Metody zapewniania jakości oprogramowania. Metody zapewniania jakości produktów są różne Nowoczesne metody zapewniania jakości
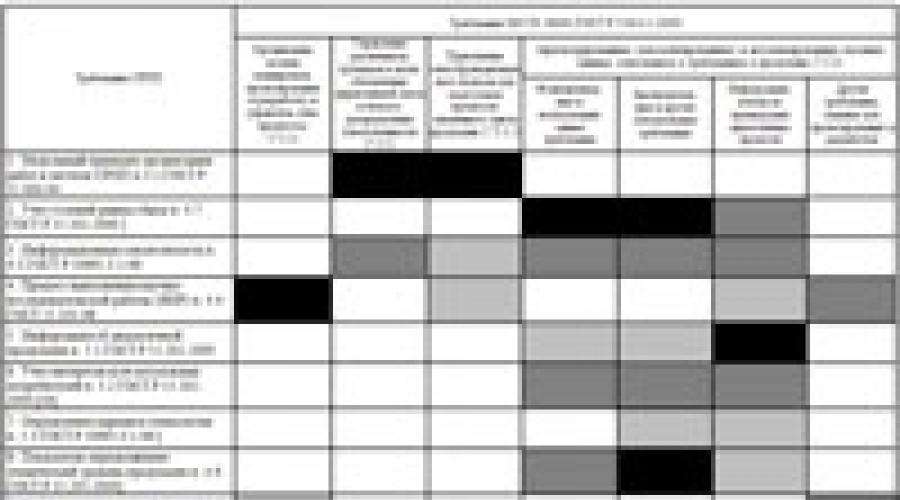
Przeczytaj także
W ostatnich latach przedsiębiorstwa maszynowe coraz częściej muszą tworzyć systemy zarządzania zgodne nie z podstawową normą ISO 9001, ale z ulepszonymi (zmodernizowanymi zgodnie z wymogami czasu i specyfiką danej branży) normami systemów zarządzania jakością. (na przykład normy Gazpromu, Kolei Rosyjskich itp.) P.).
Chociaż większość rosyjskich przedsiębiorstw już dawno wprowadziła i z powodzeniem funkcjonuje system rozwoju i uruchamiania produktów (SRPP), który jest zgodny z krajowymi standardami Federacji Rosyjskiej, obecnie wielu konsumentów wymaga od dostawców wdrożenia nowoczesnych systemów zarządzania jakością opartych na przemyśle- określone normy (na przykład norma międzynarodowa ISO / TU 16949, AS 9100 i podobne).
Przy wdrażaniu tych standardów konieczne jest powielenie wielu istniejących i istniejących w przedsiębiorstwie procedur, które wdrażają wymagania standardów SRPP. Nie ma wątpliwości, że prowadzi to do dodatkowego marnotrawstwa wszelkiego rodzaju zasobów.
Zadanie zmniejszenia czasu, zasobów ludzkich i finansowych na wdrożenie wymagań międzynarodowych standardów dotyczących metod i procedur zapewniania jakości z wykorzystaniem doświadczeń obecnych krajowych standardów Federacji Rosyjskiej jest dziś niezwykle pilne.
Pomimo pozornie oczywistych różnic w cechach produkcji budowlanej w przemyśle motoryzacyjnym i innych gałęziach inżynierii mechanicznej, wspólną cechą jest powszechne stosowanie dostaw komponentów do głównych zakładów montażowych przez stosunkowo małe przedsiębiorstwa.
Takie zasady organizacji produkcji są dobrze rozwinięte w prawie wszystkich zakładach samochodowych (zarówno krajowych, jak i zagranicznych), bez wyjątku są również wykorzystywane w inżynierii naftowej i gazowniczej - w zakładach produkujących złożone systemy technologiczne: platformy wiertnicze, kompleksy do zagospodarowania złóż offshore itp. Podobne przykłady można znaleźć również w innych branżach.
W związku z tym, że samochody są produktem o znacznie szerszym zapotrzebowaniu masowym, to właśnie w tej branży producenci musieli zwrócić szczególną uwagę na tworzenie takich systemów zarządzania jakością, które odpowiadałyby współczesnym zasadom organizacji produkcji, a ponadto mogłyby jednocześnie przyczyniają się do poprawy jakości produktu.... Ponadto przemysł motoryzacyjny ustanowił swój branżowy system standardów jakości znacznie wcześniej, niż zaistniała taka potrzeba w innych obszarach.
W tym kontekście niewątpliwym zainteresowaniem cieszą się prace w zakresie kształtowania systemu zarządzania jakością, które są obecnie prowadzone w przedsiębiorstwach motoryzacyjnych. Jest więcej niż prawdopodobne, że po uwzględnieniu drobnych korekt wyniki uzyskane na nich mogą znaleźć zastosowanie w dowolnych zakładach budowy maszyn.
Powszechnie wiadomo, że aby pokazać konsumentowi, w jaki sposób firma monitoruje jakość swoich produktów i zagwarantować tę jakość, producenci tworzą systemy zarządzania jakością spełniające wymagania ISO 9001, ISO / TU 16949, stosują opisane tam metody.
W Rosji istnieje obecnie tendencja do przechodzenia od norm krajowych do normy międzynarodowej ISO / TU 16949, która jest stosowana w przemyśle motoryzacyjnym i organizacjach produkujących odpowiednie części zamienne. W związku z tym, że ISO/TU 16949 została wydana jednocześnie z normą dotyczącą systemów zarządzania jakością, ma z tym ostatnim wiele wspólnego, ale ma też swoje własne cechy, gdyż ISO/TU 16949 zostało opracowane przez Międzynarodowy Przemysł Motoryzacyjny Task Force (IATF) i The Japan Automobile Manufacturers Association, zarejestrowana korporacja (JAMA) przy wsparciu Komitetu Technicznego ISO / TC 176, Zarządzanie jakością i zapewnienie jakości.
Główni producenci samochodów już certyfikują lub planują certyfikować swoje systemy zarządzania jakością zgodnie z międzynarodową normą ISO/TU 16949 i wymagają tego od swoich dostawców. Na przykład przedstawiciele „Wielkiej Trójki” – DaimlerChrysler, General Motors, Ford stawiają takie wymagania swoim dostawcom.
Należy zauważyć, że wdrożenie normy ISO/TS 16949 wymaga zastosowania specjalnych metod organizacji pracy – APQP (Zaawansowany Plan Planowania i Kontroli Jakości Produktu), PPAP (Proces Zatwierdzania Części Produkcyjnych) zatwierdzanie produkcji komponentów motoryzacyjnych ), a także wykorzystanie niektórych narzędzi zapewniania jakości wykorzystujących statystyczne metody analizy - FMEA (Metoda analizy potencjalnych przyczyn i skutków awarii), MSA (Measurement systems analysis - Analysis Measurement systems), SPC (Metody statystycznej kontroli procesów) oraz QSA (Analiza systemów zarządzania jakością).
Najpoważniejsze trudności w przedsiębiorstwach krajowych są spowodowane wprowadzeniem metody organizacji pracy APQP (Zaawansowane planowanie jakości produktu), w rzeczywistości - procesu planowania, rozwoju i przygotowania produkcji komponentów samochodowych, co pozwala zapewnić absolutnie wszystko wymagania i oczekiwania konsumenta już na etapie przygotowania produkcji, gdy istnieją podstawowe możliwości Zapobieganie defektom, Trudności pojawiają się z uwagi na fakt, że proces ten dotyczy prawie wszystkich działów i wszystkich procesów w organizacji i musi być realizowany na wszystkich etapach cykl życia produktu - od planowania stworzenia, projektowania i rozwoju komponentu motoryzacyjnego do jego seryjnej produkcji.
W Rosji funkcjonuje system podobny w przeznaczeniu do APQP – system rozwoju i wprowadzania produktów na rynek (SRPP).
Jak wiadomo, PPZP to zespół powiązanych ze sobą podstawowych norm organizacyjnych, metodologicznych i ogólnych stanów technicznych, które ustalają główne przepisy, zasady i wymagania zapewniające jedność techniczną i organizacyjną pracy wykonywanej na etapach cyklu życia produktu (LCP ), w tym badania i uzasadnienie rozwoju produktu lub projektu, w rzeczywistości rozwój, produkcja, eksploatacja (stosowanie, przechowywanie) produktów i naprawa (w przypadku produktów naprawionych), a także współdziałanie zainteresowanych stron.
SRPP jest powiązany z normami innych ogólnych systemów technicznych i zestawami norm: Zunifikowanym Systemem Dokumentacji Projektowej (ESKD), Zunifikowanym Systemem Dokumentacji Technologicznej (ESTD), Zunifikowanym Systemem Dokumentacji Oprogramowania (ESPD), Systemem Państwowym za zapewnienie jednolitości pomiarów i wsparcie technologiczne przy tworzeniu produktu.
Obecnie wielu specjalistów przedsiębiorstw jest zaniepokojonych następującym problemem - przedsiębiorstwa już wdrożyły i z powodzeniem obsługują system rozwoju i wprowadzania produktów zgodnie z krajowymi standardami Federacji Rosyjskiej. Nadchodzi jednak czas, kiedy konsument – pewien producent samochodów – żąda od swojego dostawcy wdrożenia systemu zarządzania jakością zgodnie z międzynarodową normą ISO/TU 16949, w tym oczywiście wprowadzenia metody APQP jako integralnej części taki system zarządzania jakością. Eksperci rozumieją, że muszą powielać wiele już trwających procesów, co wiąże się z dodatkowymi nieracjonalnymi kosztami.
Ta sytuacja jest żywo dyskutowana przez ekspertów, którzy się z nią zetknęli. To prawda, że w większości przypadków eksperci tylko spekulują, jak interesujące są wymagania organizacji międzynarodowych (międzynarodowej grupy zadaniowej przemysłu motoryzacyjnego (IATF)) z wymaganiami naszych starych, od dawna stosowanych norm krajowych, które zostały opracowane w lata osiemdziesiąte i dziewięćdziesiąte ubiegłego wieku.
Pojawia się więc problem – jak najniższym kosztem wdrożyć wymagania normy ISO/TU 16949, w tym wciąż dla nas egzotyczną metodę APQP, w przedsiębiorstwie z wdrożonym i funkcjonującym z powodzeniem SRPP.
Celem naszego badania było opracowanie algorytmu rozwoju międzynarodowych systemów zarządzania jakością w rosyjskich przedsiębiorstwach, biorąc pod uwagę specyfikę zgromadzonych dotychczasowych doświadczeń w funkcjonowaniu systemów krajowych i jednocześnie optymalizując koszty różnych zasobów: praca, finanse, czas itp.
Autor przeanalizował stopień zgodności wymagań normy ISO/TU 16949 oraz metody APQP z wymaganiami norm krajowych SRPP. W tym celu zbudowano macierze zgodności z wymaganiami powyższych dwóch systemów, w których 45 linii spełnia wymagania SRPP, a po 49 kolumn odpowiada wymaganiom ISO/TU 16949 i APQP. Każdy element przecięcia wierszy i kolumn został dodatkowo przeanalizowany przez połączenie metod oceny eksperckiej i analizy regresji.
Dla dokładniejszego zrozumienia, na czym polegał stopień uogólnienia wymagań, w jaki sposób wymagania metody APQP zostały podzielone na grupy oraz jakie wymagania z SRPP były brane pod uwagę pod kątem ich zgodności z wymaganiami procesu APQP, rozważymy niewielka część matrycy w bardziej powiększonej formie. Fragment matrycy przedstawiono w tabeli 2.
Tabela 2 - Fragment macierzy zgodności wymagań SRPP i ISO / TU 16949
W wyniku przeprowadzonej analizy okazało się, że w niektórych przypadkach istnieje zgodność (pełna lub częściowa) wymagań ISO/TU 16949 i APQP z wymaganiami SRPP i odwrotnie. W związku z tym przeprowadzono ponadto ilościową ocenę stopnia zgodności wymagań ISO / TU 16949 i metody APQP, która wykazała, że całkowitą zgodność wymagań stwierdzono w 15% przypadków, a częściową zgodność wymagań - w 13% przypadków. Ponadto zidentyfikowano sytuacje, w których wymagania mogą służyć jako podstawa do wdrożenia norm międzynarodowych: grupa wymagań ISO/TU 16949 i APQP nie pokrywa się bezpośrednio z wymaganiami SRPP, ale jeśli te ostatnie są w jakiś sposób uzupełnione, wtedy nastąpi pełny lub częściowy zbieg okoliczności... Takich sytuacji było około 22%. Wreszcie liczba przypadków z nieznacznym dopasowaniem wynosi 12%, aw 38% przypadków nie znaleziono żadnego dopasowania.
Na przykład klauzula 5.2 GOST R 15.201-2000 stanowi, co następuje: „Zaleca się uwzględnienie interesów wszystkich możliwych konsumentów w zakresie uprawnień”. Z kolei jako dane wejściowe w pierwszym etapie metody APQP konieczne jest posiadanie „informacji od konkretnych odbiorców”. Badanie wykazało, że wymagania całkowicie się pokrywały.
Inny przykład: w klauzuli 4.6 GOST R 15.201-2000 istnieje wymóg, aby projektant produktu, prowadząc prace badawcze, rozwojowe i technologiczne, zwracał szczególną uwagę na zapewnienie, w szczególności, wymagań dotyczących rozliczania wskaźników produktu, które określają to poziom techniczny. Proces APQP dotyczy benchmarków produktów/procesów konkurencji. W tym przypadku uznano, że wymagania się pokrywają. Podobnie sytuacja wygląda z takimi wymaganiami, jak obowiązkowy rozwój technologiczny produktów zgodnie z punktem 5.2.6 GOST R 50995.3.1-96 oraz potrzeba „założenia o produkcie i procesie” zgodnie z wymaganiami metody APQP.
Na podstawie wyników tych prac można wysnuć następujący wniosek – przy wdrożeniu ISO/TU 16949 i sposobu organizacji pracy APQP w przedsiębiorstwach z wdrożonym i pomyślnie funkcjonującym SRPP można znacznie obniżyć koszty zasobów.
Obniżenie kosztów można osiągnąć dzięki temu, że te elementy kontrolne procesu przedprodukcyjnego, które zostały już wdrożone w przedsiębiorstwie zgodnie z wymaganiami standardów SRPP, nie muszą być ponownie wdrażane, jeżeli są przewidziane we wniosku ISO/TU 16949 i APQP. Wystarczy wyjaśnić różnicę terminologiczną w dokumentacji przedsiębiorstwa. Wszyscy doskonale rozumiemy, że takie podejście może znacząco oszczędzić czas potrzebny na wdrożenie ISO/TU 16949 i metody APQP oraz ograniczyć zasoby ludzkie i materialne wymagane do wdrożenia.
Należy zauważyć, że przeprowadzono dość powierzchowną analizę obecnej sytuacji. W szczególności wymagania norm SRPP zostały podzielone tylko na 45 grup, wymagania ISO/TU 16949 oraz metodę APQP – na 49 grup, co chyba nie wystarcza do pełnej oceny zgodności wymagań ISO/ TU 16949 i APQP z wymaganiami norm SRPP; Należy również zauważyć, że do oceny zgodności wymagań zastosowano skalę tylko 5 kategorii, która również daje jedynie przybliżoną ocenę zgodności wymagań.
Należy również zauważyć, że w zależności od specyfiki przedsiębiorstwa i ogólnego kierunku jego działalności, procedura wdrażania różnych wymagań zarówno norm SRPP, jak i wymagań ISO/TU 16949 i APQP może być różna. Ale jednocześnie należy mieć na uwadze, że niektóre wymagania mogą być ze sobą powiązane i wtedy istnieje niepodważalna kolejność ich realizacji. Sytuację tę należy uwzględnić we wspólnym wdrażaniu norm SRPP i ISO/TU 16949.
Mając na uwadze powyższe opracowano schemat organizacji produkcji, który nazwaliśmy „modelem organizacyjnym” (rysunek 1). Model organizacyjny pozwala określić kolejność działań na etapie projektowania, rozwoju i wprowadzania produktów do produkcji oraz podczas wytwarzania produktów, identyfikować i lokalizować wąskie gardła, podejmować określone działania w celu ich wyeliminowania, rozdzielać odpowiedzialność i uprawnienia w obrębie obu jednostek odpowiedzialny za wydanie produktu oraz w całej organizacji.
Rysunek 1 – Model organizacyjny „Zarządzanie produkcją i usługami”
Opracowany model organizacyjny ma zastosowanie do każdego przedsiębiorstwa przemysłowego. Model organizacyjny może być wykorzystany do określenia kolejności realizacji i podziału pracy przy wprowadzaniu nowoczesnych metod zarządzania jakością w przedsiębiorstwie budowy maszyn, które posiada system zarządzania operacyjnego oparty na wdrożonych normach krajowego systemu SRPP.
W analizie nie uwzględniono również takiego czynnika, jak pewne nieścisłości i konwencje w tłumaczeniu tekstu opisującego metodę APQP. W takiej sytuacji uwzględnienie synonimów przy określaniu wymagań może być bardzo trudne – w końcu niektóre wymagania mogą się nawet całkowicie pokrywać, ale jednocześnie wyrażać się zupełnie innymi słowami.
Wyniki analizy pozwalają nam opracować konkretny algorytm realizacji wymagań międzynarodowych standardów, uwzględniający działający w przedsiębiorstwach system PSPP, który może znacząco skrócić czas, zasoby ludzkie i finansowe, a jednocześnie wykorzystać ogromny bagaż pozostawiony nam przez naszych poprzedników - radzieckich inżynierów - twórców norm krajowych. Algorytm ten zostanie opisany w kolejnej publikacji autora.
Natalia W. WASZCZENKO- Kierownik Działu Certyfikacji i Organizacji Pracy Centrum Koordynacji ANO „ATOMVOENCERT”
Lista wykorzystanych źródeł
1 Kudryaszow A.V. Okrągły stół. APQP: Problemy i doświadczenie wdrożeniowe // Metody zarządzania jakością. - 2012r. - nr 6.
2 Kershenbaum V.Ya., Vaschenko N.V. Metodyka oceny zgodności wymagań regulacyjnych praktyki krajowej i zagranicznej w zakresie budowy systemów zarządzania jakością // Zarządzanie jakością w kompleksie naftowo-gazowym. - 2013 r. - nr 1. - Z. 17 - 21.
3 Vaschenko N.V. O celowości udokumentowanej procedury w ramach realizacji wymagań siódmej sekcji normy ISO 9001: 2008 // Zarządzanie jakością w kompleksie naftowo-gazowym. - 2013 r. - nr 2. - Z. 14-18.
Liczne statystyki dotyczące jakości wskazują, że wadliwość produktów w około 85-90% jest spowodowana czynnikami ludzkimi. Zastanów się, jakie przyczyny związane z pracownikiem mogą mieć wpływ na niezgodność z dokumentacją techniczną, włącznie z wadliwymi produktami. Wśród nich można zauważyć: niskie kwalifikacje, krótki staż pracy, zły stan zdrowia, nieuwagę przy zapoznawaniu się z rysunkami, technologiami czy instrukcjami, kiepskie przygotowanie stanowiska pracy.
Należy podkreślić, że przyczyny zawarcia małżeństwa mogą być kojarzone nie tylko z osobą, ale także z narzędziem, sprzętem technologicznym, oprzyrządowaniem. To prawda, ale najczęściej dzieje się tak nie tyle z powodu wad samego narzędzia, wyposażenia czy samego oprzyrządowania, co w związku z ich niestarannym ostrzeniem, złymi naprawami lub niedokładnym wykonaniem i montażem wykonywanym przez pracowników. Jeśli „dojdziesz na dno” sprawcy wady, to w przeważającej większości będzie to osoba, która niekoniecznie pracuje w Twojej firmie, ale być może w firmie dostawcy.
Od czego zacząć poprawiać jakość? Japońscy eksperci radzą zacząć od jakości w miejscu pracy. Ponadto opracowali spójny system poprawy jakości w miejscu pracy, który nazywają „5S” (Dobra Praktyka Utrzymania Domu). Nazwa pochodzi od pięciu japońskich słów zaczynających się na literę „C”: seiri (sortowanie), seiso (czyszczenie), seiton (organizacja), seiketsu (standaryzacja), shitsuke (samotest). Rosyjskie tłumaczenie tych słów daje, jeśli nie do końca jasne, to całkiem wystarczające pojęcie o przybliżonej treści środków mających na celu poprawę jakości w miejscu pracy. Jeśli krótko opiszemy ten system, to możemy powiedzieć, że „przed rozpoczęciem pracy, a nawet odpowiedzialnej, musisz zrozumieć porządek w swoim miejscu pracy”.
Podajmy jaśniejszą treść każdego z etapów systemu „5S”. Przed przystąpieniem do jego realizacji należy szczegółowo opisać, a jeśli to możliwe, sfotografować obszar pracy (lub miejsce pracy), który wymaga reorganizacji. Porównanie opisów obszarów pracy (miejsc) przed i po transformacji może wywrzeć korzystny wpływ na kierownictwo, co aktywizuje pracę w przedsiębiorstwie na rzecz jakości.
Etap 1. Sortowanie. Umieść rzeczy (lub przedmioty) używane na co dzień w jednym miejscu. Przedmioty używane raz w tygodniu należy umieścić w innym miejscu, co miesiąc - w trzecim, a te bardzo rzadko potrzebne - w czwartym. Przeprowadź tę procedurę dla każdego obszaru miejsca pracy. Następnie z każdego miejsca przechowywania wybierz i zostaw po jednym egzemplarzu każdego rodzaju przedmiotu, a resztę przenieś do szafy na części zamienne.
Etap 2. Czyszczenie. Wyczyść wszystkie powierzchnie robocze przed ponownym umieszczeniem na nich czegokolwiek. Upewnij się, że w pobliżu miejsca pracy znajdują się odpowiednie pojemniki do zbierania odpadów. Umieść wszystkie części zamienne we wspólnym magazynie. Zrób listę artykułów zwróconych do magazynu, aby móc je zgłosić kierownictwu warsztatu. Uporządkuj i umieść wszystkie niezbędne dokumenty w jednym miejscu i wyczyść wszystkie narzędzia. Ustal standardy (normy) czystości, których musi przestrzegać każdy pracownik.
Etap 3. Organizacja. Ułóż starannie wszystkie dokumenty i foldery. Przedmioty używane na co dzień powinny być dla pracownika pod ręką. Przedmioty używane raz w tygodniu można ustawiać w odległości jednego kroku, a przedmioty używane raz w miesiącu w odległości 2-3 kroków. Cała reszta znajduje się kilka kroków od miejsca pracy. Niezbędne jest jasne określenie miejsca każdego przedmiotu.
Etap 4. Standaryzacja. Zapoznaj wszystkich pracowników związanych z tym miejscem pracy ze standardami czystości i zamieść zdjęcia „prawidłowego” ustawienia standardów. W stosownych przypadkach wyposażyć sprzęt i narzędzia w przezroczyste osłony przeciwpyłowe. Jeśli te osłony są nieprzezroczyste, pracownicy mogą przechowywać pod spodem przedmioty niestanowiące miejsca pracy.
Etap 5. Autotest. Po około miesiącu dokładnie zbadaj stan miejsca pracy, aby zobaczyć, czy można go poprawić. Jeśli znajdziesz dodatkowe przedmioty, wyślij je do magazynu ogólnego. Przejrzyj standardy czystości i zrewiduj je, jeśli to konieczne. Powtórz ten krok po miesiącu.
Możesz również polecić dodatkowe środki utrzymania porządku w miejscu pracy. Na przykład możesz tworzyć ruchome tablice z narzędziami do określonych zadań lub narysować kontury narzędzi na tablicach, aby od razu było jasne, którego narzędzia brakuje.
Japońscy badacze uważają, że jeśli menedżerowie firm nie mogą wdrożyć 5S, to nie mogą efektywnie zarządzać. I odwrotnie, jeśli potrafisz opanować system, oznacza to, że możesz równie skutecznie wdrażać inne, bardziej złożone systemy. Powodem takiego wniosku jest to, że system „5S” nie wymaga do jego wdrożenia żadnego specjalnego personelu menedżerów i nie będzie skuteczny, dopóki wszyscy pracownicy nie zaangażują się w niego i nie zaczną myśleć o sukcesie tego systemu. Ale jeśli system 5S został już wdrożony, to możemy założyć, że inne systemy są już prawie w połowie opanowane (pod względem gotowości personelu do wprowadzenia zmian).
Od połowy lat 80-tych. XX wiek w japońskich firmach system 5S był centralnym elementem myślenia i filozofii zarządzania. Kierownictwo firm doszło wszędzie do przekonania, że system ten jest kluczową metodą zarządzania w każdym, nawet najbardziej zaawansowanym technologicznie obszarze działalności.
W ostatnich latach system 5S stał się szeroko znany w rosyjskich przedsiębiorstwach. Z krajowej praktyki wprowadzania tego systemu można wyciągnąć następujące wnioski:
- - ma zastosowanie i może być z powodzeniem wdrażany w krajowych przedsiębiorstwach i organizacjach o różnych formach własności, jeśli kierownictwo jest tym zainteresowane;
- - treść zasad systemu i technologia jego realizacji wymagają znacznego dostosowania do specyfiki gospodarki krajowej, metod organizacji produkcji i mentalności personelu;
- - możliwość pomyślnego wdrożenia systemu zależy bezpośrednio od warunków społeczno-ekonomicznych pracy w miejscu pracy, tj. poziom i regularność wypłaty wynagrodzeń, systematyczne i rytmiczne obciążenie pracą produkcji, przestrzeganie przez administrację przynajmniej podstawowych wymagań dotyczących bezpiecznych warunków pracy.
Podjęto próby unowocześnienia tego systemu z uwzględnieniem zasad naukowej organizacji pracy i praktyki podnoszenia jakości. Nowy system, który zawierał elementy systemu „5S” i został dostosowany do krajowych warunków produkcji, otrzymał nazwę „Zamawianie” (tabela 2.4). Podstawowe zasady tego systemu są następujące:
- - usuń wszystkie niepotrzebne;
- - regularnie przeprowadzaj dokładne czyszczenie i sprawdzaj sprawność sprzętu i inwentaryzacji;
- - umieścić wszystko w miejscu pracy w najwygodniejszy sposób;
- - opracować standardy (zasady) przechowywania, użytkowania, czyszczenia i kontroli;
- - stale i świadomie przestrzegaj przyjętych zasad.
Tabela 2.4
Porównanie zasad działania systemów „5S” i „Zamawianie”
1. Udział całego zespołu. Tak jak nie da się „zagotować wody w jednym rogu basenu”, tak tego systemu nie da się skutecznie wdrożyć w jednym miejscu pracy czy w jednym dziale na polecenie jednej osoby. Nowy system wymaga determinacji i spójności całego zespołu.
Każda zasada systemu, którą trzeba spełnić, sama w sobie nie jest trudna. Trudność polega na tym, żeby nie przestać tego robić. Wymaga to wytrwałości i współpracy, co z kolei tworzy poczucie przynależności do zespołu i poprawia klimat korporacyjny.
2. Łatwość nauki - pozorny. Na pierwszy rzut oka zasady systemu „Sekwencjonowanie” wydają się jasne i łatwe do wdrożenia. Ale dlaczego tak trudno je wdrożyć?
Pozorna łatwość wdrożenia tych zasad wynika z faktu, że pracownicy nie do końca rozumieją, czym jest system „Zamawianie”. Nie jest to jednorazowe sprzątanie ogólne, nie przenoszenie narzędzia z miejsca na miejsce, ale całkowicie nowy styl podejścia do środowiska pracy, jego organizacji i bezpieczeństwa, styl ciągłego utrzymywania wysoce zorganizowanej, czystej przestrzeni roboczej.
3. Od poprawek po profilaktykę. Często można zaobserwować, ile czasu menedżerowie spędzają na naprawie tego, co zostało zrobione źle lub nie na czas. Reagują na kłopoty po fakcie. Kiedy jednak zapoznamy się z problemami, staje się jasne, że przyczyny wielu z nich są często bardzo proste.
Terminowo zauważone nieprawidłowości w działaniu sprzętu, stwierdzone awarie sprzętu lub inwentaryzacja mogą zapobiec dużym stratom i wypadkom. Nawet „drobiazgi” w niesprzyjających okolicznościach mogą przynieść duże kłopoty.
- 4. Z zarządzania wynikami - do kontroli procesu. Bardzo często menedżerowie widzą tylko efekty działań i oceniają efektywność swojej pracy. Wdrażając system „Zamawianie”, trzeba nauczyć się dostrzegać przyczyny prowadzące do pewnych rezultatów, widzieć cały proces jako całość, jego mocne i słabe strony.
- 5. Nacisk na spełnienie podstawowych wymagań. Personel musi przyzwyczaić się do ciągłego spełniania podstawowych wymagań. Na przykład sprawdzanie obecności wszystkich napisów i etykiet na ważnych przedmiotach lub przedmiotach.
- 6. Wzmocnienie odpowiedzialności każdego pracownika za wyniki swojej pracy. Pan Ford powiedział kiedyś, że „nawet najgłupszy pracownik może znaleźć sto sposobów na oszukanie najbardziej wykwalifikowanego brygadzisty”. Potwierdza to, że tylko czynnik osobistej odpowiedzialności pracownika i jego zainteresowania pracą może odgrywać dużą pozytywną rolę w produkcji, a nie ciągła regulacja pracy i ścisła kontrola. Potrzebna jest atmosfera, w której ludzie pomagają sobie nawzajem i wszyscy starają się dobrze wykonywać swoją pracę.
- 7. Zrozumienie instrukcji i przestrzeganie ich wymagań. Bardzo często instrukcje i wymagania nie są przestrzegane nie dlatego, że pracownicy je lekceważą, ale dlatego, że albo nie znają, albo nie do końca rozumieją istotę zawartych w nich wymagań lub zaleceń.
System „Zamawianie” umożliwia pracownikom samodzielne opracowywanie określonych zasad i instrukcji w odniesieniu do ich stanowisk pracy.
8. Stopniowe (krok po kroku) podejście. Oczywiście system „Usprawnianie”, nastawiony przede wszystkim na zmianę stereotypów behawioralnych pracowników, nie może zostać wdrożony szybko i od razu po rozpoczęciu jego wdrażania, a przyniesie wymierne efekty. Nowy system to pierwszy krok w kierunku długoterminowego programu naprawczego dla przedsiębiorstwa.
Technologia wdrażania systemu zakłada metodyczne, stopniowe, stopniowe opanowywanie jego zasad, ocenę i utrwalanie wyników każdego kroku.
9. System „Zamawianie» - to jest trudna droga. Nowy system, podobnie jak japońskie 5S, działa zgodnie z zasadą: „Czyny mówią głośniej niż słowa”. Każda wielka praca zaczyna się od małej rzeczy, od stopniowego zrozumienia istoty problemu, od błędów i poprawek. Nigdy nie należy odmawiać pomocy, porad, wsparcia od kolegów i personelu inżynierskiego. Prawdziwy postęp, stopniowy, nawet małymi krokami, jest o wiele bardziej przydatny niż globalne dyskusje o dużym projekcie, który może zmienić strukturę produkcji w danym miejscu pracy.
Omówione powyżej podejścia metodologiczne nie tyle odsłaniają treść i technologię realizacji zasad systemu „Zamawianie”, ale wyjaśniają przeszkody, trudności i trudności, jakie napotkamy na drodze wdrażania zarówno tego systemu, jak i „5S”. ” system.
Jeśli dla japońskiego pracownika pewność kierownictwa firmy, że wprowadzenie systemu 5S przyniesie ogromne korzyści nie tylko firmie, ale także samemu pracownikowi, wystarczy, aby długofalowa motywacja do wdrożenia elementów ten system jest realizowany w praktyce, to dla pracownika rosyjskiej firmy to wyraźnie za mało ... Potrzebne są skuteczne mechanizmy stymulujące poprawę miejsc pracy oraz poprawiające jakość produktów i pracy na każdym stanowisku pracy. Jak zawsze w rosyjskich przedsiębiorstwach wszystko, co dotyczy poprawy i racjonalizacji, łącznie z miejscami pracy, praktycznie opiera się nie na systemie, nie na skutecznych zachętach, ale wyłącznie na osobistej inicjatywie. Tak poważnej sprawy jak wdrożenie systemów 5S czy Streamlining nie można obwiniać wyłącznie entuzjastów fabryk.
Panuje opinia, że gdyby wszystkie prace można było wykonać „w nagłych wypadkach”, to Rosja nie miałaby tu konkurencji, a praca związana z codzienną żmudną pracą nad przywróceniem porządku i czystości nie odpowiada naszej mentalności. Stąd potrzeba gadatliwego wyjaśnienia za pomocą podejść metodologicznych, jak wykonać w gruncie rzeczy dość prostą pracę, czyli zasady systemu „Zamawiania”.
Jeśli chcemy żyć w cywilizowany sposób, jak na przykład w Japonii czy Europie, to nowi menedżerowie muszą inspirować pracowników, że jakość pracy nie zależy od mentalności narodu, ale od umiejętności i chęci spełniać wszystkie wymagania zapisane zarówno w specyfikacjach technicznych produktów, jak i w międzynarodowych normach ISO 9000. I nie tylko wpajać, ale także organizacyjnie i materialnie zapewnić wdrożenie niezbędnych norm.
W wyniku przestudiowania materiału z tego rozdziału student musi:
wiedzieć
- siedem narzędzi kontroli jakości produktów;
- statystyczne metody kontroli jakości produktów;
- funkcjonalna analiza kosztów;
- nowoczesne technologie zarządzania jakością (koncepcja sześciu sigma, metoda QFD itp.);
być w stanie
- zbudować przyczynowy diagram Ishikawy i diagram Pareto w celu zarządzania jakością towarów i usług;
- zastosować metodę QFD w celu śledzenia wymagań klientów na wszystkich etapach cyklu życia produktu;
- zastosować analizę funkcjonalną i kosztową w celu uzyskania niezbędnych właściwości konsumenckich produktu (usługi) przy minimalnych kosztach ich świadczenia;
własny
- umiejętności posługiwania się siedmioma narzędziami kontroli jakości towarów wprowadzanych do obrotu;
- statystyczne metody zarządzania jakością towarów wprowadzanych do obrotu.
Znaczenie i klasyfikacja metod
Jak wspomniano powyżej, w Ch. 2 jedną z zasad SM K jest to, że podstawą podejmowania decyzji powinny być same fakty, a nie intuicja. Jedną z przyczyn błędów zarządzania jakością jest mylenie faktów z subiektywnymi ocenami. Aby uniknąć błędów, należy uporządkować proces wyszukiwania faktów, tj. materiał statystyczny.
Statystyka matematyczna, która obejmuje ogromną liczbę różnych metod, zajmuje się gromadzeniem, przetwarzaniem i analizą wyników. Z tego zestawu wybrali japońscy naukowcy (głównie prof. K. Ishikawa) siedem podstawowych narzędzi kontroli jakości(rys. 4.1). Koła jakości odegrały ważną rolę w opanowaniu metod statystycznych w Japonii.
Ryż. 4.1.
Wraz ze wzrostem wielkości produkcji podczas seryjnej i masowej produkcji wyrobów konsument (jako osoba prawna) i sam producent potrzebowali informacji o rzeczywistej jakości wytwarzanych i kupowanych produktów. Jednak ze względu na dużą ilość produkowanych partii wyrobów trudno było przeprowadzić pełną kontrolę jakości, a jej niezawodność była niska. W celu zmniejszenia pracochłonności i zwiększenia niezawodności zaczęto stosować statystyczne metody kontroli jakości pobierania próbek. Ich znaczenie jest niezwykle proste: po zbadaniu niewielkiej części produktów (próbki) można wyciągnąć wiarygodne wnioski na temat jakości całej partii.
Na przełomie lat 70. i 80. XX wieku. Sojusz Japońskich Naukowców i Inżynierów opracował bardziej wyrafinowany zestaw narzędzi do kontroli jakości. Narzędzia te opierały się zarówno na metodach statystyki matematycznej, jak i na metodach innych nauk: analizy operacyjnej, teorii optymalizacji itp. Jako narzędzia bardziej subtelne, adresowane były do kadry inżynierskiej. Te metody są nazywane narzędzia zarządzania jakością. Ten samouczek obejmuje niektóre narzędzia zarządzania jakością: program „Sześć sit”, technologia wdrażania funkcji jakości, funkcjonalna analiza kosztów.
Poniżej opisano trzy grupy metod:
- 1) podstawowe narzędzia kontroli jakości;
- 2) statystyczne metody kontroli jakości pobierania próbek;
- 3) narzędzia zarządzania jakością.
Podstawowe narzędzia kontroli jakości
Głównymi narzędziami kontroli jakości są metody analizy statystycznej warunków i czynników wpływających na jakość produktu. Analiza statystyczna obejmuje analizę rodzajów i przyczyn małżeństwa, analizę wpływu poszczególnych czynników procesu technologicznego na wskaźniki jakości. W analizie zaleca się stosowanie specjalnych metod graficznych (czasem nazywanych statystyką opisową) do wizualizacji danych jakościowych. Metody te obejmują siedem narzędzi kontroli jakości (patrz Rysunek 4.1).
Lista kontrolna (arkusz)- narzędzie do zbierania i porządkowania danych w celu ułatwienia dalszego wykorzystania zebranych informacji.
Na ryc. 4.1 nie jest przypadkiem, że arkusz kontrolny znajduje się pośrodku, otoczony pozostałymi 6 instrumentami. Odgrywa szczególną rolę, ponieważ wykonanie każdego zadania analizy jakości zaczyna się od zebrania danych wyjściowych.
Lista kontrolna to papierowy formularz, na którym wstępnie drukowane są kontrolowane rodzaje defektów (w naszym przypadku na przykładzie defektów w zdobieniu wyrobów ceramicznych), zgodnie z którym częstotliwość ich występowania jest wskazywana w postaci prostych symboli.
Liczba różnych ulotek w przedsiębiorstwie liczona jest w setkach, a dla każdego konkretnego celu można w zasadzie opracować własną ulotkę. Ale zasada ich projektowania pozostaje niezmieniona: forma arkusza powinna być prosta i zrozumiała (bez dodatkowych wyjaśnień); konieczne jest wskazanie, kto zebrał dane, na jakim etapie i jak długo.
Oczywistym jest, że jakość produktu jest głównym wyznacznikiem działalności każdego przedsiębiorstwa. Do utrzymania konkurencyjności towarów i usług wykorzystuje się dziś rozwój różnych systemów zarządzania bezpieczeństwem żywności, głównie ekonomicznych i matematycznych. Na przykład programowanie dynamiczne, liniowe i nieliniowe, modelowanie symulacyjne, planowanie eksperymentów, teoria kolejek i teoria gier, funkcjonalna analiza wartości, metoda Taguchi i metoda strukturyzowania jakości.
Zostaw prośbę o bezpłatną konsultację
Wdrożenie funkcji jakości (QFD)). Jest to systematyczne podejście do identyfikacji wymagań klienta, które pomaga przedsiębiorstwu zrozumieć i zintegrować identyfikację wymagań z określonymi planami świadczenia usług. W przeciwieństwie do innych metod, QFD jest metodą zapewnienia jakości, która zakłada zaspokojenie potrzeb klienta w budowaniu matryc kręconych, zwanych później „domami jakości”, w ramach których rejestrowane są informacje o jakości usługi i podjętych decyzjach. Metoda ta to technologia projektowania produktów i procesów, która umożliwia przekształcenie życzeń konsumenta w wymagania techniczne dotyczące produktów i parametrów ich procesów produkcyjnych. Metoda QFD jest metodą ekspercką wykorzystującą tabelaryczny sposób prezentowania danych oraz ze specyficzną formą tabel, które nazywane są „domami jakości”. Główną ideą technologii QFD jest zrozumienie, że istnieje duża różnica między właściwościami konsumenta („rzeczywiste wskaźniki jakości”) a parametrami produktu określonymi w normach („pomocnicze wskaźniki jakości”). Dodatkowe miary jakości są ważne dla producenta, ale nie zawsze są niezbędne dla konsumenta. Idealnym przypadkiem byłoby, gdyby producent mógł kontrolować jakość produktów bezpośrednio z rzeczywistych wskaźników, ale z reguły jest to niemożliwe, więc używa wskaźników pomocniczych.
Technologia QFD to sekwencja działań producenta w celu przekształcenia rzeczywistych wskaźników jakości produktu w wymagania techniczne dla produktów, procesów i urządzeń. Głównym narzędziem technologii QFD jest specjalny stół zwany „domem jakości”. Poniższa tabela przedstawia relacje między rzeczywistymi wskaźnikami jakości (właściwości konsumentów) a wskaźnikami pomocniczymi (wymagania techniczne):
Zastosowanie metody QFD pozwala na uwzględnienie wymagań konsumenta na wszystkich etapach wytwarzania wyrobów gotowych, dla wszystkich elementów systemu jakości organizacji, a tym samym zwiększenie stopnia zadowolenia klienta, obniżenie kosztów procesów projektowych i przygotowanie produktów do produkcji.
Metoda FSA to technologia analizy kosztów produktu pełniącego swoje funkcje; FSA przeprowadza się dla istniejących produktów i procesów w celu obniżenia kosztów, a także dla produktów w fazie rozwoju w celu obniżenia ich kosztów. Metoda FSA jest aktywnie stosowana w przemyśle od lat 60-tych, głównie w Stanach Zjednoczonych. Jego zastosowanie umożliwiło obniżenie kosztów wielu rodzajów produktów bez obniżania ich jakości oraz optymalizację kosztów wytwarzania. FSA jest obecnie jednym z najpopularniejszych rodzajów analizy produktów i procesów. FSA jest jedną z metod analizy funkcjonalnej obiektów i systemów technicznych, do tej grupy metod zalicza się FFA (funkcjonalna analiza fizyczna) i FMEA. Przy przeprowadzaniu funkcjonalnej analizy kosztów określane są funkcje elementów obiektu technicznego lub systemu oraz oceniane są koszty realizacji tych funkcji w celu obniżenia tych kosztów. FSA obejmuje następujące główne etapy:
1. Konsekutywna budowa modeli obiektu FSA (komponentowego, konstrukcyjnego, funkcjonalnego); modele są zwykle budowane w formie tabelarycznej (macierzowej); 2. Badanie modeli i opracowanie propozycji udoskonalenia przedmiotu analizy.
Schemat Ishikawy(schemat przyczynowy, „szkielet ryby”) – narzędzie jakościowe służące do wizualizacji związków przyczynowo-skutkowych między przedmiotem analizy a czynnikami na niego wpływającymi.
Wpływ lub problem znajduje się na końcu poziomej strzałki, jak pokazano; możliwe przyczyny zostaną wyświetlone w postaci oznaczonych strzałek znajdujących się w strzałce głównej przyczyny. Każda strzałka może mieć inne strzałki, pokazujące podstawowe przyczyny lub czynniki w niej zawarte, których priorytet maleje wraz z odległością od strzałki głównej.

Analiza Pareto- może służyć do analizy pomysłów z sesji burzy mózgów. Służy do identyfikacji kilku istotnych problemów lub przyczyn tych problemów, które mają największy wpływ. Wykres Pareto przedstawia graficznie dane w postaci wykresu zbudowanego w porządku malejącym według częstotliwości występowania elementów. Zazwyczaj wykres Pareto pokazuje, że 80% wpływu jest wyjaśnione przez 20% przyczyn, stąd czasami nazywa się to regułą 80/20.
Statystyczna kontrola procesu (SPC)- to zestaw narzędzi do zarządzania procesami. Ponadto jest również strategicznym narzędziem zmniejszania zmienności produktów, dostaw materiałów, sprzętu, relacji i procesów, które są przyczyną większości problemów jakościowych. SPC pokaże, czy proces jest "pod kontrolą" - tj. czy jest stabilny tylko z przypadkowymi zmianami, czy też „poza kontrolą” i wymaga uwagi. Ponadto, SPC automatycznie ostrzega, gdy spada możliwość kontroli i może pomóc w długoterminowym zmniejszeniu wadliwości, identyfikacji szczególnych przyczyn, zmniejszeniu lub wyeliminowaniu przyczyn zmienności i osiągnięciu poziomów kontroli jak najbliżej celu. W SPC liczby i informacje stanowią podstawę decyzji i działań poprzez rygorystyczny system rejestrowania danych. Oprócz narzędzi potrzebnych do rejestrowania danych istnieje również zestaw narzędzi do analizy i interpretacji danych, z których część omówiono na kolejnych stronach. Zrozumienie narzędzi i sposobu ich używania nie wymaga wcześniejszej znajomości statystyk.
Karta kontrolna. Służy do monitorowania kontrolowanych procesów za pomocą wartości i zakresów. Lista kontrolna to dane chronologiczne, takie jak sprzedaż, wielkość, reklamacje klientów i pokazuje, jak wartości zmieniają się w czasie. Na wykresie kontrolnym każdemu punktowi odpowiada indywidualna wartość. Powyżej i poniżej średniej znajduje się górna i dolna linia ostrzegawcza oraz linie działania (UWL, LWL, UAL, LAL). Granice te pełnią rolę sygnałów i reguł podejmowania decyzji, a także dostarczają operatorom informacji o procesie i stanie jego kontroli. Mapa jest użyteczna jako historyczny opis procesu, jego przebiegu oraz jako narzędzie do identyfikacji i przewidywania zmian.