Metódy zabezpečenia kvality podľa. Metódy zabezpečenia kvality produktov sa líšia Moderné metódy zabezpečenia kvality
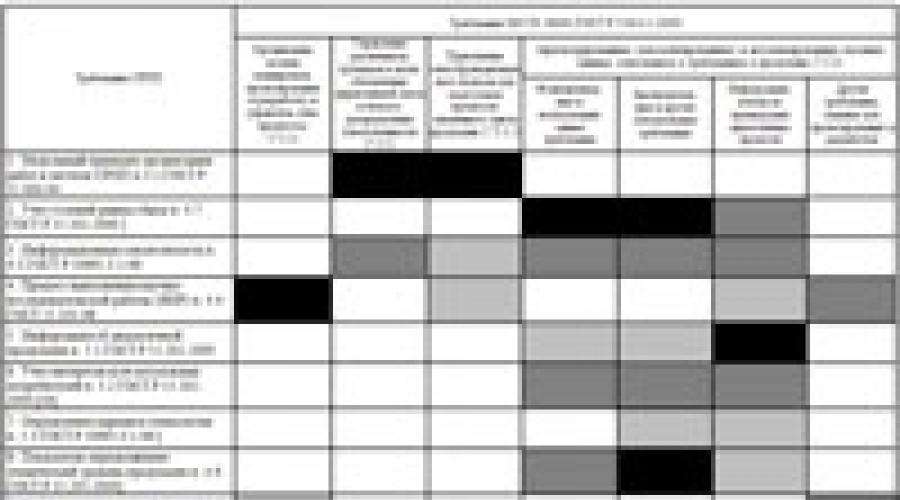
V strojárskych podnikoch v posledných rokoch narastá potreba vytvárať systémy manažérstva, ktoré nezodpovedajú základnej norme ISO 9001, ale zdokonaľujú sa (modernizujú v súlade s požiadavkami doby a špecifikami normy pre systémy manažérstva kvality (napríklad normy Gazpromu, Ruských železníc atď.).
Hoci väčšina ruských podnikov dlhodobo zaviedla a úspešne prevádzkuje systém vývoja a uvedenia výrobkov do výroby (SRPP), ktorý spĺňa národné normy Ruskej federácie, mnohí spotrebitelia dnes od dodávateľov vyžadujú implementáciu moderných systémov manažérstva kvality zameraných na normy, ktoré zohľadňovať špecifiká odvetvia (napríklad medzinárodnú normu ISO/TS 16949, AS 9100 a podobne).
Pri implementácii týchto noriem je potrebné duplikovať mnohé postupy už existujúce a fungujúce v podniku, ktoré implementujú požiadavky noriem SZVO. Niet pochýb o tom, že to vedie k dodatočným iracionálnym nákladom na všetky druhy zdrojov.
Úloha skrátiť čas, ľudské a finančné zdroje na implementáciu požiadaviek medzinárodných noriem na metódy a postupy zabezpečovania kvality s využitím skúseností z existujúcich národných noriem Ruskej federácie je dnes mimoriadne aktuálna.
Napriek zdanlivo zjavným rozdielom v špecifikách stavebnej výroby v automobilovom priemysle a v iných odvetviach strojárstva je spoločným znakom rozšírené využívanie dodávok komponentov do hlavných montážnych závodov relatívne malými podnikmi.
Takéto princípy organizácie výroby sú dobre vyvinuté takmer vo všetkých automobilových závodoch bez výnimky (domácich aj zahraničných), používajú sa aj v ropnom a plynárenskom inžinierstve - v závodoch, ktoré vyrábajú zložité technologické systémy: vrtné súpravy, komplexy na rozvoj pobrežných polí , atď. Podobné príklady možno nájsť aj v iných odvetviach.
Vzhľadom na to, že automobily sú produktom oveľa širšieho masového dopytu, práve v tomto odvetví museli výrobcovia venovať osobitnú pozornosť vytváraniu systémov manažérstva kvality, ktoré by mohli zodpovedať moderným princípom organizácie výroby a navyše mohli súčasne zlepšovať produkt. kvalita.. Automobilový priemysel navyše zaviedol svoj vlastný systém priemyselných noriem kvality oveľa skôr, ako to bolo potrebné v iných oblastiach.
Práve v tejto súvislosti je nepochybný záujem o prácu v oblasti formovania systému manažérstva kvality, ktorá sa v súčasnosti vykonáva v automobilových podnikoch. Je viac ako pravdepodobné, že s prihliadnutím na drobné úpravy sa výsledky na nich dosiahnuté dajú využiť v akýchkoľvek strojárskych závodoch.
Je dobre známe, že s cieľom ukázať spotrebiteľovi, ako spoločnosť sleduje kvalitu svojich výrobkov a garantuje túto kvalitu, výrobcovia vytvárajú systémy manažérstva kvality, ktoré spĺňajú požiadavky ISO 9001, ISO / TU 16949, aplikujú tam opísané metódy.
V Rusku je teraz trend prechodu od národných noriem k medzinárodnej norme ISO / TU 16949, ktorá sa uplatňuje v automobilovom priemysle a organizáciách, ktoré vyrábajú zodpovedajúce náhradné diely. Vzhľadom na to, že norma ISO/TS 16949 bola vydaná súčasne s normou pre systémy manažérstva kvality, má s ňou veľa spoločného, ale má aj svoje vlastné charakteristiky, keďže ISO/TS 16949 vyvinula Medzinárodná Pracovná skupina pre automobilový priemysel (IATF) a Japan Automobile Manufacturers Association registrované ako korporácia (JAMA) s podporou Technickej komisie ISO/TC 176 Riadenie kvality a zabezpečenie kvality.
Veľkí výrobcovia automobilov už certifikujú alebo plánujú certifikovať svoje systémy manažérstva kvality podľa normy ISO/TU 16949 a vyžadujú od svojich dodávateľov, aby tak urobili. Napríklad zástupcovia „veľkej trojky“ - DaimlerChrysler, General Motors, Ford predložili takéto požiadavky svojim dodávateľom.
Je potrebné poznamenať, že implementácia normy ISO / TS 16949 vyžaduje použitie špeciálnych metód organizácie práce - APQP (Advanced Product Quality Planning and Control Plan - Advanced Product Quality Planning and development of the management plan), PPAP (Production Part Approval). Proces - Proces koordinácie výroby dielu, t. j. schválenie výroby automobilových komponentov, ako aj použitie niektorých nástrojov na zabezpečenie kvality produktu pomocou štatistických metód analýzy - FMEA (metóda pre možný spôsob poruchy a analýza efektov - Metóda na analýzu typov a dôsledkov potenciálnych defektov), MSA (Analýza meracích systémov - Analýza meracích systémov), SPC (Metódy štatistického riadenia procesov - Metódy štatistického riadenia procesov) a QSA (Analýza systémov manažérstva kvality - Hodnotenie systémy manažérstva kvality).
Najzávažnejšími problémami v domácich podnikoch je zavedenie metódy organizácie práce APQP (Advanced Product Quality Planning), v skutočnosti proces plánovania, vývoja a prípravy výroby automobilových komponentov, čo umožňuje splniť absolútne všetky požiadavky. a očakávania spotrebiteľa už v predvýrobnej fáze, keď existujú základné možnosti Prevencia defektov Ťažkosti vznikajú v dôsledku skutočnosti, že tento proces sa dotýka takmer všetkých oddelení a všetkých procesov v organizácii a musí byť implementovaný vo všetkých fázach životný cyklus produktu – od plánovania vytvorenia, dizajnu a vývoja automobilového komponentu až po jeho sériovú výrobu.
V Rusku existuje systém podobný účelu ako APQP - systém vývoja a uvedenia produktov do výroby (SRPP).
Ako viete, SZVO je súbor vzájomne prepojených základných organizačných, metodických a všeobecných technických noriem štátu, ktoré stanovujú hlavné ustanovenia, pravidlá a požiadavky, ktoré zabezpečujú technickú a organizačnú jednotu vykonávanej práce v etapách životného cyklu produktu (LCP) , vrátane výskumu a zdôvodnenia vývoja produktov alebo projektu, v skutočnosti vývoja, výroby, prevádzky (aplikácie, skladovania) produktov a opravy (pre opravené produkty), ako aj interakcie zainteresovaných strán.
SZVO je prepojené s normami ďalších všeobecných technických systémov a súborov noriem: Jednotný systém projektovej dokumentácie (ESKD), Jednotný systém technologickej dokumentácie (ESTD), Jednotný systém programovej dokumentácie (ESPD), Štátny systém pre Zabezpečenie jednotnosti meraní, Technologická podpora tvorby produktov.
V súčasnosti sa veľa špecialistov podnikov obáva nasledujúceho problému - podniky už zaviedli a úspešne prevádzkujú systém vývoja a uvedenia výrobkov do výroby v súlade s národnými normami Ruskej federácie. No prichádza čas, kedy spotrebiteľ – určitá automobilka – požaduje od svojho dodávateľa zaviesť systém manažérstva kvality podľa medzinárodnej normy ISO/TU 16949, samozrejme vrátane implementácie metódy APQP ako integrálnej súčasti takéhoto Systém riadenia kvality. Špecialisti chápu, že musia duplikovať mnohé z už implementovaných procesov, čo je sprevádzané dodatočnými iracionálnymi nákladmi.
O tejto situácii aktívne diskutujú odborníci, ktorí sa s ňou stretli. Pravda, vo väčšine prípadov odborníci hovoria len o tom, aké zaujímavé sú požiadavky medzinárodných organizácií (medzinárodná pracovná skupina automobilového priemyslu (IATF) a požiadavky našich starých, dlho používaných národných noriem, ktoré boli vypracované ešte v osemdesiatych rokoch resp. deväťdesiatych rokov minulého storočia sa zhodujú.
Nastáva teda problém, ako čo najnižšie implementovať požiadavky normy ISO / TU 16949, vrátane pre nás stále exotického spôsobu organizácie práce APQP v podniku so zavedeným a úspešne fungujúcim SZVO.
Účelom našej štúdie bolo vyvinúť algoritmus na zvládnutie medzinárodných systémov manažérstva kvality v ruských podnikoch, berúc do úvahy špecifiká nahromadených predchádzajúcich skúseností s fungovaním domácich systémov a zároveň optimalizovať náklady na zdroje rôznych druhy: pracovné, finančné, časové atď.
Autor analyzoval mieru zlučiteľnosti požiadaviek normy ISO/TU 16949 a metódy APQP s požiadavkami národných noriem SZVO. Na tento účel boli zostavené matice súladu s požiadavkami vyššie uvedených dvoch systémov, v ktorých 45 riadkov spĺňa požiadavky SRPP a 49 stĺpcov spĺňa požiadavky ISO / TU 16949 a APQP. Každý prvok priesečníka riadkov a stĺpcov bol ďalej analyzovaný kombináciou expertného úsudku a metód regresnej analýzy.
Pre presnejšie pochopenie toho, aká bola miera zovšeobecnenia požiadaviek, ako boli požiadavky metódy APQP klasifikované do skupín a ktoré požiadavky zo SZVZ sa posudzovali z hľadiska ich kompatibility s požiadavkami procesu APQP, uvažujme malá časť matrice vo zväčšenej forme. Fragment matice je uvedený v tabuľke 2.
Tabuľka 2 - Fragment matice kompatibility požiadaviek SRPP a ISO / TU 16949
Výsledkom analýzy bolo zistenie, že v niektorých prípadoch existuje kompatibilita (úplná alebo čiastočná) požiadaviek ISO/TU 16949 a APQP s požiadavkami SOZPP a naopak. Preto sa ďalej uskutočnilo kvantitatívne posúdenie miery kompatibility požiadaviek ISO / TS 16949 a metódy APQP, ktoré ukázalo, že úplná zhoda požiadaviek bola zistená v 15 % prípadov a čiastočná zhoda požiadavky - v 13% prípadov. Okrem toho boli identifikované situácie, kedy požiadavky môžu slúžiť ako základ pre implementáciu medzinárodných noriem: skupina požiadaviek ISO/TU 16949 a APQP sa priamo nezhoduje s požiadavkami SOZVZ, ale ak sú tieto nejako doplnené , potom dôjde k úplnej alebo čiastočnej zhode okolností . Takýchto situácií bolo asi 22 %. Napokon, počet prípadov s menšou zhodou je 12 % a žiadna zhoda sa nenašla v 38 % prípadov.
Napríklad v bode 5.2 GOST R 15.201-2000 sa uvádza toto: „Odporúča sa, aby referenčné podmienky zohľadňovali záujmy všetkých možných spotrebiteľov.“ Na druhej strane, ako vstupné informácie v prvej fáze metódy APQP je potrebné mať „informácie od konkrétnych spotrebiteľov“. Počas štúdie sa zistilo, že existuje úplná zhoda požiadaviek.
Ďalší príklad: v článku 4.6 GOST R 15.201-2000 sa vyžaduje, aby vývojár produktu pri vykonávaní výskumných, vývojových a technologických prác venoval osobitnú pozornosť zabezpečeniu najmä požiadaviek na účtovanie ukazovateľov produktu, ktoré ho určujú. technickej úrovni. Proces APQP sa vzťahuje na referenčné hodnoty pre produkty/procesy konkurentov. V tomto prípade sa uznalo, že došlo k čiastočnému prekrývaniu požiadaviek. Situácia je podobná s takými požiadavkami, ako je povinný technologický vývoj produktov v súlade s článkom 5.2.6 GOST R 50995.3.1-96 a potreba „predpokladu o produktoch a procesoch“ v súlade s požiadavkami metódy APQP. .
Na základe výsledkov tejto práce možno vyvodiť nasledujúci záver - pri implementácii ISO / TU 16949 a metódy organizácie práce APQP v podnikoch s implementovaným a úspešne fungujúcim SZVZ je možné výrazne znížiť náklady na zdroje.
Zníženie nákladov je možné dosiahnuť tým, že tie prvky predvýrobného procesu riadenia, ktoré sú už v podniku zavedené v súlade s požiadavkami noriem SOZVZ, nie je potrebné opätovne implementovať, ak sú s nimi stanovené pri aplikácii ISO/TS 16949 a APQP. Bude stačiť objasniť rozdiel v terminológii v dokumentácii podniku. Všetci dobre vieme, že takýto prístup môže výrazne ušetriť čas na implementáciu ISO/TS 16949 a metódy APQP a znížiť ľudské a materiálne zdroje potrebné na implementáciu.
Treba poznamenať, že bola vykonaná dosť povrchná analýza súčasnej situácie. Najmä požiadavky noriem SZVO boli rozdelené len do 45 skupín, požiadavky ISO/TU 16949 a metóda APQP - do 49 skupín, čo pravdepodobne nestačí na úplné posúdenie kompatibility požiadaviek normy ISO/TU 16949. a APQP s požiadavkami noriem SZVO; Treba tiež poznamenať, že na posúdenie zlučiteľnosti požiadaviek bola použitá škála pozostávajúca len z 5 kategórií, ktorá tiež poskytuje len približné hodnotenie zlučiteľnosti požiadaviek.
Treba tiež poznamenať, že v závislosti od špecifík podniku a všeobecného smerovania jeho činností sa môže postup implementácie rôznych požiadaviek noriem SZVO a požiadaviek ISO / TU 16949 a APQP líšiť. Zároveň však treba mať na pamäti, že niektoré požiadavky môžu byť vzájomne prepojené a potom existuje nepopierateľný príkaz na ich realizáciu. Táto situácia musí byť zohľadnená pri spoločnej implementácii SZVO a noriem ISO/TU 16949.
Vzhľadom na vyššie uvedené bola vyvinutá schéma organizácie výroby, ktorú sme nazvali „organizačný model“ (obrázok 1). Organizačný model vám umožňuje určiť postupnosť akcií vo fáze návrhu, vývoja a uvedenia produktov do výroby a pri výrobe produktov, identifikovať a lokalizovať úzke miesta, prijať konkrétne opatrenia na ich odstránenie, prideliť zodpovednosť a právomoci v rámci oboch jednotiek. zodpovedný za výrobu produktov a v celej organizácii.
Obrázok 1 - Organizačný model "Riadenie výroby a služieb"
Vyvinutý organizačný model je použiteľný pre akýkoľvek priemyselný podnik. Organizačný model je možné použiť na určenie poradia implementácie a rozloženia práce pri zavádzaní moderných metód riadenia kvality v strojárskom podniku, ktorý má prevádzkový systém riadenia založený na implementovaných štandardoch národného systému SZVO.
Analýza nezohľadnila ani taký faktor, akým sú niektoré nepresnosti a konvencie v preklade textu opisujúceho metódu APQP. V takejto situácii môže byť veľmi ťažké brať do úvahy synonymá pri predkladaní požiadaviek - niektoré požiadavky sa totiž môžu dokonca úplne zhodovať, no zároveň byť vyjadrené úplne inými slovami.
Výsledky analýzy umožňujú vyvinúť špecifický algoritmus na implementáciu požiadaviek medzinárodných noriem s prihliadnutím na systém SZVO fungujúci v podnikoch, ktorý môže výrazne znížiť čas, ľudské a finančné zdroje a zároveň využiť obrovská batožina, ktorú nám zanechali naši predchodcovia – sovietski inžinieri – vývojári národných noriem. Tento algoritmus bude popísaný v ďalšej publikácii autora.
Natália Viktorovna VASHCHENKO— vedúci oddelenia certifikácie a organizácie práce koordinačného centra ANO „ATOMVOENSERT“
Zoznam použitých zdrojov
1 Kudryashov A.V. Okrúhly stôl. APQP: problémy a skúsenosti s implementáciou // Metódy manažérstva kvality. - 2012. - č.6.
2 Kershenbaum V.Ya., Vashchenko N.V. Metodika posudzovania zlučiteľnosti regulačných požiadaviek domácej a zahraničnej praxe pri budovaní systémov manažérstva kvality // Manažérstvo kvality v ropnom a plynárenskom komplexe. - 2013. - č. 1. - S. 17 - 21.
3 Vashchenko N.V. O realizovateľnosti zdokumentovaného postupu v rámci implementácie požiadaviek siedmeho oddielu ISO 9001:2008 // Manažérstvo kvality v ropnom a plynárenskom komplexe. - 2013. - č.2. - S. 14 - 18.
Početné štatistiky kvality uvádzajú, že závadnosť produktov je približne z 85 – 90 % spôsobená ľudským faktorom. Uvažujme, aké dôvody súvisiace s pracovníkom môžu ovplyvniť nesúlad s technickou dokumentáciou až po manželstvo výrobkov. Medzi nimi možno poznamenať: nízku kvalifikáciu, krátke pracovné skúsenosti, zlý zdravotný stav, nepozornosť pri čítaní výkresov, technológií alebo pokynov, zlú prípravu pracoviska.
Je potrebné zdôrazniť, že príčiny manželstva môžu byť spojené nielen s osobou, ale aj s nástrojom, technologickým vybavením, vybavením. To je pravda, ale najčastejšie sa to nedeje ani tak v dôsledku nedostatkov samotného náradia, vybavenia alebo vybavenia, ale v dôsledku ich neopatrného zaostrenia, zlých opráv alebo nepresnej výroby a montáže vykonanej pracovníkmi. Ak sa „rýpete“ do vinníka závady, tak to bude v drvivej väčšine človek, ktorý nemusí pracovať u vás, ale prípadne aj u dodávateľa.
Kde by malo začať zlepšovanie kvality? Japonskí odborníci radia začať s kvalitou na pracovisku. Okrem toho vyvinuli koherentný systém zlepšovania kvality na pracovisku, ktorý nazvali „5S“ („Dobré postupy v domácnosti“). Názov pochádza z piatich japonských slov začínajúcich na písmeno „S“: „seiri“ (triedenie), „seiso“ (čistenie), „seiton“ (organizácia), „seiketsu“ (štandardizácia), „shitsuke“ (samovyšetrenie). ). Ruský preklad týchto slov dáva, ak nie celkom jasnú, tak celkom dostatočnú predstavu o približnom obsahu opatrení na zlepšenie kvality na pracovisku. Ak stručne charakterizujeme tento systém, môžeme povedať, že „pred nástupom do práce, a to aj zodpovednej, je potrebné riešiť poriadok na vašom pracovisku“.
Uveďme si jasnejší obsah každej z etáp systému „5S“. Predtým, ako sa pristúpi k jeho realizácii, je potrebné podrobne popísať a ak je to možné, odfotografovať pracovnú oblasť (alebo pracovisko), ktorú je potrebné reorganizovať. Porovnanie popisov pracovných oblastí (miest) pred a po transformácii môže poskytnúť manažmentu priaznivý dojem, ktorý aktivuje kvalitnú prácu v podniku.
Fáza 1. Triedenie. Umiestnite veci (alebo predmety), ktoré sa používajú denne, na jedno miesto. Položky používané raz týždenne by mali byť umiestnené na inom mieste, mesačne - na treťom a čo je potrebné veľmi zriedkavo - na štvrtom. Vykonajte tento postup pre každú zónu pracoviska. Potom z každého skladovacieho miesta vyberte a ponechajte jednu kópiu každého typu položky a zvyšok preneste do skrine na uskladnenie náhradných dielov.
Fáza 2. Čistenie. Vyčistite všetky pracovné povrchy predtým, ako na ne niečo znova položíte. Uistite sa, že v blízkosti pracoviska sú vhodné nádoby na odpad. Všetky náhradné diely umiestnite do všeobecného skladu. Vytvorte zoznam položiek vrátených do skladu, aby ste ich mohli nahlásiť vedeniu dielne. Zorganizujte a uložte na jedno miesto všetky potrebné dokumenty a vyčistite všetky nástroje. Stanovte štandardy (normy) čistoty, ktoré musí dodržiavať každý zamestnanec.
Fáza 3. Organizácia. Usporiadajte si všetky papiere a priečinky prehľadne. Položky, ktoré sa používajú denne, by mali mať pracovník na dosah ruky. Položky používané raz týždenne môžu byť umiestnené vo vzdialenosti jedného kroku a položky používané raz za mesiac - vo vzdialenosti 2-3 krokov. Všetko ostatné je možné umiestniť na pár krokov od pracoviska. Je potrebné jasne definovať miesto každej položky.
Etapa 4. Štandardizácia. Oboznámte všetkých zamestnancov spojených s týmto pracoviskom so štandardmi čistoty a uverejňujte fotografie so „správnym“ štandardným prostredím. V prípade potreby zabezpečte vybavenie a nástroje priehľadnými prachotesnými krytmi. Ak sú takéto kryty nepriehľadné, pracovníci pod nimi budú pravdepodobne skladovať predmety, ktoré nesúvisia s pracoviskom.
Fáza 5. Samotest. Asi po mesiaci starostlivo skontrolujte stav pracoviska, aby ste ho zlepšili. Ak existujú ďalšie položky - odošlite ich do všeobecného skladu. Skontrolujte štandardy čistoty a v prípade potreby ich upravte. Opakujte tento krok po mesiaci.
Môžete odporučiť aj ďalšie opatrenia na udržanie poriadku na pracovisku. Môžete tak napríklad vytvárať pohyblivé dosky s náradím na konkrétne práce, alebo si na dosky kresliť obrysy náradia, aby bolo hneď jasné, ktorý nástroj chýba.
Japonskí vedci sa domnievajú, že ak manažéri spoločnosti nedokážu implementovať „5S“, potom nedokážu efektívne riadiť. A naopak, ak si tento systém osvojíte, znamená to, že rovnako úspešne dokážete implementovať aj iné, zložitejšie systémy. Dôvodom tohto záveru je, že systém 5S si na svoju implementáciu nevyžaduje žiadnych špeciálnych pracovníkov manažérov a nadobudne účinnosť až vtedy, keď sa doň zapoja všetci pracovníci a nezačnú uvažovať o úspechu tohto systému. Ale ak je systém 5S už implementovaný, potom môžeme predpokladať, že ostatné systémy sú takmer z polovice asimilované (z hľadiska pripravenosti personálu na implementáciu zmien).
Od polovice 80-tych rokov. 20. storočie v japonských firmách bol systém 5S ústredným prvkom myslenia a filozofie manažmentu. Manažment spoločností všade dospel k záveru, že tento systém je kľúčovou metódou riadenia v akejkoľvek, aj tej najmodernejšej oblasti činnosti.
Systém 5S si v posledných rokoch získal veľkú popularitu v ruských podnikoch. Z domácej praxe implementácie tohto systému možno vyvodiť tieto závery:
- - je aplikovateľný a úspešne realizovateľný v domácich podnikoch a organizáciách rôznych foriem vlastníctva so záujmom manažmentu o to;
- - obsah zásad systému a technológia jeho implementácie si vyžadujú výrazné prispôsobenie osobitostiam domácej ekonomiky, metódam organizácie výroby a mentalite personálu;
- - možnosť úspešnej implementácie systému priamo závisí od sociálno-ekonomických pracovných podmienok na pracovisku, t.j. úroveň a pravidelnosť vyplácania miezd, systematické a rytmické zaťažovanie výroby, dodržiavanie aspoň základných požiadaviek na bezpečné pracovné podmienky zo strany správy.
Uskutočnili sa pokusy o modernizáciu tohto systému, berúc do úvahy princípy vedeckej organizácie práce a prax zvyšovania kvality. Nový systém, ktorý obsahoval prvky systému „5S“ a prispôsobil sa domácim výrobným podmienkam, sa nazýval „Objednávanie“ (tabuľka 2.4). Hlavné princípy tohto systému sú nasledovné:
- - odstráňte všetky nepotrebné;
- - pravidelne vykonávať dôkladné čistenie a kontrolu prevádzkyschopnosti zariadení a inventára;
- - umiestniť všetko na pracovisku čo najpohodlnejším spôsobom;
- - vypracovať normy (pravidlá) pre skladovanie, používanie, čistenie a kontrolu;
- - neustále a vedome dodržiavať prijaté pravidlá.
Tabuľka 2.4
Porovnanie princípov systémov „5S“ a „Objednávka“.
1. Účasť celého tímu. Tak ako nie je možné „variť vodu v jednom rohu bazéna“, tak ani tento systém nie je možné efektívne zaviesť na jednom pracovisku alebo v jednej jednotke podľa vôle jednej osoby. Nový systém si vyžaduje rozhodnosť a súdržnosť konania celého tímu.
Každé pravidlo systému, ktoré je potrebné vykonať, nie je samo o sebe ťažké. Problém spočíva v tom, že sa nezastaví jeho implementácia. Vyžaduje si to vytrvalosť a spoluprácu, čo zase vytvára pocit spolupatričnosti k tímu a zlepšuje firemnú klímu.
2. Jednoduchosť vývoja - zjavný. Princípy systému „Objednávka“ sa na prvý pohľad zdajú také jasné a ľahko realizovateľné. Prečo je však také ťažké ich implementovať?
Zjavná jednoduchosť implementácie týchto princípov je spôsobená skutočnosťou, že zamestnanci úplne nerozumejú tomu, čo je systém „Objednávka“. Nejde o jednorazové generálne upratovanie, nepresúvanie nástrojov z jedného miesta na druhé, ale o zásadne nový štýl prístupu k pracovnému prostrediu, jeho organizácii a bezpečnosti, štýl neustáleho udržiavania vysoko organizovaného, čistého pracovného priestoru.
3. Od nápravy po prevenciu.Často môžete vidieť, koľko času manažéri strávia opravou toho, čo bolo urobené nesprávne alebo nečas. Na nepriazeň osudu reagujú až dodatočne. Ale keď spoznáme problémy, je jasné, že príčiny mnohých z nich sú často veľmi jednoduché veci.
Včas zaznamenané porušenia v prevádzke zariadení, zistené poruchy zariadení alebo inventára môžu zabrániť veľkým stratám a nehodám. Aj niektoré „maličkosti“ za nepriaznivých okolností môžu priniesť veľké problémy.
- 4. Z manažmentu založeného na výsledkoch - na kontrolu procesu. Veľmi často majú manažéri tendenciu vidieť len výsledky činností a posudzovať efektivitu svojej práce. Pri zavádzaní systému „Objednávka“ je potrebné naučiť sa vidieť dôvody vedúce k určitým výsledkom, vidieť celý proces ako celok, jeho silné a slabé stránky.
- 5. Dôraz na splnenie základných požiadaviek. Personál si musí zvyknúť na neustále plnenie elementárnych požiadaviek. Napríklad kontrola prítomnosti všetkých nápisov a štítkov na dôležitých predmetoch alebo predmetoch.
- 6. Posilnenie zodpovednosti každého zamestnanca za výsledky jeho práce. G. Ford raz povedal, že „aj ten najhlúpejší robotník dokáže nájsť sto spôsobov, ako oklamať najšikovnejšieho remeselníka“. To potvrdzuje, že veľkú pozitívnu úlohu vo výrobe môže zohrať len faktor osobnej zodpovednosti pracovníka a jeho záujem o prácu, a nie neustála regulácia práce a prísna kontrola. Potrebujeme atmosféru, kde si ľudia navzájom pomáhajú a každý sa snaží robiť dobrú prácu.
- 7. Pochopenie pokynov a dodržiavanie ich požiadaviek. Veľmi často sa pokyny a požiadavky nedodržiavajú nie preto, že ich zamestnanci zanedbávajú, ale preto, že buď nepoznajú, alebo úplne nerozumejú podstate požiadaviek alebo odporúčaní v nich obsiahnutých.
Objednávkový systém umožňuje zamestnancom samostatne vypracovať špecifické pravidlá a pokyny vo vzťahu k ich pracoviskám.
8. Postupný (krok za krokom) prístup. Je zrejmé, že systém „Objednávka“, ktorý je primárne zameraný na zmenu stereotypov správania zamestnancov, nie je možné zaviesť rýchlo a hneď po začatí jeho implementácie priniesť hmatateľné výsledky. Nový systém je prvým krokom k dlhodobému programu obnovy podniku.
Technológia implementácie systému zahŕňa metodické, postupné, krokové osvojenie si jeho princípov, vyhodnotenie a konsolidáciu výsledkov každého kroku.
9. Systém "Objednávka» - je to náročná cesta. Nový systém, podobne ako japonský "5S", funguje na princípe: "Akcie hovoria hlasnejšie ako slová." Každá veľká práca sa začína malým skutkom, postupným pochopením podstaty problému, chybami a opravami. Nikdy by ste nemali odmietnuť pomoc, radu, podporu od kolegov a technického personálu. Skutočný pokrok v postupných, hoci aj malých krokoch je oveľa užitočnejší ako celosvetové diskusie o veľkom projekte, ktorý dokáže otočiť štruktúru výroby na danom pracovisku.
Vyššie diskutované metodické prístupy odhaľujú nielen obsah a technológiu implementácie princípov systému „Objednávka“, ale skôr vysvetľujú prekážky, ťažkosti a ťažkosti, ktoré sa vyskytnú na ceste implementácie tohto systému aj systému „5S“. .
Ak pre japonského zamestnanca úplne stačí mať u vedenia firmy istotu, že zavedenie systému „5S“ prinesie veľké výhody nielen firme, ale aj samotnému zamestnancovi, aby bola dlhodobá motivácia na implementáciu prvkov tohto systému do praxe, potom to zamestnancovi ruského podniku zjavne nestačí. Sú potrebné účinné mechanizmy, ktoré by stimulovali zlepšenie pracovných miest a zlepšenie kvality výrobkov a práce na každom pracovisku. Ako vždy, v ruských podnikoch všetko, čo súvisí so zlepšovaním, racionalizáciou, vrátane pracovných miest, nie je prakticky založené na systéme, nie na účinných stimuloch, ale výlučne na osobnej iniciatíve. Takú vážnu vec, akou je zavedenie systémov „5S“ či „Objednávka“, nemožno „kecať“ len na továrenských nadšencov.
Existuje názor, že ak by sa všetka práca mohla vykonať „naliehavo“, Rusko by tu nemalo konkurentov, zatiaľ čo práca spojená s každodennou usilovnou prácou na obnovení poriadku a čistoty nezodpovedá našej mentalite. Z toho vyplýva potreba podrobného vysvetlenia pomocou metodických prístupov, ako vykonávať v podstate pomerne jednoduchú prácu, ktorou sú princípy systému „Objednávka“.
Ak chceme žiť civilizovane, ako napríklad v Japonsku alebo v Európe, musia noví manažéri presvedčiť pracujúcich, že kvalita práce nezávisí od mentality národa, ale od schopnosti a túžby spĺňať všetky požiadavky zaznamenané ako v technických špecifikáciách na produkty, tak aj v medzinárodných normách ISO 9000. A nielen inšpirovať, ale aj organizačne a materiálne zabezpečiť implementáciu potrebných noriem.
V dôsledku štúdia materiálu v tejto kapitole by študent mal:
vedieť
- sedem nástrojov na kontrolu kvality výrobkov;
- štatistické metódy kontroly kvality výrobkov;
- funkčná analýza nákladov;
- moderné technológie riadenia kvality (koncept six sigma, metóda QFD atď.);
byť schopný
- vytvoriť kauzálny Ishikawov diagram a Paretov diagram s cieľom riadiť kvalitu tovarov a služieb;
- použiť metódu QFD s cieľom sledovať požiadavky spotrebiteľov vo všetkých fázach životného cyklu produktu;
- aplikovať funkčnú analýzu nákladov s cieľom dosiahnuť potrebné spotrebiteľské vlastnosti produktu (služby) s minimálnymi nákladmi na ich poskytovanie;
vlastné
- zručnosti pri uplatňovaní siedmich nástrojov na kontrolu kvality tovaru vstupujúceho do obchodu;
- štatistické metódy riadenia kvality tovaru vstupujúceho do obchodu.
Význam a klasifikácia metód
Ako je uvedené vyššie, v kap. 2, jednou zo zásad SM K je, že základom pre rozhodovanie by mali byť len fakty, nie intuícia. Jedným z dôvodov chýb v riadení kvality je, že fakty sú zamieňané so subjektívnymi úsudkami. Aby sa predišlo chybám, je potrebné organizovať proces vyhľadávania faktov, t.j. štatistický materiál.
Problematikou zberu, spracovania a analýzy výsledkov sa zaoberá matematická štatistika, ktorá zahŕňa obrovské množstvo rôznych metód. Z tohto súboru vyberali japonskí vedci (predovšetkým profesor K. Ishikawa). sedem základných nástrojov kontroly kvality(obr. 4.1). Pri vývoji štatistických metód v Japonsku zohrali významnú úlohu kruhy kvality.
Ryža. 4.1.
S rastom objemov výroby v sériovej a hromadnej výrobe produktov potreboval spotrebiteľ (ako právnická osoba) aj samotný výrobca informácie o skutočnej kvalite vyrábaných a nakupovaných produktov. Kvôli veľkému objemu vyrobených sérií produktov sa však kompletná kontrola kvality ťažko vykonávala a jej spoľahlivosť bola nízka. Aby sa znížila pracovná náročnosť a zvýšila spoľahlivosť, začali sa uplatňovať štatistické metódy selektívnej kontroly kvality. Ich význam je veľmi jednoduchý: po preštudovaní malej časti produktov (vzorka) je možné vyvodiť spoľahlivé závery o kvalite celej šarže.
Koncom 70. a začiatkom 80. rokov 20. storočia. Zväz japonských vedcov a inžinierov vyvinul sofistikovanejšiu sadu nástrojov kontroly kvality. Tieto nástroje boli založené tak na metódach matematickej štatistiky, ako aj na metódach iných vied: operačná analýza, teória optimalizácie atď. Ako subtílnejšie nástroje boli určené pre inžinierov. Tieto metódy sú tzv nástroje riadenia kvality. Tento tutoriál obsahuje niektoré z nástrojov riadenia kvality: "Šesť sít", technológia nasadenia kvalitných funkcií, analýza nákladov.
Nižšie sú opísané tri skupiny metód:
- 1) základné nástroje kontroly kvality;
- 2) štatistické metódy selektívnej kontroly kvality;
- 3) nástroje riadenia kvality.
Základné nástroje kontroly kvality
Hlavnými nástrojmi kontroly kvality sú metódy štatistickej analýzy podmienok a faktorov ovplyvňujúcich kvalitu produktu. Štatistická analýza zahŕňa analýzu druhov a príčin sobášov, analýzu vplyvu jednotlivých faktorov technologického procesu na ukazovatele kvality. Pri analýze sa odporúča použiť špeciálne grafické metódy (niekedy nazývané deskriptívna štatistika) na vizualizáciu kvalitných údajov. Tieto metódy zahŕňajú sedem nástrojov kontroly kvality (pozri obrázok 4.1).
Kontrolný hárok (hárok)- nástroj na zhromažďovanie a organizovanie údajov na uľahčenie ďalšieho používania zozbieraných informácií.
Na obr. 4.1, kontrolný hárok nie je náhodne umiestnený v strede, obklopený ďalšími 6 nástrojmi. Hrá osobitnú úlohu, pretože implementácia akejkoľvek úlohy analýzy kvality začína zberom počiatočných údajov.
Kontrolný hárok - papierová forma, na ktorej sú predtlačené kontrolované typy defektov (v našom prípade na príklade defektov vo výzdobe keramických výrobkov), ktoré formou jednoduchých symbolov označujú frekvenciu ich výskytu.
Počet rôznych letákov v podniku sa pohybuje v stovkách a pre každý konkrétny účel je možné vytvoriť vlastný leták. Princíp ich dizajnu však zostáva nezmenený: forma listu by mala byť jednoduchá a zrozumiteľná (bez ďalších vysvetlení); je potrebné uviesť, kto, v akom štádiu a ako dlho zbieral údaje.
Je zrejmé, že kvalita výrobkov je hlavným ukazovateľom činnosti každého podniku. Na udržanie konkurencieschopnosti tovarov a služieb sa dnes pri vývoji systému manažérstva bezpečnosti potravín využívajú rôzne, väčšinou ekonomické a matematické. Napríklad dynamické, lineárne a nelineárne programovanie, simulačné modelovanie, návrh experimentov, teória čakania a hier, funkčná analýza nákladov, metóda Taguchi a metóda štruktúrovania kvality.
Zanechajte žiadosť o bezplatnú konzultáciu
Metóda nasadenia funkcie kvality - QFD (Nasadenie funkcie kvality). Ide o systematický prístup k identifikácii požiadaviek zákazníkov, ktorý pomáha podniku pochopiť a integrovať zisťovanie požiadaviek do konkrétnych plánov poskytovania služieb. Na rozdiel od iných metód je QFD metódou zabezpečenia kvality, ktorá zahŕňa uspokojovanie potrieb zákazníka pri budovaní zložených matíc, neskôr nazývaných „domy kvality“, v rámci ktorých sa zaznamenávajú informácie o kvalite služieb a prijatých rozhodnutiach. Táto metóda je technológiou navrhovania produktov a procesov, ktorá umožňuje premeniť priania spotrebiteľa na technické požiadavky na produkty a parametre ich výrobných procesov. Metóda QFD je expertná metóda, ktorá využíva tabuľkový spôsob prezentácie údajov a so špecifickou formou tabuliek, ktoré sa nazývajú „domy kvality“. Hlavnou myšlienkou technológie QFD je pochopenie, že existuje veľký rozdiel medzi spotrebiteľskými vlastnosťami („skutočné ukazovatele kvality“) a parametrami produktu stanovenými v normách („pomocné ukazovatele kvality“). Pomocné ukazovatele kvality sú dôležité pre výrobcu, ale nie vždy nevyhnutné pre spotrebiteľa. Ideálnym prípadom by bolo, keby výrobca mohol kontrolovať kvalitu produktu priamo zo skutočných ukazovateľov, ale väčšinou to nie je možné, preto používa pomocné ukazovatele.
Technológia QFD je postupnosť činností výrobcu na premenu skutočných ukazovateľov kvality produktu na technické požiadavky na produkty, procesy a zariadenia. Hlavným nástrojom technológie QFD je stôl špeciálneho typu, nazývaný „dom kvality“. Táto tabuľka ukazuje vzťah medzi skutočnými indikátormi kvality (vlastnosti spotrebiteľov) a pomocnými indikátormi (technické požiadavky):
Aplikácia metódy QFD umožňuje zohľadniť požiadavky spotrebiteľa vo všetkých fázach výroby hotových výrobkov, pre všetky prvky systému kvality organizácie a tým zvýšiť mieru spokojnosti zákazníkov, znížiť náklady. konštrukčných procesov a prípravy produktov do výroby.
metóda FSA je technológia analýzy nákladov produktu, aby mohol vykonávať svoje funkcie; FSA sa vykonáva pre existujúce produkty a procesy s cieľom znížiť náklady, ako aj pre produkty vo vývoji s cieľom znížiť ich náklady. Metóda FSA sa v priemysle aktívne používa od 60. rokov 20. storočia, predovšetkým v USA. Jeho použitie umožnilo znížiť cenu mnohých druhov výrobkov bez zníženia ich kvality a optimalizovať výrobné náklady. FSA je teraz jedným z najpopulárnejších typov analýzy produktov a procesov. FSA je jednou z metód funkčnej analýzy technických objektov a systémov, do rovnakej skupiny metód patrí FFA (funkčná fyzikálna analýza) a FMEA analýza. Pri vykonávaní funkčnej analýzy nákladov sa zisťujú funkcie prvkov technického objektu alebo systému a posudzujú sa náklady na implementáciu týchto funkcií s cieľom znížiť tieto náklady. Vykonávanie FSA zahŕňa tieto hlavné fázy:
1. Dôsledná konštrukcia modelov objektu FSA (komponentový, štrukturálny, funkčný); modely sú zvyčajne zostavené v tabuľkovej (maticovej) forme; 2. Štúdium modelov a vývoj návrhov na zlepšenie predmetu analýzy.
Ishikawov diagram(diagram príčiny a následku, "rybia kosť") - kvalitný nástroj, ktorý slúži na vizualizáciu vzťahov príčin a následkov medzi objektom analýzy a faktormi, ktoré ho ovplyvňujú.
Ovplyvňujúci faktor alebo problém sa nachádza, ako je znázornené, na konci vodorovnej šípky; možné príčiny sa zobrazia ako označené šípky, ktoré sú zahrnuté v šípke hlavnej príčiny. Každá šípka môže mať aj ďalšie šípky, ktoré zobrazujú hlavné príčiny alebo faktory v nej zahrnuté, ktorých priorita klesá so vzdialenosťou od hlavnej šípky.

Paretova analýza- Môže byť použitý na analýzu nápadov z brainstormingu. Používa sa na identifikáciu niekoľkých životne dôležitých problémov alebo príčin problémov, ktoré majú najväčší vplyv. Paretov diagram vizuálne predstavuje údaje vo forme diagramu zostaveného v zostupnom poradí podľa frekvencie výskytu prvkov. Vo všeobecnosti Paretov graf ukazuje, že 80 % vplyvu je spôsobených 20 % príčin, preto sa niekedy nazýva pravidlo 80/20.
Štatistická kontrola procesu (SPC)- je súbor nástrojov na riadenie procesov. Okrem toho je aj strategickým nástrojom na zníženie variability produktov, dodávok materiálu, vybavenia, vzťahov a procesov, ktoré sú príčinou väčšiny problémov s kvalitou. SPC ukáže, či je proces „pod kontrolou“ – t.j. či je stabilný len s náhodnými variáciami, alebo „mimo kontroly“ a vyžaduje si pozornosť. navyše SPC automaticky varuje pri klesajúcej ovládateľnosti a môže pomôcť pri dlhodobom znižovaní chybovosti, identifikácii špeciálnych príčin, znižovaní alebo odstraňovaní príčin variácií a dosahovaní úrovní ovládateľnosti čo najbližšie k cieľu. V SPC tvoria čísla a informácie základ pre rozhodovanie a konanie prostredníctvom prísneho systému zaznamenávania údajov. Okrem nástrojov potrebných na zaznamenávanie údajov existuje aj sada nástrojov na analýzu a interpretáciu údajov, z ktorých niektoré sú popísané na nasledujúcich stranách. Pochopenie nástrojov a ich používania si nevyžaduje predchádzajúce znalosti štatistiky.
Kontrolná karta. Používa sa na monitorovanie riadených procesov pomocou hodnôt a rozsahov. Kontrolná tabuľka predstavuje údaje, ako sú predaj, objem, sťažnosti zákazníkov prezentované v chronologickom poradí a ukazuje, ako sa hodnoty menia v priebehu času. V kontrolnom diagrame každý bod zodpovedá individuálnej hodnote. Nad a pod priemerom prechádza horná a dolná varovná línia a akčné línie (UWL, LWL, UAL, LAL). Tieto hranice fungujú ako rozhodovacie podnety a pravidlá a poskytujú operátorom informácie o procese a jeho stave riadenia. Mapa je užitočná ako historický záznam procesu, ako postupuje a ako prostriedok na identifikáciu a predpovedanie zmien.