Programinės įrangos kokybės užtikrinimo metodai. Gaminių kokybės užtikrinimo metodai skiriasi Šiuolaikiniai kokybės užtikrinimo metodai
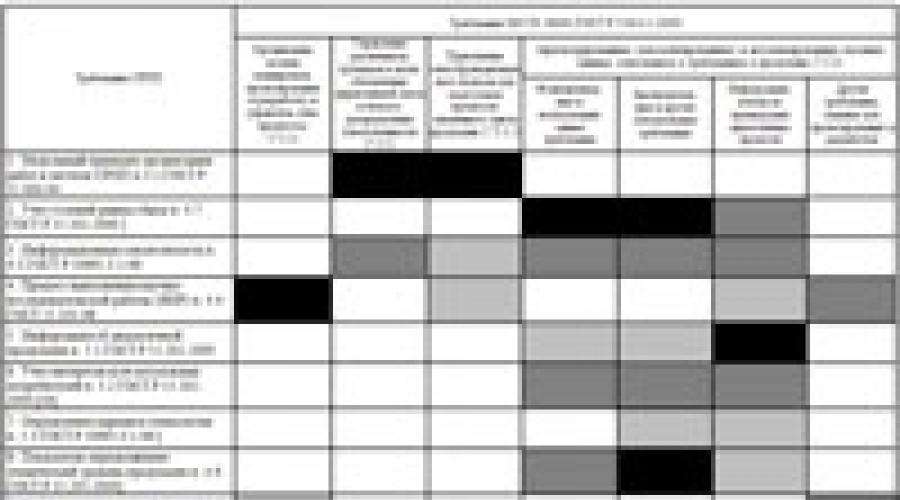
Taip pat skaitykite
Pastaraisiais metais mašinų gamybos įmonėse vis dažniau reikia kurti valdymo sistemas, kurios atitiktų ne pagrindinį ISO 9001 standartą, o patobulintus (modernizuotus pagal to meto reikalavimus ir konkrečios pramonės specifiką) kokybės vadybos sistemų standartus. (pvz., Gazprom, Rusijos geležinkelių ir kt. standartai). P.).
Nors dauguma Rusijos įmonių jau seniai įdiegė ir gana sėkmingai veikia gaminių kūrimo ir paleidimo sistemą (SRPP), atitinkančią Rusijos Federacijos nacionalinius standartus, daugelis vartotojų šiandien reikalauja, kad tiekėjai įdiegtų modernias kokybės valdymo sistemas, pagrįstas pramone. specifiniai standartai (pavyzdžiui, tarptautinis standartas ISO / TU 16949, AS 9100 ir panašus).
Diegiant šiuos standartus, būtina dubliuoti daugelį įmonėje esamų ir esamų procedūrų, įgyvendinančių SRPP standartų reikalavimus. Neabejotina, kad dėl to papildomai švaistomi visų rūšių ištekliai.
Šiandien itin aktuali užduotis sutrumpinti laiką, žmogiškuosius ir finansinius išteklius, skirtus kokybės užtikrinimo metodų ir procedūrų tarptautinių standartų reikalavimams įgyvendinti, naudojant dabartinių Rusijos Federacijos nacionalinių standartų patirtį.
Nepaisant iš pažiūros akivaizdžių pastatų gamybos ypatybių automobilių pramonėje ir kitose mechaninės inžinerijos šakose skirtumų, bendras bruožas yra tai, kad gana mažos įmonės plačiai naudoja komponentų tiekimą pagrindinėms surinkimo gamykloms.
Tokie gamybos organizavimo principai yra gerai išvystyti beveik visose automobilių gamyklose (tiek vidaus, tiek užsienio), jie taip pat naudojami naftos ir dujų inžinerijoje - gamyklose, gaminančiose sudėtingas technologines sistemas: gręžimo įrenginius, kompleksus atviroje jūroje esančių laukų plėtrai ir kt. Panašių pavyzdžių galima rasti ir kitose pramonės šakose.
Kadangi automobiliai yra daug didesnės masinės paklausos produktas, būtent šioje pramonės šakoje gamintojai turėjo skirti ypatingą dėmesį tokių kokybės valdymo sistemų kūrimui, kurios atitiktų šiuolaikinius gamybos organizavimo principus, be to, galėtų tuo pačiu prisideda prie produktų kokybės gerinimo. ... Be to, automobilių pramonė savo pramonės kokybės standartų sistemą sukūrė daug anksčiau, nei atsirado jos poreikis kitose srityse.
Šiame kontekste neabejotinai įdomus darbas kokybės vadybos sistemos formavimo srityje, kuris šiuo metu vyksta automobilių įmonėse. Daugiau nei tikėtina, kad, atsižvelgiant į nedidelius pakeitimus, pasiekti rezultatai gali būti pritaikyti bet kurioje mašinų gamybos gamykloje.
Gerai žinoma, kad norėdami parodyti vartotojui, kaip įmonė stebi savo gaminių kokybę ir šią kokybę garantuoti, gamintojai kuria kokybės vadybos sistemas, atitinkančias ISO 9001, ISO / TU 16949 reikalavimus, taiko ten aprašytus metodus.
Rusijoje dabar pastebima tendencija pereiti nuo nacionalinių standartų prie tarptautinio standarto ISO / TU 16949, kuris taikomas automobilių pramonei ir organizacijoms, gaminančioms atitinkamas atsargines dalis. Dėl to, kad ISO / TU 16949 buvo išleistas kartu su kokybės vadybos sistemų standartu, jis turi daug bendro su pastaruoju, tačiau turi ir savo ypatybių, nes ISO / TU 16949 sukūrė Tarptautinė automobilių pramonė. Darbo grupė (IATF) ir Japonijos automobilių gamintojų asociacija, registruota korporacija (JAMA), remiama Techninio komiteto ISO / TC 176, Kokybės valdymas ir kokybės užtikrinimas.
Didieji automobilių gamintojai jau sertifikuoja arba planuoja sertifikuoti savo kokybės valdymo sistemas pagal tarptautinį standartą ISO / TU 16949 ir reikalauja to iš savo tiekėjų. Pavyzdžiui, tokius reikalavimus savo tiekėjams kelia „didžiojo trejeto“ – DaimlerChrysler, General Motors, Ford – atstovai.
Atkreiptinas dėmesys, kad ISO / TS 16949 standarto įgyvendinimui reikia naudoti specialius darbo organizavimo metodus – APQP (Advanced Product Quality Planning and Control Plan), PPAP (Production Part Approval Process) automobilių komponentų gamybos patvirtinimą. ), taip pat kai kurių kokybės užtikrinimo priemonių panaudojimas naudojant statistinius analizės metodus – FMEA (Galimų gedimų režimo ir padarinių analizės metodas – Galimų defektų tipų ir pasekmių analizės metodas), MSA (Matavimo sistemų analizė – Analizės matavimo sistemos ), SPC (Statistinės procesų kontrolės metodai) ir QSA (Vadybos kokybės sistemų analizė).
Didžiausius sunkumus šalies įmonėse sukelia APQP (Advanced Product Quality Planning) darbo organizavimo metodo įdiegimas, iš tikrųjų - automobilių komponentų gamybos planavimo, kūrimo ir paruošimo procesas, leidžiantis visiškai užtikrinti. visi vartotojo reikalavimai ir lūkesčiai jau gamybos paruošimo stadijoje, kai yra pagrindinės galimybės Defektų prevencija, Sunkumai kyla dėl to, kad šis procesas liečia beveik visus padalinius ir visus procesus organizacijoje ir turi būti įgyvendinamas visuose etapuose gaminio gyvavimo ciklo – nuo automobilių komponento sukūrimo, projektavimo ir tobulinimo planavimo iki serijinės gamybos.
Rusijoje yra sistema, panaši į APQP - produktų kūrimo ir paleidimo sistemą (SRPP).
Kaip žinote, SRPP yra tarpusavyje susijusių esminių organizacinių, metodinių ir bendrųjų techninių valstybės standartų kompleksas, kuriame nustatomos pagrindinės nuostatos, taisyklės ir reikalavimai, užtikrinantys techninį ir organizacinį gaminio gyvavimo ciklo etapuose atliekamų darbų vieningumą (LCP). ).
SRPP yra susieta su kitų bendrųjų techninių sistemų standartais ir standartų rinkiniais: vieninga projektavimo dokumentavimo sistema (ESKD), vieninga technologinio dokumentavimo sistema (ESTD), vieninga programinės įrangos dokumentavimo sistema (ESPD), valstybine sistema. už matavimų vienodumo užtikrinimą ir produkto kūrimo technologinę pagalbą.
Šiuo metu daugelis įmonių specialistų yra susirūpinę dėl šios problemos - įmonės jau įdiegė ir sėkmingai veikia produktų kūrimo ir paleidimo į rinką sistemą pagal Rusijos Federacijos nacionalinius standartus. Tačiau ateina laikas, kai vartotojas – tam tikras automobilių gamintojas – reikalauja iš savo tiekėjo įdiegti kokybės valdymo sistemą pagal tarptautinį standartą ISO / TU 16949, įskaitant, žinoma, APQP metodo, kaip neatskiriamos dalies, įdiegimą. tokia kokybės vadybos sistema. Ekspertai supranta, kad jie turi dubliuoti daugelį jau vykstančių procesų, o tai lydi papildomos neracionalios išlaidos.
Šią situaciją gyvai aptarinėja su ja susidūrę ekspertai. Tiesa, dažniausiai ekspertai tik spėlioja, kaip įdomiai tarptautinių organizacijų (Tarptautinės automobilių pramonės darbo grupės (IATF)) reikalavimai sutampa su mūsų senų, seniai naudojamų nacionalinių standartų, kurie buvo sukurti dar 2010 m. praėjusio amžiaus aštuntajame ir devintajame dešimtmetyje.
Taigi iškyla problema – kaip mažiausiomis sąnaudomis įgyvendinti ISO / TU 16949 standarto reikalavimus, įskaitant mums vis dar egzotišką APQP metodą, įmonėje, kurioje įdiegtas ir sėkmingai veikiantis SRPP.
Mūsų tyrimo tikslas buvo sukurti tarptautinių kokybės vadybos sistemų kūrimo Rusijos įmonėse algoritmą, atsižvelgiant į sukauptos ankstesnės vidaus sistemų veikimo patirties specifiką ir tuo pačiu optimizuojant įvairių išteklių sąnaudas: darbo, finansų, laiko ir kt.
Autorius išanalizavo ISO / TU 16949 standarto ir APQP metodo reikalavimų suderinamumo su SRPP nacionalinių standartų reikalavimais laipsnį. Tam buvo sukurtos aukščiau minėtų dviejų sistemų reikalavimų atitikimo matricos, kuriose SRPP reikalavimus atitinka 45 eilutės, o po 49 stulpelius atitinka ISO / TU 16949 ir APQP reikalavimus. Kiekvienas eilučių ir stulpelių sankirtos elementas buvo toliau analizuojamas derinant ekspertų sprendimus ir regresinės analizės metodus.
Norėdami tiksliau suprasti, koks buvo reikalavimų apibendrinimo laipsnis, kaip APQP metodo reikalavimai buvo suskirstyti į grupes ir kurie SRPP reikalavimai buvo įvertinti dėl jų suderinamumo su APQP proceso reikalavimais, apsvarstysime. maža matricos dalis labiau padidinta forma. Matricos fragmentas pateiktas 2 lentelėje.
2 lentelė. SRPP ir ISO / TU 16949 reikalavimų suderinamumo matricos fragmentas
Atlikus analizę paaiškėjo, kad kai kuriais atvejais yra (visiškas arba dalinis) ISO / TU 16949 ir APQP reikalavimų suderinamumas su SRPP reikalavimais ir atvirkščiai. Todėl toliau buvo atliktas kiekybinis ISO / TU 16949 ir APQP metodo reikalavimų suderinamumo laipsnio įvertinimas, kuris parodė, kad visiškas reikalavimų sutapimas nustatytas 15% atvejų, o dalinis reikalavimų sutapimas - 13% atvejų. Be to, buvo nustatytos situacijos, kai reikalavimai gali būti tarptautinių standartų įgyvendinimo pagrindas: ISO / TU 16949 ir APQP reikalavimų grupė tiesiogiai nesutampa su SRPP reikalavimais, tačiau jei pastarieji kažkaip papildomi, tada įvyks visiškas ar dalinis sutapimas... Tokių situacijų buvo apie 22 proc. Galiausiai atvejų, kai atitikimas nereikšmingas, skaičius yra 12%, o 38% atvejų nerasta atitikties.
Pavyzdžiui, GOST R 15.201-2000 5.2 punktas teigia: „Rekomenduojame atsižvelgti į visų galimų vartotojų interesus techninėje užduotyje“. Savo ruožtu, kaip įvestis pirmajame APQP metodo etape, būtina turėti „informaciją iš konkrečių vartotojų“. Tyrimas parodė, kad reikalavimai visiškai sutampa.
Kitas pavyzdys: GOST R 15.201-2000 4.6 punkte nustatytas reikalavimas, kad produkto kūrėjas, atlikdamas mokslinius tyrimus, plėtrą ir technologinius darbus, ypatingą dėmesį turėtų skirti tam, kad būtų užtikrintas, visų pirma, gaminio rodiklių, kurie lemia, apskaitos reikalavimai. tai techninis lygis. APQP procesas susijęs su konkurentų produktų / procesų etalonais. Šiuo atveju buvo pripažinta, kad reikalavimai sutapo. Panaši situacija ir su tokiais reikalavimais kaip privalomas technologinis gaminių tobulinimas pagal GOST R 50995.3.1-96 5.2.6 punktą ir „produkto ir proceso prielaidos“ poreikis pagal APQP metodo reikalavimus.
Remiantis šio darbo rezultatais, galima daryti tokią išvadą – diegiant ISO / TU 16949 ir APQP darbo organizavimo metodą įmonėse, kuriose įdiegtas ir sėkmingai veikiantis SRPP, galima ženkliai sumažinti išteklių sąnaudas.
Sąnaudas galima sumažinti dėl to, kad tų ikigamybinio proceso valdymo elementų, kurie jau buvo įdiegti įmonėje pagal SRPP standartų reikalavimus, nereikia diegti iš naujo, jeigu jie yra numatyti paraiškoje. ISO / TU 16949 ir APQP. Pakaks išsiaiškinti terminų skirtumus įmonės dokumentacijoje. Visi puikiai suprantame, kad toks požiūris gali ženkliai sutaupyti ISO / TU 16949 ir APQP metodo diegimo laiką bei sumažinti įgyvendinimui reikalingus žmogiškuosius ir materialinius išteklius.
Pažymėtina, kad buvo atlikta gana paviršutiniška esamos situacijos analizė. Visų pirma, SRPP standartų reikalavimai buvo suskirstyti tik į 45 grupes, ISO / TU 16949 ir APQP metodo reikalavimai - į 49 grupes, kurių tikriausiai nepakanka pilnam ISO / reikalavimų suderinamumo įvertinimui. TU 16949 ir APQP su SRPP standartų reikalavimais; Taip pat pažymėtina, kad reikalavimų suderinamumui vertinti buvo naudojama tik 5 kategorijų skalė, kuri taip pat tik apytiksliai įvertina reikalavimų suderinamumą.
Taip pat pažymėtina, kad priklausomai nuo įmonės specifikos ir bendros veiklos krypties, įvairių tiek SRPP standartų, tiek ISO / TU 16949 ir APQP reikalavimų įgyvendinimo tvarka gali skirtis. Tačiau tuo pat metu reikia turėti omenyje, kad kai kurie reikalavimai gali būti tarpusavyje susiję ir tuomet yra neginčijama jų įgyvendinimo tvarka. Į šią situaciją reikia atsižvelgti kartu įgyvendinant SRPP ir ISO / TU 16949 standartus.
Atsižvelgiant į tai, kas išdėstyta aukščiau, buvo sukurta gamybos organizavimo schema, kurią pavadinome „organizaciniu modeliu“ (1 pav.). Organizacinis modelis leidžia nustatyti veiksmų seką projektavimo, gaminių kūrimo ir paleidimo į gamybą stadijoje bei gaminių gamybos metu, nustatyti ir lokalizuoti kliūtis, imtis konkrečių veiksmų joms pašalinti, paskirstyti atsakomybę ir įgaliojimus abiejuose padaliniuose. atsakingas už produkto išleidimą ir visoje organizacijoje.
1 pav. Organizacinis modelis „Gamybos ir paslaugų valdymas“
Sukurtas organizacinis modelis pritaikomas bet kuriai pramonės įmonei. Organizacinis modelis gali būti naudojamas nustatant įgyvendinimo tvarką ir paskirstant darbus, diegiant modernius kokybės vadybos metodus mašinų gamybos įmonėje, kuri turi veikiančią valdymo sistemą, pagrįstą įdiegtais SRPP nacionalinės sistemos standartais.
Analizėje taip pat nebuvo atsižvelgta į tokį veiksnį kaip kai kurie netikslumai ir susitarimai verčiant tekstą, aprašantį APQP metodą. Tokioje situacijoje, nustatant reikalavimus, gali būti labai sunku atsižvelgti į sinonimus – juk kai kurie reikalavimai gali net visiškai sutapti, bet tuo pačiu būti išreikšti visai kitais žodžiais.
Analizės rezultatai leidžia sukurti specifinį tarptautinių standartų reikalavimų įgyvendinimo algoritmą, atsižvelgiant į įmonėse veikiančią PSPP sistemą, kuri gali žymiai sumažinti laiką, žmogiškuosius ir finansinius išteklius ir tuo pačiu panaudoti didžiulis bagažas, kurį mums paliko mūsų pirmtakai – sovietiniai inžinieriai – nacionalinių standartų kūrėjai. Šis algoritmas bus aprašytas kitoje autoriaus publikacijoje.
Natalija V. VAŠČENKO- ANO koordinavimo centro „ATOMVOENCERT“ Sertifikavimo ir darbo organizavimo skyriaus vedėjas
Naudotų šaltinių sąrašas
1 Kudriašovas A.V. Apvalus stalas. APQP: problemos ir įgyvendinimo patirtis // Kokybės vadybos metodai. - 2012. - Nr.6.
2 Kershenbaum V.Ya., Vaschenko N.V. Vidaus ir užsienio norminių reikalavimų atitikimo kokybės vadybos sistemų kūrimo praktikoje vertinimo metodika // Kokybės vadyba naftos ir dujų komplekse. - 2013. - Nr.1. - Su. 17-21.
3 Vaschenko N.V. Dėl dokumentuotos procedūros tikslingumo įgyvendinant ISO 9001:2008 septinto skyriaus reikalavimus // Kokybės vadyba naftos ir dujų komplekse. - 2013. - Nr. 2. - Su. 14-18.
Daugybė statistinių duomenų apie kokybę rodo, kad apie 85-90% gaminių trūkumą lemia žmogiškieji veiksniai. Apsvarstykite, kokios su darbuotoju susijusios priežastys gali turėti įtakos techninės dokumentacijos nesilaikymui, įskaitant gaminių su trūkumais. Tarp jų galima pastebėti: žemą kvalifikaciją, trumpą darbo patirtį, silpną sveikatą, nedėmesingumą susipažįstant su brėžiniais, technologijomis ar instrukcijomis, nekokybišką darbo vietos paruošimą.
Reikia pabrėžti, kad santuokos priežastys gali būti siejamos ne tik su žmogumi, bet ir su įrankiu, technologine įranga, įrankiais. Tai tiesa, tačiau dažniausiai taip nutinka ne tiek dėl paties įrankio, įrangos ar įrankių trūkumų, kiek dėl neatsargaus jų galandimo, nekokybiško remonto ar netiksliai darbuotojų atliekamo gamybos ir surinkimo. Jei „pateksite į dugną“ broko kaltininkui, tai didžioji dauguma bus asmuo, kuris dirba nebūtinai jūsų įmonėje, o, galbūt, tiekėjo įmonėje.
Nuo ko pradėti gerinti kokybę? Japonijos ekspertai pataria pradėti nuo kokybės darbo vietoje. Be to, jie sukūrė nuoseklią kokybės gerinimo darbo vietoje sistemą, kurią vadina „5S“ (gera namų priežiūros praktika). Pavadinimas kilęs iš penkių japoniškų žodžių, prasidedančių raide „C“: seiri (rūšiavimas), seiso (valymas), seiton (organizacija), seiketsu (standartizavimas), shitsuke (savęs patikrinimas). Šių žodžių vertimas į rusų kalbą suteikia, jei ne visiškai aiškų, tai pakankamai supratimą apie apytikslį priemonių, skirtų darbo kokybei gerinti, turinį. Jei trumpai apibūdinsime šią sistemą, galime pasakyti, kad „prieš pradėdami dirbti ir net atsakingai, turite suprasti tvarką savo darbo vietoje“.
Pateikime aiškesnį kiekvieno „5S“ sistemos etapo turinį. Prieš pradedant jį įgyvendinti, būtina išsamiai aprašyti, o jei įmanoma, nufotografuoti darbo zoną (ar darbo vietą), kurią reikia pertvarkyti. Darbo sričių (vietų) aprašymų palyginimas prieš ir po pertvarkos gali turėti palankų įspūdį vadovybei, o tai suaktyvina darbą įmonėje kokybei.
1 etapas. Rūšiavimas. Kasdien naudojamus daiktus (ar daiktus) sudėkite į vieną vietą. Daiktus, kurie naudojami kartą per savaitę, reikėtų dėti į kitą vietą, kas mėnesį – į trečią, o tuos, kurių prireikia labai retai – į ketvirtą. Atlikite šią procedūrą kiekvienai darbo vietos sričiai. Tada iš kiekvienos saugojimo vietos pasirinkite ir palikite po vieną kiekvieno tipo daikto kopiją, o likusią perkelkite į spintelę atsarginėms dalims laikyti.
2 etapas. Valymas. Nuvalykite visus darbinius paviršius, prieš vėl ką nors ant jų padėdami. Įsitikinkite, kad šalia darbo zonos yra tinkami konteineriai atliekoms surinkti. Visas atsargines dalis dėkite į bendrą sandėlį. Sudarykite į sandėlį grąžintų prekių sąrašą, kad galėtumėte apie jas pranešti dirbtuvių vadovybei. Sutvarkykite ir sudėkite visus reikalingus dokumentus vienoje vietoje bei išvalykite visus įrankius. Nustatyti švaros standartus (normas), kurių turi laikytis kiekvienas darbuotojas.
3 etapas. Organizavimas. Tvarkingai išdėliokite visus popierius ir aplankus. Kasdien naudojami daiktai turi būti darbuotojui po ranka. Kartą per savaitę naudojami daiktai gali būti išdėstyti vieno žingsnio atstumu, o kartą per mėnesį naudojami daiktai – 2-3 žingsnių atstumu. Visa kita gali būti už kelių žingsnių nuo darbo vietos. Būtina aiškiai apibrėžti kiekvieno daikto vietą.
4 etapas. Standartizavimas. Supažindinkite visus su šia darbo vieta susijusius darbuotojus su švaros standartais ir pateikite „teisingo“ standarto nustatymo nuotraukas. Jei reikia, aprūpinkite įrangą ir įrankius su skaidriais dulkių dangteliais. Jei šie dangčiai yra nepermatomi, darbuotojai gali laikyti po jais ne darbo vietai skirtus daiktus.
5 etapas. Savikontrolė. Maždaug po mėnesio atidžiai ištirkite darbo vietos būklę, kad pamatytumėte, ar galima ją pagerinti. Jei radote papildomų prekių, nusiųskite jas į bendrą sandėlį. Peržiūrėkite grynumo standartus ir, jei reikia, pataisykite. Pakartokite šį veiksmą po mėnesio.
Taip pat galite rekomenduoti papildomų priemonių tvarkai darbo vietoje palaikyti. Taigi, pavyzdžiui, galite sukurti kilnojamas lentas su įrankiais konkretiems darbams arba ant lentų nubrėžti įrankių kontūrus, kad iš karto būtų aišku, kokio įrankio trūksta.
Japonijos mokslininkai mano, kad jei įmonių vadovai negali įdiegti 5S, jie negali efektyviai valdyti. Ir atvirkščiai, jei įvaldote sistemą, tai reiškia, kad galite lygiai taip pat sėkmingai įdiegti ir kitas, sudėtingesnes sistemas. Tokios išvados priežastis yra ta, kad „5S“ sistemai įdiegti nereikia specialių vadovų darbuotojų ir netaps efektyvi tol, kol visi darbuotojai nebus įtraukti į ją ir pradės galvoti apie šios sistemos sėkmę. Bet jei 5S sistema jau buvo įdiegta, tai galime manyti, kad kitos sistemos yra beveik pusiau įsisavintos (kalbant apie personalo pasirengimą įgyvendinti pokyčius).
Nuo 80-ųjų vidurio. XX amžiuje Japonijos įmonėse 5S sistema buvo pagrindinė valdymo mąstymo ir filosofijos dalis. Įmonių vadovybė visur priėjo prie nuomonės, kad ši sistema yra pagrindinis valdymo metodas bet kurioje, net pažangiausioje veiklos srityje.
Pastaraisiais metais 5S sistema tapo plačiai žinoma Rusijos įmonėse. Iš vidaus praktikos diegiant šią sistemą galima padaryti tokias išvadas:
- - jis taikomas ir gali būti sėkmingai įgyvendinamas šalies įmonėse ir įvairių nuosavybės formų organizacijose, jei vadovybė tuo suinteresuota;
- - sistemos principų turinys ir jos įgyvendinimo technologija reikalauja reikšmingo prisitaikymo prie šalies ūkio ypatumų, gamybos organizavimo metodų ir personalo mentaliteto;
- - sėkmingo sistemos diegimo galimybė tiesiogiai priklauso nuo socialinių-ekonominių darbo sąlygų darbo vietoje, t.y. darbo užmokesčio mokėjimo lygis ir reguliarumas, sistemingas ir ritmiškas gamybos krūvis, administracijos atitikimas bent jau baziniams saugių darbo sąlygų reikalavimams.
Šią sistemą bandyta modernizuoti, atsižvelgiant į mokslinio darbo organizavimo principus ir kokybės gerinimo praktiką. Naujoji sistema, apjungusi „5S“ sistemos elementus ir pritaikyta vidaus gamybos sąlygoms, buvo pavadinta „Užsakymu“ (2.4 lentelė). Pagrindiniai šios sistemos principai yra šie:
- - pašalinti visus nereikalingus;
- - reguliariai atlikti kruopštų valymą ir tikrinti įrangos bei inventoriaus tinkamumą naudoti;
- - viską išdėstyti darbo vietoje patogiausiu būdu;
- - parengti saugojimo, naudojimo, valymo ir tikrinimo standartus (taisykles);
- - nuolat ir sąmoningai laikytis priimtų taisyklių.
2.4 lentelė
Sistemų „5S“ ir „Užsakymas“ principų palyginimas
1. Dalyvauja visa komanda. Kaip neįmanoma „užvirti vandens viename baseino kampe“, taip ir ši sistema negali būti efektyviai įdiegta vienoje darbo vietoje ar viename skyriuje vieno žmogaus užsakymu. Naujoji sistema reikalauja visos komandos ryžto ir darnos.
Kiekviena sistemos taisyklė, kurią reikia įvykdyti, pati savaime nėra sunki. Sunkumas yra nenustoti to daryti. Tam reikia užsispyrimo ir bendradarbiavimo, o tai savo ruožtu sukuria priklausymo komandai jausmą ir gerina įmonės atmosferą.
2. Mokymosi lengvumas - atrodo. Iš pirmo žvilgsnio „Sequencing“ sistemos principai atrodo tokie aiškūs ir lengvai įgyvendinami. Tačiau kodėl taip sunku juos įgyvendinti?
Iš pažiūros šių principų įgyvendinimo paprastumas kyla dėl to, kad darbuotojai iki galo nesuvokia, kas yra „Užsakymo“ sistema. Tai ne vienkartinis generalinis valymas, ne įrankio perkėlimas iš vienos vietos į kitą, o iš esmės naujas požiūrio į darbo aplinką, jos organizavimą ir saugą stilius, stilius nuolat palaikyti itin tvarkingą, švarią darbo erdvę.
3. Nuo korekcijos iki prevencijos. Dažnai galite stebėti, kiek laiko vadovai skiria taisydami, kas buvo padaryta neteisingai ar ne laiku. Jie reaguoja į bėdas po fakto. Tačiau susipažinus su problemomis tampa aišku, kad daugelio jų priežastys dažnai būna labai paprasti dalykai.
Laiku pastebėti įrangos veikimo sutrikimai, nustatyti įrangos ar inventoriaus gedimai gali išvengti didelių nuostolių ir nelaimingų atsitikimų. Net ir bet kokios „smulkmenos“ susiklosčius nepalankioms aplinkybėms gali atnešti didelių bėdų.
- 4. Iš rezultatų valdymo - proceso kontrolei. Labai dažnai vadovai linkę matyti tik veiklos rezultatus ir spręsti apie savo darbo efektyvumą. Diegiant „Užsakymo“ sistemą, reikia išmokti įžvelgti priežastis, vedančias prie tam tikrų rezultatų, matyti visą procesą kaip visumą, jo stipriąsias ir silpnąsias puses.
- 5. Dėmesys pagrindinių reikalavimų tenkinimui. Personalas turi priprasti prie nuolatinio pagrindinių reikalavimų vykdymo. Pavyzdžiui, patikrinti, ar ant svarbių daiktų ar objektų yra visų užrašų ir etikečių.
- 6. Kiekvieno darbuotojo atsakomybės už savo darbo rezultatus stiprinimas. P. Fordas kartą yra pasakęs, kad „net pats kvailiausias darbuotojas gali rasti šimtą būdų, kaip apgauti labiausiai kvalifikuotą meistrą“. Tai patvirtina, kad gamyboje didelį teigiamą vaidmenį gali turėti tik asmeninės darbuotojo atsakomybės veiksnys ir jo susidomėjimas darbu, o ne nuolatinis darbo reguliavimas ir griežta kontrolė. Reikia tokios atmosferos, kurioje žmonės padėtų vieni kitiems ir visi stengtųsi gerai atlikti savo darbą.
- 7. Instrukcijų supratimas ir jų reikalavimų laikymasis. Labai dažnai nurodymų ir reikalavimų nesilaikoma ne todėl, kad darbuotojai jų nepaiso, o todėl, kad arba nežino, arba iki galo nesuvokia juose esančių reikalavimų ar rekomendacijų esmės.
„Užsakymo“ sistema leidžia darbuotojams savarankiškai kurti konkrečias taisykles ir instrukcijas, susijusias su jų darbo vieta.
8. Laipsniškas (žingsnis po žingsnio) požiūris. Akivaizdu, kad „Racionalizavimo“ sistema, pirmiausia orientuota į darbuotojų elgsenos stereotipų keitimą, negali būti įdiegta greitai ir iškart po jos įgyvendinimo pradžios bei duoti apčiuopiamų rezultatų. Naujoji sistema yra pirmasis žingsnis link ilgalaikės įmonės atkūrimo programos.
Sistemos diegimo technologija numato metodišką, laipsnišką, žingsnis po žingsnio jos principų įsisavinimą, kiekvieno žingsnio rezultatų įvertinimą ir konsolidavimą.
9. Sistema „Užsakymas» - tai yra sunkus kelias. Naujoji sistema, kaip ir japoniškas 5S, veikia pagal principą: „Veiksmai kalba garsiau nei žodžiai“. Bet koks didelis darbas prasideda nuo smulkmenų, nuo laipsniško problemos esmės suvokimo, nuo klaidų ir taisymų. Niekada neturėtumėte atsisakyti pagalbos, patarimų, pagalbos iš kolegų ir inžinierių. Tikras progresas, laipsniškas, net ir mažais žingsneliais, yra daug naudingesnis nei visuotinės diskusijos apie didelį projektą, galintį pakeisti gamybos struktūrą tam tikroje darbo vietoje.
Aukščiau aptarti metodologiniai požiūriai ne tiek atskleidžia „Užsakymo“ sistemos principų įgyvendinimo turinį ir technologiją, bet paaiškina kliūtis, sunkumus ir sunkumus, su kuriais susidurs diegiant tiek šią sistemą, tiek „5S“. “ sistema.
Jei Japonijos darbuotojui visiškai pakanka įmonės vadovybės pasitikėjimo, kad 5S sistemos įdiegimas bus labai naudingas ne tik įmonei, bet ir pačiam darbuotojui, kad ilgalaikė motyvacija diegti ši sistema praktiškai vykdoma, tada Rusijos įmonės darbuotojui to aiškiai nepakanka ... Reikalingi veiksmingi mechanizmai, kurie skatintų darbo vietų gerinimą ir gaminių bei darbo kokybę kiekvienoje darbo vietoje. Kaip visada, Rusijos įmonėse viskas, kas susiję su tobulėjimu ir racionalizavimu, įskaitant darbo vietas, praktiškai priklauso ne nuo sistemos, ne nuo efektyvių paskatų, o tik nuo asmeninės iniciatyvos. Tokio rimto reikalo kaip 5S ar Streamlining sistemų diegimas negalima kaltinti vien gamyklų entuziastų.
Yra nuomonė, kad jei visus darbus pavyktų atlikti „avariniu būdu“, tai Rusija čia neturėtų konkurentų, o darbas, susijęs su kasdieniu kruopščiu tvarkos ir švaros darbu, neatitinka mūsų mentaliteto. Iš čia ir reikalingas išsamus paaiškinimas naudojant metodinius metodus, kaip atlikti iš esmės gana paprastą darbą, o tai yra „Užsakymo“ sistemos principai.
Jeigu norime gyventi civilizuotai, kaip, pavyzdžiui, Japonijoje ar Europoje, tai naujieji vadovai turi įkvėpti darbuotojus, kad darbo kokybė priklauso ne nuo tautos mentaliteto, o nuo gebėjimo ir noro. atitikti visus reikalavimus, užfiksuotus tiek gaminių techninėse specifikacijose, tiek tarptautiniuose standartuose ISO 9000. Ir ne tik diegti, bet ir organizaciškai bei materialiai užtikrinti reikiamų standartų įgyvendinimą.
Studijuodamas šio skyriaus medžiagą, studentas privalo:
žinoti
- septyni gaminių kokybės kontrolės įrankiai;
- statistiniai gaminių kokybės kontrolės metodai;
- funkcinių kaštų analizė;
- modernios kokybės vadybos technologijos (šešių sigmų koncepcija, QFD metodas ir kt.);
galėti
- sukurti priežastinę Ishikawa diagramą ir Pareto diagramą, kad būtų galima valdyti prekių ir paslaugų kokybę;
- taikyti QFD metodą, kad būtų galima sekti klientų poreikius visuose gaminio gyvavimo ciklo etapuose;
- taikyti funkcinę ir kaštų analizę, kad būtų pasiektos būtinos prekės (paslaugos) vartotojiškos savybės su minimaliomis jų teikimo sąnaudomis;
savo
- septynių į prekybą patenkančių prekių kokybės kontrolės įrankių naudojimo įgūdžiai;
- statistiniai į prekybą patenkančių prekių kokybės valdymo metodai.
Metodų reikšmė ir klasifikacija
Kaip minėta aukščiau, Ch. 2 d., vienas iš SM K principų – sprendimo priėmimo pagrindas turi būti tik faktai, o ne intuicija. Viena iš kokybės valdymo klaidų priežasčių yra ta, kad faktai painiojami su subjektyviais sprendimais. Norint išvengti klaidų, reikėtų organizuoti faktų paieškos procesą, t.y. statistinė medžiaga.
Matematinė statistika, apimanti daugybę skirtingų metodų, yra susijusi su rezultatų rinkimu, apdorojimu ir analize. Japonijos mokslininkai (pirmiausia profesorius K. Ishikawa) pasirinko iš šio rinkinio septynios esminės kokybės kontrolės priemonės(4.1 pav.). Kokybės ratas vaidino svarbų vaidmenį įsisavinant statistinius metodus Japonijoje.
Ryžiai. 4.1.
Serijinės ir masinės produkcijos gamybos metu augant gamybos apimtims, vartotojui (kaip juridiniam asmeniui) ir pačiam gamintojui prireikė informacijos apie realią gaminamos ir perkamos produkcijos kokybę. Tačiau dėl didelės pagamintų produkcijos partijų apimties buvo sunku atlikti pilną kokybės kontrolę, o jos patikimumas buvo žemas. Siekiant sumažinti darbo intensyvumą ir padidinti patikimumą, jie pradėjo naudoti imčių kokybės kontrolės statistiniai metodai. Jų reikšmė labai paprasta: ištyrę nedidelę gaminių dalį (pavyzdį), galite padaryti patikimas išvadas apie visos partijos kokybę.
Aštuntojo dešimtmečio pabaigoje ir devintojo dešimtmečio pradžioje. Japonijos mokslininkų ir inžinierių aljansas sukūrė sudėtingesnį kokybės kontrolės įrankių rinkinį. Šios priemonės buvo pagrįstos tiek matematinės statistikos metodais, tiek kitų mokslų metodais: operacine analize, optimizavimo teorija ir kt. Kaip subtilesnės priemonės buvo skirtos inžinieriams. Šie metodai vadinami kokybės valdymo įrankiai.Ši pamoka apima kai kurias kokybės valdymo priemones: programą „Šeši sietai“, kokybės funkcijų diegimo technologija, funkcinių kaštų analizė.
Toliau aprašomos trys metodų grupės:
- 1) pagrindinės kokybės kontrolės priemonės;
- 2) statistiniai atrankos kokybės kontrolės metodai;
- 3) kokybės valdymo įrankiai.
Pagrindinės kokybės kontrolės priemonės
Pagrindinės kokybės kontrolės priemonės yra produktų kokybei įtakos turinčių sąlygų ir veiksnių statistinės analizės metodai. Statistinė analizė apima santuokos tipų ir priežasčių analizę, atskirų technologinio proceso veiksnių įtakos kokybės rodikliams analizę. Atliekant analizę, kokybiškiems duomenims vizualizuoti rekomenduojama naudoti specialius grafinius metodus (kartais vadinamus aprašomąja statistika). Šie metodai apima septynias kokybės kontrolės priemones (žr. 4.1 pav.).
Kontrolinis sąrašas (lapas)- duomenims rinkti ir tvarkyti skirta priemonė, palengvinanti tolesnį surinktos informacijos naudojimą.
Fig. 4.1. Neatsitiktinai valdymo lapas yra centre, apsuptas kitų 6 prietaisų. Ji atlieka ypatingą vaidmenį, nes bet kokios kokybės analizės užduoties vykdymas prasideda nuo pradinių duomenų rinkimo.
Kontrolinis sąrašas yra popierinė forma, kurioje iš anksto atspausdinami kontroliuojami defektų tipai (mūsų atveju, naudojant keramikos gaminių dekoravimo defektų pavyzdį), pagal kurią paprastais simboliais nurodomas jų atsiradimo dažnis.
Įvairių lankstinukų skaičius įmonėje skaičiuojamas šimtais ir kiekvienam konkrečiam tikslui iš esmės galima sukurti savo lankstinuką. Tačiau jų dizaino principas išlieka nepakitęs: lapo forma turi būti paprasta ir suprantama (be papildomų paaiškinimų); būtina nurodyti, kas, kokiame etape ir kiek laiko rinko duomenis.
Akivaizdu, kad gaminių kokybė yra pagrindinis bet kurios įmonės veiklos rodiklis. Prekių ir paslaugų konkurencingumui palaikyti šiandien naudojama maisto saugos vadybos sistemos kūrimas, įvairios, dažniausiai ekonominės ir matematinės. Pavyzdžiui, dinaminis, tiesinis ir netiesinis programavimas, simuliacinis modeliavimas, eksperimentų planavimas, eilių teorija ir žaidimo teorija, funkcinės vertės analizė, Taguchi metodas ir kokybės struktūravimo metodas.
Palikite užklausą nemokamai konsultacijai
Kokybės funkcijų diegimas (QFD)). Tai sisteminis požiūris į klientų reikalavimų nustatymą, padedantis įmonei suprasti ir integruoti reikalavimų identifikavimą į konkrečius paslaugų teikimo planus. Skirtingai nuo kitų metodų, QFD yra kokybės užtikrinimo metodas, kuris suponuoja kliento poreikių tenkinimą statant garbanotas matricas, vėliau pavadintas „kokybės namais“, kuriose fiksuojama informacija apie paslaugos kokybę ir priimtus sprendimus. Šis metodas – tai gaminių ir procesų projektavimo technologija, leidžianti vartotojo pageidavimus paversti techniniais reikalavimais gaminiams ir jų gamybos procesų parametrams. QFD metodas yra ekspertinis metodas, kuris naudoja lentelės formos duomenų pateikimo būdą ir tam tikros formos lenteles, kurios vadinamos „kokybiškais namais“. Pagrindinė QFD technologijos idėja yra suprasti, kad yra didelis skirtumas tarp vartotojų savybių („faktinės kokybės rodikliai“) ir standartuose nustatytų gaminio parametrų („pagalbiniai kokybės rodikliai“). Pagalbinės kokybės priemonės yra svarbios gamintojui, bet ne visada svarbios vartotojui. Idealus atvejis būtų, kai gamintojas galėtų kontroliuoti gaminių kokybę tiesiogiai iš faktinių rodiklių, tačiau dažniausiai tai neįmanoma, todėl jis naudoja pagalbinius rodiklius.
QFD technologija – tai gamintojo veiksmų seka, paverčianti faktinius produkto kokybės rodiklius į techninius gaminių, procesų ir įrangos reikalavimus. Pagrindinis QFD technologijos įrankis yra specialus stalas, vadinamas „kokybišku namu“. Šioje lentelėje rodomas ryšys tarp faktinių kokybės rodiklių (vartotojo savybių) ir pagalbinių rodiklių (techninių reikalavimų):
QFD metodo taikymas leidžia atsižvelgti į vartotojo reikalavimus visuose gatavų gaminių gamybos etapuose, visiems organizacijos kokybės sistemos elementams ir taip padidinti klientų pasitenkinimo laipsnį, sumažinti projektavimo išlaidas ir gaminių paruošimas gamybai.
FSA metodas yra savo funkcijas atliekančios prekės kaštų analizės technologija; FSA atliekama esamiems produktams ir procesams siekiant sumažinti sąnaudas, taip pat kuriamiems produktams, siekiant sumažinti jų savikainą. FSA metodas buvo aktyviai naudojamas pramonėje nuo 60-ųjų, visų pirma JAV. Jo naudojimas leido sumažinti daugelio rūšių gaminių savikainą nesumažinant jų kokybės ir optimizuoti gamybos sąnaudas. FSA dabar yra viena iš populiariausių produktų ir procesų analizės rūšių. FSA yra vienas iš techninių objektų ir sistemų funkcinės analizės metodų, į šią metodų grupę įeina FFA (funkcinė fizinė analizė) ir FMEA analizė. Atliekant funkcinę kaštų analizę, nustatomos techninio objekto ar sistemos elementų funkcijos ir įvertinamos šių funkcijų įgyvendinimo sąnaudos, siekiant šias išlaidas sumažinti. FSA apima šiuos pagrindinius etapus:
1. Nuoseklus FSA objekto modelių konstravimas (komponentinis, konstrukcinis, funkcinis); modeliai dažniausiai statomi lentelės (matricos) forma; 2. Modelių tyrimas ir analizės objekto tobulinimo pasiūlymų rengimas.
Ishikawa diagrama(priežastinė diagrama, „žuvies griaučiai“) – kokybiškas įrankis, padedantis vizualizuoti priežasties ir pasekmės ryšius tarp analizės objekto ir jį įtakojančių veiksnių.
Įtakos veiksnys arba problema yra horizontalios rodyklės gale, kaip parodyta; galimos priežastys bus rodomos kaip pažymėtos rodyklės, įtrauktos į pagrindinės priežasties rodyklę. Kiekviena rodyklė gali turėti kitas rodykles, rodančias pagrindines priežastis arba į ją įtrauktus veiksnius, kurių prioritetas mažėja didėjant atstumui nuo pagrindinės rodyklės.

Pareto analizė- gali būti naudojamas idėjoms iš minčių šturmo seansų analizuoti. Jis naudojamas siekiant nustatyti keletą gyvybiškai svarbių problemų arba šių problemų priežastis, kurios turi didžiausią poveikį. Pareto diagrama grafiškai pateikia duomenis diagramos forma, sudaryta mažėjančia tvarka pagal elementų atsiradimo dažnį. Paprastai Pareto diagrama rodo, kad 80% įtakos paaiškinama 20% priežasčių, todėl ji kartais vadinama 80/20 taisykle.
Statistinio proceso valdymas (SPC)- yra procesų valdymo įrankių rinkinys. Be to, tai taip pat yra strateginis įrankis, leidžiantis sumažinti gaminių, medžiagų, įrangos tiekimo, ryšių ir procesų kintamumą, kurie yra daugumos kokybės problemų priežastis. SPC parodys, ar procesas „valdomas“ – t.y. ar jis stabilus tik atsitiktiniais variantais, ar „nekontroliuojamas“ ir reikalauja dėmesio. Be to, SPC automatiškai perspėja, kai valdomumas mažėja, ir gali padėti ilgalaikiam defektų dažnio mažinimui, nustatyti ypatingas priežastis, sumažinti ar pašalinti svyravimų priežastis ir pasiekti kuo artimesnį valdomumo lygį. SPC skaičiai ir informacija sudaro sprendimų ir veiksmų pagrindą naudojant griežtą duomenų registravimo sistemą. Be įrankių, reikalingų duomenims įrašyti, taip pat yra duomenų analizės ir interpretavimo įrankių rinkinys, kai kurie iš jų aptariami tolesniuose puslapiuose. Norint suprasti priemones ir jomis naudotis, nereikia išankstinių statistikos žinių.
Valdymo kortelė. Jis naudojamas kontroliuojamiems procesams stebėti naudojant vertes ir diapazonus. Kontrolinis sąrašas yra chronologiniai duomenys, tokie kaip pardavimai, apimtis, klientų skundai ir parodo, kaip vertės keičiasi laikui bėgant. Kontrolinėje diagramoje kiekvienas taškas atitinka atskirą reikšmę. Viršuje ir žemiau vidurkio yra viršutinė ir apatinė įspėjamoji linija bei veiksmų linijos (UWL, LWL, UAL, LAL). Šios ribos veikia kaip signalai ir sprendimų priėmimo taisyklės, taip pat suteikia operatoriams informaciją apie procesą ir jo valdymo būklę. Žemėlapis yra naudingas kaip istorinė proceso, jo eigos istorija ir kaip priemonė pokyčiams nustatyti ir numatyti.