Poprawa naprawy samochodów osobowych z rozwojem urządzenia do malowania elementów ciała. Poprawa procesu konserwacji i naprawy sprzętu (TORO)
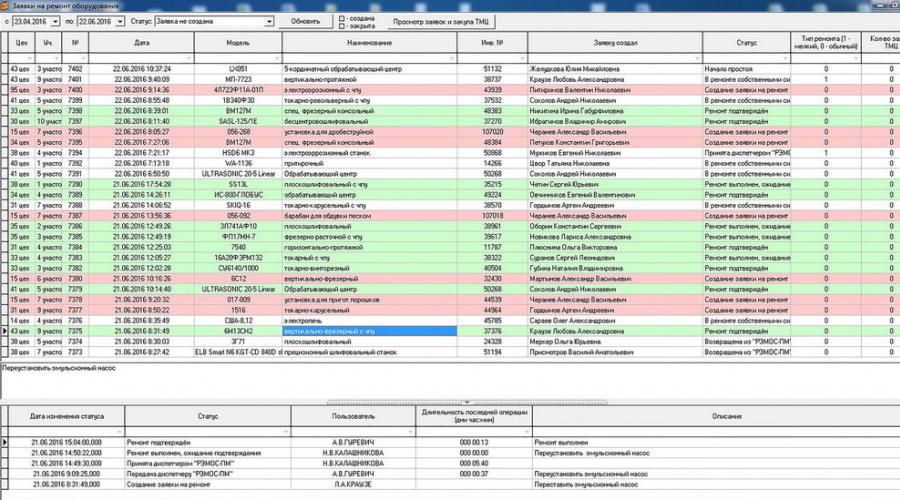
Przeczytaj także.
1. Główne aspekty planowania i analizy produkcji w warsztatach naprawczych i mechanicznych
1.1 Ogólne cechy warsztatów naprawczych i mechanicznych oraz treść prac wykonywanych przez nich
Warsztaty są organizacyjne i technologicznie oddzielne link Enterprise, który wykonuje pewną część procesu produkcyjnego lub wytwarzania produkcji roślinnej każdego rodzaju produktu. Zgodnie z powołaniem procesów produkcyjnych przeprowadzonych przez warsztaty, różnią się gospodarstwa główne, pomocnicze i serwisowe.
Główne obiekty obejmują podstawowe procesy produkcyjne, tj. związane z produkcją produktów i usług produkcyjnych, które tworzą program zakładu. Pomocniczy obejmuje instrumentalny, model, naprawa i mechaniczne itp.; Słuzyć magazyn gospodarstw, transport itp.
W związku z tym warsztat mechaniczny jest warsztatem pomocniczym, którego głównym zadaniem jest utrzymanie wszystkich urządzeń w warunkach roboczych, terminowej naprawy i aktualizacji. Warsztaty naprawiają główny i pomocniczy, podnoszenie i transport oraz inny sprzęt, który roślina ma.
W działaniu sklepu naprawczego, konserwacja (MOT) sprzętu powinna być w pierwszej kolejności i naprawa, na której nie można przeglądać jako koniec w drugim.
Formy do organizacji pracy naprawczej
Forma prac naprawczy ma ogromne znaczenie dla istniejącej produkcji. Wszystkie rodzaje napraw z wyjątkiem kapitału są wykonywane w miejscu instalacji naprawionego urządzenia. W przypadku poważnych napraw, narzędzie maszyny do 2,5 tony jest transportowane do warsztatów naprawczych i mechanicznych, cięższe są naprawione na miejscu. Aby zmniejszyć przestoje sprzętu, pośredni i remont jest używany przez metodę naprawów węzłowych, w których elementy z urządzeń są usuwane i zainstalowane na nim wcześniej odnowione z innego podobnego sprzętu. Cała wielkość pracy naprawczych jest dystrybuowana między warsztatami naprawczymi i mechanicznymi a podstawami warsztatów produkcyjnych. W zależności od rodzaju produkcji stosuje się rozmiar rośliny i charakteru sprzętu, scentralizowane, zdecentralizowane i mieszane formy organizacji prac naprawczych.
Z scentralizowaną formą prac naprawczych, wszystkie prace nad naprawą i modernizacją sprzętu są wykonywane tylko w warsztacie naprawy i mechanicznych. Podstawy naprawy warsztatów są wykonywane wyłącznie przez pracę związaną z inspekcjami i usługą INTERTALL. Ta forma organizacji jest stosowana, w fabrykach z małymi warsztatami głównie w produkcji na małą skalę (w szczególności FSUE "KalugapryBor"). Dzięki zdecentralizowanej formie organizacji prac naprawczych, prawie wszystkie prace nad naprawą i modernizacją sprzętu przeprowadza się przez naprawy warsztatów produkcyjnych. W warsztacie naprawczym i mechanicznym części zamienne są wykonane i produkują remont najbardziej złożonych elementów i agregatów. Ta forma organizacji jest stosowana w fabrykach z dużymi warsztatami głównie w produkcji masowej i na dużą skalę.
Dzięki mieszanej formie organizacji prac naprawczych w warsztacie naprawy i mechaniczne, remont, a pozostałe rodzaje naprawy prowadzone są przez podstawy naprawy warsztatów. Taka forma naprawy jest stosowana w seryjnych fabrykach produkcji i ciężkiej inżynierii.
Rodzaje konserwacji i naprawy są podzielone na następujące:
Konserwacja i naprawa (TOR) wykonana przez główny personel naprawczy mechanik;
Konserwacja wykonywana przez personel przemysłowy.
Rodzaje: regulowane (WOM), codziennie (TED), okresowe.
WOM zawiera:
Następnie 1 - konserwacja pierwszego typu;
Następnie 2 - konserwacja drugiego typu;
Trzy - utrzymanie trzeciego typu.
Wtedy 1 ECM (miesięczna konserwacja) powinna być przeprowadzona i dodatkowo - kontrola nad realizacją zasad działania technicznego, sprawdzania urządzeń bezpieczeństwa, poprawności funkcjonowania systemów smarowania i mechanizmów, których usterka może powodować duże awarie lub przedwczesne zużycie sprzętu.
Tego 2 zapewnia wydajność pracy 1, a także sprawdzanie i regulację pasów i łańcuchów, elementów sterujących, sterujących, napędowych śrub i nakrętki macicy, łączniki itp. Dzięki częściowym usuwaniu obudów i okładek, sprawdzanie stanu powierzchni roboczych, gładkości mechanizmów ruchomych.
W ten sposób 3 przewiduje wykonanie pracy do 2, a także bardziej pracochłonną pracę z częściowym lub całkowitym demontażem indywidualnych jednostek montażowych oraz stosowania przyrządów i przyrządów do pomiaru i pomiaru, wymiany smarowania i zużyte części (jednostki montażowe) , dostosowując węzły i mechanizmy.
Codzienna konserwacja (TOF) odbywa się przez warsztaty naprawy i mechaniczne na wnioski personelu produkcyjnego, wymienne zamki i elektryków w celu wyeliminowania błędów i przyczyn, które generują niepowodzenia.
Okresowa konserwacja jest podzielona na następujące operacje:
1) sprawdzanie dokładności jako niezależnej operacji;
2) Konserwacja (dekozwolnienie).
Rodzaje naprawy
Naprawa może być zaplanowana (PR) i bez planowania (HP).
Planowana naprawa (PR) - naprawa, której preparat jest przeprowadzany zgodnie z wymaganiami dokumentacji regulacyjnej i technicznej (warunki techniczne do wytwarzania sprzętu, wymagań przemysłu). Zgodnie z kompozycją i wielkością pracy przewiduje się trzy typy planowanych napraw:
· Kapitał (CR);
· Średni (CP);
· Prąd (tr).
Remont jest naprawą wykonaną w celu przywrócenia zdrowia i pełnego lub w pobliżu pełnej przywrócenia zasobu produktu z zastąpieniem lub przywróceniem dowolnych części, w tym podstawowych. Z remontem, kompletny demontaż wyposażenia, prania, defektu, wymiany lub przywrócenie wszystkich części i węzłów, montaż wyposażenia, jego zintegrowany kontrolny kontrolny, test na bezczynności i pod obciążeniem, malowanie, a także sprawdzanie stanu i naprawy fundamentu.
Średnia naprawa jest naprawą wykonaną w celu przywrócenia zdrowia i częściowego przywrócenia zasobu produktu z zastąpieniem lub przywracaniem składników ograniczonej nomenklatury oraz kontroli stanu technicznego części składowych wykonanych w kwocie ustalonej w dokumentacji regulacyjnej i technicznej.
Przy średniej naprawie, kompletny (do 65%) demontażu jednostek montażowych urządzeń i częściowych pozostałych, częściowych części i elementów, remontu poszczególnych węzłów, wymianę lub przywrócenie odpowiedzialnych noszonych części, w tym podstawowego, montażu sprzętu, jego zintegrowanej regulacji , Sprawdź, przetestuj w biegu jałowym i pod obciążeniem, malowanie, a także sprawdzanie stanu i naprawy fundamentu.
Obecne naprawy - Naprawy wykonane w celu zapewnienia lub przywracania wydajności produktu i składają się w zastępowaniu i (lub) przywróceniu poszczególnych części. W bieżącym naprawie, częściowy demontaż sprzętu jest wykonany, kompletny demontaż niektórych węzłów, defektowania, wymiany lub odzyskiwania szybko zużytywanych części i węzłów oraz niezbędny montaż i regulacja działa.
Nieplanowana naprawa (HP) - naprawa, produkcja produktów, do których prowadzi się bez uprzedniego spotkania.
Naprawa awaryjna (AB) związana z nagłym zatrzymaniem sprzętu spowodowanego wadami projektowania lub produkcji, wady naprawcze z naruszeniem zasad działania technicznego i wymagań bezpieczeństwa, nie jest również planowane.
1.2 Esencja i wydajność systemu planowania i naprawy prewencyjnej (PPR)
Istota systemu planowania i ostrzeżenia
Główne prace na temat naprawy sprzętu w zakładzie Kalugapribor są produkowane zgodnie z planowanym systemem ostrzegania, których głównymi przepisami są wykonane z "jednolitego systemu planowania i naprawy zapobiegawczej oraz racjonalne działanie urządzeń technologicznych przedsiębiorstw budowlanych" .
Dzięki temu systemowi naprawa maszyn jest wykonywana w określonych datach, po badaniu maszyny pewnej liczby godzin, nie spodziewając się awarii. Oczywiście taki system nie wyklucza potrzeby naprawy losowej natury, na przykład, nieoczekiwany rozkład maszyny z powodu niewłaściwego wykorzystania ich lub wad dokonanych w produkcji.
Codzienna konserwacja jest prowadzona podczas przerw w sprzęcie lub w przypadku nieporozmawiającej.
Okresowa konserwacja jest wykonywana przez interwały czasowe zainstalowane w dokumentacji technicznej.
Regulowana konserwacja prowadzona jest z okresowością iw objętościach ustalonych przez system sektorowy lub instrukcję obsługi dla tego sprzętu.
Wszystkie rodzaje pracy na planowanej (regulowanej) i naprawie są wykonywane w określonej sekwencji, tworząc powtarzające się cykle.
Cykl naprawczy
Cykl naprawczy (C P) to najmniejsze powtarzające się przedziały czasowe lub operacje sprzętu, podczas których jest wykonywane: w określonej sekwencji zgodnie z wymaganiami systemu, wszystkie ustalone typy naprawy. Sprzęt roboczy jest określany przez liczbę godzin pracy operacyjnej jego działania. Cykl naprawczy jest zakończony remontu i charakteryzuje się strukturą i czasem trwania.
Struktura cyklu naprawczego (z C.R.) jest listą i sekwencją zaplanowanych napraw w okresie 1 między remontu lub między uruchomieniem sprzętu a pierwszym remontem.
Struktura cyklu naprawczego jest określona przez normy przedsiębiorstwa dla każdej grupy obrabiarek. Na przykład struktura cyklu naprawczego do maszyn do cięcia metali o normalnej dokładności ważącej do 10 ton składających się z czterech prądu, jednego medium i remontu, wygląda tak:
Kr - TP 1 - TP 2 - CP - TP 3 - TP 4 - KR (1.1)
Czas trwania cyklu naprawczego (tss.r.) jest liczbą godzin pracy operacyjnej sprzętu, podczas którego wszystkie zaplanowane naprawy są wykonywane w cyklu. Czas trwania cyklu naprawczego nie obejmuje sprzętu przestojów związanego z realizacją planowanych i nie planujących napraw, a następnie, a także innych przyczyn organizacyjnych i technicznych. Czas trwania cyklu naprawczego jest przedstawiony przez linię wymiarową między oznaczeniami napraw kapitałowych, które rozpoczyna się cykl i kończy. Nad linią wymiarową wskazuje czas trwania cyklu w zużytym zegara.
Okres InterRemer (T M.) jest okresem czasu operacyjnego sprzętu między dwoma kolejno przeprowadzonymi przez planowane naprawy. Czas trwania okresu częstotliwości jest równy okresie trwania cyklu naprawczego podzielonego przez liczbę planowanych napraw w cyklu, w tym remont.
Czas trwania cyklu naprawczego i okres interremmerów jest zdefiniowany dla każdej rośliny w instalacji i są standardowo zredukowane do tabeli.
Cykl konserwacji
Cykl konserwacji (C.O.) jest najmniejszymi powtarzających się przedziałów czasowych lub operacji sprzętu, podczas których występują w pewnej sekwencji zgodnie z wymaganiami tego systemu, wszystkie ustalone typy zaplanowanych konserwacji regulowanej.
Sprzęt roboczy jest określany przez liczbę godzin pracy operacyjnej jego działania. Cykl konserwacji charakteryzuje się strukturą i czasem trwania 1, a następnie 2, a następnie 3 tworzą cykl konserwacji (CS jest wtedy). W zależności od czasu trwania okresu INTRITAL można przeprowadzić 1-8 cykli między planowanymi naprawami.
Struktura cyklu konserwacji (z C.T.) jest listą gatunków WOM, które są częścią cyklu. Rodzaje wykonywane przez personel Unrepair (samochody maszynowe, środki czyszczące) oraz takie operacje konserwacji okresowej (PR, K) w strukturze z TS8T. Nie zawiera. W systemie branżowym, następująca struktura cyklu konserwacji została warunkowo przyjęta:
PR-to 1 - następnie 1 - następnie 1 - następnie 2 -
Następnie 1 - następnie 1 - następnie 1 - następnie 2 - C TS (1.2)
Następnie 1 - następnie 1 - a następnie 1 - a następnie 3 -
Następnie 1 - następnie 1 - następnie 1 - następnie 2 -...,
te. Cykl konserwacji
Z tss.to. \u003d 9to 1 + 2to 2 + T0 3. (1.3)
Czas trwania cyklu konserwacji (t tsss.) w spędzonych godzinach czasu pracy operacyjnej sprzętu zależy od wzoru
gdzie Pan jest czasem trwania okresu częstotliwości, h.
Tss.r. - Czas trwania cyklu naprawczego, h;
n c - liczba przeciętnych napraw w cyklu naprawy;
n t - liczba bieżących napraw w cyklu naprawy;
n na - liczba cykli regulowanej konserwacji w okresie InterRemer.
Okres świadczenia usług międzyoperacyjnym (T) jest okresem czasu operacyjnego sprzętu między dwoma konsekwentnie wykonane przez te same nazwy TTO
Okresy wykonania konserwacji do przeprowadzenia 1, a następnie 2 są określone przez wzory:
gdzie t c.to jest czasem trwania cyklu konserwacji, h.
Czas trwania cykli naprawczych, okresów częstotliwości i liczbę cykli RTO w okresie międzyrelatowania sprzętu do cięcia metalu i odlewniczego obsługiwane w warunkach innych niż warunki określone w tabelach są obliczane jako produkt ich wartości podanych w tabelach do współczynników korekcyjnych.
gdzie t c.r. - Szacowany czas trwania cyklu naprawy, h.;
Tss.r. - Wartość tabelaryczna czasu trwania cyklu naprawczego, h.;
Do O.M. - współczynnik przetworzonego materiału;
K ts. - współczynnik klasy dokładności maszyny (wyposażenie klas dokładności p, b, a, c);
K.S. - współczynnik kategorii maszyny (masową);
K IN - współczynnik wieku.
Wartości numeryczne współczynników do S.M. , K.S. , K w, k ts Dioda w tabelach.
Okres Interremer T MR jest obliczany przez wzór:
gdzie - liczba przeciętnych napraw w cyklu naprawy;
Liczba bieżących napraw w cyklu naprawy.
Następnie dostosuj liczbę cykli RTO w okresie wzajemnym wzoru:
zaokrąglić do najbliższej liczby całkowitej.
1.3 Techniczne przygotowanie systemu planowania i naprawień
Przygotowanie techniczne i materialne systemu zaprojektowania zaprojektowania składa się z projektowania i przygotowania technologicznego. Przygotowanie projektu obejmuje przygotowanie albumów rysunków części, określenie nomenklatury i normalizacji (unifikacja) wymiennych części i jednostek montażowych.
Albumy rysunków części sprzętu są używane podczas planowania, opracowywania technologii i produkcji wymiennych części zamiennych, ustanowienie wymiary napraw, normalizację i zjednoczenie wymiennych części i półfabrykatów, wprowadzenie materiałów zastępczych i ulepszeń sprzętu.
Album rysunków jest sporządzony dla każdego rozmiaru sprzętu, który zawiera paszport i schematy (kinematyczne, hydrauliczne, pneumatyczne, elektryczne i smarne), rysunki ogólnego widoku jednostek montażowych, części zamiennych, specyfikacji łożysk walcowych, pasów, normalne, zakupione części i urządzenia itp. Rysunki części powinny być skompilowane podczas demontażu urządzenia do planowanych napraw.
Szczegóły zastąpione nowym sprzętem są nazywane wymiennymi. Normalizacja (zjednoczenie) części wymiennych umożliwia zmniejszenie liczby ich rozmiarów, a tym samym zmniejszają koszty związane z ich produkcją.
Przygotowanie technologiczne polega na wytwarzaniu typowych procesów montażowych, demontażu agregatów i produkcji najbardziej pracochłonnych i złożonych części, a także kompilacji wadliwego oświadczenia.
Wadliwe oświadczenie jest oświadczeniem technologicznym wykonawczym i powinien być sporządzony w ramach napraw kapitałowych, a także ze średnią naprawą o częstotliwości ponad jednego roku. Wstępne wadliwe oświadczenie odbywa się 2-3 miesiące przed zatrzymaniem urządzenia do naprawy jednej z planowanych inspekcji, a końcowy - podczas demontażu jednostki dla technika kapitału lub medium naprawy lub naprawy.
Przygotowanie materiału powinno zapewnić tworzenie stale odnawialnej rezerwy (park) wymiennych części przechowywanych w magazynie. Takie dane są nazywane zapasami.
Rezerwa zawiera szczegóły:
a) z żywotnością nie przekraczającą okresu intertalu;
b) spędzony w dużych ilościach niezależnie od żywotności;
c) duże, złożone i czasochłonne, wymagające ich produkcji złożonych i dużych odkuwek;
d) Wyprodukowany z boku;
e) Wszystkie wymienialne szczegóły unikalnej, szczególnie odpowiedzialnej lub ograniczającej ilości produkcji sprzętu.
Szczegóły ze znaczącą żywotnością (1,5-2 lata lub więcej) nie są przechowywane w spiżarni, ale zamówić przed czasem trwania cyklu produkcyjnego ich produkcji i naprawy i terminu naprawy.
Dostawa zakupionych części, jednostek montażowych i sprzętowych spożywanych w dużych ilościach zależy od analogii z rezerwami materiałów i zakupionymi półproduktów dla głównej produkcji.
Sklepy magazynowe Części są w pełni przetwarzane, które można zainstalować bez żadnych wykończeń i dopasowania, w postaci wstępnej obróbki, jeśli są one zainstalowane podczas naprawy i montażu, lub w postaci pustego, jeśli dokładne wymiary części nie są znane.
Regulacyjna dostawa części w magazynach w warunkach pieniężnych jest ustalana przez rodzaj sprzętu na jednostkę naprawczą w zależności od rodzaju produkcji. Normy rezerwowe są podane w "Unified System planowania i naprawieńek".
Zużycie materiału wielkości H-T dla wszystkich rodzajów prac naprawczych rocznie jest określony przez wzór:
gdzie jest zużycie typu H-TIn na remoncie sprzętu do jednostki naprawczej na rok;
Współczynnik, który uwzględnia zużycie materiału podczas inspekcji i konserwacji;
Ilość jednostek naprawczych jednostek poddanych naprawach kapitałowych, średnich i niskich naprawach w ciągu roku;
Współczynniki charakteryzujące relacje między ilością spożywanych odpowiednio ze średnią a kapitałem, małymi i głównymi naprawami.
Wartości są ustawiane dla każdego rodzaju sprzętu i zgodnie z podgrupami materiału przez eksperymentalną metodę statystyczną opartą na analizie rzeczywistego zużycia materiałów na temat naprawy urządzeń w fabrykach.
Do przechowywania części zamiennych i materiałów naprawczych, fabryka spiżarnia jest zorganizowana, podporządkowana OGM i magazyn sklepowych w dużych warsztatach. W magazynie sklepu części zamienne są przechowywane dla agregatów dostępnych w tym warsztacie lub spędzane w tym warsztacie w dużych ilościach.
1.4 Naprawa sprzętu do planowania w warsztacie naprawy i mechanicznych
Roczny plan naprawy sprzętu składa się z zakładu REM z udziałem mechanika warsztatowego dla każdej jednostki sprzętu. Naprawy kalendarzowe są ustalane na podstawie danych księgowych magazynów w zakresie pracy sprzętu i innych materiałów o jednostce, w oparciu o faktycznie działały godziny na okres od ostatniej naprawy i wyników rocznej kontroli technicznej w październiku - listopad .
W rocznym planie napraw obejmuje inspekcje i zaplanowane naprawy. Miesiąc, w którym należy wykonać następną naprawę (inspekcja) zgodnie z planem, jest określona przez dodanie do miesiąca poprzedniej naprawy długości okresu InterRemer (okres między tryb) w miesiącach. Rodzaj naprawy jest ustalany przez strukturę cyklu naprawczego, w zależności od rodzajów poprzednich napraw.
Złożoność instalacji wodno-kanalizacyjnej i maszyn jest mnożąc złożoność jednej jednostki naprawczej zgodnie z odpowiednim rodzajem naprawy kategorii złożoności.
System PPR przewiduje ustanowienie przestojów sprzętu. Tak więc przyjęto teraz, że gdy brygada naprawcza pracuje w jednej zmianie, proste w dni robocze w jednostce naprawczej nie powinno przekraczać małej naprawy 0,25, średniej - 0,6 i kapitału - 1.0.
Osiąga się przyspieszenie naprawy:
a) zmniejszenie złożoności prac konserwacyjnych ze względu na ich większą mechanizację, stosowanie technologii progresywnej naprawy, wstępne przygotowywanie części zamiennych i jednostek montażowych oraz rozbudowy ich nomenklatury, uproszczenie konstrukcji sprzętu (zmniejszanie złożoności naprawy);
b) wzrost liczby pracowników w brygadzie (rozszerzenie przedniej pracy) lub zanotek ich pracy;
c) Większa specjalizacja zamków naprawczych, najlepsza organizacja pracy i miejsce pracy Brygad naprawczych i nieprzerwany zapewniający je wszystkie niezbędne (rysunki, materiały, wymienne szczegóły itp.).
Wymagana liczba pracowników do wykonywania planowanych napraw s p.r. Określony przez wzór:
gdzie - standardy czasu na 1 jednostkę naprawczą, subiektywnie przez kapitał, średni i niską naprawę;
F R - Roczny efektywny fundusz czasu pracy jednego pracownika naprawczego, C / Ch;
P - średni odsetek zasad pracowników naprawczych.
Całkowita liczba jednostek naprawy urządzeń.
Złożoność wszystkich napraw w każdym miesiącu zgodnie z planem powinna być w przybliżeniu taka sama, aby nie ma braku lub nadwyżki pracowników naprawczych w pewnych miesiącach.
Roczny plan naprawy sprzętu jest podpisany przez główny mechanik zakładu, głowy i mechanika warsztatów i jest zatwierdzony przez dyrektora zakładu.
Rachunkowość realizacji planu napraw odbywa się w tym samym harmonogramie planu, w dolnej linii, dla każdej jednostki.
Na podstawie rocznego planu i jego rzeczywistej realizacji w poprzednich miesiącach, a także liczba godzin faktycznie pracował jako agregat od ostatniej naprawy, rzeczywisty stan sprzętu zidentyfikowanego podczas kontroli, a dostępność naprawy napraw i materiałów jest naprawionych Na każdym warsztacie miesięczny plan naprawczy. Miesięczny plan naprawy sprzętu musi być zgodny z głównym planem produkcyjnym. Jest skompilowany przez OGM wraz z mechanikiem warsztatów.
Jeśli urządzenie na początku naprawy jest dobrymi lub regularnymi naprawami, można zastąpić innym, mniejszym objętości, a następnie anulowanie tego typu naprawy lub wymiany jest wykonane za zgodą głównego mechanika zakładu. Okres międzyoprzestrzeni nie można wyeliminować. Księgowość i monitorowanie wykonania planów prowadzi się przez Biuro Planowanie i Produkcyjne.
2. Analiza organizacji istniejącej produkcji w warsztacie naprawczych i mechanicznych FSUE "Kalugaprybor"
2.1. Charakterystyka warsztatów naprawczych i mechanicznych FSUE "Kalugaprybor"
Struktura organizacyjna warsztatów naprawczych i mechanicznych w FSUE "Kalugapribor" ma następujący formularz:
Figa. 2.1. Struktura produkcji warsztatów naprawczych i mechanicznych w FSUE "Kalugapribor"
Struktura produkcyjna warsztatów jest skład jego zakładów produkcyjnych, innych jednostek wewnątrztrakcyjnych i form ich relacji.
Powstawanie sklepów z przedsiębiorstw jest głównie w dwóch obszarach specjalizacji: zgodnie z jednorodnością procesów technologicznych wykonanych przez nich (specjalizacja technologiczna) oraz o charakterze produkowanych w nich produktach (przedmiot i sprawiedliwa specjalizacja).
W specjalizacji technologicznej w warsztacie przeprowadzana jest część procesu technologicznego, składająca się z jednej lub więcej operacji z bardzo szeroką gamą części (produktów). W tym samym czasie warsztat ustanawia głównie ten sam rodzaj sprzętu. Ta forma specjalizacji warsztatów ma swoje zalety i wady. Z małą różnorodnością operacji i urządzeń, przewodnik techniczny jest ułatwiony, a bardziej szerokie możliwości regulacji ładowania sprzętu, tworzona jest organizacja wymiany doświadczeń. Jednak w specjalizacji technologicznej warsztatów przetwarzania, złożonych, wydłużonych tras ruchowych elementów pracy z nimi wielokrotnie powrócić do tych samych celów. Narusza to zasadę bezpośredniej dokładności, utrudnia koordynowanie pracy warsztatów i prowadzi do wzrostu cyklu produkcyjnego.
W warsztatach specjalizacji przedmiotowej, odpowiedni etap (częściowy proces) wytwarzania stałych części w stosunku do wąskiej nomenklaturze jest w pełni wdrożone. Dla tych warsztatów charakteryzuje się różnorodność sprzętu i sprzętu, ale wąska nomenklatura przetworzonych części (węzłów). Koordynacja warsztatów w tym przypadku jest znacznie łatwiejsza, ponieważ wszystkie operacje przetwarzania koncentrują się w jednym warsztacie. Prowadzi to do stabilnej powtarzalności procesu, upraszcza planowanie kalendarza operacyjnego, geograficznie przynosi operacje i poszczególne etapy procesu, a ostatecznie zmniejsza cykl produkcyjny.
Jedną z kierunków poprawy struktury produkcji przedsiębiorstwa jest zastąpienie technologicznej formy specjalizacji przedmiotów.
W przypadku tego warsztatu naprawczego i mechanicznego jest charakterystyczna specjalizacja spójna spójna specjalizacja. Wykorzystuje wiele urządzeń i wyposażonych. Rodzaje prac: głównie przetwarzanie mechaniczne, dopasowanie i naprawa (montaż i inne) odzyskiwanie, spawanie. Dokładne typy prac wykonywanych w tym warsztacie opisano poniżej.
Sekcje warsztatów specjalizuje się technologicznie i wyposażone w jednorodny sprzęt do wykonywania indywidualnych operacji. Są one utworzone przez grupy tych samych maszyn typu.
Wydziały obejmują:
Komora obrotowa;
Komora frezowania;
Komora nudna;
Komora strugania;
Oddzielenie maszyn zielonoświaterowych.
Dostawy są przedziałami:
Ostry;
Spiżarnia instrumentalna i dystrybucyjna;
Urządzenia magazynowe.
Strukturalny obszar łącza jest miejscem pracy. Miejsce pracy nazywa się częścią obszaru produkcyjnego, wyposażonego i wyposażonego w środki techniczne i urządzenia, odpowiednio charakter wykonanej pracy. Różnorodność prac wykonywanych w miejscach pracy wynika z natury i poziomu specjalizacji warsztatów i witryny. W warsztatach naprawczych i mechanicznych FSUE "Kalugapribor" dominuje specjalizację technologiczną w miejscu pracy, tj. Wiele szczegółów jest wykonywanych w cechach technologicznych sprzętu. Układ warsztatowy jest przedstawiony w dodatku 1.
2.2 Określenie ilości pracy przeprowadzonej w warsztacie naprawy i mechanicznym FSUE "Kalugapribor"
System określania zakresu pracy dla warsztatów naprawczych i mechanicznych używanych na FSUE "Kalugapribor"
Planowanie prac dla sklepu naprawczego rozpoczyna się od księgowania obecności, ruchu i wykorzystania sprzętu w warsztatach przemysłowych. Utylizacja i odbiór znajduje odzwierciedlenie w sprawozdaniu finansowym.
Aby określić potrzebę niezbędnych rodzajów napraw, konieczne jest, aby mieć czas, aby mieć dane na czas faktycznie spędzonej maszynie od momentu uruchomienia lub z ostatnich napraw planów (jest składnikiem czasu naprawy kalendarza).
Kalendarz Time Shift T, równy przedsiębiorstwom branży Osiem, składa się z:
T r.O. - czas operacyjny sprzętu;
T pz - przygotowawczy - ostatni czas;
T pon - bezczynności czasu, aby utrzymać lub przywrócić wydajność;
T.O. - czas bezczynności dla przyczyn organizacyjnych i technicznych.
Rachunkowość czasu operacyjnego może być również zorganizowany za pomocą liczników operacyjnych sprzętu.
Miarki sprzętu, zapewniające dokładne wyniki, są podłączone do każdej maszyny. Miesięczny zbiorów pracowników OGM zbiorczy "Vedomosti Meter Testimony", który rekordowy sprzęt, wyposażony w czasy, na warsztatach i działkach. Ta metoda wymaga określonych kosztów, aw przedsiębiorstwie "Kalugaprybor" nie jest używana. Dane dotyczące czasu operacyjnego sprzętu uzyskuje się od podziałów normalizacji warsztatów produkcyjnych.
Głównym dokumentem, który odzwierciedla planowanie prac naprawczy jest harmonogram (plan harmonogramu jest sporządzony z okresami negregnacji). Harmonogram naprawy sprzętu jest opracowany tylko przez rok. Sześć miesięcy przed rozpoczęciem planowanego roku w całym zakresie sprzętu znajdującego się w Enterprise Kalugapribor, możliwe jest obliczenie zapotrzebowania na wszystkie rodzaje naprawy. Następujące naprawy są następnie przeprowadzane dla każdej maszyny na rok w formularzu 1 "roczny plan naprawy sprzętu do naprawy", gdzie wskazano numer zapasów, nazwa urządzenia, model, kategoria złożoności, a także Wymiana, rodzaj i data ostatniej naprawy, rodzaj operacji naprawczych dla każdego miesiąca.
Cała ilość pracy jest rozprowadzana w ciągu miesięcy w zależności od rodzaju i czasu trwania naprawy każdej jednostki sprzętu.
Obliczanie czasu miesięcznego rozważenia pracy dla warsztatów naprawczych i mechanicznych na rok 2009
Miesięczna zdolność pracy pracy (w godzinach) przeprowadzonych przez warsztaty naprawy i mechaniczne są określane w następujący sposób.
W miesięcznym planu naprawy sprzętu warsztat jest zainstalowany:
1. Nazwa i numer urządzenia do zapasów;
2. Model maszyny;
4. Planowanie złożoności pracy w normalnym zegara.
Mechaniczna część maszyn i maszyn w ogólnym przypadku składa się z części kinematycznych i hydraulicznych, których naprawa jest odpowiednio oznaczona przez R. i
W związku z tym,
W przypadku jednostki naprawy części mechanicznej podjęto 0,09 czasochłonu remontu maszyny 1k62.
Poradność mechanicznych prac naprawczych jest obliczana dla każdego rodzaju naprawy oddzielnie.
T km \u003d t k.сles. + T K.stan. ; (2.2)
T cm \u003d t s.sles. + T s.sta. ; (2.3)
T tm \u003d t t.sles. + T t.stan. ; (2.4)
gdzie m km jest złożoność remontu części mechanicznej;
T cm - złożoność średniej naprawy części mechanicznej;
T tm - złożoność bieżącej naprawy części mechanicznej;
T k.sles. - złożoność remontowania prac konserwacyjnych;
T s.sles. - złożoność środkowej naprawy prac wodno-kanalizacyjnych;
T t t. sles. - złożoność bieżącej naprawy prac wodno-kanalizacyjnych;
T k.stan. - intensywność pracy remontu maszyn;
T s.stan. - złożoność średniej naprawy maszyn;
T.antan. - intensywność pracy bieżącej naprawy maszyn.
Zatem złożoność każdego rodzaju naprawy, składa się z złożoności pracy maszyny i etykietowania. Złożoność wodociągów wodno-kanalizacyjnych i maszyn jest w formułach:
gdzie t k.sles. - norma ciężkości głównych napraw jednostek naprawy prac konserwacyjnych;
t k.stan. - norma intensywności pracy remontu jednostki naprawy maszyn;
t s.sles. - standard intensywności pracy średniej jednostki naprawczej naprawy prac wodno-kanalizacyjnych;
t s.stan. - norma złożoności średniej jednostki naprawczej renowacji maszyn;
t. - norma intensywności pracy bieżącej naprawy jednostki naprawy prac konserwacyjnych;
t. - norma intensywności pracy bieżącej naprawy jednostki naprawy maszyn;
(R m) k - całkowita naprawa mechanicznej części urządzenia przechodzącej remontu;
(R m) C - całkowita naprawa mechanicznej części urządzenia przechodzącej do naprawy średniej;
(R m) t - całkowita naprawa mechanicznej części urządzenia przechodzącej bieżące naprawy.
W ten sposób,
gdzie T RM jest całkowitą intensywnością pracy (całkowita intensywność pracy wrażenia naprawy mechanicznej części urządzenia);
0,1 - współczynnik, biorąc pod uwagę nieoczekiwane naprawy.
W "Sektorowym systemie konserwacji i naprawy sprzętu do obróbki metali", podano tabelę złożoności planowanych napraw (patrz Dodatek 2), zgodnie z którymi stawka czasowa jest określona przez 1 WE w godzinach. Stopa czasu uwzględnia rodzaje naprawy i pracy (hydraulika lub maszyna).
Poradność konserwacji jest podobna do ciężkości naprawy, przy użyciu standardów czasowych na jednostkę naprawczą (patrz Dodatek 3).
W "Sektorowej konserwacji i naprawy sprzętu do obróbki metali" tabela standardów czasowych w godzinach na jednostkę naprawczą (patrz załącznik 3), na którym stopień czasu opiera się na zależności złożoności naprawy od otrzymania części zamiennych Strona.
Obliczanie złożoności pracy warsztatów naprawczych i mechanicznych odbędzie się przez przykład z lipca 2009 r. (Lipiec jest wybrany jako najbardziej obciążony miesiąc roku) (patrz tabela 2.1, Tabela 2.2, Tabela 2.3).
Tabela 2.1. Obliczanie złożoności dzieł RMC
Używane formuły:
T s.stan. \u003d (T s.stan. -T s.m.stan.) (R m) c; (2.7)
T s.sles. \u003d (T S.Sles. -T S.M. Sles.) (R m) C; (2.8)
T k.stan. \u003d (T K.stan. -T K.um.stan.) (R m) do; (2.9)
T k. sles. \u003d (T k.shesles. -T K.m. Sles.) (R m) do; (2.10)
T.antan. \u003d (t t.stan. -t T. a.stan.) (R m) t; (2.11)
T t t. sles. \u003d (T t.sles. -T t.d.sles.) (R m) t; (2.12)
gdzie mit. - Ilość zmniejszenia intensywności pracy, w zależności od podaży części zamiennych z boku. Określony przez tabelę (patrz załącznik 4).
Ogólna intensywność pracy maszyn podczas naprawy (T.).
T suma. \u003d T s.stan. + T K.stan. + T T.Sc. ; (2.13)
T łącznie. Stan.osm. \u003d T o.stan. ; (2.14)
T suma. \u003d T sumy. + T suma. (2.15)
Podobnie w przypadku działań monterowych, z wyjątkiem uzyskanych danych normatywnych.
T łącznie. Sles.osm. \u003d T o.sles. 1,1; (2.16)
te. Przemyślana wzrośnie o 10% z powodu pracy w różnych warsztatach (tabela 2.2).
Tabela 2.2. Remont
Nazwa kruszywa |
Lokalizacja maszyny |
Rodzaj naprawy |
Total drgor, N-H. |
||||||
Belka dźwigowa |
|||||||||
Strrogalny |
|||||||||
Wiercenie |
|||||||||
Stacker dźwigowy |
|||||||||
Przemiał |
|||||||||
Polerowanie |
|||||||||
Wiertarka pionowo. |
|||||||||
Wiertarka pionowo. |
|||||||||
Galwanicznie. |
|||||||||
Edko-Slip. |
Ze względu na brak dostawy w sklepie części zamiennych, na lipiec 2009 r., Ich współczynnik rachunkowości, ogólna intensywność pracy naprawy nie zmniejsza się i jest równa 1.
Tabela 2.3. Inspekcje
Nazwa kruszywa |
Lokalizacja maszyny |
Intensywność pracy wodno-hydraulicznych, N-H. |
Intensywność pracy maszyn, N-H. |
Całkowita praca, N-H. |
||||
"Pionier" |
||||||||
Winda |
||||||||
Winda |
Kotłownia |
|||||||
"Pionier" |
||||||||
Galwanicznie. |
||||||||
Galwanicznie. |
||||||||
Galwanicznie. |
||||||||
Winda |
||||||||
Galwanicznie. |
||||||||
Stacker. |
||||||||
Stacker. |
T łącznie. Sles. \u003d 3065 N-H; T suma. \u003d 1037 N-H; T suma. \u003d 3065 + 1037 \u003d 4102 N-H.
Laborusy prac naprawczych przez inne miesiące roku jest przeznaczone podobnie (patrz tabela 2.4). W oparciu o te dane, łączny harmonogram zmiany złożoności planowanych prac naprawczych w warsztacie naprawy i mechanicznych na 2009 r. Budynek przeprowadza się biorąc pod uwagę możliwe plany przebudowy przez miesiące, tj. Od najbardziej obciążonych miesięcy, pewna ilość głównych napraw została przeniesiona do poprzedniego miesiąca. Ten harmonogram ma następujący formularz:
Figa. 2.2. Złożoność wykresu planowanych napraw na rok 2009
Tabela 2.4.
Tombsch (godzina) |
wrzesień |
|||||||
Tombsch (godzina) |
3. Proponowane środki w celu poprawy organizacji produkcji i ich efektywności ekonomicznej
3.1 Budowanie harmonogramu kalendarza do pracy naprawczej
Aby spełnić wszystkie naprawy i konserwację sprzętu i innych rodzajów środków trwałych, potrzebna jest racjonalna organizacja i jasno planowane prace naprawy i warsztatów mechanicznych. Zatem zoptymalizować ręczne i zarządzanie organizacją pracy, wskazane jest zaplanowanie czasu trwania naprawy.
Planowany czas trwania naprawy sprzętu zależy od złożoności prac naprawczych, złożoności naprawy sprzętu, liczbę brygady naprawczej. Posiadanie tych danych możesz zbudować harmonogram kalendarza na czas trwania napraw. Taki harmonogram w tym warsztacie Niestety nie jest używany. Jednak możliwe jest dokładniejsze określenie dni dostarczania sprzętu do napraw, obciążenia pracownikami w ciągu dnia, możliwość rozszerzenia pracy.
Wykres planowanych napraw pokazuje, że lipiec jest najbardziej pobrany miesiąc roku.
Budowanie harmonogramu pracy kalendarza dla warsztatów naprawczych i mechanicznych na lipca, konieczne jest rozpoczęcie od grupowania niezbędnych inspekcji na obiektach.
Od 21 do 39 - Nominuj numery obiektów serwisowych.
Tabela 3.1. Grupowanie inspekcji na obiektach
KOTŁOWNIA |
||
Biuro sprzedaży. |
||
Całkowita intensywność pracy inspekcji i konserwacji w każdym warsztacie i Departament definiuje się jako suma złożoności obiektów do utrzymania obiektów oddzielnie do maszyn i zamków. Badanie może wystąpić w czasie wolnym od planów z planowanych napraw. Aby zbudować harmonogram kalendarza do naprawy napraw, obliczymy czas trwania napraw według wzoru:
gdzie t n jest planowanym czasem trwania jednostki naprawczej, h.;
t- Standard złożoności odpowiadający rodzajowi naprawy jednostki złożoności naprawczej;
R m - jednostki złożoności naprawy;
H P - Liczba naprawy Brygady, Ludzie;
Współczynnik przetwarzania okrągłego.
Niemożliwe jest dokładne określenie alteracji pracy zamków i maszyn w warsztacie w czasie, więc wewnątrz brygady konieczne jest niezależnie określać objętość i czas indywidualnych rodzajów prac (hydraulika i maszyny).
Biorąc pod uwagę obliczone powyżej liczbę pracy i kategorii złożoności napraw przemysłowych, powinno być 16 osób w brygadzie. Podczas budowy harmonogramu kalendarza bierzemy pod uwagę, że całkowity czas pracy jest podzielony na 16 pracowników brygady (z czego 11 locksterów, 5 zszywek).
Tabela 3.2. Obliczanie czasu trwania planowanych napraw
Obiekt Numer naprawy |
Identyfikacja sprzętu |
Lokalizacja sprzętu |
Planowany czas naprawy |
|
Belka dźwigowa |
(88+202,4)/1,9516=9,07 |
|||
(66+151,8)/1,9516=6,8 |
||||
Strrogalny |
(297+683,1)/1,9516=30,1 |
|||
Wiercenie |
(55+126)/1,9516=5,6 |
|||
Stacker dźwigowy |
(23,1+52,8)/1,9516=2,37 |
|||
Przemiał |
(100,1+288,8)/1,9516=12 |
|||
Polerowanie |
(33+75,9)/1,9516=3,4 |
|||
Wiercenie pionowo. |
(46,2+105,6)/1,9516=4,7 |
|||
Wiercenie pionowo. |
(42,35+96,8)/1,9516=4,3 |
|||
Galwanicznie. |
(15,4+35,2)/1,9516=3,5 |
|||
Edko-Slip. |
(38,5+88)/1,9516=3,9 |
|||
Galwanicznie. |
(4,4+8,8)/1,9516=0,4 |
|||
Galwanicznie. |
(4,4+8,8)/1,9516=0,4 |
Na podstawie uzyskanych danych budujemy harmonogram, kierując się następującymi zasadami:
1. Aby naprawić każdą maszynę, konieczne jest opuszczenie czasu przekraczającego czas trwania planowanych napraw w przypadku konieczności naprawy większej złożoności niż regulacyjny. Tym razem nazywa się czasem kopii zapasowej.
2. Każda nowa maszyna zaczyna służyć pierwszej kolejnej zmianie lub z drugiej połowy (jest to konieczne, aby pracownik widzi wynik swojej pracy, a obszar obszaru nie jest niepotrzebny nie załadowany).
3. Jeżeli planowane obliczenia, czas naprawy maszyny kończy się wśród przesunięcia, ale nie przekracza go połowę, a następnie czas kopii zapasowej bierze liczbę pozostałych godzin tego dnia.
4. Jeśli czas naprawy maszyny zakończy się wśród przesunięcia i przekracza go do połowy, a następnie na czas kopii zapasowej pozostałe godziny dnia i pierwszej połowy następnej zmiany.
5. Jeśli nie nastąpi nieoczekiwana naprawa, ten dzień jest używany do konserwacji, aby pracownicy nie są bezczynni.
W oparciu o te zasady, harmonogram kalendarza na czas trwania planowanych napraw wykonano na lipiec 2009 r. (Patrz Rys. 3.1).
Tak więc, zgodnie z harmonogramem, dokładne daty naprawy niektórych maszyn i dni serwisowych są widoczne. Godziny wolne mogą być wykorzystywane do produkcji w warsztacie różnych usług.
Tworzenie harmonogramu kalendarza do naprawy napraw, które usprawnią odbiór określonego typu sprzętu do napraw, zapisze obszar warsztatu z nadmiernego obciążenia pracą, pozwoli pracownikom lepiej skupić się w kategoriach pracy, która będzie złagodzić ich od gwałtownego wzrostu pracy pod koniec miesiąca. Dzięki temu harmonogramowi możesz wyraźniej projektować sprzęt ładujący w przedziałach produkcyjnych. Budowanie tego harmonogramu dla wszystkich dwunastu miesięcy wyraźnie odzwierciedlają przestoje w ciągu roku i pozwoli Ci bardziej racjonalnie rozpowszechniać naprawę w miesiącu, określić najbardziej pożądany czas pracujących z wakacji.
3.2 Organizacja kompleksowej brygady naprawczej
Ponieważ naprawa wszelkiego rodzaju, a czasami usługa przecinana jest dokonana przez warsztat naprawy i mechaniczne, jakość i składowa skład pracowników warsztatów, jego struktura organizacyjna ma ogromne znaczenie.
W tym artykule, edukacja jest proponowana w warsztacie złożonej brygady naprawczej, która obejmuje pracowników różnych zawodów wykonujących kompleks technologicznie heterogenicznej pracy obejmujących wszystkie rodzaje naprawy i konserwacji obróbki metali i innych urządzeń. Wykonanie wyboru tego typu brygad wyjaśniono następującymi czynnikami:
Wdrożenie kompleksu wspólnej pracy wymagającej jednoczesnego uczestnictwa grupy wykonawców;
Niezdolność do ustalenia stałej objętości i składu pracy z powodu nieprzewidzianych napraw;
Numer, skład profesjonalny i kwalifikacyjny brygady jest ustalany w zależności od planowanej intensywności pracy i złożoności planowanych prac nad naprawą i konserwacją.
W rozdziale 2 praca dyplomowa została określona przez określenie niezbędnej liczby pracowników. Obliczenia wykazały, że nawet w najbardziej pobieranym miesiącu 2009 - 5 maszyn i 11 locksterów powinny być zajęte w naprawie i konserwacji. Stanowią one brygadę naprawczą.
Obecnie 6 maszyn i 15 zamków, zatrudnionych w pracach naprawczych i konserwacyjnych w warsztacie, co przekraczają wymaganą liczbę pracowników na 5 osób (1 maszyna i 4 lockstery). Dlatego zaleca się zmniejszenie liczby pracowników najmniejszych wyładowania kwalifikacyjnego, które nie odpowiada utrzymaniu sprzętu środkowej i wysokiej kategorii złożoności lub tłumaczenia je do sklepów naprawczych głównych sklepów produkcyjnych.
Aby uzasadnić tę propozycję, wykonano obliczenie porównawcze wynagrodzeń dla pełnej i skróconej kompozycji.
Fundusz płacowy jest ustanowiony jako produkt planowanej intensywności pracy dla średnich wartości średniej jednej normy, biorąc pod uwagę% składki. Wszystkie rodzaje prac nad naprawą i konserwacją sprzętu są ustalane przez normy czasu w normalnym zegara. Prace te są wykonywane zgodnie z planem stacyjnym, który opiera się na miesięcznych harmonogramach harmonogramów napraw i konserwacji. Planowany i płatny dokument Brygady jest miesięcznym wyposażeniem planu. W planowym planu ustawia się brygada:
Nazwy i liczby naprawionych i serwisowanych urządzeń.
Ilość jednostek naprawy
Rodzaj naprawy i średnie absolutorium pracy;
Planowana intensywność pracy w normalnych godzinach;
Kwota wynagrodzeń regulacyjnych do wykonania prac w rublach;
Zaplanowany czas na wykonanie pracy;
Podczas wypełniania stroju planu, średnia absolutorium taryfowa ustala się w zależności od ich nazwy i naprawy sprzętu do naprawy w tym miesiącu.
Tabela 3.3. Plan-Outfit.
Dla każdego pracownika miesięczne zyski taryfowe są określane zgodnie ze zegarem pracownikami i przyznanym absolutorium.
Tabela 3.4. Obliczanie miesięcznych zarobków taryfowych (ZP TAR.POVR.M.) dla pełnej kompozycji brygad robotniczych
Zp tarpovr. , pocierać. |
|||||
Dla ślusarzy: |
|||||
Tabela 3.5. Obliczanie miesięcznych zysków taryfowych (ZP TAR.POVR.M.) dla skróconej składu brygad robotniczych
Czas spędzony czas (f fakt. Seks.), H. |
Stawka taryfowa (od godziny. I), pocierać. |
Zp tarpovr. , pocierać. |
|||
Dla ślusarzy: |
|||||
Wynagrodzenie robotnicze składają się z:
Miesięczne zarobki taryfowe;
Robienie akordowe, naliczone z uwzględnieniem współczynnika dystrybucji gospodarza;
Nagrody naliczone współczynnikiem dystrybucji nagrody.
Obliczenia jest wykonane w następującej kolejności:
CDC \u003d Zpr prizht tar.povr. , (3.2)
gdzie PPC SD. - wzmocnienie brygady.
K r.pr. - współczynnik dystrybucji akordowej robienia przez brygadę.
Obliczono współczynnik dystrybucji premii Brigadier (K \u200b\u200bR.P.):
Tabela 3.6. Obliczanie płac dla pełnej składu brygad robotniczych
Zp tarpovr. , pocierać. |
Wzmocnienie, pocierać. (K r.pr. \u003d 0,1) |
Nagroda, pocierać. (K r.p. \u003d 0,33) |
Wynagrodzenie, Rub. |
||
Dla ślusarzy: |
|||||
Tabela 3.7. Obliczanie wynagrodzeń do skróconej składu brygad robotniczych
Zp tarpovr. , pocierać. |
Wzmocnienie, pocierać. (K r.pr. \u003d 0,35) |
Nagroda, pocierać. (K r.p. \u003d 0,4) |
Wynagrodzenie, Rub. |
||
Dla ślusarzy: |
|||||
Do obrabiarek maszynowych: |
|||||
Z tych obliczeń można stwierdzić, że taki środek zwiększa płace pracowników średnio o 22,5%, co zwiększa ich istotne odsetki.
Kolejnym pozytywnym wskaźnikiem może być rozwój jednego pracownika:
gdzie w 1 - rozwój jednego pracownika z pełną brygadą;
W 2 - rozwój na pracownika pod skróconą kompozycją brygady;
N 1, n 2 - liczba pracowników w brygadzie;
T jest złożonością prac naprawczych.
W oparciu o wcześniej produkowane obliczenia liczby warsztatów roboczych i ITER, proponuje się następującą strukturę organizacyjną:
Figa. 3.2. Nowa struktura organizacyjna warsztatów naprawczych i mechanicznych w FSUE "Kalugaprybor"
Wniosek
Aby utrzymać sprzęt w stanie roboczym, prace naprawcze, umożliwiające zmniejszenie czasu na naprawę sprzętu na FSUE "Kalugaprybor" jest specjalny sklep naprawczy, który jest jedną z ważnych sekcji produkcji pomocniczej. Warsztaty naprawiają główny i pomocniczy, podnoszenie i transport oraz inny sprzęt, który roślina ma. Głównymi zadaniami warsztatów naprawczych i mechanicznych są: przeprowadzenie przepisów utrzymania sprzętu, terminowej naprawy i modernizacji.
Specyfika warsztatów naprawczych jest wyjątkowo duża różnorodność procesów używanych w naprawie. Dlatego wprowadzenie nowych technologii na rośliny, naprawy nietypowe, jest trudne. Wymaga to zwiększenia organizacji pracy w sklepie do naprawy i weź pod uwagę najbardziej racjonalny i możliwy udział w akcji odbioru części zamiennych do sprzętu fabrycznego z boku.
Z wielkiej wagi, przy obliczaniu liczby pracowników, wybrana metoda organizacji pracy (scentralizowana, zdecentralizowana, mieszana) została znaleziona. Główną różnicą metod jest dystrybucja pracy między warsztatami naprawczymi i mechanicznymi i podstawami naprawy sklepu, co zmniejsza lub zwiększa złożoność.
Po pierwsze, proponuje się utworzenie kompleksowej brygady naprawczej w warsztacie, który obejmuje pracowników z różnych zawodów wykonujących kompleks technologicznie heterogenicznej pracy obejmujących wszystkie rodzaje naprawy i konserwacji obróbki metali i innych urządzeń. Głównymi zaletami złożonych brygad to:
Podobne dokumenty
Koncepcja i wskaźniki oceny jakości usług. Kompleksowa analiza działań firmy naprawczej i budowlanej. Poprawa jakości usług poprzez poprawę kwalifikacji personelu, organizację systemu kontroli do podania obiektów i czyszczenia.
teza dodana 15.06.2012
Teoretyczne aspekty, typy, kształty i metody, opracowanie form produkcji produkcji. Analiza produkcji i działalności gospodarczej przedsiębiorstwa, struktura zarządzania i produkcji. Wydarzenia dotyczące poprawy głównej produkcji przedsiębiorstwa.
teza dodana 25.05.2010
Obliczanie programu produkcyjnego, określenie rodzaju produkcji, potrzeba sprzętu, liczby głównych pracowników produkcyjnych. Zarządzanie warsztatami i sposobami poprawy organizacji zapewnienia produkcji przez pojazdy.
zajęcia, dodano 02.03.2010
Charakterystyka i główne wyniki OJSC "INProtekhservis". Poprawa planowania organizacji organizacji organizacji z powodu wzrostu produkcji i stworzenia nowego warsztatu do produkcji materiałów geosyntetycznych.
praca kursu, dodano 24.02.2014
Ocena skuteczności i rozwoju wniosków o poprawę struktur produkcji, organizacyjnych i zarządzających organizacji na przykładzie JSC Agopromtrans. Poprawa systemu zarządzania konfliktem w organizacji rolnej.
egzaminowanie dodane 01/18/2015
Charakterystyka gatunków, form i rodzajów organizacji produkcji. Charakterystyczne cechy przepływu, części i indywidualnych metod organizacji produkcji. Cechy organizacji produkcji w pomocniczym i obsługującym podziały przedsiębiorstwa.
abstract, dodał 06.06.2010
Ogólne postanowienia organizacji metod produkcji strumieniowej. Opracowanie przedmiotowej formy specjalizacji warsztatów. Produkcja potacyjna jest progresywną formą organizacji procesów produkcyjnych. Charakterystyczne oznaki organizacji produkcji przepływowej.
egzaminowanie dodane 03.06.2008
Zasady, formy, metody organizacji produkcji. Obliczanie programu produkcyjnego, potrzeba sprzętu, obszar warsztatu i liczby głównych pracowników produkcyjnych. Organizacja naprawy, instrumentalny, magazynowy, transport.
zajęcia, dodano 02.03.2010
Ekonomiczna istota wynagrodzenia w gospodarce rynkowej, jej forma. Analiza systemu wynagrodzenia w przedsiębiorstwie "prawdziwa" naprawa i firma transportowa LLC. Wdrożenie propozycji stosowania metod materialnych do poprawy motywacji personelu.
teza, dodano 01.07.2014
Rodzaje organizacji produkcyjnej: Esencja, koncepcja i charakterystyka porównawcza. Cechy i zalety typu seryjnego metody partii organizacji produkcji. Główne kierunki poprawy efektywności ekonomicznej organizacji produkcji.
Dziękujemy Zarządem Dziennika "Saturn" NPO "Saturn" za dostarczenie tego materiału.
Z biegiem lat istnienie przedsiębiorstw opracowało praktykę, że fabryka tworzy siedzibę głównego mechanika, aw warsztatach istnieją niezależne usługi do naprawy i utrzymania sprzętu. Jednocześnie zarządzanie takimi usługami jest przeprowadzane bezpośrednio przez głowę warsztatu lub jego podstawnika i funkcjonalnie głównym mechanikiem. W warsztatach organizowanych są magazyny części zamiennych do ich sprzętu, personel jest zatrudniony do naprawy sprzętu, tworzy się własne harmonogramy napraw, które są wykonywane przez ich własnych ludzi. I tak przez wiele lat, aż pojawi się zaawansowany sprzęt, który jest raczej podobny do "szafy z przewodami" niż zwykła maszyna. A takie maszyny są bardziej trudne do ich obsługi ...
Nowe technologie produkcyjne i wymagania jakości wymagały również zupełnie nowych rodzajów sprzętu. Oczywiście było możliwe uzyskanie specjalistów na tym urządzeniu lub w celu uczenia się w każdym warsztacie pracowników. Ale nadal muszą je znaleźć!
Jest to tylko jedno z problemów, które musiałem zmierzyć się z głównym służbą mechanikiem silników ADC-Perm. W końcu, z początkiem przygotowania do seryjnej produkcji silnika PD-14, nie tylko liczba otrzymanych urządzeń, ale także jego złożoność wzrosła. Nowe technologie produkcyjne i wymagania jakości wymagały również zupełnie nowych rodzajów sprzętu. Oczywiście było możliwe uzyskanie specjalistów na tym urządzeniu lub w celu uczenia się w każdym warsztacie pracowników. Ale nadal muszą je znaleźć!
Jednocześnie, dla nabytego sprzętu, musisz nadal tworzyć własne szczegóły naprawy funduszy. I tak w każdym warsztacie ... stał się problemem "numer dwa" do służby głównego mechanika.
A on był pogorszył fakt, że warsztaty nie były prawie żadne statystyki w sprawie niepowodzenia, przestoje nie zostało naprawione, naruszyli rekordy dostępnych części zamiennych do sprzętu i żadnych jasnych informacji, które będą wymagane w najbliższej przyszłości.
W kontekście wzrostu produkcji, każda godzina przestojów sprzętu była wrażliwa ze względu na naprawę. A tym dalej, tym trudniej było poradzić sobie ze wzrostem wielkości "pracy". I tak kontynuowane aż do istniejącego systemu usług i sprzętu naprawczego przestaną poradzić sobie.
Konieczne było zbudowanie wszystkiego od podstaw. Są to procesy planowania usług sprzętu, tworzenie połączenia operacyjnego z głównym serwisem mechaniku, gdy maszyny są niedostępne, organizacja zarządzanego funduszu części zamiennych, tworzenia i przywrócenie możliwości naprawczych "na własną rękę" .
Analiza aktualnego stanu
Analiza organizacji pracy nad utrzymaniem sprzętu wewnątrz sklepów pokazała jego wady. Po pierwsze, nie ma pewnych zasad, jakich prac iw jakich objętościach powinny być przeprowadzane w warsztacie i kiedy konieczne jest podanie maszyny do organizacji Umawiającej się. Po drugie, warsztaty są wykonywane tylko przez prace, które mogą być w bieżącym czasie w zależności od dostępności części zamiennych. Po trzecie, jak wspomniano wcześniej, praca wykonywana nigdzie nie jest rejestrowana, a przypadki naprawy mogą być ujawnione tylko w przypadku zakupu części zamiennych lub ze stałym odwołaniem do organizacji Umawiającej się.
Aby zbudować system powiadamiania o awarii sprzętu, zdecydowano zawęzić istniejącą Armę "Aplikacje do naprawy aplikacji". Wcześniej, aby poinformować o właściwym usługach, Master Manufacturing był konieczne, aby znaleźć mechanikę warsztatów, poczekać na pracowników służby mechanicznej, przynieść problem z wykonawcami, do których w rezultacie poszedł do kilku godzin zmian.
Statystyki dotyczące awarii sprzętu i przyczyn awarii
W tej chwili, w przypadku awaryjnego lub zaplanowanego konserwacji, mistrz produkcji wystarczy, aby umieścić znak na stanie sprzętu, a następnie cały proces już się dzieje bez jej udziału. Jednocześnie, ze względu na automatyzację, możliwe stało się zbieranie statystyk przy każdej okazji dla każdego przypadku, z czego jedno lub inna maszyna zatrzymuje się i już planuje niezbędne rodzaje napraw dla każdej jednostki sprzętu.
Rachunkowość stanu naprawy przestojów i aktualnego sprzętu
Optymalizacja istniejących zasobów
Głównym zadaniem tej fazy była ocena istniejących zasobów na utrzymywanie sprzętu w warunkach roboczych. W każdym warsztacie zorganizowano inwentaryzację części zamiennych i przeprowadzono analizę. Warto zauważyć, że w tym samym czasie spis przeprowadzono w organizacji pojedynczego magazynu części zamiennych. W tym czasie umożliwiło zmniejszenie potrzeb dla szczegółów amfibu dla obrabiarek. Gdy wszystkie informacje zostały zebrane, okazało się, że większość części zamiennych potrzebnych w tym momencie była w sąsiednich sklepach, a częściej w magazynach warsztatów "Lay" Szczegóły do \u200b\u200bmaszyn, które są już odpisane w tym warsztacie.
Równie ważnym zadaniem było ocena istniejącej kompozycji personelu ...
Przepraszamy, materiał ten jest dostępny całkowicie dla uczestników Wspólnoty menedżerów produkcji.
Możesz zarejestrować się i uzyskać dostęp do ekskluzywnych materiałów analitycznych, metodologicznych i tłumaczeniowych opublikowanych na stronie.
Udział daje również wiele dodatkowych funkcji.
Tak. Kosinov, A.a. Romanov, Yu.v. Troofimov.
(OJSC "TSKB Energoremont", OJSC "RAO UES Rosji" ")
1. Oświadczenie o poprawach naprawy obiektów
Energetyka elektryczna
Podstawowe kryteria poprawy konserwacji i naprawy muszą być odpowiedzialne za zakończone cele produkcji energii - zapewnienie niezawodności dostaw energii konsumentów.
Na poziomie indywidualnych firm produkujących, ostateczne cele są odpowiednio zróżnicowane. W tym względzie objawia się grupa drugorzędowa końcowa korzyści z produkcji energii - zapewniająca konkurencyjność transmisji energetycznej.
Wszystkie te cele są ze sobą powiązane i stanowią podstawę do tworzenia zadań poprawy naprawy mocy elektrycznych bez uwzględnienia ich przynależności państwa i urządzenia społeczno-ekonomicznego.
Aby zapewnić kryteria priorytetowe do poprawy produkcji energii, pragnienie osiągnięcia wyższych wskaźników gotowości źródeł energii w celu przeprowadzenia obciążeń.
Takie wskaźniki w obszarze teorii niezawodności są uważane za złożone. Pomimo znanej treści powyższego kadencji, w sferze stosunków energetycznych i konsumentów, coś takiego jest wykorzystywane jako wskaźnik, który może wpływać na rating firmy energetycznej w realizacji akcji i innych papierów wartościowych. Zasadniczo takie relacje są przyjęte w krajach Ameryki Północnej.
Aby zapewnić bardziej wyładowane kryteria do poprawy produkcji energii, należy przypisać pragnienie osiągnięcia niższych wskaźników składnika naprawczego taryf dla energii elektrycznej i termicznej. Te ostatnie zmniejsza warunkowy stały składnik taryf, a także przyczynia się do zwiększenia konkurencyjności spółek energetycznych.
Wskazane kryteria poprawy konserwacji i naprawy, naturalnie, nie można uznać za wyczerpujące, ale na podstawie ich możliwe jest sformułowanie niektórych warunków wstępnych do bardziej szczegółowych zadań w dziedzinie produkcji energii krajowej.
Od początku lat 90., ze względu na znane okoliczności, krajowa energetyka elektryczna dołączyła do fazy zmniejszenia produkcji energii. Wybierane rezerwy w połączeniu z osłabieniem funkcji systemu administracyjnego polecenia doprowadziły szereg negatywnych manifestacji. Wyrażali one w zwiększaniu czasu trwania przestoju efektywności energetycznej w różnych rodzajach napraw, a także w nieprzewidywalnym zwiększeniu kosztów konserwacji i naprawy.
Zewnętrzne warunki wstępne zmniejszenie efektywności energetycznej okazały się znacznie znaczące, ale nie dominujące. Podstawą negatywnych procesów były ekonomiczne i fizyczne aspekty starzenia się sprzętu.
Negatywne trendy powstałe w odpowiednim czasie badano w odpowiednim czasie, a ich konsekwencje były w dużej mierze pokonano. Proponowany projekt poprawy produkcji naprawy energetycznej nie naruszył istniejącego systemu istniejących standardów państwowych, dokumentów regulacyjnych w ramach nadzoru technicznego państwa-górskiego, zasad działania technicznego i zasad organizacji utrzymania i naprawy sprzętu, budynków i Struktury elektrowni i sieci. Jego istotą było zorganizowanie przejścia z cykli naprawczych w kalendarzu do cykli tego samego typu, ale weź pod uwagę wcześniej osiągnięte operacje w okresach INTROTALNYCH na określonych typach podstawowych urządzeń. Pozostałe warunki zostały zachowane niezmienione, w tym wykonanie kapitału i przeciętnych napraw w tym samym czasie dla wszystkich rodzajów sprzętu sprzętu, które naturalnie nie przyczyniły się do zmniejszenia kosztów sprzętu naprawczego i przestojów.
W wyniku wdrożenia rozwiniętego projektu w celu poprawy produkcji naprawy energetycznej, miękkie przejście z sztywnego systemu regulacji cykli naprawczych do systemu napraw, biorąc pod uwagę poprzednio osiągnięty występowanie w okresach częstotliwości.
Pomimo empirycznego podejścia do oceny zasobów interrepromerów, pierwszy krok został dokonany do badania nieformalizowanych procesów diagnostyki technicznej urządzenia elektrowni TPP.
Rozwój te zostały zapisane w dokumencie kierownicy Rd 34.20.601-96 "Instrukcje metodyczne w sprawie poprawy systemu konserwacji i naprawy elektrowni i elektrowni elektrowni termicznych na podstawie cyklu naprawczego z wyznaczonym zasobem międzyrektorowym".
W ramach "miękkiej" przejścia do naprawy z wyznaczonym zasobem INTERONTAL, pewnego spadku poziomu wcześniej praktykującego zasobów administracyjnych w realizacji innowacji należy rozumieć. Założono, że urządzenia energetyczne powinny niezależnie podejmować decyzje dotyczące wprowadzenia proponowanych ulepszeń. Tutaj odzwierciedlono naturalne oczekiwania na najbliższe przejście krajowej elektrowni elektrycznej do stosunków rynkowych.
Pomimo tych, którzy do tej pory nie byli uzasadnione, były tylko częściowe wdrażanie opracowanych działań, ogólnie udało się ustabilizować wydajność gotowości TPP do przenoszenia ładunków. Jednak przezwyciężenie wzrostu kosztów utrzymania i naprawy nie był możliwy.
Fundamentalny czynnik systemu administracyjnego polecenia został objawiony tutaj do pewnego stopnia - koszty planowania od wcześniej osiągniętych wskaźników. Woluminy fizyczne wzrosły - zwiększyły koszty. W przypadku udowodnienia dodatkowych woluminów fizycznych, składnik naprawczych taryf produktów końcowych wzrasta odpowiednio.
Dodatkowe do typowych fizycznych woluminów napraw są zwykle przypisywane "superdipov". Charakteryzują się znacznie dużą zawartością stosowanych materiałów, części zamiennych i niezbędnych elementów strukturalnych w postaci zastępowanych jednostek zużycia i często dominują w wycenie komponentu naprawczego taryf.
W tym względzie nie zawsze jest możliwe ustalenie zrównoważonych korelacji między tymczasowym wykonywaniem przestojów sprzętu w naprawach i odpowiednich kosztach.
Jednocześnie rozwiązywanie zadań w celu ustabilizowania rocznych przestojów sprzętu we wszystkich rodzajach napraw okazało się dość przejrzyste i skorelowane. Wzrost czasów przestojów określonych sprzętu lub grup sprzętu było ogólnie zrekompensowane przez wzrost okresu INTROTALIA, co prowadzi do zmniejszenia udziału sprzętu, rocznie rejestrowane na remonty kapitałowe i przeciętne naprawy.
W rezultacie wskaźniki gotowości źródeł energii do ładowania obciążeń, niezależnie od znanych danych o zwiększonych kosztów napraw i zapewniły zrównoważone funkcjonowanie energetyki elektrycznej.
Kolejne badania wykazały, że tylko stosunki rynkowe w dziedzinie produkcji energii mogą stworzyć niezbędne warunki pragnienia zmniejszenia kosztów utrzymania i naprawy mocy elektrycznej.
Instrument ekonomiczny kolejnych oczekiwań powinno być stosunkiem konkurencyjnymi wśród spółek energetycznych, a funkcjonalne - przejście do naprawy konserwacji.
Podczas opracowywania systemu na naprawę konserwacji należy pamiętać, że krajowa energetyka elektryczna na etapie startowej ma wskaźniki niezawodności odpowiednie do zagranicznych analogów, a wszelkie innowacje muszą być wystarczająco zbadane i uzasadnione, aby nie zniesławić ich korzyści.
Należy również zapłacić fakt, że nasza energetyka elektryczna działa w nie-zwykłą przestrzenią gospodarczą. Ceny materiałów i produktów mechanicznych inżynierii podejścia do świata. Ceny paliwowe są sztucznie zanigularne w warunkach rynku gęstości wewnętrznej w proporcjach odwrócić świat. Regulowane taryfy energii elektrycznej i termicznej są koncentratem niespójności ekonomicznych. W takich warunkach jest mało prawdopodobne, aby liczyć na ujawnienie jakichkolwiek wzorów wpływających na zmianę składnika naprawy kosztów produkcji.
W obecnej sytuacji wydaje się, że jest większy w większym stopniu w celu prowadzenia różnych rodzajów ilości fizycznych, wskaźników ilościowych i jakościowych, takich jak wskaźniki niezawodności, wydajności itp.
2. Uruchomienie warunków do dalszej poprawy naprawy
Usługi. Średniookresowe prognozy zmiany indywidualne
Charakterystyka stanu sprzętu TPP
Oceniając obecny stan energii cieplnej w dziedzinie gospodarki naprawczej, można zauważyć, że przez 12 lat (od 1987 r.), Koszty napraw na podstawie TPP zmniejszyły się o 24%, a federalny poziom federalny poziom wzrósł o 2%.
W tym samym okresie koszty napraw jako całości wzrosły przez TPP wzrosły o 27%, zgodnie z jednostką mocy "AO-ENERGO" - o 23%, oraz w federalnym TPP poziomu federalnego - o 73%.
Jednocześnie liczba godzin korzystania z zainstalowanej pojemności spadła o 1,48 razy.
W okresie od 1999 r. Do 2001 r. Szczegółowe koszty 1 kW naprawionej mocy federalnej TPP Federalnego poziomu wzrosły o 3,53 razy.
Dane te wskazują na wadę gospodarki
Wydajność stosowania pojazdów silnikowych zależy od doskonałości organizacji procesu transportowego i właściwości pojazdów do zapisania w pewnych ograniczenia parametry charakteryzujące ich zdolność do wykonywania wymaganych funkcji. Podczas pracy samochodu jego właściwości funkcjonalne stopniowo pogarszają się ze względu na zużycie, korozję, uszkodzenia części, zmęczenie materiału, z których są wykonane, itd. Istnieją różne awarie w samochodzie, które zmniejszają wydajność jego wykorzystania. Aby zapobiec wyglądowi defektów i terminowej eliminacji, samochód jest utrzymany (COM) i naprawa.
Konserwacja w przedsiębiorstwie jest wykonana przez samych kierowców i, jeśli to konieczne, ślusarzy na tym. Wniosek o naprawy jest odbierany przez Departament Workshop Autor Naprawa (ramiona), które kieruje obfitości w określonej strefie konserwacji. Dzięki bieżącą pozycję przedsiębiorstwo stale nie stanowi częstotliwości konserwacji. Wbrew wymogom organizacji konserwacji w reklamach nie ma kontroli samochodów, które były obsługiwane przez Departament Service. Z reguły samochody są wysyłane do jednoczesnych napraw, ponieważ samochody są bezczynne w obszarze serwisowym bardziej określony czas, przeszkadzając w ten sposób rytm produkcji naprawczej. Tankowanie, zmieniające się oleje silnika i transmisji odbywa się za pomocą prymitywnych środków, co przyczynia się do utraty cennych produktów naftowych, naruszenie standardów sanitarnych, wymagań przeciwpożarowych, a także wymogi ochrony pracy w ogóle. Ponadto taka organizacja pracy uniemożliwia normalną zbiór zużytych olejów do regeneracji i ponownego użycia.
W polu strefy i naprawy, oświetlenie naturalne i sztuczne, a także reżim temperaturowy jest znacznie niższy niż dopuszczalne normy. Brak sztucznej wentylacji prowadzi do silnego stycznego gazu. Jest to również naruszenie wymagań bezpieczeństwa. Niewielka liczba części zamiennych, prowadzi do długotrwałej naprawy samochodu. Tak więc słaba organizacja konserwacji i naprawy magazynowania pojawia się przede wszystkim w następujących punktach: brakiem czasu jest przedtem bezpośrednio w obszarach; niewystarczający poziom mechanizacji; Nieprzestrzeganie niektórych wymogów bezpieczeństwa, w szczególności niewystarczające oświetlenie pomieszczeń przemysłowych i brak sztucznej wentylacji w strefie. Biorąc pod uwagę istotną rolę samochodów i z uwzględnieniem analizy działań przedsiębiorstwa w zapewnieniu wystarczającej wiarygodności operacyjnej akcji tocznych powinna zakończyć następujące. Istniejąca organizacja konserwacji i bieżących napraw walcowanych wymaga poprawy. Konieczne jest rozwój środków na rzecz poprawy organizacji produkcji i służby technicznej przedsiębiorstwa.
W zależności od zakresu prac są wykonywane przez przepływ lub metodę dead-end. Organizacja jest metodą dead-end (na uniwersalnych stawach końcowych), zaleca się różnego czasu trwania pobytu samochodu na każdym poście. Wady tej metody obejmują znaczną utratę czasu na instalacji samochodu na stanowisko oraz kongres z niego, zanieczyszczenie powietrza przez odpady gazów podczas manewrowania i potrzeby korzystania z dużej liczby identycznych urządzeń.
Płynna metoda organizacji przewiduje wykonanie pracy na wyspecjalizowanych stanowiskach roboczych w określonej sekwencji o określonym czasie pracy. Metoda ta pozwala na zmniejszenie utraty czasu na ruchomych samochodach i przejście pracowników z jednego posta do drugiego, a także bardziej ekonomicznie korzystać z obszaru pomieszczenia produkcyjnego. Wadą metody przepływu jest złożoność zmian w zakresie pracy w miejscu pracy.
Operacje konserwacji samochodowej są wykonywane zgodnie z postodologicznymi kartami operacyjnymi. Wskazują nazwę operacji, te. Warunki i standardy czasowe dotyczące jego wykonania, stosowane narzędzie i sprzęt, pracownik specjalny, wykonanie post i liczba punktów serwisowych. Publikowanie kart technologicznych są przeznaczone do wykonywania pracy do sterowania regulacją i smarowaniem kruszywa lub węzła.
W samochodach na liniach strumienia wypełnij mapę - schemat aranżacji pracowników na stanowiskach. Mapa - schemat zawiera informacje o liczbie pracowników, wydajność linii serwisowej dla przesunięcia i danych mapy po technologicznej.
Organizacja produkcji może być brygadą lub dzielką brygay. W formie brygady organizacji brygady wykonują prace na wszystkich jednostkach maszynowych w tym rodzaju serwisie. W formacie obwodowej organizacji Brigaya, wszystkie prace nad utrzymaniem odpowiednich agregatów są wykonywane na oddzielnych miejscach produkcyjnych. W zależności od programu pracy ATP ustanawia inną liczbę sekcji przemysłowych różnych celów. Dzięki małym programowi pracy ATP możliwe jest utrzymanie kilku rodzajów agregatów w jednym miejscu.
We wszystkich ATP, działki lub brygady można łączyć w celu łączenia do kompleksów produkcyjnych w następujących rodzajach pracy: konserwacja maszyn i zdiagnozować ich stan techniczny; ciągła naprawa bezpośrednio w samochodach; Obecna naprawa agregatów, węzłów i części pobranych z samochodów.
Główne kierunki poprawy bazy naprawczej to:
Poprawa systemu zaplanowanej naprawy, która zapewni wyraźny nadzór i terminowe zapobieganie pracom sprzętu, co z kolei zwiększy jego wydajność, zwiększy okresy INTROSTALNE.
Poprawa technicznego przygotowania napraw, w tym rozwój typowych procesów technologicznych, a także wsparcie materiałowe.
Określanie optymalnych okresów wymiany zużytych części w zależności od stopnia amortyzacji i wymaganych kosztów naprawy.
Usługi naprawy transportu technologicznego i warsztatowego powinny być tak bardzo, jak to możliwe, wyposażone w nowoczesny sprzęt, umożliwiający stosowanie technologii progresywnej, zaawansowanych form organizacji produkcyjnych, środki mechanizacji i automatyzacji procesów produkcyjnych.
Wskaźniki zespołu naprawczego powinny być zapewnione przez prawidłową dystrybucję prac między członkami brygady.
Aby zmniejszyć przestoje samochodowe, konieczne byłoby użycie metody napraw podnośnikowych. Istotą metody jest to, że węzły i mechanizmy wymagające naprawy są usuwane i zastąpione nowymi lub zaawansowanymi odnowionymi.
Konieczne jest również poprawę reżimu oświetlenia i temperatury w polach naprawczych. Dość szybsze podaż części zamiennych.
Analiza zarządzania naprawczem PolimerProm ma na celu zidentyfikowanie osiągnięć i wad w tym obszarze, kontur sposoby wyeliminowania niedociągnięć i środków w celu poprawy systemu PPR w fabryce.
Głównymi kierunkami poprawy polimerprom zarządzania naprawcze to:
1. Organizacja scentralizowanego specjalistycznego naprawy sprzętu. Warunek ten jest przeprowadzany w obecności centrum serwisowego dostawcy, jako ponad 70% zagranicznych urządzeń produkcyjnych.
2. Organizacja wyspecjalizowanej produkcji części zamiennych do sprzętu. Wydaje się możliwe, aby zmniejszyć koszty produkcji części zamiennych do sprzętu i poprawę swojej jakości do poszukiwania podstawy przetargowej (producentów) z liczby przedsiębiorstw narzędziowych i naprawczych, które są zdolne do wykonania nomenklatury części niezbędne do naprawy.
3. Dalsza poprawa w przedsiębiorstwie systemu planowania naprawy sprzętu, która zapewni wyraźny nadzór i terminowe zapobieganie pracom sprzętu, co z kolei zwiększy jego wydajność, zwiększy okresy częstotliwości.
4. Poprawa technicznego przygotowania napraw, w tym opracowywanie typowych procesów technologicznych, a także wsparcie materiałowe.
W związku z małym wielkością przedsiębiorstwa serwis naprawczy polimerprom ma również ograniczoną wielkość. Dlatego wydaje się właściwą obecność w przedsiębiorstwie bieżącej scentralizowanej usługi naprawy, która wykonuje wszystkie funkcje do konserwacji i naprawy sprzętu.
W odniesieniu do pracowników serwisu naprawczego stosuje się system wynagrodzenia demonstracyjnego. Ta forma wynagrodzenia nie jest wystarczająco skuteczna. Najbardziej skuteczną formą wynagrodzenia jest umowna forma wynagrodzenia z ustanowieniem składek i składek, w zależności od dostępności sprzętu do winy pracownika serwisowego naprawczego, a także na dostępności roszczeń do pracy sprzętu z głowy działek.
Aby poprawić efektywność serwisu naprawczego, zaleca się korzystanie z automatycznego systemu serwisowego naprawczego w przedsiębiorstwie.
Konieczne jest również powszechnie korzystać z wytycznych i zaleceń natury krajowej, rozwoju i dostawy organizacji badawczych i projektowych.
Zautomatyzowany system zarządzania naprawcze jest funkcjonalnym podsystemem zarządzania, gdy z odpowiednim działem organizacyjnym i administracyjnym, głównym działem mechanikiem jest głównym ośrodkiem koordynującym i niezbędnym związkiem w zintegrowanym systemie zarządzania przedsiębiorstwem. Wprowadzenie tego podsystemu umożliwia wykorzystanie metod komputerowych i matematycznych, aby określić optymalną strategię dla sprzętu do konserwacji i naprawy, optymalne stężenie wolumenów pracy i stężenie sprzętu do warunków specjalistycznej produkcji prac naprawczych.
Za pomocą zautomatyzowanego systemu zarządzania usługami naprawczymi, taka organizacja naprawy i konserwacji przedsiębiorstw parku maszynowego powinna być tworzona, w której stosowanie pracy, materiałów i środków finansowych byłoby optymalne, a przestoje sprzęt jest minimalny.
Opracowywanie badań danych jednostek naprawczych, model gospodarczych gospodarczych i organizacyjnej zarządzania produkcją naprawy, ujednolicone formy dokumentów są opracowywane, schemat przepływu dokumentów jest budowany, a model opracowywania łączy informacji, Opracowywane są metody i modele ekonomiczne i matematyczne do mechanizacji i automatyzacji rozliczeń gospodarczych oraz skład środka technicznego. Model gospodarczy i organizacyjny jest podstawą utworzonego podsystemu podtrzymującego, określa zasady jego funkcjonowania i podstaw organizacyjnych systemu zarządzania, a także uwzględnia potrzebę powszechnych wrażliwych relacji, spełniają zasady zachęt istotnych.
Przy projektowaniu zautomatyzowanego systemu zarządzania usługą naprawczą, opracowanie połączonego kompleksu pracy jest niezbędne do rozwiązania głównych problemów produkcji naprawy. Ten kompleks pracy koncentruje się na tworzeniu menedżerów funkcjonalnych podsystemów i niezbędnych do ich funkcjonowania dostarczania podsystemów.
Podsystemy funkcjonalne wykonują funkcje zarządzania dla organizacyjnych i technicznych przygotowań produkcji, prognozowania i obiecującego planowania, wykonalności oraz planowania gospodarczego i operacyjnego, rachunkowości, sprawozdawczości i analizy działalności gospodarczej, a także monitorowania i regulujących pracę jednostek naprawczych.
Podsystemy, które zapewniają podsystemy, obejmują podsystem wsparcia gospodarczego i organizacyjnego, informacyjnego, matematycznego i technicznego. Główną funkcją dostarczania podsystemów jest transformacja wszystkich informacji cyrkulacyjnych między podsystemami funkcjonalnymi i jednostkami produkcyjnymi w celu wygenerowania efektu kontroli na jednostkach produkcyjnych głównego serwisu mechanika.
Rozwój zautomatyzowanego systemu kontroli usługi naprawy UE "polimerprom" powinno być przeprowadzane przez wyspecjalizowane organizacje z zaangażowaniem przedsiębiorstwa Klienta lub sił przedsiębiorstw w obecności wystarczającej liczby specjalistów.
Przy projektowaniu podsystemu zautomatyzowanego systemu zarządzania naprawcze należy zwrócić szczególną uwagę na następujące prace:
1. Utworzenie zautomatyzowanej księgowości sprzętu w działkach i przedsiębiorstwie jako całości; wykorzystanie działania sprzętu produkcyjnego w czasie i w mocy; rachunkowość wyposażenia przestojów w naprawie; awarie i awarie każdej jednostki sprzętu i poszczególnych węzłów, bloków, części; Potrzeby, dostępność i ruch części zamiennych do operacyjnej floty sprzętu.
Automatyzacja planowanych obliczeń w pracy nad pracą nad planowaniem i systemem prewencyjnym opartym na wykorzystaniu nowoczesnych urządzeń komputerowych, stosowanych metod matematycznych i progresywnych standardów dotyczących kosztów materiałów i pracy.
Organizacja regulowanego smarowania sprzętu.
Określanie optymalnych terminów do wymiany zużytych urządzeń w zależności od stopnia amortyzacji i niezbędnych kosztów serwisu naprawczego.
Sukces zautomatyzowanego systemu kontroli usługi naprawczej zależy od tego, jak w pełni następujące etapy pracy: rozwój przepisów ogólnych; Badanie wstępnego projektu (diagnostyczne) pracy jednostek naprawczych; projekt techniczny; projektowanie pracy; Wprowadzenie podsystemu.
Produkcja naprawa charakteryzuje się szeregiem określonych funkcji, które utrudniają proces zarządzania i racjonalną organizację składników strukturalnych (jednostki naprawcze). Takie funkcje obejmują przede wszystkim niejednorodność prac naprawczych.
Gospodarcze uzasadnienie celowania wdrażania zautomatyzowanego systemu zarządzania naprawcze powinno towarzyszyć obliczenie efektywności ekonomicznej.
Pociągi naprawcze i mechaniczne i usługi naprawy warsztatów powinny być najbardziej wyspecjalizowane, wyposażone w nowoczesny sprzęt, umożliwiający stosowanie technologii progresywnej, zaawansowanych form organizacji produkcyjnych, środki mechanizacji i automatyzacji procesów produkcyjnych.
Wskaźniki zespołów naprawczych zapewniają odpowiednią dystrybucję prac między członkami brygady, skutecznej organizacji miejsc pracy, wykorzystanie progresywnych metod organizowania napraw i jasnej organizacji usług pracy.
Znaczące koszty redukcji rezerwy na naprawę i wyposażenie przestojów w naprawie są wielokrotne korzystanie z części.
Przywrócenie części umożliwia zmniejszenie zużycia zasobów materiałowych i finansowych podczas naprawy części do 60-90%. Koszt odrestaurowanych części jest często 10-25% kosztów nowej części.
Wniosek
Podczas wykonywania prac naprawczych w przedsiębiorstwach przemysłowych konieczne jest dążenie do maksymalnego stężenia tego samego rodzaju pracy w niektórych zakładach produkcyjnych usług naprawczych. Muszą być tworzone i wyposażone w pełną zgodność z zadaniami, które są dostarczane im, a zakres pracy do spełnienia.
Głównymi kierunkami poprawy usługi naprawy przedsiębiorstwa są:
Organizacja scentralizowanego wyspecjalizowanego naprawy sprzętu;
Organizacja wyspecjalizowanej produkcji części zamiennych do sprzętu;
Dalsza poprawa planowania systemu i prewencyjna naprawa sprzętu;
Poprawa technicznego przygotowania napraw, w tym opracowywanie typowych procesów technologicznych, a także materialne wsparcie prac naprawczych;
Poprawa planowania, w tym kompilację harmonogramów prac naprawczych.
Organizacja zarządzania naprawcze w przedsiębiorstwach jest ulepszona w następujących kierunkach.
Usługi naprawy przedsiębiorstw powinny być najbardziej wyspecjalizowane, aby być wyposażone w nowoczesne lub umożliwiające stosowanie technologii progresywnej, zaawansowanych form organizacji produkcyjnych, środki mechanizacji i automatyzacji procesów produkcyjnych.
Najbardziej efektywne wykorzystanie wyspecjalizowanych brygad naprawczych. Jednocześnie wskazane jest tworzenie i złożone brygady, które spełniają wszystkie prace nad opieką techniczną i naprawą sprzętu na działce produkcyjnej przymocowanej do brygady.
Progresywne metody naprawy odnoszą się głównie do węzoru. Istotą metody jest to, że węzły i mechanizmy wymagające naprawy są usuwane i zastąpione nowymi lub zaawansowanymi odnowionymi. Korzystanie z tej metody pozwala zmniejszyć do minimum sprzętu do naprawy, poprawić jakość naprawy i zmniejszyć koszty naprawy ze względu na możliwość najbardziej racjonalnej organizacji naprawy węzłów i mechanizmów.
Również znaczące koszty redukcji rezerwy na naprawę i wyposażenie przestojów w naprawie jest powtarzane stosowanie części.
Lista referencji:
1. Bakanov M.i., Sherimet A.D. Teoria analizy ekonomicznej. - M.: Finanse i statystyki, 2011.
2. Latfullin, G.r. Teoria organizacyjna: Podręcznik do uniwersytetów / G. Latfullin, A. V. Rychenko- spb.: Peter, 2007.
3. Milner, B.Z. Teoria organizacyjna: Podręcznik / B. Z. Milner- M.: Infra-M, 2008.
4. Terchistnik, Michaił Ivanovich Enterprise Economics: Samouczek dla studentów wyższych instytucji edukacyjnych, studenci w specjalności 080101 "Teoria ekonomiczna" (Reg. Review Number 404 Dated 03.07.2009, MGUP) / M. I. Torchshnik; Stan bajki. University of Economics and Law. - 2nd ed. - Moskwa: Infra-M, 2010.
5. Sergeev I.v. Enterprise Gospodarka. - M.: Finanse i statystyki, 2013.
6. Analiza działalności gospodarczej organizacji: Instrukcja szkolenia / W sumie. ed. D. A. Pankow, E. A. Golovkov. - 2 ED., ACT. - M.: Nowa wiedza, 2013.
7. Organizacja produkcji w przedsiębiorstwie (firmie): badania. Ręczny / ed.: O. I. Volkov, O. V. Devyatkina - M.: Infra-M, 2010.
8. Gospodarka korporacyjna: badania. Na uniwersytety przez ECO. specjalista. / [W. Ya. Gifinkel i in.]; Ed. V. Ya. Gorfinkel, V. A. Schward. - 4 ed. - Moskwa: Uniti-Dana, 2014.
9. Gospodarka korporacyjna (w schematach, tabelach, obliczeniach): Instrukcja szkolenia dla studentów studiujących w kierunku 521600 "Ekonomia" / V. K. Sklyarenko [i innych]; Ed. V.K. Sklyarenko, V. M. Prudnikova. - Moskwa: Infra-M, 2010.
10. Ekonomia przedsiębiorstwa (firmy): podręcznik dla studentów wyższych instytucji edukacyjnych studiujących w gospodarce. Specjalności / [O. I. Volkov i in.]; Ed. O. I. Volkov, O. V. Devyatkina; Ros. ECON. ACAD. im. G. V. Plekhanova. - 3rd ed., Peerab. i dodaj. - Moskwa: Infra-M, 2009.