, по графику видны точные даты ремонта определенных станков и дни обслуживания. Свободные часы можно использовать для производства в цехе различных услуг.
Создание календарного графика продолжительности ремонтов, что позволит упорядочить поступление конкретного вида оборудования на ремонт, избавит площадь цеха от излишней загруженности, даст возможность работникам лучше ориентироваться в сроках выполнения работ, что избавит их от резкого увеличения объемов работ в конце месяца. С помощью данного графика можно более четко проектировать загрузку оборудования в производственных отделениях. Построение данного графика для всех двенадцати месяцев наглядно отразит дни простоя в течение года и позволит более рационально разнести ремонт по месяцам, определить наиболее желательное время отпусков рабочих.
3.2 Организация комплексной ремонтной бригады
Так как на ФГУП «Калугаприбор» ремонт всех видов, а иногда и межремонтное обслуживание производится силами ремонтно-механического цеха, большое значение имеет качественный и количественный состав работников цеха, его организационная структура.
В данной работе предлагается образование в цехе комплексной ремонтной бригады, которая будет включать рабочих разных профессий, выполняющих комплекс технологически разнородных работ, охватывающих все виды ремонта и технического обслуживания металлообрабатывающего и другого оборудования. Целесообразность выбора данного вида бригад объясняется следующими факторами:
Осуществлением комплекса взаимосвязанных работ, требующих одновременного участия группы исполнителей;
Невозможностью установить постоянный объем и состав работ вследствие непредвиденных ремонтов;
Численность, профессиональный и квалификационный состав бригады устанавливается в зависимости от плановой трудоемкости и сложности планируемых работ по ремонту и техническому обслуживанию.
В Главе 2 дипломной работы было произведено определение необходимого числа работников. Расчеты показали, что даже в самый загруженный месяц 2009 года - в осуществлении ремонта и обслуживания должны быть заняты 5 станочников и 11 слесарей. Они и составляют ремонтную бригаду.
В настоящее время в цехе работают 6 станочников и 15 слесарей, занятых в ремонте и техническом обслуживание, что превышает необходимое количество рабочих на 5 человек (1 станочника и 4 слесарей). Поэтому рекомендуется сокращение численности рабочих наименьшего квалификационного разряда, не соответствующего обслуживанию оборудования средней и высокой категории сложности или перевод их в ремонтные цеховые базы цехов основного производства.
Для обоснования данного предложения был произведен сравнительный расчет заработной платы для полного и сокращенного состава.
Фонд заработной платы устанавливается как произведение плановой трудоемкости на сдельную среднечасовую стоимость одного нормо-часа, с учетом% премии. На все виды работ по ремонту и техническому обслуживанию оборудования устанавливают нормы времени в нормо-часах. Эти работы выполняют в соответствии с планом-нарядом, который составляют на основании месячных планов-графиков ремонта и технического обслуживания. Плановым и оплачиваемым документом для бригады является месячный план-наряд. В месячном плане-наряде бригаде устанавливают:
Наименования и номера ремонтируемого и обслуживаемого оборудования.
Сумму единиц ремонтосложности,
Вид ремонта и средний разряд работ;
Плановую трудоемкость в нормо-часах;
Сумму нормативной заработной платы за выполнение работ в рублях;
Плановые сроки выполнения работ;
При заполнении плана-наряда средний тарифный разряд работ устанавливается в зависимости от их наименования и ремонтосложности оборудования, подлежащего ремонту в данном месяце.
Таблица 3.3. План-наряд
Для каждого работника определяется месячный тарифный заработок в соответствии с проработанными им часами и присвоенным разрядом.
Таблица 3.4. Расчет месячного тарифного заработка (ЗП тар.повр.мес.) для полного состава рабочих бригады
ЗП тар.повр.мес. , руб. |
|||||
Для слесарей: |
|||||
Таблица 3.5. Расчет месячного тарифного заработка (ЗП тар.повр.мес.) для сокращенного состава рабочих бригады
Отработанное время (F факт.мес.), ч. |
Тарифная ставка (С час. i), руб. |
ЗП тар.повр.мес. , руб. |
|||
Для слесарей: |
|||||
Заработная плата рабочих состоит из:
Месячного тарифного заработка;
Сдельного приработка, начисленного с учетом коэффициента распределения прирабока;
Премии, начисленной с учетом коэффициента распределения премии.
Расчет производится в следующем порядке:
ПРк сд. =ЗП бр -ЗП тар.повр.мес. , (3.2)
где ПРк сд. - сдельный приработок бригады.
К р.пр. - коэффициент распределения сдельного приработка бригады.
Рассчитывается коэффициент распределения бригадной премии (К р.п.):
Таблица 3.6. Расчет заработной платы для полного состава рабочих бригады
ЗП тар.повр.мес. , руб. |
Сдельный приработок, руб. (К р.пр. =0,1) |
Премия, руб. (К р.п. =0,33) |
Заработная плата, руб |
||
Для слесарей: |
|||||
Таблица 3.7. Расчет заработной платы для сокращенного состава рабочих бригады
ЗП тар.повр.мес. , руб. |
Сдельный приработок, руб. (К р.пр. =0,35) |
Премия, руб. (К р.п. =0,4) |
Заработная плата, руб |
||
Для слесарей: |
|||||
Для станочников: |
|||||
Из данных расчетов можно сделать вывод, что такая мера увеличивает заработную плату рабочих в среднем на 22,5%, что повышает их материальную заинтересованность.
Другим положительным показателем может служить выработка на одного рабочего:
где В 1 - выработка на одного рабочего при полном составе бригады;
В 2 - выработка на одного рабочего при сокращенном составе бригады;
N 1 , N 2 - количество работников в бригаде;
Т - трудоемкость ремонтных работ.
Исходя из ранее произведенных расчетов численности рабочих и ИТР цеха, предлагается следующая организационная структура:
Рис. 3.2. Новая организационная структура ремонтно-механического цеха на ФГУП «Калугаприбор»
Заключение
Для поддержания оборудования в работоспособном состоянии, проведения ремонтных работ, позволяющих сократить потери времени на ремонт оборудования на ФГУП «Калугаприбор» существует специальный ремонтный цех, который является одним из важных участков вспомогательного производства. В цехе осуществляется ремонт основного и вспомогательного, подъемно-транспортного и другого оборудования, которым располагает завод. Основными задачами ремонтно-механического цеха являются: проведение межремонтного обслуживания оборудования, своевременный ремонт и модернизация.
Особенность ремонтного цеха заключается в исключительно большом разнообразии используемых при ремонте процессов. Поэтому внедрение новых технологий на заводах, неспециализированных на ремонте, затруднительно. Это требует повышения организации работ в ремонтном цехе и учета наиболее рациональной и возможной в данный момент доли получения запасных частей к заводскому оборудованию со стороны.
Большое значение при расчете численности работающих имеет выбранный метод организации работ (централизованный, децентрализованный, смешанный). Основное различие методов заключается в распределении работ между ремонтно-механическим цехом и цеховыми ремонтными базами, что уменьшает или увеличивает трудоемкость.
Во-первых, предлагается образование в цехе комплексной ремонтной бригады, которая будет включать рабочих разных профессий, выполняющих комплекс технологически разнородных работ, охватывающих все виды ремонта и технического обслуживания металлообрабатывающего и другого оборудования. Основными преимуществами комплексных бригад являются:
Подобные документы
Понятие и показатели оценки качества услуг. Комплексный анализ деятельности ремонтно-строительной компании. Совершенствование качества услуг путем повышения квалификации персонала, организации системы контроля за сдачей объектов в эксплуатацию и клининга.
дипломная работа , добавлен 15.06.2012
Теоретические аспекты, типы, формы и методы, развитие форм организации производства. Анализ производственно-хозяйственной деятельности предприятия, структура управления и производства. Мероприятия по совершенствованию основного производства предприятия.
дипломная работа , добавлен 25.05.2010
Расчет производственной программы, определение типа производства, потребности в оборудовании, численности основных производственных рабочих. Управления цехом и пути совершенствования организации обеспечения производства транспортными средствами.
курсовая работа , добавлен 02.03.2010
Характеристика и основные результаты деятельности ОАО "Инпротехсервис". Совершенствование планирования организации производства продукции за счет за счет увеличения объемов производства и создания нового цеха по выпуску геосинтетических материалов.
курсовая работа , добавлен 24.02.2014
Оценка эффективности и разработка предложений по совершенствованию производственной, организационной и управленческой структур организации на примере ОАО "Агропромтранс". Совершенствование системы управления конфликтами в сельскохозяйственной организации.
контрольная работа , добавлен 18.01.2015
Характеристика видов, форм и типов организации производства. Отличительные черты поточного, партионного и индивидуального методов организации производства. Особенности организации производства во вспомогательных и обслуживающих подразделениях предприятия.
реферат , добавлен 16.06.2010
Общие положения организации поточных методов производства. Развитие предметной формы специализации цехов. Поточное производств – прогрессивная форма организации производственных процессов. Характерные признаки организации поточного производства.
контрольная работа , добавлен 03.06.2008
Принципы, формы, методы организации производства. Расчет производственной программы, потребности в оборудовании, площади цеха и численности основных производственных рабочих. Организация ремонтного, инструментального, складского, транспортного хозяйства.
курсовая работа , добавлен 02.03.2010
Экономическая сущность оплаты труда в условиях рыночной экономики, ее формы. Анализ системы оплаты труда на предприятии ООО "Ремонтно-транспортная компания "Реал". Реализация предложений по использованию материальных методов повышения мотивации персонала.
дипломная работа , добавлен 01.07.2014
Типы организации производства: сущность, понятие и сравнительная характеристика. Особенности и преимущества серийного типа партионного метода организации производства. Основные направления повышения экономической эффективности организации производства.
Благодарим редакцию журнала «Трамплин к успеху» НПО «Сатурн» за предоставление данного материала.
За многие годы существования предприятий сложилась практика, что на заводе создается головное управление главного механика, а в цехах организовываются самостоятельные службы по ремонту и обслуживанию оборудования. При этом управление такими службами осуществляется непосредственно начальником цеха или его заместителем и функционально главным механиком. В цехах организовываются склады запчастей для своего оборудования, набирается персонал для ремонта оборудования, формируются собственные графики ремонтов, которые выполняются своими же людьми. И так продолжалось долгие годы, пока не появилось передовое оборудование, которое скорее похоже на «шкаф с проводами» чем на привычный станок. И чем таких станков больше, тем сложнее их обслуживать…
Новые технологии изготовления и требования к качеству изделий также требовали совершенно новых типов оборудования. Конечно, можно было набрать специалистов по данному оборудованию или точечно обучить в каждом цехе работников. Но ведь их еще нужно найти!
И это только одна из проблем, с которой пришлось столкнуться службе главного механика АО «ОДК-Пермские моторы». Ведь с началом подготовки к серийному производству двигателя ПД-14 увеличилось не только количество поступаемого оборудования, но и его сложность. Новые технологии изготовления и требования к качеству изделий также требовали совершенно новых типов оборудования. Конечно, можно было набрать специалистов по данному оборудованию или точечно обучить в каждом цехе работников. Но ведь их еще нужно найти!
В то же время для приобретаемого оборудования необходимо еще создать собственный фонд ремонтных деталей. И так в каждом цехе… Это стало проблемой «номер два» для службы главного механика.
И усугубляло ситуацию то, что в цехах почти не велась статистика по выходу из строя, простои не фиксировались, нарушен учет имеющихся запасных частей к оборудованию и нет четкой информации, что потребуется в ближайшем времени.
А в условиях роста объемов производства всё чувствительнее сказывался каждый час простоя оборудования по причине ремонта. И чем дальше, тем сложнее было справляться с ростом объема возникающей «работы». И так продолжалось, пока существующая система обслуживания и ремонта оборудования перестала справляться.
Было необходимо всё выстраивать с нуля. Это и процессы планирования обслуживания оборудования, создание оперативной связи со службой главного механика при выходе из строя станков, организация управляемого фонда запасных частей, формирование и восстановление возможностей ремонта «собственными силами».
АНАЛИЗ ТЕКУЩЕГО СОСТОЯНИЯ
Анализ организации работ по обслуживанию оборудования внутри цехов показал свои недостатки. Во-первых, отсутствуют определенные правила, какие работы и в каком объемы должны выполняться внутри цеха и когда необходимо отдавать станок в подрядную организацию. Во-вторых, цеховыми службами выполняются только те работы, которые возможно выполнить в текущий момент в зависимости от наличия запчастей. В-третьих, как было сказано ранее, выполненные работы нигде не фиксируются, а случаи ремонта можно выявить только в случае приобретения запасных частей или при зафиксированном обращении в подрядную организацию.
Чтобы выстроить систему оповещения о выходе из строя оборудования, было принято решение о доработке существующего АРМа «Заявки на ремонт оборудования». Ранее, чтобы поставить в известность компетентные службы, производственному мастеру необходимо было найти механика цеха, потом дождаться работников службы механика, довести проблему до исполнителей, на что, в итоге, уходило до нескольких часов смены.
Статистика по выходу из строя оборудования и причины отказов
В настоящий момент в случае аварийного или планового обслуживания, производственному мастеру достаточно поставить отметку о состоянии оборудования и дальше весь процесс уже происходит без его участия. В то же время, за счет автоматизации стало возможно собрать статистику по каждому случаю из строя, по каким причинам останавливается тот или иной станок и уже планировать необходимые виды ремонта под каждую единицу оборудования.
Учет простоев и текущего состояния по ремонту оборудования
ОПТИМИЗАЦИЯ СУЩЕСТВУЮЩИХ РЕСУРСОВ
Основной задачей данного этапа стала оценка существующих ресурсов по поддержанию оборудования в работоспособном состоянии. В каждом цехе была организована инвентаризация запасных частей и проведен анализ. Стоит отметить, что одновременно с инвентаризацией проводились работы по организации единого склада запчастей. На тот момент это позволило сократить потребности в остродефицитных деталях для станков. Когда вся информация была собрана, получилось, что большинство нужных в этот момент запчастей находилось в соседних цехах, а еще чаще на складах цехов «лежали» детали для станков, которые уже списаны в этом цехе.
Не менее важной задачей являлась оценка существующего кадрового состава...
Извините, этот материал доступен целиком только участникам Сообщества производственных менеджеров.
Вы можете пройти регистрацию и получить доступ к эксклюзивным аналитическим, методическим и переводным материалам, опубликованным на сайте.
Участие также дает много дополнительных возможностей.
Ю.П. Косинов, А.А. Романов, Ю.В. Трофимов
(ОАО "ЦКБ Энергоремонт", ОАО «"РАО ЕЭС России"»)
1. Постановка задач совершенствования ремонта объектов
электроэнергетики
Основополагающие критерии совершенствования технического обслуживания и ремонта должны отвечать конечным целям энергопроизводства - обеспечению надежности энергоснабжения потребителей.
На уровне отдельных генерирующих компаний конечные цели соответственно дифференцируются. В связи с этим проявляется вторичная группа конечных целей энергопроизводства - обеспечение конкурентоспособности энергопрозводителей.
Все эти цели оказываются взаимосвязанными и составляют базу для формирования задач совершенствования ремонта объектов электроэнергетики без учета их государственной принадлежности и социально-экономического устройства.
К обеспечению первоочередных критериев совершенствования энергоремонтного производства следует отнести стремление к достижению более высоких показателей готовности энергоисточников к несению нагрузок.
Такие показатели в области теории надежности считаются комплексными. Несмотря на известное содержание приведенного термина, в сфере взаимоотношений энергопрозводителей и потребителей такое понятие принято использовать в качестве индикатора, способного влиять на рейтинг энергокомпаний при реализации акций и других ценных бумаг. В основном такие взаимоотношения приняты в странах Северной Америки.
К обеспечению более приземленных критериев совершенствования энергоремонтного производства следует отнести стремление к достижению более низких показателей ремонтной составляющей тарифов на электрическую и тепловую энергию. Последнее снижает условно-постоянную составляющую тарифов и также способствует повышению конкурентоспособности энергокомпаний.
Обозначенные критерии совершенствования технического обслуживания и ремонта, естественно, не могут считаться исчерпывающими, однако на их основе можно сформулировать некоторые предпосылки более конкретных задач в области отечественного энергопроизводства.
С начала 90-х годов в силу известных обстоятельств отечественная электроэнергетика вступила в фазу снижения энергопроизводства. Возникшие резервы в сочетании с ослаблением функций командно-административной системы обусловили ряд негативных проявлений. Они выразились в увеличении продолжительности простоев энергооборудования в различных видах ремонтов, а также в непредсказуемом росте затрат на техническое обслуживание и ремонт.
Внешние предпосылки снижения эффективности энергоремонта оказались хотя и существенными, но не доминирующими. Основу негативных процессов составили экономические и физические аспекты старения эксплуатируемого оборудования.
Возникшие негативные тенденции своевременно были изучены, и их последствия в значительной степени удалось преодолеть. Предложенный проект совершенствования энергоремонтного производства не нарушал существующую систему действующих государственных стандартов, нормативных документов Гос-гор-технадзора, правил технической эксплуатации и правил организации технического обслуживания и ремонта оборудования, зданий и сооружений электростанций и сетей. Его суть заключалась в организации перехода от ремонтных циклов в календарном исчислении к циклам такого же типа, но учитывающим ранее достигнутые наработки в межремонтных периодах по конкретным типам основного оборудования. Другие условия сохранились неизменными, включая выполнение капитальных и средних ремонтов одновременно по всем видам оборудования энергоблоков, что, естественно, не способствовало сокращению затрат на ремонт и простоев оборудования.
В результате внедрения разработанного проекта совершенствования энергоремонтного производства был осуществлен мягкий переход от жесткой системы регламентации ремонтных циклов к системе ремонтов, учитывающих достигнутую ранее наработку в пределах межремонтных периодов.
Несмотря на эмпирический подход к оценке межремонтных ресурсов был сделан первый шаг к изучению неформализованных процессов технического диагностирования энергооборудования ТЭС.
Указанные разработки были закреплены в руководящем документе РД 34.20.601-96 "Методические указания по совершенствованию системы технического обслуживания и ремонта энергоблоков и энергоустановок ТЭС на основе ремонтного цикла с назначенным межремонтным ресурсом".
Под "мягким" переходом к ремонтам с назначенным межремонтным ресурсом следует понимать некоторое снижение уровня ранее практикуемого административного ресурса в осуществлении нововведений. Предполагалось, что энергообъединения должны самостоятельно принимать решения о внедрении предлагаемых усовершенствований. Здесь нашли свое отражение естественные ожидания ближайшего перехода отечественной электроэнергетики к рыночным отношениям.
Несмотря на не оправдавшиеся до настоящего времени знаковые ожидания, что обусловило лишь частичное внедрение разработанных мероприятий, в общем удалось стабилизировать показатели готовности ТЭС к несению нагрузок. Однако преодолеть рост затрат на техническое обслуживание и ремонт не представилось возможным.
Здесь в известной степени проявился основополагающий фактор командно-административ-ной системы - планирование затрат от ранее достигнутых показателей. Возросли физические объемы - увеличились затраты. Если дополнительные физические объемы удается доказать, то ремонтная составляющая тарифов конечной продукции соответственно возрастает.
Дополнительные к типовым физические объемы ремонта принято относить к "сверхтиповым". Они характеризуются значительно большим содержанием используемых материалов, запасных частей и необходимых конструктивных элементов в виде заменяемых износившихся узлов и зачастую являются доминирующими в ценообразовании ремонтной составляющей тарифов.
В связи с этим не всегда представляется возможность установить устойчивые корреляционные связи между временными показателями простоев оборудования в ремонтах и адекватных им затратами.
Вместе с тем решение задач стабилизации ежегодных простоев оборудования во всех видах ремонтов оказалось достаточно прозрачным и коррелируемым. Увеличение простоев конкретного оборудования или групп оборудования в целом компенсировалось увеличением межремонтного периода, приводящего к сокращению доли оборудования, ежегодно выводимого в капитальные и средние ремонты.
В итоге показатели готовности энергоисточников к несению нагрузок оказались вне зависимости от известных данных о повышенных ремонтных затратах и обеспечили устойчивое функционирование электроэнергетики.
Последующие исследования показали, что только рыночные отношения в сфере энергопроизводства могут создать необходимые условия для стремления к снижению затрат на техническое обслуживание и ремонт объектов электроэнергетики.
Экономическим инструментом очередных ожиданий должны явиться конкурентные отношения среди энергокомпаний, а функциональным - переход на ремонты по техническому состоянию.
При разработке системы ремонтов по техническому состоянию следует учитывать, что отечественная электроэнергетика на стартовом этапе имеет показатели надежности, адекватные зарубежным аналогам, и любые нововведения должны быть достаточно исследованы и обоснованы с тем, чтобы не опорочить их достоинства.
Следует также обратить внимание на то, что наша электроэнергетика функционирует в не-обыч-ном экономическом пространстве. Цены на материалы и изделия машиностроения прибли-жены к мировым. Цены на топливо искусственно занижены по условиям внут-реннего рынка в пропорциях, обратных мировым. Регулируемые тарифы на электрическую и тепловую энергию представляют собой концентрат экономических несоответствий. В таких условиях вряд ли следует рассчитывать на раскрытие каких-либо закономерностей, влияющих на изменение ремонтной составляющей себестоимости продукции.
В сложившейся ситуации представляется целесообразным в большей степени оперировать различного рода физическими величинами, количественными и качественными показателями, такими как показатели надежности, экономичности и др.
2. Стартовые условия дальнейшего совершенствования ремонтного
обслуживания. Среднесрочный прогноз изменений отдельных
характеристик состояния оборудования ТЭС
Оценивая современное состояние теплоэнергетики в области экономики ремонта можно отметить, что за 12 лет (с 1987 г.) удельные к установленной мощности затраты на ремонт в целом по ТЭС сократились на 24 %, а по ТЭС федерального уровня возросли на 2 %.
За этот же период удельные к приведенной выработке затраты на ремонт в целом по ТЭС увеличились на 27 %, по энергоблочным ТЭС "АО-энерго" - на 23 %, а по ТЭС федерального уровня - на 73 %.
При этом количество часов использования установленной мощности сократилось в 1,48 раза.
За период с 1999 по 2001 г. удельные затраты на 1 кВт отремонтированной мощности ТЭС федерального уровня возросли в 3,53 раза.
Приведенные данные свидетельствуют о неблагополучном состоянии экономи
Эффективность использования автотранспортных средств зависит от совершенства организации транспортного процесса и свойств автомобилей сохранять в определенных пределах значения параметров, характеризующих их способность выполнять требуемые функции. В процессе эксплуатации автомобиля его функциональные свойства постепенно ухудшаются вследствие изнашивания, коррозии, повреждения деталей, усталости материала, из которого они изготовлены и др. В автомобиле появляются различные неисправности, которые снижают эффективность его использования. Для предупреждения появления дефектов и своевременного их устранения автомобиль подвергают техническому обслуживанию (ТО) и ремонту.
Техническое обслуживание на предприятии производится самими водителями и при необходимости слесарями по ТО. Заявка на ремонт поступает заведующему авторемонтной мастерской (АРМ), который направляет слесарей в ту или иную зону технического обслуживания. При существующем положении проведение ТО на предприятии постоянно не соблюдается периодичность обслуживания. Вопреки требованиям по организации технического обслуживания в АРМ отсутствуют контрольные осмотры автомобилей, прошедших обслуживание, со стороны отдела технического контроля. Как правило, на ТО направляются автомобили с сопутствующим ремонтом, из-за чего автомобили простаивают в зоне обслуживания больше положенного времени, тем самым нарушая ритм ремонтного производства. Дозаправка, смена моторных и трансмиссионных масел производится примитивными средствами, что способствует потерям ценных нефтепродуктов, нарушению санитарных норм, противопожарных требований, а также требований охраны труда в целом. Кроме того, такая организация труда препятствует нормальному сбору отработанных масел для их регенерации и повторного использования.
В зоне ТО и ремонтном боксе естественное и искусственное освещение также как и температурный режим значительно ниже допустимых норм. Отсутствие искусственной вентиляции приводит к сильной загазованности помещений. Это – также нарушение требований техники безопасности. Малое количество запасных частей, приводит к длительному простою автомобилей в ремонте. Итак, слабая организация технического обслуживания и ремонта подвижного состава проявляется прежде всего в следующем: отсутствие норм времени ТО и ТР непосредственно на участках; недостаточный уровень механизации; несоблюдение отдельных требований техники безопасности, в частности - недостаточная освещённость производственных помещений и отсутствие искусственной вентиляции в зоне ТО. Учитывая значительную роль автомобилей и принимая во внимание приведённый анализ деятельности предприятия в обеспечении достаточной эксплуатационной надёжности подвижного состава следует заключить следующее. Существующая организация технического обслуживания и текущего ремонта подвижного состава требует совершенствования. Необходима разработка мероприятий по совершенствованию организации производственно-технической службы предприятия.
В зависимости от объема работ ТО автомобилей выполняют поточным или тупиковым методом. Организация ТО тупиковым методом (на универсальных тупиковых постах) целесообразна при различной продолжительности пребывания автомобиля на каждом посту. К недостаткам этого метода относятся значительные потери времени на установку автомобиля на пост и съезд с него, загрязнение воздуха отработавшими газами при маневрировании и необходимость использования большого числа одинакового оборудования.
Поточный метод организации ТО предусматривает выполнение работ на специализированных рабочих постах в определенной последовательности с заданным временем выполнения работ. Этот метод позволяет сократить потери времени на перемещение автомобилей и переход рабочих с одного поста на другой, а также более экономно использовать площадь производственного помещения. Недостатком поточного метода организации ТО является сложность изменения объема работ на рабочих местах.
Операции по обслуживанию автомобилей выполняют в соответствии с постовыми технологическими операционными картами. В них указывают наименование операции, тех. условия и нормы времени на ее выполнение, применяемый инструмент и оборудование, специальность рабочего, пост выполнения операции и число точек обслуживания. Постовые технологические карты предназначены для выполнения работ по контролю регулировке и смазыванию агрегата или узла.
При ТО автомобилей на поточных линиях заполняют карту – схему расстановки рабочих на постах. Карта – схема содержит информацию о числе рабочих, производительности линии обслуживания за смену и данные постовых технологических карт.
Организация производства ТО может быть бригадной или бригадно-участковой. При бригадной форме организации бригады выполняют работы по всем агрегатам машины в пределах данного вида обслуживания. При бригадно-участковой форме организации ТО на отдельных производственных участках выполняются все работы по обслуживанию соответствующих агрегатов. В зависимости от программы работ АТП устанавливают различное число производственных участков разного назначения. При небольшой программе работ АТП возможно обслуживание нескольких видов агрегатов на одном участке.
Во всех АТП участки или бригады можно для удобства управления объединить в производственные комплексы по следующим видам работ: техническому обслуживанию машин и диагностированию их технического состояния; текущему ремонту непосредственно на автомобилях; текущему ремонту агрегатов, узлов и деталей, снятых с автомобилей.
Основными направлениями совершенствования ремонтной базы являются:
Совершенствование системы планово-предупредительного ремонта, которое обеспечит четкий надзор и своевременную профилактику работы оборудования, что в свою очередь повысит его производительность, позволит увеличить межремонтные периоды.
Совершенствование технической подготовки ремонта, включающей разработку типовых технологических процессов, а также материальное обеспечение.
Определение оптимальных сроков замены изношенных деталей в зависимости от степени их амортизации и необходимых затрат на ремонтное обслуживание.
Цеха технологического транспорта и цеховые ремонтные службы должны быть максимально специализированы, оснащаться современным оборудованием, позволяющим использовать прогрессивную технологию, передовые формы организации производства, средства механизации и автоматизации производственных процессов.
Показатели работы ремонтных бригад должны обеспечиваться правильным распределением работ между членами бригады.
Для уменьшения простоя автомобилей в ремонте, следовало бы использовать узловой метод ремонта. Сущность метода состоит в том, что узлы и механизмы, требующие ремонта, снимают и заменяют новыми или заранее отремонтированными.
Также необходимо улучшить освещение и температурный режим в ремонтных боксах. Необходима более быстрая поставка запчастей.
Анализ ремонтного хозяйства УП «Полимерпром» имеет целью выявить достижения и недостатки в этой области, наметить пути ликвидации недостатков и мероприятий по совершенствованию системы ППР на заводе.
Основными направлениями совершенствования ремонтного хозяйства УП «Полимерпром» являются:
1. Организация централизованного специализированного ремонта оборудования. Данное условие выполнимо при наличии сервисного центра поставщика оборудования, так как более 70 % оборудования иностранного производства.
2. Организация специализированного производства запасных частей к оборудованию. Представляется возможным с целью снижения затрат на изготовление запасных частей к оборудованию и повышению их качества проведение поиска на тендерной основе изготовителя (изготовителей) из числа станкостроительных и ремонтных предприятий, которые способны изготавливать необходимую для ремонта номенклатуру деталей.
3. Дальнейшее совершенствование на предприятии системы планово-предупредительного ремонта оборудования, которое обеспечит четкий надзор и своевременную профилактику работы оборудования, что в свою очередь повысит его производительность, позволит увеличить межремонтные периоды.
4. Совершенствование технической подготовки ремонта, включающей разработку типовых технологических процессов, а также материальное обеспечение.
Ввиду небольших размеров предприятия ремонтная служба УП «Полимерпром» также имеет ограниченный размер. Поэтому представляется правильным наличие на предприятии действующей централизованной ремонтной службы, выполняющей все функции по обслуживанию и ремонту оборудования.
По отношению к сотрудникам ремонтной службы применяется повременно-премиальная система оплаты труда. Такая форма оплаты труда не является достаточно эффективной. Наиболее эффективной формой оплаты труда является контрактная форма оплаты труда с установлением величины надбавок и премий в зависимости от наличия выходов из строя оборудования по вине работника ремонтной службы, а также от наличия претензий к работе оборудования со стороны начальников участков.
Для повышения эффективности деятельности ремонтной службы, представляется целесообразным использование на предприятии автоматизированной системы управления ремонтной службой.
Необходимо также широко использовать руководящие указания и рекомендации общегосударственного характера, разработки и предложения научно-исследовательских и проектных организаций.
Автоматизированная система управления ремонтной службой является функциональной подсистемой управления, когда при соответствующем организационно-административном делении отдел главного механика является главным координирующим центром и необходимым звеном в комплексной системе управления предприятием. Внедрение этой подсистемы дает возможность с помощью применения ЭВМ и математических методов определить оптимальную стратегию обслуживания и ремонтов оборудования, оптимальную концентрацию объемов работ и концентрацию оборудования для условий специализированного производства ремонтных работ.
С помощью автоматизированной системы управления ремонтной службой следует создать такую организацию ремонта и обслуживания станочного парка предприятий, при которой использование трудовых, материальных и финансовых ресурсов было бы оптимальным, а простои оборудования минимальными.
На основании данных обследования работы ремонтных подразделений разрабатывается экономико-организационная модель управления ремонтным производством, составляются унифицированные формы документов, строится схема документооборота и разрабатывается модель информационных связей, выбираются и разрабатываются экономико-математические методы и модели для механизации и автоматизации экономических расчетов, определяется не обходимое количество и состав технических средств. Экономико-организационная модель является основой создаваемой подсистемы ремонтного производства, определяет принципы ее функционирования и организационные основы системы управления, а также учитывает необходимость широкого развития хозрасчетных отношений, более полного использования принципов материального стимулирования.
При проектировании автоматизированной системы управления ремонтной службой необходима разработка взаимоувязанного комплекса работ для разрешения основных проблем ремонтного производства. Этот комплекс работ ориентируется на создание функциональных управляющих подсистем и необходимых для их функционирования обеспечивающих подсистем.
Функциональные подсистемы реализуют функции управления по организационно-технической подготовке ремонтного производства, прогнозированию и перспективному планированию, технико-экономическому и оперативному планированию, учету, отчетности и анализу хозяйственной деятельности, а также контролю и регулированию работы ремонтных подразделений.
К числу обеспечивающих подсистем относятся: экономико-организационная, информационная, подсистема математического и технического обеспечения. Основной функцией обеспечивающих подсистем является преобразование всей информации, циркулирующей между функциональными подсистемами и производственными подразделениями, для выработки управляющего воздействия на производственные подразделения службы главного механика.
Разработка автоматизированной системы управления ремонтной службой УП «Полимерпром» должна осуществляться специализированными организациями с привлечением предприятия-заказчика либо силами предприятий при наличии достаточного количества специалистов.
При проектировании подсистемы автоматизированной системы управления ремонтной службой необходимо особое внимание обратить на следующие работы:
1. Создание автоматизированного учета наличного парка оборудования по участкам и предприятию в целом; использования работы производственного оборудования по времени и по мощности; учета простоев оборудования в ремонте; отказов и неисправностей каждой единицы оборудования и отдельных узлов, блоков, деталей; потребности, наличия и движения запасных частей для действующего парка оборудования.
Автоматизацию плановых расчетов в условиях работы по планово-предупредительной системе на базе применения современной вычислительной техники, прикладных математических методов и прогрессивных нормативов материальных и трудовых затрат.
Организацию регламентированной смазки оборудования.
Определение оптимальных сроков замены изношенного оборудования в зависимости от степени его амортизации и необходимых затрат на ремонтное обслуживание.
Успешность функционирования автоматизированной системы управления ремонтной службой зависит от того, насколько полно и точно проведены следующие этапы работ: разработка общих положений; предпроектное (диагностическое) обследование работы ремонтных подразделений; техническое проектирование; рабочее проектирование; внедрение подсистемы.
Ремонтное производство характеризуется рядом специфических особенностей, затрудняющих процесс управления и рациональную организацию структурных составляющих (ремонтных подразделений). К числу таких особенностей относятся, прежде всего, неоднородность работ по ремонту.
Экономическое обоснование целесообразности внедрения автоматизированной системы управления ремонтной службой должно сопровождаться расчетом экономической эффективности.
Ремонтно-механические цехи и цеховые ремонтные службы должны быть максимально специализированы, оснащаться современным оборудованием, позволяющим использовать прогрессивную технологию, передовые формы организации производства, средства механизации и автоматизации производственных процессов.
Показатели работы ремонтных бригад обеспечиваются правильным распределением работ между членами бригады, эффективной организацией рабочих мест, применением прогрессивных методов организации ремонта и четкой организацией обслуживания рабочих мест.
Существенным резервом сокращения затрат на ремонт и простоев оборудования в ремонте является многократное использование деталей.
Восстановление деталей позволяет добиться сокращения расхода материальных и финансовых средств при ремонте деталей до 60-90%. Себестоимость восстановленных деталей нередко составляет 10-25% стоимости новой детали.
Заключение
При выполнении ремонтных работ на промышленных предприятиях необходимо стремиться к максимальной концентрации однотипных работ на определенных производственных участках ремонтных служб. Они должны создаваться и оборудоваться в полном соответствии с задачами, которые перед ними поставлены, и объемом работ, подлежащих выполнению.
Основными направлениями совершенствования ремонтной службы предприятия являются:
Организация централизованного специализированного ремонта оборудования;
Организация специализированного производства запасных частей к оборудованию;
Дальнейшее совершенствование системы планово-предупредительного ремонта оборудования;
Совершенствование технической подготовки ремонта, включающей разработку типовых технологических процессов, а также материальное обеспечение ремонтных работ;
Совершенствование планирования, включающее составление планов-графиков проведения ремонтных работ.
Организация ремонтного хозяйства на предприятиях совершенствуется в следующих направлениях.
Ремонтные службы предприятия должны быть максимально специализированы, оснащаться современным либо позволяющим использовать прогрессивную технологию, передовые формы организации производства, средства механизации и автоматизации производственных процессов.
Наиболее эффективно использование специализированных ремонтных бригад. Вместе с тем целесообразно создавать и комплексные бригады, выполняющие все работы по техническому уходу и ремонту оборудования на закрепленном за бригадой производственном участке.
К числу прогрессивных методов ремонта в первую очередь относится узловой. Сущность метода состоит в том, что узлы и механизмы, требующие ремонта, снимают и заменяют новыми или заранее отремонтированными. Применение этого метода позволяет сократить до минимума простои оборудования в ремонте, повысить качество ремонта и сократить затраты на ремонт в связи с возможностью наиболее рациональной организации ремонта узлов и механизмов.
Также существенным резервом сокращения затрат на ремонт и простоев оборудования в ремонте является многократное использование деталей.
Список использованной литературы:
1. Баканов М.И., Шеримет А.Д. Теория экономического анализа. – М.: Финансы и статистика, 2011.
2. Латфуллин, Г.Р. Теория организации: учебник для вузов/ Г. Р. Латфуллин, А. В. Райченко- СПб.: Питер, 2007.
3. Мильнер, Б.З. Теория организации: учебник/ Б. З. Мильнер- М.: ИНФРА-М, 2008.
4. Тертышник, Михаил Иванович Экономика предприятия: учебное пособие для студентов высших учебных заведений, обучающихся по специальности 080101 "Экономическая теория" (рег. номер рецензии 404 от 03.07.2009 г., МГУП) / М. И. Тертышник; Байкальский гос. ун-т экономики и права. - 2-е изд.. - Москва: ИНФРА-М, 2010.
5. Сергеев И.В. Экономика предприятия. – М.: Финансы и статистика, 2013.
6. Анализ хозяйственной деятельности организаций: учебное пособие / под общ. ред. Д. А. Панкова, Е. А. Головковой. - 2-е изд., испр. - М.: Новое знание, 2013.
7. Организация производства на предприятии (фирме): учеб. пособие/ ред.: О. И. Волков, О. В. Девяткина- М.: ИНФРА-М, 2010.
8. Экономика предприятия: учеб. для вузов по экон. спец. / [В. Я. Горфинкель и др.] ; под ред. В. Я. Горфинкеля, В. А. Швандара. - 4-е изд.. - Москва: ЮНИТИ-ДАНА, 2014.
9. Экономика предприятия (в схемах, таблицах, расчетах) : учебное пособие для студентов, обучающихся по направлению 521600 "Экономика" / В. К. Скляренко [и др.] ; под ред. В. К. Скляренко, В. М. Прудникова. - Москва: ИНФРА-М, 2010.
10. Экономика предприятия (фирмы): учебник для студентов высших учебных заведений, обучающихся по эконом. специальностям/ [О. И. Волков и др.] ; под ред. О. И. Волкова, О. В. Девяткина; Рос. экон. акад. им. Г. В. Плеханова. - 3-е изд., перераб. и доп. - Москва: ИНФРА-М, 2009.