Методы обеспечения качества по. Методы обеспечения качества продукции бывают разными Современные методы обеспечения качества
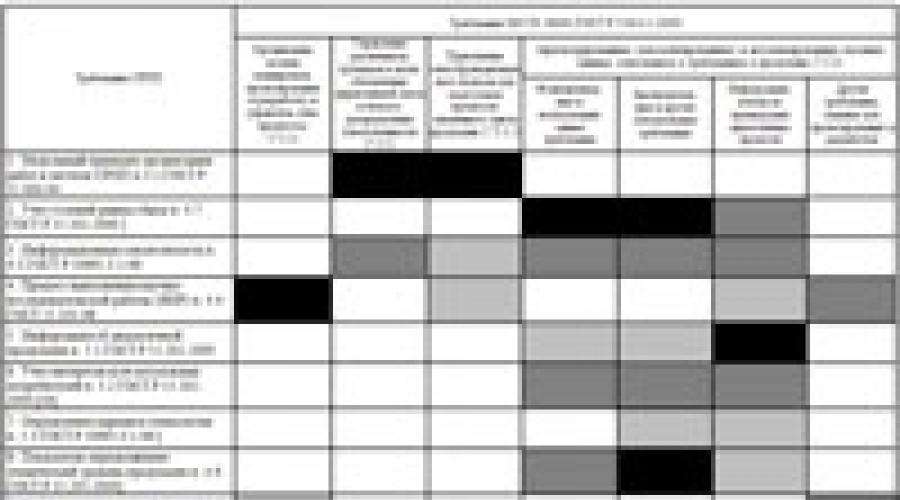
На предприятиях машиностроения в последнее время все чаще возникает необходимость создавать системы управления, соответствующие не основополагающему стандарту ИСО 9001, а усовершенствованным (модернизированным в соответствии с требованиями времени и спецификой конкретной отрасли) стандартам на системы менеджмента качества (например, стандарты Газпрома, РЖД и т.п.).
Хотя на большинстве российских предприятий давно внедрена и достаточно успешно функционирует система разработки и постановки продукции на производство (СРПП), соответствующая национальным стандартам РФ, многие потребители сегодня требуют от поставщиков внедрения современных систем менеджмента качества, ориентированных на стандарты, учитывающие отраслевую специфику (например международный стандарт ИСО/ТУ 16949, AS 9100 и аналогичные им).
При внедрении этих стандартов необходимо дублировать многие уже существующие и действующие на предприятии процедуры, реализующие требования стандартов СРПП. Нет сомнений, что это ведет к дополнительным нерациональным затратам всех видов ресурсов.
Задача сокращения временных, человеческих и финансовых ресурсов на внедрение требований международных стандартов к методам и процедурам обеспечения качества с использованием опыта действующих национальных стандартов РФ сегодня чрезвычайно актуальна.
Несмотря на, казалось бы, очевидные различия в особенностях построения производства в автомобильной индустрии и в других отраслях машиностроения, общей характерной чертой является широкое использование поставок комплектующих на основные сборочные заводы сравнительно небольшими предприятиями.
Такие принципы организации производства хорошо отработаны на практически всех без исключения автомобильных заводах (как отечественных, так и зарубежных), применяются они и для нефтегазового машиностроения - на заводах, выпускающих сложные технологические системы: буровые установки, комплексы для освоения морских месторождений и пр. Аналогичные примеры можно найти и в других отраслях.
В силу того, что автомобили представляют собой изделие гораздо более широкого массового спроса, именно в этой отрасли изготовителям пришлось уделить особое внимание созданию таких систем менеджмента качества, какие могли бы соответствовать современным принципам организации производства и, более того, могли бы одновременно способствовать повышению качества продукции. Кроме того, автомобильная промышленность создала свою отраслевую систему стандартов качества гораздо раньше, чем потребность в этом возникла в других областях.
Именно в этом контексте представляют несомненный интерес работы в области формирования системы менеджмента качества, проводимые в настоящее время на предприятиях автомобилестроения. Более чем вероятно, что с учетом незначительных корректив, достигнутые на них результаты могут найти применение на любых машиностроительных заводах.
Хорошо известно, что для того, чтобы показать потребителю, как компания следит за качеством своей продукции и гарантировать ему это качество, производители создают системы менеджмента качества, соответствующие требованиям стандартов ИСО 9001, ИСО/ТУ 16949, применяют описанные там методы.
В России сейчас наблюдается тенденция перехода от национальных стандартов к международному стандарту ИСО/ТУ 16949, который применяется к предприятиям автомобильной промышленности и организациям, производящим соответствующие запасные части. Вследствие того, что ИСО/ТУ 16949 был выпущен одновременно со стандартом для систем менеджмента качества, он имеет с последним много общего, но есть у него и свои особенности, так как ИСО/ТУ 16949 был разработан международной целевой группой автомобильной промышленности (IATF) и Японской ассоциацией производителей автомобилей, зарегистрированной в качестве корпорации (JAMA) при поддержке Технического комитета ИСО/TC 176 «Менеджмент качества и обеспечение качества».
Крупнейшие автопроизводители уже сертифицируют или планируют сертифицировать свои системы менеджмента качества по международному стандарту ИСО/ТУ 16949, и требуют этого от своих поставщиков. Например, такие требования выдвигают к своим поставщикам представители «Большой Тройки» -DaimlerChrysler, General Motors, Ford.
Следует отметить, что внедрение стандарта ISO/TS 16949 требует применения специальных методов организации работ - APQP (Advanced Product Quality Planning and Control Plan - Перспективное планирование качества продукции и разработка плана управления), PPAP (Production Part Approval Process - Процесс согласования производства части, т.е. одобрение производства автомобильных компонентов), а также использования некоторых инструментов обеспечения качества продукции с применением статистических методов анализа - FMEA (Method for potential failure mode and effects analysis - Метод анализа видов и последствий потенциальных дефектов), MSA (Measurement systems analysis - Анализ системы измерений), SPC (Methods of statistical process control - Методы статистического управления процессом) и QSA (Management quality systems analysis - Оценка систем менеджмента качества).
Наиболее серьезные трудности на отечественных предприятиях вызывает внедрение метода организации работ APQP (Advanced Product Quality Planning), фактически - процесса планирования, разработки и подготовки производства автомобильных компонентов, дающего возможность обеспечения абсолютно всех требований и ожиданий потребителя уже на этапе подготовки производства, когда имеются основные возможности предотвращения дефектов, Сложности возникают из-за того, что этот процесс затрагивает практически все подразделения и все процессы в организации и должен быть реализован на всех этапах жизненного цикла продукции - от планирования создания, проектирования и разработки автомобильного компонента до его серийного производства.
В России существует система схожая по назначению с APQP - система разработки и постановки продукции на производство (СРПП).
Как известно, СРПП - комплекс взаимосвязанных основополагающих организационно-методических и общетехнических государственных стандартов, устанавливающих основные положения, правила и требования, обеспечивающие техническое и организационное единство выполняемых работ на стадиях жизненного цикла продукции (ЖЦП), включающих исследование и обоснование разработки продукции или проекта, собственно разработку, производство, эксплуатацию (применение, хранение) продукции и ремонт (для ремонтируемой продукции), а также взаимодействие заинтересованных сторон.
СРПП взаимоувязана со стандартами других общетехнических систем и комплексов стандартов: Единой системой конструкторской документации (ЕСКД), Единой системой технологической документации (ЕСТД), Единой системой программной документации (ЕСПД), Государственной системой обеспечения единства измерений, Технологическим обеспечением создания продукции.
В настоящее время многие специалисты предприятий озабочены следующей проблемой - на предприятиях уже внедрена и успешно функционирует система разработки и постановки продукции на производство в соответствии с национальными стандартами РФ. Но наступает момент, когда потребитель - некий автопроизводитель - требует от своего поставщика внедрения системы менеджмента качества по международному стандарту ИСО/ТУ 16949, в том числе, естественно, внедрения метода APQP как неотъемлемой составной части такой системы менеджмента качества. Специалисты понимают, что им приходится дублировать многие уже осуществляемые процессы, что сопровождается дополнительными нерациональными затратами.
Эта ситуация живо обсуждается специалистами, которые с ней столкнулись . Правда, в большинстве случаев специалисты только рассуждают о том, как интересно совпадают требования международных организаций (международной целевой группой автомобильной промышленности (IATF) и требования наших старых, давно используемых национальных стандартов, которые были разработаны еще в восьмидесятые и девяностые годы прошлого века.
Итак, есть проблема - как с наименьшими затратами внедрить требования стандарта ИСО/ТУ 16949, в том числе экзотический пока для нас метод организации работ APQP на предприятии с внедренной и успешно функционирующей СРПП.
Целью нашего исследования являлась разработка алгоритма освоения на российских предприятиях международных систем управления качеством с учетом специфики накопленного предшествующего опыта функционирования отечественных систем и при этом оптимизации затрат ресурсов различного рода: трудовые, финансовые, временные и пр.
Автором был проведен анализ степени совместимости требований стандарта ИСО/ТУ 16949 и метода APQP с требованиями национальных стандартов СРПП. Для этого были построены матрицы соответствия требований вышеуказанных двух систем, в которой 45 строк отвечают требованиям СРПП, и по 49 столбцов соответствуют требованиям ИСО/ТУ 16949 и APQP. Каждый элемент пересечения строк и столбцов был далее проанализирован путем сочетания экспертных оценок и методов регрессионного анализа .
Для более точного понимания, какова была степень обобщения требований, как проводилась классификация требований метода APQP по группам и какие именно требования из СРПП рассматривались на предмет их совместимости с требованиями APQP-процесса, рассмотрим небольшую часть матрицы в более укрупненном виде. Фрагмент матрицы представлен в таблице 2.
Таблица 2 - Фрагмент матрицы совместимости требований СРПП и ИСО/ТУ 16949
В результате анализа выявлено, что в отдельных случаях имеет место совместимость (полная или частичная) требований ИСО/ТУ 16949 и APQP с требованиями СРПП и наоборот. Поэтому далее была проведена количественная оценка степени совместимости требований ИСО/ТУ 16949 и APQP-метода, которая показала, что полное совпадение требований обнаружено в 15 % случаев, и частичное совпадение требований - в 13 % случаев. Кроме того, были выявлены ситуации, когда требования могут служить основой для внедрения международных стандартов: группа требований ИСО/ТУ 16949 и APQP напрямую не совпадает с требованиями СРПП, но, если последние каким-то образом дополнить, то полное или частичное совпадение будет иметь место. Таких ситуаций оказалось около 22 %. Наконец, число случаев с незначительным совпадением равно 12 %, и отсутствие совпадения обнаружено в 38 % случаев.
Например, в п. 5.2 ГОСТ Р 15.201-2000 указано следующее: «В техническом задании рекомендуется предусматривать учет интересов всех возможных потребителей». В свою очередь, в качестве входной информации на первом этапе метода APQP необходимо иметь «информацию от конкретных потребителей». При исследовании было признано, что имеет место полное совпадение требований.
Еще один пример: в п. 4.6 ГОСТ Р 15.201-2000 есть требование о том, что разработчик продукции при проведении научно-исследовательских, опытно-конструкторских и технологических работ должен обращать особое внимание на обеспечение, в частности, требований учета показателей продукции, определяющих ее технический уровень. В APQP-процессе речь идет об опорных показателях продукции/процессов конкурентов. В данном случае было признано, что имеет место частичное совпадение требований. Аналогичная ситуация и с такими требованиями, как обязательность технологической проработки продукции в соответствии с п. 5.2.6 ГОСТ Р 50995.3.1-96 и необходимость наличия «предположения о продукции и процессах» в соответствии с требованиями метода APQP.
На основании результатов этой работы можно сделать следующий вывод - при внедрении ИСО/ТУ 16949 и метода организации работ APQP на предприятиях с внедренной и успешно функционирующей СРПП можно существенно сократить затраты ресурсов.
Сокращение затрат может быть достигнуто за счет того, что те элементы управления процессом подготовки производства, которые уже внедрены на предприятии в соответствии с требованиями стандартов СРПП нет необходимости повторно внедрять в том случае, если они предусмотрены при применении ИСО/ТУ 16949 и APQP. Вполне достаточно будет уточнить в документации предприятия разницу в терминологии. Все мы прекрасно понимаем, что такой подход может в значительной степени сэкономить и время внедрения ИСО/ТУ 16949 и APQP-метода, и сократить требуемые для внедрения людские и материальные ресурсы.
Следует отметить, что проведен достаточно поверхностный анализ существующей ситуации. В частности, требования стандартов СРПП были разбиты всего на 45 групп, требования ИСО/ТУ 16949 и APQP-метода - на 49 групп, что, вероятно, недостаточно для полноценной оценки совместимости требований ИСО/ТУ 16949 и APQP с требованиями стандартов СРПП; следует также отметить, что для оценки совместимости требований применялась шкала, состоящая всего из 5 категорий, что также дает только приблизительную оценку совместимости требований.
Необходимо также отметить, что, в зависимости от специфики предприятия и общей направленности его деятельности, порядок внедрения различных требований как стандартов СРПП, так и требований ИСО/ТУ 16949 и APQP может быть различным. Но, при этом, следует учитывать, что некоторые требования могут быть взаимосвязаны и тогда существует неоспоримый порядок их внедрения. Эта ситуация обязательно должна быть учтена при совместном внедрении стандартов СРПП и ИСО/ТУ 16949.
С учетом вышесказанного разработана схема организации производства, которую мы назвали «организационной моделью» (рисунок 1). Организационная модель позволяет определить последовательность действий на стадии проектирования, разработки и постановки продукции на производство и при производстве продукции, выявить и локализовать узкие места, предпринять конкретные действия для их устранения, распределить ответственность и полномочия в рамках как подразделения, ответственного за выпуск продукции, так и во всей организации .
Рисунок 1 - Организационная модель «Управление производством и обслуживанием»
Разработанная организационная модель применима на любом промышленном предприятии. Организационная модель может быть применена для определения порядка внедрения и для распределения работ при внедрении современных методов управления качеством на машиностроительном предприятии, имеющем действующую систему управления, основанную на внедренных стандартах национальной системы СРПП.
В проведенном анализе также не был учтен такой фактор, как некоторые неточности и условности перевода текста, описывающего метод APQP. В такой ситуации бывает очень трудно учесть синонимы при изложении требований - ведь некоторые требования могут даже полностью совпадать, но при этом быть изложены совершенно разными словами.
Результаты анализа позволяют разработать конкретный алгоритм внедрения требований международных стандартов, учитывающий действующую на предприятиях систему СРПП, что может существенно сократить затраты времени, людских и финансовых ресурсов и при этом использовать громадный багаж, оставленный нам нашими предшественниками - советскими инженерами - разработчиками национальных стандартов. Этот алгоритм будет описан в следующей публикации автора.
Наталия Викторовна ВАЩЕНКО — начальник отдела сертификации и организации работ АНО Координационный Центр «АТОМВОЕНСЕРТ»
Список использованных источников
1 Кудряшов А.В. Круглый стол. APQP: проблемы и опыт внедрения // Методы менеджмента качества. - 2012. - №6.
2 Кершенбаум В.Я., Ващенко Н.В. Методология оценки совместимости нормативных требований отечественной и зарубежной практики при построении систем менеджмента качества // Управление качеством в нефтегазовом комплексе. - 2013. - №1. - с. 17 - 21.
3 Ващенко Н.В. О целесообразности документированной процедуры в рамках реализации требований седьмого раздела ISO 9001:2008 // Управление качеством в нефтегазовом комплексе. - 2013. - №2. - с. 14 - 18.
Многочисленная статистика по качеству отмечает, что дефектность продукции примерно на 85-90% вызвана человеческим фактором. Рассмотрим, какие причины, связанные с рабочим, могут оказать влияние на несоблюдение технической документации, вплоть до брака продукции. Среди них можно отметить: низкую квалификацию, малый стаж работы, плохое самочувствие, невнимательность при ознакомлении с чертежами, технологиями или инструкциями, некачественную подготовку рабочего места.
Следует подчеркнуть, что причины брака могут быть связаны не только с человеком, но и с инструментом, технологическим оборудованием, оснасткой. Это верно, но чаще всего это происходит не столько за счет недостатков самого инструмента, оборудования или оснастки, а в связи с небрежной их заточкой, плохим ремонтом или неточным изготовлением и сборкой, которые выполняют рабочие. Если «докапываться» до виновника дефекта, то в подавляющем большинстве это будет человек, который работает не обязательно на вашем предприятии, но и, возможно, на предприятии поставщика.
С чего надо начинать улучшение качества? Японские специалисты советуют начинать с качества на рабочем месте . Более того, они разработали стройную систему улучшения качества на рабочем месте, которую назвали «5S» («Практика хорошего домосодержания»). Название происходит от пяти японских слов, начинающихся на букву «С»: «сэйри» (сортировка), «сэйсо» (очистка), «сэйтон» (организация), «сэйкэцу» (стандартизация), «сицукэ» (самопроверка). Русский перевод этих слов дает если не совсем четкое, то вполне достаточное представление о примерном содержании мероприятий по улучшению качества на рабочем месте. Если кратко охарактеризовать эту систему, то можно сказать, что «прежде, чем начинать работу, да еще ответственную, надо разобраться с порядком на своем рабочем месте».
Дадим более четкое содержание каждого из этапов системы «5S» . Прежде чем приступить к ее реализации, необходимо подробно описать, а если возможно, то и сфотографировать рабочую зону (или рабочее место), которую надо реорганизовать. Сравнение описаний рабочих зон (мест) до и после преобразований может оказать на руководство благоприятное впечатление, которое активизирует работу на предприятии по качеству.
Этап 1. Сортировка. Поместить вещи (или предметы), которые используются ежедневно, в одно место. Предметы, используемые раз в неделю, поместить в другое место, ежемесячно - в третье, а то, что требуется очень редко,- в четвертое. Проделать эту процедуру для каждой зоны рабочего места. Затем из каждого места хранения отобрать и оставить по одному экземпляру каждого типа предметов, а остальные переложить в шкаф для хранения запасных частей.
Этап 2. Очистка. Очистить все рабочие поверхности, прежде чем снова на них что-нибудь положить. Убедиться, что рядом с рабочим местом имеются соответствующие контейнеры для сбора отходов. Поместить все запасные части на общий склад. Составить список возвращенных на склад предметов, чтобы иметь возможность сообщить о них руководству цеха. Систематизировать и сложить в одно место все необходимые документы и почистить все инструменты. Установить стандарты (нормативы) чистоты, которые должны соблюдаться каждым работником.
Этап 3. Организация. Аккуратно разложить все бумаги и папки. Предметы, которые используются ежедневно, должны быть у рабочего под рукой. Предметы, используемые раз в неделю, можно расположить на расстоянии одного шага, а используемые раз в месяц - на расстоянии 2-3 шагов. Все остальное может быть расположено на расстояние нескольких шагов от рабочего места. Необходимо четко определить место каждого предмета.
Этап 4. Стандартизация. Ознакомить всех сотрудников, имеющих отношение к этому рабочему месту, со стандартами чистоты и поместить фотографии с «правильной» стандартной обстановкой. Где это необходимо, обеспечить оборудование и инструменты прозрачными чехлами, защищающими от пыли. Если такие чехлы будут непрозрачными, то работники, скорее всего, станут под ними хранить предметы, не имеющие отношения к рабочему месту.
Этап 5. Самопроверка. Примерно через месяц внимательно осмотрите состояние рабочего места с целью возможности его улучшения. Если найдутся лишние предметы - отправьте их на общий склад. Проанализируйте стандарты чистоты и при необходимости пересмотрите их. Повторите этот шаг через месяц.
Можно порекомендовать и дополнительные меры по поддержанию порядка на рабочем месте. Так, например, можно создать передвижные доски с инструментами для конкретных работ или нарисовать контуры инструментов на досках, чтобы было сразу ясно, какой инструмент отсутствует.
Японские исследователи считают: если менеджеры компании не могут реализовать «5S», значит, они не могут эффективно управлять. И напротив, если вы сможете освоить данную систему, это означает, что вы можете так же успешно внедрить и другие, более сложные системы. Причина этого заключения в том, что система «5S» не требует для своего осуществления какого-то особого штата управленцев и не станет эффективной, пока весь персонал не будет к ней приобщен и не начнет думать об успехе этой системы. Но если система «5S» уже внедрена, то можно считать, что и другие системы почти наполовину освоены (в части готовности персонала к осуществлению изменений).
С середины 80-х гг. XX в. в японских фирмах система «5S» занимала центральное место в мышлении и философии менеджмента. Руководство фирм повсеместно пришло к мнению, что данная система - это ключевой метод управления в любой, даже самой высокотехнологичной области деятельности.
Система «5S» получила в последние годы широкую известность на российских предприятиях. Из отечественной практики внедрения этой системы можно сделать следующие выводы:
- - она применима и может успешно внедряться на отечественных предприятиях и в организациях различных форм собственности при заинтересованности в этом руководства;
- - содержание принципов системы и технология ее внедрения требуют существенной адаптации к особенностям отечественной экономики, методам организации производства и ментальности персонала;
- - возможность успешного внедрения системы непосредственно зависит от социально-экономических условий труда на рабочих местах, т.е. уровня и регулярности выплаты заработной платы, систематической и ритмичной загрузки производства, соблюдения со стороны администрации хотя бы основных требований к безопасным условиям труда.
Предприняты попытки модернизации этой системы с учетом принципов научной организации труда и практики улучшения качества. Новая система, вобравшая в себя элементы системы «5S» и адаптированная к отечественным условиям производства, получила название «Упорядочение» (табл. 2.4) . Основные принципы этой системы заключаются в следующем:
- - убрать все лишнее;
- - регулярно проводить тщательную уборку и проверку исправности оборудования и инвентаря;
- - разместить на рабочем месте все наиболее удобным образом;
- - выработать стандарты (правила) хранения, использования, уборки и проверки;
- - постоянно и сознательно следовать принятым правилам.
Таблица 2.4
Сравнение принципов систем «5S» и «Упорядочение»
1. Участие всей команды. Как невозможно «вскипятить воду в одном углу бассейна», так и данную систему нельзя эффективно внедрить на одном рабочем месте или в одном подразделении по воле одного человека. Новая система требует решимости и слаженности действий всего коллектива.
Каждое правило системы, которое необходимо выполнить, само по себе не сложно. Трудность заключается в том, чтобы не прекращать его выполнение. Это требует настойчивости и сотрудничества, что, в свою очередь, создает ощущение принадлежности к команде и улучшает корпоративный климат.
2. Легкость освоения - кажущаяся. Принципы системы «Упорядочение», на первый взгляд, кажутся такими понятными и легко осуществимыми. Но почему же их так непросто реализовать?
Кажущаяся легкость реализации этих принципов связана с тем, что работники не до конца понимают, что же представляет собой система «Упорядочение». Это не разовая генеральная уборка, не перемещение инструмента с одного на другое место, а принципиально новый стиль отношения к рабочей среде, ее организации и безопасности, стиль постоянного поддержания высокоорганизованного, чистого рабочего пространства.
3. От исправлений - к профилактике. Часто можно наблюдать, как много времени менеджеры тратят на исправление того, что было сделано неправильно или несвоевременно. Они реагируют на неприятности постфактум. Но когда мы знакомимся с проблемами, то становится ясно, что причинами возникновения многих из них часто являются очень простые вещи.
Своевременно замеченные нарушения в работе оборудования, выявленные неисправности оснастки или инвентаря могут предотвратить большие потери и несчастные случаи. Даже какие-либо «мелочи» при неблагоприятном стечении обстоятельств могут принести большие неприятности.
- 4. От управления по результатам - к управлению по процессу. Очень часто менеджеры склонны видеть только результаты деятельности и по ним судить об эффективности работы. При реализации системы «Упорядочение» необходимо научиться видеть причины, приводящие к тем или иным результатам, видеть весь процесс в целом, его сильные и слабые стороны.
- 5. Упор на выполнение элементарных требований. Персонал должен привыкнуть к постоянному выполнению элементарных требований. Например, проверка наличия на важных предметах или объектах всех надписей и этикеток.
- 6. Усиление ответственности каждого работника за результаты своего труда. Г. Форд как-то сказал, что «даже самый глупый работник сможет найти сто способов, как обмануть самого квалифицированного мастера». Это подтверждает, что только фактор личной ответственности рабочего и его заинтересованность в работе могут сыграть в производстве большую позитивную роль, а не постоянная регламентация работ и жесткий контроль. Необходима атмосфера, когда люди помогают друг другу и каждый старается выполнить работу хорошо.
- 7. Понимание инструкций и следование их требованиям. Очень часто инструкции и требования не соблюдаются не потому, что работники пренебрегают ими, а из-за того, что они либо не знают, либо не понимают до конца сути содержащихся в них требований или рекомендаций.
Система «Упорядочение» позволяет работникам самостоятельно вырабатывать конкретные правила и инструкции по отношению к своим рабочим местам.
8. Постепенный (пошаговый) подход. Очевидно, что система «Упорядочение», ориентированная прежде всего на изменение поведенческих стереотипов работников, не может быть реализована быстро и сразу после начала ее внедрения, принести ощутимые результаты. Новая система - это первый шаг в направлении долгосрочной программы «выздоровления» предприятия.
Технология внедрения системы предполагает методическое, постепенное, пошаговое освоение ее принципов, оценку и закрепление результатов каждого шага.
9. Система «Упорядочение » - это трудный путь. Новая система, как и японская «5S», функционирует по принципу: «Действия говорят громче, чем слова». Всякая большая работа начинается с малого дела, с постепенного осмысления сути проблемы, с ошибок и исправлений. Никогда нельзя отказываться от помощи, от консультаций, от поддержки коллег и инженерного персонала. Реальные подвижки постепенными, пусть даже малыми шагами гораздо полезнее глобальных рассуждений о крупном проекте, способном перевернуть структуру производства на данном рабочем месте.
Рассмотренные выше методологические подходы не столько раскрывают содержание и технологию выполнения принципов системы «Упорядочение», сколько объясняют те препятствия, трудности и сложности, которые будут встречаться на пути внедрения и этой системы, и системы «5S».
Если для японского работника вполне достаточно уверенности руководства фирмы в том, что внедрение системы «5S» принесет большую пользу не только фирме, но и самому работнику, чтобы осуществлялась длительная мотивация к реализации элементов данной системы на практике, то для работника российского предприятия этого явно недостаточно. Необходимы эффективные механизмы, которые стимулировали бы совершенствование рабочих мест и повышение качества продукции и труда на каждом рабочем месте. Как всегда, на российских предприятиях все, что касается совершенствования, рационализации, в том числе рабочих мест, практически держится не на системе, не на эффективных стимулах, а исключительно на личной инициативе. Такое серьезное дело, как внедрение систем «5S» или «Упорядочение», нельзя «сваливать» только на одних заводских энтузиастов .
Бытует такое мнение, что если бы все работы можно было выполнить «аврально», то Россия здесь не имела бы конкурентов, в то время как работы, связанные с ежедневным кропотливым трудом по наведению порядка и чистоты, не соответствуют нашему менталитету. Отсюда необходимость многословного разъяснения с использованием методологических подходов, как выполнить по существу достаточно простую работу, каковой и являются принципы системы «Упорядочение».
Если мы хотим жить цивилизованно, как, например, в Японии или Европе, то новые менеджеры должны внушить рабочим, что качество работы зависит не от менталитета нации, а от умения и желания соблюдать все требования, записанные как в технических условиях на продукцию, так и в международных стандартах ИСО 9000. И не только внушить, но и организационно, и материально обеспечить внедрение необходимых стандартов.
В результате изучения материала данной главы студент должен:
знать
- семь инструментов контроля качества продукции;
- статистические методы контроля качества продукции;
- функционально-стоимостной анализ;
- современные технологии управления качеством (концепция "шесть сигм", метод QFD и др.);
уметь
- строить причинно-следственную диаграмму Исикавы и диаграмму Парето с целью управления качеством товаров и услуг;
- применять метод QFD в целях отслеживания требований потребителей на всех этапах жизненного цикла продукции;
- применять функционально-стоимостной анализ с целью достижения необходимых потребительских свойств товара (услуги) с минимальными затратами на их обеспечение;
владеть
- навыками применения семи инструментов контроля качества товаров, поступающих в торговлю;
- статистическими методами управления качеством товаров, поступающих в торговлю.
Значение и классификация методов
Как отмечалось выше, в гл. 2, одним из принципов СМ К является то, что основой для принятия решения должны быть только факты, а не интуиция. Одна из причин ошибок при управлении качеством состоит в том, что факты путают с субъективными суждениями. Для предупреждения ошибок следует организовать процесс поиска фактов, т.е. статистического материала.
Вопросами сбора, обработки и анализа результатов занимается математическая статистика, которая включает огромное количество различных методов. Японские ученые (в первую очередь профессор К. Исикава) выбрали из этого множества семь основных инструментов контроля качества (рис. 4.1). Большую роль в освоении статистических методов в Японии сыграли кружки качества.
Рис. 4.1.
С ростом объемов производства при серийном и массовом изготовлении продукции потребителю (как юридическому лицу) и самому изготовителю стала необходима информация о реальном качестве производимой и покупаемой продукции. Однако в связи с большим объемом выпускаемых партий продукции сплошной контроль качества выполнить было трудно, да и достоверность его была невелика. С целью снижения трудоемкости и повышения достоверности начали применяться статистические методы выборочного контроля качества. Их смысл предельно прост: изучив небольшую часть изделий (выборку), можно сделать надежные выводы о качестве всей партии.
В конце 1970-х и в начале 1980-х гг. Союз японских ученых и инженеров разработал более сложный набор инструментов контроля качества. Эти инструменты базировались как на методах математической статистики, так и на методах других наук: операционного анализа, теории оптимизации и др. Как более тонкие инструменты они были адресованы инженерному составу. Эти методы получили название инструменты управления качеством. В данном учебнике рассматриваются некоторые из инструментов управления качеством: программа "Шесть сит", технология развертывания функции качества, функционально-стоимостной анализ.
Ниже описаны три группы методов:
- 1) основные инструменты контроля качества;
- 2) статистические методы выборочного контроля качества;
- 3) инструменты управления качеством.
Основные инструменты контроля качества
Основные инструменты контроля качества - это методы статистического анализа условий и факторов, влияющих на качество продукции. Статистический анализ включает в себя анализ видов и причин брака, анализ влияния отдельных факторов технологического процесса на показатели качества. При анализе рекомендуется использовать специальные графические методы (их иногда называют описательной статистикой) для наглядного представления данных о качестве. К таким методам относят семь инструментов контроля качества (см. рис. 4.1).
Контрольный листок (лист) - инструмент для сбора и упорядочения данных для облегчения дальнейшего использования собранной информации.
На рис. 4.1 контрольный листок не случайно расположен в центре, в окружении остальных 6 инструментов. Он играет особую роль, ведь выполнение любой задачи по анализу качества начинается со сбора исходных данных.
Контрольный листок - бумажный бланк, на котором заранее напечатаны контролируемые виды брака (в нашем случае на примере дефектов декорирования керамических изделий), по которым указывается в виде простых символов частота их появления.
Количество различных листков на предприятии исчисляется сотнями, и для каждой конкретной цели может быть, в сущности, разработан свой листок. Но принцип их оформления остается неизменным: форма листка должна быть простой и понятной (без дополнительных пояснений); необходимо указывать, кто, на каком этапе и в течение какого времени собирал данные.
Очевидно, что качество продукции - это основной показатель деятельности любого предприятия. Для поддержания конкурентоспособности товаров и услуг, разработки системы управления пищевой безопасностью сегодня используются самые разные , в большинстве своем экономико-математические. Например, динамическое, линейное и нелинейное программирование, имитационное моделирование, планирование экспериментов, теория массового обслуживания и теория игр, функционально-стоимостный анализ, метод Тагути и метод структурирования качества.
Оставьте заявку на бесплатную консультацию
Метод развертывания функции качества - QFD (Quality Function Deployment ). Это системный подход к определению требований потребителей, который помогает предприятию понять и интегрировать выявление требования в конкретные планы производства услуг. В отличие от других методов, QFD - метод обеспечения качества, который предполагает удовлетворение потребностей заказчика в построении фигурных матриц, названных впоследствии «домами качества», в рамках которых фиксируется информация о качестве услуги и принимаемых решениях. Данный метод представляет собой технологию проектирования изделий и процессов, позволяющую преобразовывать пожелания потребителя в технические требования к изделиям и параметрам процессов их производств. Метод QFD - это экспертный метод, использующий табличный способ представления данных, причем со специфической формой таблиц, которые получили название "домиков качества". Основная идея технологии QFD заключается в понимании того, что между потребительскими свойствами ("фактическими показателями качества") и установленными в стандартах параметрами продукта ("вспомогательными показателями качества") существует большое различие. Вспомогательные показатели качества важны для производителя, но не всегда существенны для потребителя. Идеальным случаем был бы такой, когда производитель мог проконтролировать качество продукции непосредственно по фактическим показателям, но это, как правило, невозможно, поэтому он пользуется вспомогательными показателями.
Технология QFD - это последовательность действий производителя по преобразованию фактических показателей качества изделия в технические требования к продукции, процессам и оборудованию. Основным инструментом технологии QFD является таблица специального вида, получившая название "домик качества". В этой таблице отображается связь между фактическими показателями качества (потребительскими свойствами) и вспомогательными показателями (техническими требованиями):
Применение метода QFD позволяет учитывать требования потребителя на всех стадиях производства готовой продукции, для всех элементов системы качества организации и, таким образом, повысить степень удовлетворенности потребителя, снизить затраты на процессы проектирования и подготовки изделий к производству.
Метод ФСА представляет собой технологию анализа затрат на выполнение изделием его функций; ФСА проводится для существующих продуктов и процессов с целью снижения затрат, а также для разрабатываемых продуктов с целью снижения их себестоимости. Метод ФСА начал активно применяться в промышленности с 60-х годов, прежде всего в США. Его использование позволило снизить себестоимость многих видов продукции без снижения ее качества и оптимизировать затраты на изготовление. Сейчас ФСА является одним из самых популярных видов анализа изделий и процессов. ФСА - один из методов функционального анализа технических объектов и систем, к этой же группе методов относятся ФФА (функционально-физический анализ) и FMEA-анализ. При проведении функционально-стоимостного анализа определяют функции элементов технического объекта или системы и проводят оценку затрат на реализацию этих функций с тем, чтобы эти затраты снизить. Проведение ФСА включает следующие основные этапы:
1. Последовательное построение моделей объекта ФСА (компонентной, структурной, функциональной); модели строят обычно в табличной (матричной) форме; 2. Исследование моделей и разработка предложений по совершенствованию объекта анализа.
Диаграмма Исикавы (причинно-следственная диаграмма, «рыбий скелет») - инструмент качества, служащий для наглядного представления причинно-следственных связей между объектом анализа и влияющими на него факторами.
Влияющий фактор или проблема располагается, как показано, в конце горизонтальной стрелки; возможные причины будут отображаться как помеченные стрелки, входящие в стрелку основной причины. Каждая стрелка может иметь и другие стрелки, отображающие входящие в нее принципиальные причины или факторы, первостепенность которых снижается по мере удаления от основной стрелки.

Анализ Парето - может быть использован для анализа идей, полученных в результате мозгового штурма. Он используется для определения нескольких жизненно важных проблем или причин возникновения этих проблем, которые оказывают наибольшее влияние. Диаграмма Парето наглядно представляет данные в виде диаграммы, построенной в порядке убывания частоты проявления элементов. Как правило, диаграмма Парето, показывает, что 80% влияния объясняется 20% причин, следовательно, она иногда называется правило 80/20.
Статистическое управление процессами (SPC) - представляет собой набор инструментов для управления процессами. Кроме того, это также стратегический инструмент для снижения изменчивости продукции, поставок материалов, оборудования, отношений и процессов, которые являются причиной большинства проблем с качеством. SPC покажет, находиться ли процесс «под контролем» - т.е. является ли он стабильным только со случайными вариациями, или "вышедшим из-под контроля" и требующим внимания. Кроме того, SPC автоматически предупреждает, когда управляемость снижается и может помочь с долгосрочным снижением уровня дефектности, определением специальных причин, сокращением или устранением причин вариации и достижения уровня управляемости как можно ближе к целевому значению. В SPC, числа и информация формируют основу для принятия решений и действий с помощью тщательной системы регистрации данных. В дополнение к инструментам, необходимым для записи данных, существует также набор инструментов для анализа и интерпретации данных, некоторые из которых рассматриваются на следующих страницах. Понимание средств и способов их использования не требует предварительных знаний статистики.
Контрольная карта. Она используется для наблюдения за контролируемыми процессами с использованием значений и диапазонов. Контрольная карта представляет собой данные, например, касательно продаж, объема, жалоб клиентов, представленные в хронологическом порядке, и показывает, как значения меняются с течением времени. В контрольной карте каждая точка соответствует индивидуальному значению. Выше и ниже среднего, проходит верхняя и нижняя предупреждающая линия и линии действия (UWL, LWL, UAL, LAL). Эти границы действуют как сигналы и правила для принятия решений, а также предоставляют операторам информацию о процессе, и о состоянии его контроля. Карта полезна как исторический отчет о процессе, о его протекании, и в качестве средства для определения и прогнозирования изменений.