Podstawy automatyzacji procesów technologicznych. Wprowadzenie (Podstawy automatyzacji procesów)
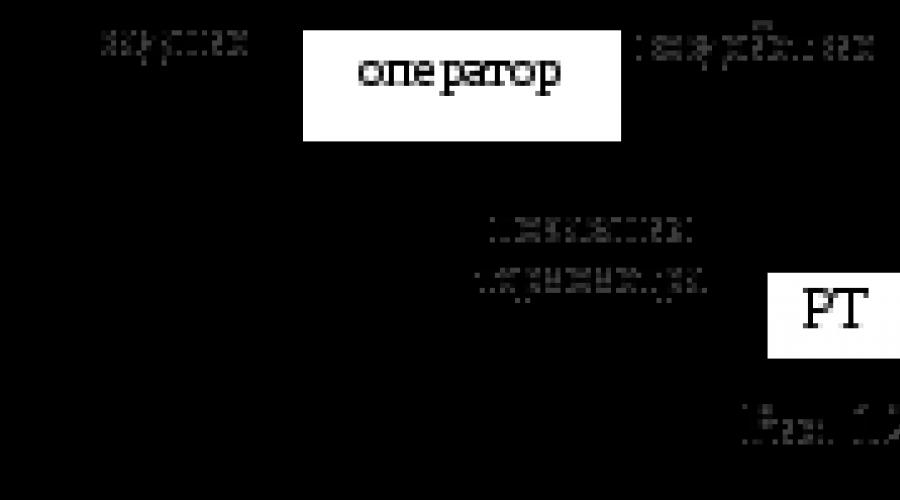
Ministerstwo Edukacji Zawodowej
Politechnika Tomska
Skorospeshkin M.V.
Podstawy automatyzacji procesów przemysłowych
Notatki do wykładów
Część 1. Teoria automatycznego sterowania (TAU)
1. Podstawowe pojęcia i definicje TAU.
1.1. Podstawowe koncepcje.
Systemy sterowania nowoczesnymi procesami technologicznymi charakteryzują się dużą liczbą parametrów technologicznych, których liczba może sięgać kilku tysięcy. Aby utrzymać wymagany tryb pracy, a ostatecznie jakość produktów, wszystkie te ilości muszą być utrzymywane na stałym poziomie lub zmieniane zgodnie z pewnym prawem.
Wielkości fizyczne, które determinują przebieg procesu technologicznego nazywamy parametry procesu . Na przykład parametrami procesu mogą być: temperatura, ciśnienie, przepływ, napięcie itp.
Parametr procesu technologicznego, który zgodnie z pewnym prawem musi być utrzymywany na stałym poziomie lub zmieniany, nazywa się kontrolowana zmienna lub regulowany parametr .
Wartość zmiennej sterowanej w rozpatrywanym momencie nazywamy wartość chwilowa .
Wartość zmiennej sterowanej uzyskana w rozpatrywanym momencie na podstawie danych z pewnego urządzenia pomiarowego nazywana jest jej zmierzona wartość .
Przykład 1 Schemat ręcznego sterowania temperaturą suszarni.
Wymagane jest ręczne utrzymywanie temperatury w suszarce na poziomie T ass.
Operator, w zależności od wskazań termometru rtęciowego RT, włącza lub wyłącza element grzejny H za pomocą przełącznika nożowego P.
Na podstawie tego przykładu możesz wprowadzić definicje:
Obiekt kontrolny (przedmiot regulacji, OS) - urządzenie, którego wymagany tryb pracy musi być wspierany z zewnątrz przez specjalnie zorganizowane czynności kontrolne.
Kontrola – tworzenie działań kontrolnych, które zapewniają wymagany tryb pracy systemu operacyjnego.
Rozporządzenie - szczególny rodzaj kontroli, gdy zadaniem jest zapewnienie stałości dowolnej wartości wyjściowej systemu operacyjnego.
Automatyczna kontrola - zarządzanie prowadzone bez bezpośredniego udziału osoby.
Akcja wprowadzania (X)– wpływ wywierany na wejście systemu lub urządzenia.
Akcja wyjściowa (Y) - wpływ wystawiony na wyjściu systemu lub urządzenia.
Wpływ zewnętrzny - wpływ środowiska zewnętrznego na system.
Schemat blokowy układu sterowania dla przykładu 1 pokazano na ryc. 1.2.
Przykład 2 Schemat automatycznej kontroli temperatury suszarni.
W obwodzie zastosowano termometr rtęciowy ze stykami RTK. Gdy temperatura wzrośnie do zadanej wartości, styki zwierają się słupkiem rtęci, cewka elementu przekaźnikowego RE zostaje wzbudzona, a obwód grzałki H zostaje rozwarty przez styk RE. Gdy temperatura spada, styki termometru otwierają się, przekaźnik wyłącza się, wznawiając dostarczanie energii do obiektu (patrz rys. 1.3).
R jest. 1,3
Przykład 3 Schemat temperatury ACP z mostkiem pomiarowym.
Gdy temperatura obiektu jest równa podanej, mostek pomiarowy M (patrz rys. 1.4) jest zrównoważony, wejście wzmacniacza elektronicznego EI nie otrzymuje sygnału i układ jest w równowadze. Gdy temperatura odbiega, rezystancja termistora RT zmienia się i równowaga mostka jest zaburzona. Na wejściu ED pojawia się napięcie, którego faza zależy od znaku odchylenia temperatury od zadanej. Wzmocnione w UE napięcie podawane jest na silnik D, który przesuwa silnik autotransformatora AT w odpowiednim kierunku. Gdy temperatura osiągnie wartość zadaną, mostek zostanie zrównoważony i silnik się wyłączy.
(ćwiczenie)
Wartość nastawy temperatury ustawia się za pomocą rezystora Rset.
Na podstawie opisanych przykładów można wyznaczyć typowy schemat strukturalny jednopętlowego ASR (patrz rys. 1.5). Przyjęte oznaczenia:
x - działanie ustawiające (zadanie), e \u003d x - y - błąd sterowania, u - działanie sterujące, f - działanie zakłócające (zakłócenie).
Definicje:
Wpływ ustawienia (tak samo jak akcja wejściowa X) - wpływ na system, który wyznacza wymagane prawo zmiany zmiennej sterowanej).
Akcja kontrolna (u) - wpływ urządzenia sterującego na obiekt sterowania.
urządzenie sterujące (CU) - urządzenie oddziałujące na obiekt sterowania w celu zapewnienia wymaganego trybu pracy.
Niepokojący wpływ (f) - działanie, które ma tendencję do przerywania wymaganej zależności funkcjonalnej między działaniem nastawczym a kontrolowaną wartością.
Błąd kontroli (e = x - y) - różnica między zalecaną (x) a rzeczywistą (y) wartością regulowanej zmiennej.
Regulator (P) - zespół urządzeń podłączonych do regulowanego obiektu i zapewniający automatyczne utrzymywanie zadanej wartości jego regulowanej wartości lub automatyczną jej zmianę zgodnie z określonym prawem.
Automatyczny system sterowania (ACP) – układ automatyczny z zamkniętym obwodem wpływu, w którym sterowanie (u) jest generowane w wyniku porównania rzeczywistej wartości y z zadaną wartością x.
Dodatkowe połączenie na schemacie blokowym AKP, skierowane z wyjścia do wejścia rozważanego odcinka łańcucha wpływów, nazywa się sprzężeniem zwrotnym (FB). Opinia może być negatywna lub pozytywna.
Automatyzacja procesów produkcyjnych to główny kierunek, w którym obecnie posuwa się produkcja na całym świecie. Wszystko, co wcześniej wykonywał sam człowiek, jego funkcje, nie tylko fizyczne, ale i intelektualne, stopniowo przechodzą do techniki, która sama wykonuje cykle technologiczne i sprawuje nad nimi kontrolę. To jest teraz ogólny kierunek nowoczesnych technologii. Rola człowieka w wielu branżach sprowadza się już tylko do kontrolera dla automatu.
Generalnie pod pojęciem „sterowania procesem” rozumie się zestaw operacji niezbędnych do uruchomienia, zatrzymania procesu, a także utrzymania lub zmiany wielkości fizycznych (wskaźników procesu) w wymaganym kierunku. Poszczególne maszyny, zespoły, urządzenia, urządzenia, zespoły maszyn i urządzeń, które wymagają sterowania, realizujące procesy technologiczne, w automatyce nazywamy obiektami sterującymi lub obiektami sterowanymi. Obiekty zarządzane mają bardzo zróżnicowane przeznaczenie.
Automatyzacja procesów technologicznych- zastąpienie fizycznej pracy osoby poświęcanej na sterowanie mechanizmami i maszynami przez działanie specjalnych urządzeń, które zapewniają tę kontrolę (regulacja różnych parametrów, uzyskanie określonej wydajności i jakości produktu bez ingerencji człowieka).
Automatyzacja procesów produkcyjnych pozwala wielokrotnie zwiększyć wydajność pracy, poprawić jej bezpieczeństwo, przyjazność dla środowiska, poprawić jakość produktu oraz bardziej racjonalne wykorzystanie zasobów produkcyjnych, w tym potencjału ludzkiego.
Każdy proces technologiczny jest tworzony i realizowany w konkretnym celu. Produkcja wyrobów finalnych lub uzyskanie wyniku pośredniego. Tak więc celem zautomatyzowanej produkcji może być sortowanie, transportowanie, pakowanie produktów. Automatyzacja produkcji może być kompletna, złożona i częściowa.
Częściowa automatyzacja występuje, gdy jedna operacja lub oddzielny cykl produkcyjny jest wykonywany w trybie automatycznym. W takim przypadku dozwolony jest ograniczony udział człowieka. Najczęściej do częściowej automatyzacji dochodzi wtedy, gdy proces jest zbyt szybki, aby osoba mogła w nim w pełni uczestniczyć, podczas gdy prymitywne urządzenia mechaniczne napędzane sprzętem elektrycznym doskonale sobie z tym radzą.
Częściowa automatyzacja z reguły jest stosowana na istniejącym sprzęcie i jest do niego dodatkiem. Największą efektywność wykazuje jednak, gdy jest początkowo włączony do całego systemu automatyki - jest natychmiast rozwijany, wytwarzany i instalowany jako jego integralna część.
Zintegrowana automatyka powinien obejmować osobny duży zakład produkcyjny, może to być osobny warsztat, elektrownia. W tym przypadku cała produkcja działa w trybie jednego połączonego zautomatyzowanego kompleksu. Złożona automatyzacja procesów produkcyjnych nie zawsze jest wskazana. Jej zakres to nowoczesna, wysoko rozwinięta produkcja, w której wykorzystuje się niezwykleniezawodny sprzęt.
Awaria jednej z maszyn lub jednostek natychmiast zatrzymuje cały cykl produkcyjny. Taka produkcja powinna mieć samoregulację i samoorganizację, która jest realizowana według wcześniej stworzonego programu. Jednocześnie osoba bierze udział w procesie produkcyjnym tylko jako stały kontroler, monitorując stan całego systemu i jego poszczególnych części, ingeruje w produkcję w celu uruchomienia oraz w przypadku wystąpienia sytuacji awaryjnych lub zagrożenia takie zdarzenie.
Najwyższy poziom automatyzacji procesów produkcyjnych - pełna automatyzacja. Dzięki niemu sam system realizuje nie tylko proces produkcyjny, ale również pełną kontrolę nad nim, którą realizują automatyczne systemy sterowania. Pełna automatyzacja ma sens w opłacalnej, zrównoważonej produkcji z ustalonymi procesami i stałym trybem działania.
Wszelkie możliwe odstępstwa od normy należy z góry przewidzieć i opracować systemy ochrony przed nimi. Pełna automatyzacja jest również niezbędna do prac, które mogą zagrażać życiu, zdrowiu człowieka, czy są wykonywane w miejscach dla niego niedostępnych - pod wodą, w agresywnym środowisku, w kosmosie.
Każdy system składa się z komponentów, które wykonują określone funkcje. W zautomatyzowanym systemie czujniki dokonują odczytów i przekazują je w celu podjęcia decyzji o sterowaniu systemem, polecenie jest już wykonywane przez napęd. Najczęściej jest to sprzęt elektryczny, ponieważ za pomocą prądu elektrycznego bardziej celowe jest wykonywanie poleceń.
Konieczne jest oddzielenie zautomatyzowanego systemu sterowania i automatycznego. Na zautomatyzowany system sterowania czujniki przesyłają odczyty do pilota do operatora, a on, po podjęciu decyzji, przekazuje polecenie do sprzętu wykonawczego. Na system automatyczny- sygnał jest już analizowany przez urządzenia elektroniczne, które po podjęciu decyzji wydają polecenia urządzeniom wykonawczym.
Uczestnictwo człowieka w systemach automatycznych jest nadal konieczne, aczkolwiek jako kontroler. Ma możliwość w każdej chwili interweniować w ten proces, poprawiać go lub go zatrzymać.
Tak więc czujnik temperatury może ulec awarii i podawać nieprawidłowe odczyty. Elektronika w tym przypadku będzie postrzegać swoje dane jako wiarygodne, bez ich kwestionowania.
Umysł ludzki jest wielokrotnie większy niż możliwości urządzeń elektronicznych, choć ustępuje im pod względem szybkości reakcji. Operator może rozpoznać, że czujnik jest uszkodzony, ocenić ryzyko i po prostu go wyłączyć bez przerywania procesu. Jednocześnie musi mieć całkowitą pewność, że nie doprowadzi to do wypadku. W podjęciu decyzji pomaga mu niedostępne dla maszyn doświadczenie i intuicja.
Taka ukierunkowana interwencja w systemy automatyczne nie niesie ze sobą poważnego ryzyka, jeśli decyzję podejmuje profesjonalista. Jednak wyłączenie całej automatyki i przełączenie systemu w tryb sterowania ręcznego jest obarczone poważnymi konsekwencjami, ponieważ dana osoba nie może szybko zareagować na zmianę sytuacji.
Klasycznym przykładem jest wypadek w elektrowni jądrowej w Czarnobylu, który stał się największą katastrofą spowodowaną przez człowieka ubiegłego wieku. Stało się tak właśnie z powodu wyłączenia trybu automatycznego, kiedy opracowane już programy zapobiegania wypadkom nie mogły wpłynąć na rozwój sytuacji w reaktorze zakładowym.
Automatyzacja poszczególnych procesów rozpoczęła się w przemyśle już w XIX wieku. Wystarczy przypomnieć sobie automatyczny regulator odśrodkowy firmy Watt do silników parowych. Jednak dopiero wraz z początkiem przemysłowego wykorzystania energii elektrycznej możliwa stała się szersza automatyzacja nie pojedynczych procesów, ale całych cykli technologicznych. Wynika to z faktu, że wcześniej siła mechaniczna była przenoszona na obrabiarki za pomocą przekładni i napędów.
Scentralizowana produkcja energii elektrycznej i jej wykorzystanie w przemyśle w zasadzie rozpoczęły się dopiero w XX wieku - przed I wojną światową, kiedy każda maszyna była wyposażona we własny silnik elektryczny. To właśnie ta okoliczność pozwoliła zmechanizować nie tylko sam proces produkcyjny na maszynie, ale także zmechanizować jego sterowanie. To był pierwszy krok w kierunku tworzenia automaty. Pierwsze próbki pojawiły się już na początku lat 30. XX wieku. Wtedy powstał sam termin „zautomatyzowana produkcja”.
W Rosji, wówczas w ZSRR, pierwsze kroki w tym kierunku podjęto w latach 30. i 40. ubiegłego wieku. Po raz pierwszy do produkcji części łożyskowych zastosowano automaty. Potem nastąpiła pierwsza na świecie w pełni zautomatyzowana produkcja tłoków do silników ciągników.
Cykle technologiczne zostały połączone w jeden zautomatyzowany proces, który rozpoczynał się od załadunku surowców, a kończył się pakowaniem gotowych części. Stało się to możliwe dzięki powszechnemu wówczas stosowaniu nowoczesnego sprzętu elektrycznego, różnych przekaźników, zdalnych przełączników i oczywiście napędów.
Dopiero pojawienie się pierwszych komputerów elektronicznych umożliwiło osiągnięcie nowego poziomu automatyzacji. Teraz proces technologiczny przestał być uważany za po prostu zestaw pojedynczych operacji, które należy wykonać w określonej kolejności, aby uzyskać wynik. Teraz cały proces stał się jednym.
Obecnie automatyczne systemy sterowania nie tylko prowadzą proces produkcyjny, ale również kontrolują go, monitorują występowanie sytuacji awaryjnych i awaryjnych. Uruchamiają i zatrzymują urządzenia technologiczne, monitorują przeciążenia, ćwiczą działania w razie wypadku.
Ostatnio automatyczne systemy sterowania sprawiają, że przebudowa sprzętu do produkcji nowych produktów jest dość łatwa. To już cały system, składający się z oddzielnych automatycznych systemów wielotrybowych podłączonych do centralnego komputera, który łączy je w jedną sieć i wydaje zadania do wykonania.
Każdy podsystem to osobny komputer z własnym oprogramowaniem przeznaczonym do wykonywania własnych zadań. to już jest elastyczne moduły produkcyjne. Nazywa się je elastycznymi, ponieważ można je przekonfigurować do innych procesów technologicznych, a tym samym rozszerzyć produkcję, weryfikować ją.
Szczytem zautomatyzowanej produkcji są. Automatyzacja przeniknęła produkcję od góry do dołu. Automatyczna linia transportowa do dostarczania surowców do produkcji. Zautomatyzowane zarządzanie i projektowanie. Ludzkie doświadczenie i inteligencja są wykorzystywane tylko tam, gdzie nie można ich zastąpić elektroniką.
3 ..Wstęp ( Podstawy automatyzacji procesów)
Obecnie następuje szybki rozwój produkcji i wykorzystania samoczynnych maszyn i aparatury, wzrost liczby procesów produkcyjnych realizowanych zgodnie z rodzajem technologii bezzałogowej. Różne urządzenia automatyczne przenikają do wszystkich sfer ludzkiej działalności, w tym nauki, produkcji i życia codziennego. Dla inżyniera każdej specjalności konieczne stało się zapoznanie z teoretycznymi podstawami i praktycznymi zastosowaniami automatyki w odniesieniu do jego zainteresowań zawodowych. Jest to szczególnie ważne dla inżynierów elektryków specjalizujących się w dziedzinie zautomatyzowanego napędu elektrycznego, ponieważ większość ich aktywności zawodowej polega na tworzeniu urządzeń do automatyzacji różnych procesów technologicznych, ich regulacji i eksploatacji w warunkach produkcyjnych.
Zwykły przebieg automatyzacji procesów technologicznych budowany jest w oparciu o technologię określonej produkcji: maszynowej, hutniczej, chemicznej, tekstylnej itp. Poświęca dużo miejsca na szczegóły, które są bardzo ważne dla specjalistów w branżach, ale nie tak ważnych dla inżynierów zajmujących się tworzeniem i eksploatacją systemów sterowania urządzeniami procesowymi. Dla specjalistów od zautomatyzowanego napędu elektrycznego ważne jest, aby mieć wyobrażenie o ogólnych zadaniach rozwiązywanych przez automatyzację w nowoczesnej, wysoko zmechanizowanej i zautomatyzowanej produkcji, o miejscu napędu elektrycznego w układach automatyki. Muszą poznać podstawy teorii automatyzacji procesów technologicznych oraz nauczyć się rozwiązywania prostych problemów technicznych związanych z projektowaniem, doborem sprzętu do zautomatyzowanych systemów, opracowywaniem algorytmów i oprogramowania do ich pracy w określonych warunkach eksploatacyjnych.
Termin automatyzacja odnosi się do bardzo szerokiej klasy procesów produkcyjnych i innych systemów organizacji pracy i innej działalności człowieka, w których znaczna część operacji związanych z procesami pozyskiwania, przetwarzania, przesyłania i użytkowania energii, materiałów, a zwłaszcza informacji, jest przekazywana do specjalistyczne urządzenia techniczne, narzędzia mechanizacji i maszyny sterujące. Zautomatyzowane procesy, w tym zarządzanie, regulacja i (częściowa) kontrola nad nimi, przebiegają autonomicznie, zgodnie z wcześniej przygotowanym programem i wpisanym na specjalny nośnik programowy, dzięki czemu nie ma potrzeby bezpośredniego udziału człowieka w ich normalnym funkcjonowaniu. Jedynie funkcje kontroli ogólnej oraz, jeśli to konieczne, naprawy i regulacji pozostają w gestii personelu konserwacyjnego. Nieodzownym elementem automatyzacji jest mechanizacja polegająca na zastępowaniu pracy fizycznej, wysiłku fizycznego człowieka działaniem maszynowym. W przeciwieństwie do prostej mechanizacji, automatyzacja z konieczności obejmuje przeniesienie do maszyn kontrolnych operacji zarządzania i organizowania zautomatyzowanego procesu zgodnie z celem wcześniej sformułowanym i ewentualnie dopracowanym podczas realizacji procesu. Cele automatyzacji są wielorakie. Mogą obejmować rozwiązywanie problemów zwiększania produktywności i wydajności pracy, poprawy jakości produktów, optymalizacji zarządzania, zapewnienia bezpieczeństwa pracy ludzi, ochrony środowiska itp.
Cele automatyzacji realizowane są przy pomocy zautomatyzowane systemy sterowania(ACS), ACS to zestaw metod matematycznych, środków technicznych (główne to komputery i inne urządzenia mikroprocesorowe), ich oprogramowania i kompleksów organizacyjnych, które zapewniają kontrolę i monitorowanie parametrów zautomatyzowanych obiektów zgodnie z celem ich autonomii funkcjonowanie. Obiekty automatyzacji obejmują:
procesy technologiczne, energetyczne, transportowe i inne procesy produkcyjne;
projektowanie różnych jednostek i maszyn, statków, budynków i innych konstrukcji, kompleksów przemysłowych;
organizacja, planowanie i zarządzanie w obrębie warsztatu, przedsiębiorstwa, placu budowy, jednostki wojskowej itp.;
badania naukowe i techniczne, diagnostyka medyczna, rozliczanie i przetwarzanie danych statystycznych, programowanie, sprzęt AGD, systemy bezpieczeństwa itp.
Spośród wszystkich wymienionych rodzajów zautomatyzowanych obiektów rozważymy tylko procesy technologiczne produkcji przemysłowej. Podczas automatyzacji tych ostatnich funkcje kontrolne i kontrolne wykonywane wcześniej przez osobę są przenoszone na automatyczne urządzenia sterujące i oprzyrządowanie. Jednocześnie doskonalona jest mechanizacja poszczególnych czynności roboczych. Urządzenia sterujące, odbierające informacje kanałami zwrotnymi o zmianach kontrolowanych parametrów, takich jak wymiary detali, prędkość obróbki, temperatura, forma, zgodnie z zadanym programem obróbki, sygnały sterujące zapewniające wykonanie programu obróbki w optymalnym trybie pracy .
Rozdział pierwszy zajmuje się ogólnymi zagadnieniami automatyzacji procesów technologicznych, głównymi funkcjami i strukturą systemu sterowania procesami. Ponieważ zarządzanie procesem technologicznym staje się możliwe dzięki procesom informacyjnym, które powstają równolegle z dotychczasowym procesem technicznym, w rozdziale drugim omówiono elementy teorii informacji w odniesieniu do kształtowania się procesów zarządzania informacją. Szczególną uwagę zwrócono na zagadnienia kodowania informacji w kodach binarnych, gdyż kody te są podstawą funkcjonowania wszystkich nowoczesnych urządzeń sterujących. Rozdział kończy omówienie sposobów organizacji wymiany informacji poprzez jej transmisję kanałami komunikacyjnymi w ramach systemu sterowania procesami.
Budowa zautomatyzowanego systemu sterowania procesem jest niemożliwa bez wystarczająco dokładnego i szczegółowego opisu właściwości i cech kontrolowanego obiektu technologicznego (TO). Dlatego rozdział trzeci poświęcony jest przedstawieniu analitycznych i eksperymentalnych metod tworzenia modelu TO, który odzwierciedla wskazane właściwości i cechy.
Centralne miejsce w podręczniku zajmują rozdziały 4 i 5, poświęcone metodom analizy i syntezy algorytmów sterowania dla systemów sterowania procesami. Algorytmy sterowania przedstawiają planowane metody rozwiązywania zadań układu sterowania procesem stabilizacji i programowego sterowania parametrami i trybami utrzymania, co zapewnia przepływ procesów technicznych zgodnie z określonym kryterium optymalności. Szczególną uwagę zwraca się na rozważenie metod optymalizacji trybów pracy TO o charakterystyce liniowej i nieliniowej oraz tworzenie schematów blokowych algorytmów sterowania. Te ostatnie są podstawą tworzenia programów sterujących w procesie programowania sprzętu układów automatyki.
Rozdział szósty przedstawia etapy projektowania systemu sterowania procesem, począwszy od doboru niezbędnych środków technicznych do budowy systemu sterowania procesem, opracowania specyfikacji technicznych, a skończywszy na projekcie wykonawczym. Podsumowując, w rozdziale siódmym jako przykład omówiono zagadnienia systemów automatyki budynkowej w inżynierii mechanicznej opartych na CNC i programowalnych sterownikach logicznych.
PRZEDMOWA
WPROWADZENIE
Rozdział 1
1.1 Podstawowe pojęcia i definicje teorii sterowania automatycznego
1.1 Zasady regulacyjne
1.3 Algorytm (prawo) regulacji5
1.4 Podstawowe wymagania dla automatycznych systemów sterowania
2 Transmisje funkcji układu liniowego. Schematy blokowe i ich przekształcenia
3 Statyka układów automatyki
3.1 Charakterystyki statyczne elementów i połączeń ACS
3.2 Charakterystyki statyczne połączenia łączy
4 Pojęcie stabilności układów automatyki
Rozdział 2. CHARAKTERYSTYKI METROLOGICZNE POMIARÓW TECHNICZNYCH
2.1 Podstawowe pojęcia i definicje metrologiczne. Pojęcie pomiaru
2 Rodzaje przyrządów pomiarowych (SI)
3 Układy i jednostki wielkości fizycznych
4 Charakterystyki metrologiczne przyrządów pomiarowych. Stopniowanie i weryfikacja przyrządów pomiarowych
Rozdział 3. CZUJNIKI ELEKTRYCZNE MECHANICZNE
3.1 Enkodery liniowe i kątowe
2 czujniki siły
3 czujniki prędkości
Rozdział 4. METODY I NARZĘDZIA POMIARU GŁÓWNYCH PARAMETRÓW TECHNOLOGICZNYCH
4.1 Metody pomiarów elektrycznych
2 Metody i środki pomiaru temperatury
3 Metody i środki pomiaru poziomu
4 Metody i środki pomiaru ciśnienia
4.1 Metody bezpośredniego pomiaru ciśnienia
4.2 Metody pośrednich pomiarów ciśnienia
5 Metody i środki pomiaru przepływu
5.1 Mierniki ciśnienia zmiennego
5.2 Mierniki stałej różnicy ciśnień
5.3 Przepływomierze elektromagnetyczne
5.4 Przepływomierze ultradźwiękowe
5.5 Zmienne mierniki poziomu
5.6 Przepływomierze termiczne
5.7 Mierniki wirów
5.8 metrów Coriolisa
Rozdział 5. METODY I NARZĘDZIA POMIARU DRGAŃ
5.1 Metody pomiaru drgań
2 Przyrządy do pomiaru drgań
Rozdział 6
6.1 Pomiar właściwości fizycznych i chemicznych olejów i wód złożowych
1.1 Pomiar właściwości fizycznych i chemicznych oleju
1.2 Pomiar właściwości fizykochemicznych wody złożowej
2 Pomiar właściwości fizykochemicznych gazów
Rozdział 7. ELEMENTY PRZEKAŹNIKOWE
7.1 Przekaźniki elektromagnetyczne prądu stałego i przemiennego
1.1 Przekaźniki elektromagnetyczne stałe (neutralne)
1.2 Przekaźniki elektromagnetyczne AC
2 styki magnetyczne (kontaktrony)
Rozdział 8. PRZEKAZYWANIE INFORMACJI W SYSTEMACH AUTOMATYKI
8.1 Podstawowe informacje o systemach telemechaniki
2 interfejsy danych
Rozdział 9. MIKROPROCESORY
9.1 Podstawy mikroprocesora
2 Konwersja informacji analogowo-cyfrowych i cyfrowo-analogowych
WNIOSEK
LITERATURA
APLIKACJE
Załącznik 1. Materiały kontrolno-pomiarowe
Załącznik 2. Wykaz prac praktycznych i laboratoryjnych
Załącznik 3. Lista tematów do prac rozliczeniowych i graficznych (streszczenia)
Załącznik 4. Spis literatury podstawowej i dodatkowej
PRZEDMOWA
Podręcznik „Podstawy automatyzacji procesów technologicznych w wydobyciu ropy i gazu” zawiera systematyczną prezentację dyscypliny akademickiej o tej samej nazwie, w pełni odpowiada programowi nauczania i jest w istocie główną książką edukacyjną dotyczącą tej dyscypliny. Odzwierciedla podstawową wiedzę określoną przez jednostki dydaktyczne Federalnego Państwowego Standardu Edukacyjnego w kierunku 131000 „Biznes naftowy i gazowy”, specjalność „Obsługa i konserwacja instalacji do produkcji ropy naftowej”. Treść podręcznika szkoleniowego obejmuje opis metod pozyskiwania i wykorzystania wiedzy z zakresu automatyzacji procesów technologicznych, podstawy metodyczne podstawowych metod i schematów funkcjonowania przyrządów pomiarowych i systemów automatyki oraz rozwój dziedzin odzwierciedlenie w nich działalności, a także kluczowych problemów i głównych trendów rozwoju przemysłu naftowego i gazowniczego.
Celem podręcznika jest zapewnienie studentom pomocy metodycznej w tworzeniu niezbędnej wstępnej bazy wiedzy teoretycznej dla studentów na temat podstawowych zasad budowy systemów automatyki procesów produkcyjnych, a także technicznych środków automatyzacji, w oparciu o które te systemy są zbudowane. Studiując materiał edukacyjny student otrzyma informacje o podstawach automatyzacji procesów pomiarowych, rodzajach i metodach pomiaru, urządzeniu i cechach działania poszczególnych czujników głównych parametrów technologicznych, urządzeniach wtórnych i technologii mikroprocesorowej.
Zadaniem podręcznika jest umożliwienie studentom zapoznania się z urządzeniem oraz zasadą działania poszczególnych urządzeń i automatyki, a także niektórych zasad ich obsługi.
W trakcie studiowania materiału studenci powinni zapoznać się z podstawami i klasyfikacją metod i przyrządów pomiarowych; uzyskać jasne wyobrażenie o kompleksie technologicznym, o punktach odbioru sygnału parametrów procesu technologicznego; opanować schematy ideowe urządzeń, zasady działania czujników i przekaźników, możliwości techniczne urządzeń mikroprocesorowych i urządzeń automatyki, zasady konstruowania schematów blokowych, kryteria sterowania, perspektywy wprowadzenia komputerów w zabudowie i eksploatacji odwiertów , zasady prawidłowej technicznie eksploatacji urządzeń i urządzeń automatyki; nabyć umiejętności przeprowadzania analizy porównawczej sterowania i automatyki; poznaj zawiłości korzystania z narzędzi automatyzacji i perspektywy ich rozwoju.
W oparciu o zdobytą wiedzę teoretyczną studenci powinni nauczyć się wykonywać prace praktyczne i laboratoryjne, a następnie umieć montować proste urządzenia, rozszyfrowywać i analizować schematy rejestracji urządzeń, oceniać otrzymane informacje, dostosowywać tryby rozwoju i eksploatacji procesu wydobycia ropy i gazu systemy automatyki z wykorzystaniem specjalistycznego sprzętu.
WPROWADZENIE
Automatyzacja procesów technologicznych jest czynnikiem decydującym o zwiększeniu wydajności pracy i poprawie jakości produktów.
Procesy technologiczne nowoczesnych obiektów przemysłowych wymagają kontroli dużej liczby parametrów i są trudne w zarządzaniu. W związku z tym przy projektowaniu i eksploatacji instalacji przemysłowych szczególną wagę przywiązuje się do kwestii profesjonalizmu specjalistów pracujących w przedsiębiorstwach kompleksu paliwowo-energetycznego.
Przez lata rozwoju rafinacji ropy naftowej i przemysłu petrochemicznego doszło do komplikacji procesów, które wymagają bardziej precyzyjnego zarządzania. W pierwszej połowie XX wieku pojawiły się urządzenia do rejestracji i monitorowania parametrów, tzw. urządzenia kontrolno-pomiarowe - oprzyrządowanie. Pochodzenie, tworzenie i rozwój przyrządów pomiarowych i kontrolnych, proces od automatycznej kontroli do automatycznych systemów kontroli i zarządzania na poziomie makro i mikro jest integralną częścią procesów wydobycia ropy i gazu, rafinacji ropy naftowej i petrochemii.
Dalsze doskonalenie urządzeń do rejestracji, monitorowania i kontroli parametrów doprowadziło do automatyzacji i telemechanizacji rafinacji ropy naftowej i petrochemii. To ostatnie doprowadziło do komputeryzacji i sterowania procesami, czyli zautomatyzowanych systemów sterowania (ACS).
I oczywiście postęp w budowie przyrządów i aparatury w zautomatyzowanych systemach sterowania jest ciekawym zadaniem, którego rozwiązanie jest niezbędne do określenia dalszych perspektyw rozwoju w oparciu o przezwyciężenie globalnych problemów zarządzania w sektorze naftowo-gazowym.
Sformułowano sześć głównych współczesnych problemów zarządzania operacyjnego produkcją i automatyzacją w wydobyciu ropy i gazu:
Rozliczanie wydobycia, przemieszczania i wykorzystania węglowodorów, ropy naftowej, gazu, produktów naftowych, dla rozwiązania których ważne jest zapewnienie możliwości monitorowania operacji księgowych, w tym z obszarów koncesyjnych, a także zapewnienie audytów wewnętrznych i zewnętrznych księgowość olejowa, co z kolei wymaga opracowania odpowiednich przyrządów pomiarowych, a także oprogramowania i systemu informatycznego.
Zarządzanie majątkiem terytorialnym, organizacja konserwacji i naprawy sprzętu, zapewnienie bezpieczeństwa produkcji i personelu. Aby rozwiązać ten problem, konieczne jest opracowanie oprogramowania i narzędzi informatycznych zapewniających księgowość, planowanie konserwacji i napraw, monitorowanie stanu majątku produkcyjnego i wykonywanych prac; kontrola zawierania i realizacji umów z wykonawcami na wykonanie prac; kontrola obecności personelu w zakładach produkcyjnych; możliwość szkolenia personelu na miejscu na symulatorach; dostępność w miejscu pracy aktualnej dokumentacji dotyczącej użytkowania sprzętu, technologii wykonywania procedur i operacji.
Wysoki poziom zużycia energii produkcyjnej oraz konieczność oszczędzania energii i środków efektywności energetycznej. Do rozwiązania tego problemu potrzebne jest oprogramowanie i narzędzia informacyjne zapewniające księgowość, planowanie konserwacji i napraw, monitorowanie stanu zużycia energii przez elementy procesu technologicznego; identyfikacja obiektów energochłonnych z nadmiernym zużyciem energii elektrycznej; kontrola wdrażania środków oszczędzania energii.
Różnorodne narzędzia, systemy modelowania i informacyjne APCS. Problem ten wymaga opracowania oprogramowania i narzędzi informacyjnych, które zapewniają tworzenie szeregu informacji wstępnych o charakterze strategicznym (plany rozwoju i lokalizacji produkcji), średnioterminowym (plany roczne i miesięczne) oraz operacyjnym (plany dobowe i zmianowe) plany zarządzania; spełnienie wymagań dotyczących składu i struktury dokumentów zgodnie z wewnętrznymi regulacjami przedsiębiorstwa, wymagania standaryzacji wspólników; ujednolicenie dostępu i zróżnicowanie uprawnień podczas pracy z dokumentami.
Minimalizacja kosztów eksploatacji systemu przy maksymalnym poziomie obsługi informacyjnej decydentów. Do rozwiązania problemu wymagane jest: opracowanie metodyki wykonywania prac nad rozwojem poziomu MES, automatyzacja dotychczas niezautomatyzowanych zakładów produkcyjnych oraz oprogramowanie i narzędzia informacyjne zapewniające: utrzymanie aktualności baz danych i oprogramowanie systemowe w stanie roboczym; kontrola funkcjonowania oprogramowania systemu (o wymianie informacji z systemami systemów sterowania procesami, ERP itp.); ustalenie działań personelu zaangażowanego w obsługę systemu.
Wzrost funduszy i pracy przy wydobyciu każdej tony ropy, spowodowany stopniowym wyczerpywaniem się tanich pól naftowych Syberii Zachodniej, odkrytych pod koniec lat pięćdziesiątych. W rejonie roponośnym występują głównie złoża o trudnej produkcji, wymagające nowych rozwiązań technologicznych i dodatkowych inwestycji kapitałowych. Aby rozwiązać ten problem, konieczne jest zwiększenie efektywności inwestycji kapitałowych i ułatwienie zarządzania wydobyciem ropy; zwiększyć efektywność inwestycji kapitałowych i ułatwić zarządzanie wydobyciem ropy z podglebia poprzez podejście zwane „inteligentnymi polami”, „inteligentnymi polami”, „inteligentnymi polami naftowymi”, „inteligentnymi studniami”; zoptymalizować pracę wszystkich obiektów polowych: studni, zbiorników, rurociągów i innych obiektów naziemnych.
Rozdział 1
1Podstawowe pojęcia i definicje teorii sterowania automatycznego Wiadomo, że proces techniczny charakteryzuje się zestawem danych, wartości, wskaźników. Zestaw operacji do uruchomienia, zatrzymania procesu, utrzymania stałości wskaźników procesu lub zmiany ich zgodnie z danym prawem nazywamy kontrolą. Utrzymywanie wskaźników na danym poziomie lub zmienianie ich zgodnie z danym prawem nazywamy regulacją, czyli regulacja jest częścią zarządzania. A jeśli te procesy kontrolne są przeprowadzane bez udziału osoby (operatora), to nazywane są automatycznymi. Urządzenie realizujące proces technologiczny, którego wskaźniki muszą być sterowane lub regulowane, nazywane jest obiektem kontrolnym lub obiektem kontrolowanym. Obiektami sterującymi mogą być pompa wiertnicza, wiertnica, napęd wiertnicy itp. lub ich poszczególne jednostki, które wykonują określone operacje procesu technologicznego, np. wciągarka wiertnicy. Urządzenie techniczne, które steruje zgodnie z programem (algorytmem) nazywamy automatycznym urządzeniem sterującym. Połączenie obiektu sterującego i urządzenia sterującego nazywa się automatycznym systemem sterowania (ACS). Nie interesują nas wszystkie operacje automatycznego sterowania, a jedynie regulacja, czyli te operacje, które dotyczą utrzymania lub zmiany wskaźników procesu. Można przeprowadzić dowolny proces regulacyjny · bez kontroli wyników - kontrola w otwartej pętli; · z kontrolą wyniku - regulacja na cyklu zamkniętym. Przykładem sterowania w pętli otwartej bez kontroli wyniku (przepływu Q) jest stabilizacja dopływu płynu płuczącego Q przy pełnej wydajności pompy tłokowej przy załączonej odpowiedniej prędkości skrzyni biegów (niezmienna napęd i brak zrzutu płynu do płukania). Tutaj, przy znacznych (nieawaryjnych) zmianach w charakterystyce ścieżki hydraulicznej (z powodu szlamu w otworze dennym, wypadania kawałków skalnych ze ścian studni itp.), natężenie przepływu płynu płuczącego pozostaje stałe. W podanym przykładzie obiektem sterowania jest pompa wiertnicza z nieregulowanym napędem (agregat pompowy). Korpusem sterującym (regulacyjnym), który musi zawierać obiekt do sterowania dopływem płynu do płukania, jest skrzynia biegów. Regulacja w pętli otwartej jest stosowana znacznie rzadziej niż regulacja w pętli zamkniętej ze względu na niestabilność charakterystyk elementów. Elementy systemu podlegają różnego rodzaju perturbacji. W podanym przykładzie może to być zmiana współczynnika wypełnienia cylindrów pompy spowodowana zmianą parametrów płynu płuczącego lub przewodu ssącego. Rozważmy przykład sterowania w pętli zamkniętej z kontrolą wyniku - natężenie przepływu Q. Na rys. Rysunek 1.1 przedstawia schemat blokowy regulatora (stabilizatora) natężenia przepływu cieczy płuczącej Q. Tutaj natężenie przepływu Q jest kontrolowane przez czujnik przepływu DR. Wartość zadaną Z poprzez regulację napięcia U tyłek nastawione jest wymagane natężenie przepływu Q. Prędkość wału silnika n (a tym samym natężenie przepływu Q) jest określona przez obciążenie i napięcie U G , która zależy od wartości ∆U. ∆U = U tyłek - U ok1 , (1.1)
gdzie jesteś ok1 - napięcie na wyjściu czujnika (U d ) proporcjonalna do natężenia przepływu Q i nazywana jest napięciem sprzężenia zwrotnego. A ta zależność w tym przypadku jest ujemna (warunkowo wskazuje zacieniowanie sektora): zmniejsza wartość U tyłek . Gdy natężenie przepływu Q odbiega od ustawionej wartości, zmienia się również U ok1 , co prowadzi do zmiany n a tym samym do przywrócenia prędkości przepływu Q. Automatyczne utrzymywanie danego prawa zmian wskaźników procesu za pomocą sprzężenia zwrotnego nazywamy regulacją automatyczną. W rozważanym przykładzie jednym wskaźnikiem jest Q. Jest on nazywany zmienną kontrolowaną. Tak więc na podstawie rozważanego przykładu założymy, że automatyczne urządzenie, które wykonuje automatyczną regulację, nazywa się automatycznym regulatorem. Z kolei obiekt sterowany przez regulator nazywany jest obiektem regulowanym. Całość regulowanego obiektu i regulatora automatyki stanowią system automatycznego sterowania (ACS). Ze względu na cel funkcjonalny systemy automatyki dzielą się na systemy automatycznego sterowania w pętli otwartej, systemy sterowania automatycznego w pętli zamkniętej i systemy sterowania automatycznego. Rozważ przykłady pokazujące działanie rozważanych schematów. 1.Przykład. Elektroniczny stabilizator prądu żarnika. Schemat przedstawia sterowanie w pętli otwartej. Utrzymanie stałego prądu żarzenia I H następuje bez udziału operatora, tj. kontrola nie jest sprawowana. Przykład Ręczna kontrola prędkości ω wał silnika elektrycznego. Częstotliwość rotacji ω wał silnika napędowego D jest funkcją napięcia na zaciskach generatora U G , który przy stałej częstotliwości obrotu twornika ( ω VD = const) zależy od prądu w uzwojeniu wzbudzenia generatora. Aby regulować lub utrzymywać stałą prędkość ω operator monitoruje wskazania woltomierza V, skalibrowanego pod kątem prędkości obrotowej ω i ręczna zmiana prądu P reostatu I Owg w uzwojeniu wzbudzenia osiąga wymaganą wartość ω.
Tutaj obserwujemy zamknięty system regulacji. Ale taki ręczny system sterowania ma istotną wadę: niską dokładność sterowania i niepożądaną obecność operatora. Ponadto istnieje szereg zakłócających wpływów: zmienny moment na wale silnika M Z , zmiany temperatury otoczenia, zużycie szczotek maszyn elektrycznych itp., stąd niedokładność układu sterowania; system nie ma zastosowania do szybkich procesów. Rozważane przykłady stanowią podstawę do rozważenia kwestii zasad regulacyjnych. 1.1.1 Zasady regulacyjne W trakcie pracy omówionych powyżej systemów wpływ czynników zewnętrznych (zakłóceń) staje się oczywisty. Najprostszym rozwiązaniem uwzględniającym każde zakłócenie jest zainstalowanie odpowiedniego czujnika. Jednak takie podejście nie zawsze jest możliwe. Jako wyjście z tej sytuacji stosuje się zwykle metody, zgodnie z którymi najpierw mierzy się odchylenie od wartości zadanej wraz z zamontowaniem czujnika, a następnie wprowadza się poprawkę według odchyłki mierzonej (podobnie jak w przykładzie z zmiana położenia suwaka reostatu P). Istnieją następujące podstawowe zasady regulacji: · przez odchylenie; · z oburzenia; · odszkodowanie; · łączny. Na rysunku 1.4 przedstawiono schemat automatycznej regulacji (stabilizacji) prędkości obrotowej wału silnika z wykorzystaniem jednego czujnika monitorującego odchylenie prędkości od wartości zadanej, którym jest tachogenerator. Schemat ten w rzeczywistości jest przekształceniem schematu ręcznego sterowania (ryc. 1.3) w automatyczny schemat sterowania (ryc. 1.4). Tutaj operator zostaje zastąpiony elektrycznym systemem sterowania i systemem wpływania na reostat R. Reostaty R są wprowadzane do obwodu. 1 i R 2, odwracalny silnik RD, wzmacniacz elektroniczny EI i skrzynia biegów Red, która jest mechanicznie połączona z silnikiem z reostatem R. Rozważ główne elementy regulacyjne (ryc. 1.4): · obiekt regulacji, którym jest silnik, wszystkie pozostałe elementy wchodzą w skład regulatora układu; · wskaźnik procesu regulacji, jakim jest prędkość kątowa ω , tj. wartość regulowana, która może być zarówno stała, jak i zmienna zgodnie z dowolnym prawem; · regulator, którego rolę pełni łańcuch kotwicy silnika, poprzez zmianę położenia lub stanu można zmienić kontrolowaną wartość; · działanie regulacyjne - napięcie w obwodzie kotwicy silnika; · wartość nastawcza (wpływ) układu - U tyłek ; tj. jest to wartość proporcjonalna lub funkcjonalnie związana ze zmienną sterowaną i służy do zmiany poziomu tej ostatniej; przez ciebie tyłek ustawiona jest określona wartość ω.
Jeśli U = U tyłek - U os = 0, wtedy nadejdzie stan równowagi. U os jest napięciem sprzężenia zwrotnego, które jest proporcjonalne do kontrolowanej wartości ω. Kiedy to się zmieni ω ( ze względu na zmianę momentu M z rezystancji na wale silnika) napięcie sprzężenia zwrotnego U wytwarzane przez tachogenerator zmienia się os równowaga zostaje zachwiana (∆U ≠ 0), która prowadzi wzdłuż łańcucha (EU - RD - Red - R - I Owg ) do zmiany napięcia generowanego przez generator U G i przywrócić kontrolowaną wartość ω.
W rozważanym schemacie sterowanie wartością regulowaną odbywa się w sposób aktywny, a łańcuch transmisji sygnału od wyjścia do wejścia układu nazywany jest głównym sprzężeniem zwrotnym. Zasada regulacji, która jest włączona do schematu (ryc. 1.4), nazywana jest zasadą regulacji przez odchylenie. Systemy budowane zgodnie z tą zasadą zawsze zawierają informację zwrotną. Oznacza to, że działają w zamkniętej pętli. Pod pojęciem automatycznego układu regulacji przez odchylenie rozumiemy taki układ, w trakcie którego mierzy się odchylenie wielkości regulowanej od wartości zadanej i w funkcji wartości odchyłki powstaje określone działanie regulacyjne, które sprowadza to odchylenie do minimalna wartość. Zwróć uwagę i pamiętaj, że systemy kontroli odchyleń muszą zawsze zawierać główne negatywne sprzężenie zwrotne. Inną zasadą sterowania, znacznie rzadziej stosowaną w regulatorach automatycznych, jest zasada regulacji zakłóceniowej lub zasada kompensacji oraz kompensacja zakłóceń. Na ryc. 1.5 pokazuje obwód generatora prądu stałego. Ta ilustracja wyjaśnia zasadę kontroli zakłóceń. Tutaj generator pracuje dla zmiennego obciążenia R n . Napięcie U jest wartością regulowaną. Generator emf jest proporcjonalny do strumienia wzbudzenia Φ w mi G = k Φ w .
U = E - I n R a , (1.2)
E \u003d U + I n R a = I n R n + ja n R a = I n (R a + R n ) (1.3)
Załóżmy, że gdy obecny I n napięcie U = U o = const. Wtedy warunek E=U o + Δ E = U o + ja n R a = k ( Φ w + ΔΦ w ). (1.4)
Znaczy, Δ E zmieni się z powodu Φ w U o = k Φ w oraz ΔΦ w = (R a /k)I n = cI n , (1.5)
tych. zmiana zmiennej kontrolowanej ΔΦ musi być proporcjonalna do prądu obciążenia I n . Warunek ten jest spełniony dzięki uzwojeniu złożonemu, które daje dodatkowy strumień wzbudzenia Φ dodatkowy , proporcjonalny do obciążenia zakłóceniami - prąd I H . Na tej podstawie uzwojenie główne (główny strumień wzbudzenia Ф Główny ) ma na celu wytworzenie napięcia początkowego U O. Oznaczający Δ E jest określone przez uzwojenie złożone. Oba uzwojenia wytwarzają całkowity strumień magnetyczny Ф w. W wyniku zmiany prądu obciążenia I H całkowity przepływ Ф zmienia się w , a napięcie U o stale. Jest to przykład realizacji zasady kompensacji w regulacji, gdy podczas pomiaru obciążenia (zaburzenia) w funkcji wartości mierzonej powstaje pewne działanie regulacyjne, które pozwala na utrzymanie stałej wartości kontrolowanej. Systemy działające na tej zasadzie kompensacji to systemy z otwartą pętlą, które nie mają sprzężenia zwrotnego. Główną zaletą takich systemów jest szybkość. Jednak system ma również szereg wad: · ze względu na to, że obiekt posiada kilka oddziaływań zakłócających i dla układów kompensacyjnych konieczne jest zmierzenie każdego wpływu zakłócającego osobno i opracowanie w jego funkcji działania regulacyjnego, co znacznie komplikuje układ; · problem pomiaru zaburzeń nieelektrycznych; · niejednoznaczność i złożoność zależności regulatora od zakłócającego oddziaływania. Ze względu na te niedociągnięcia rozważane systemy są znacznie rzadziej stosowane w porównaniu z systemami realizującymi zasadę kontroli odchyleń. Trzecia zasada regulacji jest połączona (połączenie dwóch pierwszych zasad). Jest używany nawet rzadziej niż dwa pierwsze. Zalety i wady są takie same. Systemy są dość złożone, a ich analiza nie jest jeszcze dostępna. 1.2 Klasyfikacja automatycznych systemów sterowania Zgodnie z prawem reprodukcji (zmiany) wartości regulowanej, zamknięte układy regulacji dzielą się na trzy typy: · systemy stabilizacji, · systemy sterowania programem, · systemy śledzenia. Różnią się od siebie nie zasadniczo, ale tylko sposobem działania i konstruktywnym. Mają wspólną teorię i są badane tymi samymi metodami. System stabilizacji to system utrzymania stałości kontrolowanej wartości. Omówione powyżej systemy są związane z systemami stabilizacji. W programowanych układach sterowania regulowana wartość musi zmieniać się w czasie zgodnie z wcześniej znanym programem. system namierzający. Tutaj kontrolowana wartość zmienia się zgodnie z nieznanym arbitralnym prawem. Prawo jest określane przez pewien wpływ otoczenia zewnętrznego (arbitralnie). W zależności od charakteru wpływu regulacji na element wykonawczy, układy automatyki dzielą się na: · systemy ciągłe, · impuls i · sterowanie przekaźnikiem. W układach sterowania ciągłego sygnały na wyjściach wszystkich elementów układu są funkcjami ciągłymi sygnałów na wejściu elementów. Systemy sterowania impulsowego wyróżniają się tym, że w określonych odstępach czasu otwierają i zamykają pętlę sterowania za pomocą specjalnego urządzenia. Czas sterowania podzielony jest na impulsy, podczas których procesy przebiegają analogicznie jak w układach regulacji ciągłej, oraz na interwały, podczas których ustaje oddziaływanie regulatora na układ. Regulatory takie służą do sterowania procesami powolnymi (regulacja temperatury w piecach przemysłowych, temperatura i ciśnienie w kotłach). W przekaźnikowych układach sterowania pętla sterowania jest otwierana przez jeden z elementów systemu (element przekaźnikowy) w zależności od wpływu zewnętrznego. W zależności od wyników uzyskanych przy automatycznym sterowaniu rozróżnia się dwa rodzaje automatycznego sterowania: · statyczne i · astatyczny. Statyczne nazywa się taką automatyczną kontrolą, w której regulowana wartość, z różnymi stałymi wpływami zewnętrznymi na regulowany obiekt, przyjmuje różne wartości na końcu procesu przejściowego, w zależności od wielkości wpływu zewnętrznego (na przykład obciążenia ). Na ryc. 1.6 oraz przedstawiono regulator poziomu wody w zbiorniku. W regulatorze poziomu wody wraz ze wzrostem przepływu wody q poziom spada, zawór otwiera się przez pływak i dźwignię, dopływ q 1 wzrasta i na odwrót. System kontroli statycznej ma następujące charakterystyczne właściwości: równowaga układu jest możliwa przy różnych wartościach regulowanej zmiennej; każda wartość regulowanej zmiennej odpowiada jednej określonej pozycji korpusu regulacyjnego. Aby zrealizować takie połączenie czujnika z siłownikiem, pętla sterowania musi składać się z tzw. połączeń statycznych, w których w stanie równowagi wartość wyjściowa jednoznacznie zależy od wejścia: . Tłumaczy się to tym, że natężenie przepływu wody q jest równe dopływowi q1 na pewnym ściśle określonym, własnym poziomie H. Zmieni się natężenie przepływu, zmieni się poziom, dopływ będzie równy natężeniu przepływu - i równowaga przyjdzie ponownie. Regulator, który wykonuje regulację statyczną, nazywany jest regulatorem statycznym. Do scharakteryzowania stopnia zależności odchylenia zmiennej regulowanej od obciążenia w teorii regulacji stosuje się pojęcie nierównomierności, czyli opadu regulacji. Niech wykres zależności wartości ustalonych zmiennej sterowanej x od obciążenia q (charakterystyka kontrolna) ma postać pokazaną na ryc. 1.6, b (charakterystyka kontrolna podana jest w określonych współrzędnych dla poziomu wody regulatora w zbiorniku; poniżej współrzędne podane są w formie ogólnej, dla dowolnych regulatorów statycznych ). Maksymalna wartość regulowanej wartości xmax odpowiada biegu jałowym obiektu (bez obciążenia); wartość minimalna - obciążenie znamionowe - qnom. Do określenia spadku regulacji posługujemy się współrzędnymi względnymi: gdzie φ jest względną wartością kontrolowanej zmiennej; Sama kontrolowana wartość; Minimalna wartość regulowanej wartości (w trybie nominalnym); i qnom - podstawowe wartości wielkości; λ to względna wartość obciążenia. Wtedy niejednorodność δ (lub spadek) układu w ogólnym przypadku jest pochodną cząstkową w danym punkcie (lub względną stromością charakterystyki sterowania w tym punkcie): Jeżeli charakterystyka regulacji jest liniowa, to spadek będzie stały dla wszystkich wartości obciążenia. I można to zdefiniować tak: Regulator statyczny nie utrzymuje ściśle stałej wartości zmiennej sterowanej, ale z błędem, który nazywamy błędem statycznym systemu. Zatem spadek regulacji jest względnym błędem statycznym, gdy obciążenie zmienia się z jałowego na nominalne. W niektórych systemach błąd statyczny (nawet setne procenta) jest niepożądany, a następnie przejdź do regulacji, w której jest równy zero - do regulacji astatycznej. Charakterystykę regulacji takiego układu reprezentuje linia równoległa do osi obciążenia. Sterowanie astatyczne nazywa się sterowaniem automatycznym, w którym przy różnych stałych wartościach zewnętrznego wpływu na obiekt odchylenie wartości kontrolowanej od wartości zadanej na końcu procesu przejściowego staje się równe zeru. W astatycznym regulatorze poziomu wody H w zbiorniku (ryc. 1.7) pływak przesuwa suwak reostatu w jednym lub drugim kierunku, w zależności od zmiany poziomu od ustawionej wartości, zasilając w ten sposób silnik sterujący przepustnicą pozycja. Silnik wyłączy się, gdy poziom wody osiągnie ustawioną wartość. System sterowania astatycznego posiada następujące cechy charakterystyczne: równowaga układu zachodzi tylko przy jednej wartości zmiennej sterowanej równej danej; regulator ma możliwość zajmowania różnych pozycji przy tej samej wartości regulowanej zmiennej. W prawdziwych sterownikach pierwszy warunek jest spełniony z pewnym błędem. Aby spełnić drugi warunek, do pętli sterowania wprowadza się tzw. łącze astatyczne. W powyższym przykładzie silnik z tą właściwością, że przy braku napięcia jego wał jest nieruchomy w dowolnej pozycji, aw obecności napięcia stale się obraca. W zależności od źródła energii odbieranej przez regulator, istnieją: · bezpośrednie i · regulacja pośrednia. W systemach bezpośredniego sterowania energia potrzebna do regulacji elementu sterującego jest uzyskiwana z czujnika (na przykład statycznego regulatora poziomu wody). W układach sterowania pośredniego energia do poruszania elementem sterującym pozyskiwana jest z zewnętrznego źródła (przykładem jest astatyczny regulator poziomu wody). Układy sterowania automatycznego z kilkoma regulowanymi wartościami (np. ciśnienie pary w kotle, doprowadzenie wody do kotła, doprowadzenie paliwa i powietrza do paleniska) dzielą się na niesprzężone i sprzężone układy sterowania. Systemy regulacji niesprzężonej to takie, w których regulatory przeznaczone do regulacji różnych wielkości nie są ze sobą połączone i mogą współdziałać tylko poprzez wspólny dla nich przedmiot regulacji. Jeżeli w niesprzężonym układzie regulacji zmiana jednej ze zmiennych kontrolowanych pociąga za sobą zmianę innych zmiennych kontrolowanych, to taki układ nazywamy zależnym; a jeśli nie, to system nazywa się niezależnym. Sprzężone układy sterowania to takie, w których regulatory różnych sterowanych zmiennych są połączone ze sobą i dodatkowo z przedmiotem regulacji. Sprzężony układ sterowania nazywany jest autonomicznym, jeżeli powiązania między jego regulatorami składowymi są takie, że zmiana jednej ze zmiennych regulowanych w trakcie procesu regulacji nie powoduje zmiany pozostałych zmiennych regulowanych. Autonomiczne systemy sterowania z zamkniętą pętlą, które mają tylko jedno (główne) sprzężenie zwrotne, nazywane są pojedynczą pętlą. Automatyczne systemy sterowania, które oprócz jednego głównego sprzężenia zwrotnego mają jedno lub więcej głównych lub lokalnych sprzężeń zwrotnych, nazywane są wielopętlowymi. W zależności od rodzaju cech elementów składających się na systemy, wszystkie systemy dzielą się na: · liniowy i · nieliniowy. Systemy liniowe to systemy składające się wyłącznie z elementów o charakterystyce liniowej; procesy przejściowe w takich elementach opisane są liniowymi równaniami różniczkowymi. Systemy nieliniowe to takie, które mają jeden lub więcej elementów o nieliniowych charakterystykach; procesy przejściowe w takich układach są opisane nieliniowymi równaniami różniczkowymi. Po sklasyfikowaniu według rodzaju wykorzystywanej energii, wszystkie systemy można podzielić na: · elektryczny, · hydrauliczny, · pneumatyczny, · elektrohydrauliczny, · elektropneumatyczne itp. W zależności od liczby regulowanych wartości układu automatyki (ACS): jednowymiarowy,