"Atyashevo": مراقبة الجودة في كل مرحلة من مراحل الإنتاج. حلقة الجودة ومراحلها. الرقابة والاختبار
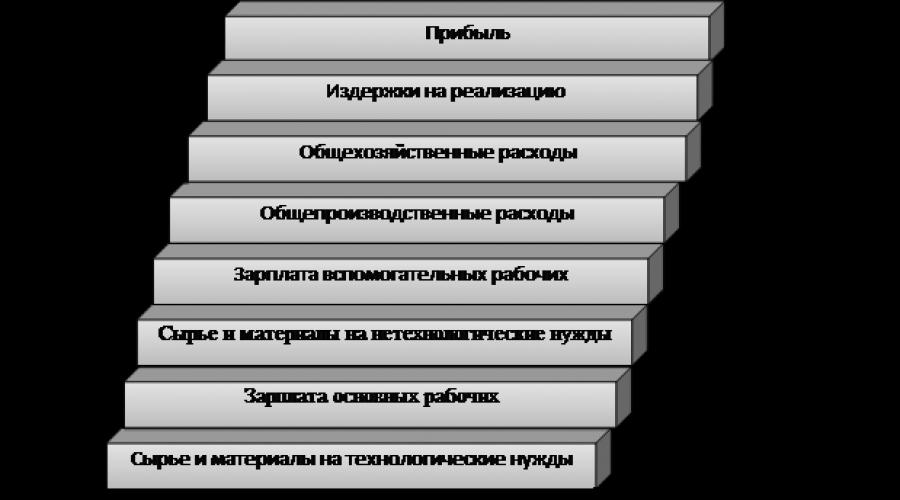
اقرأ أيضا
مراحل التكوين وضمان جودة المنتج:
1. التنبؤ بالاحتياجات والمستوى الفني وجودة المنتج.
2. تكوين مستوى جودة يتوافق مع أعلى فئة جودة. إعداد الوثائق العلمية والتقنية.
3. تحليل قدرات الشركة المصنعة.
4. الدعم اللوجستي بالمواد الخام والمواد والمكونات.
5. الإعداد الفني للإنتاج. تطوير العمليات التكنولوجية. توفير المعدات والملحقات والأدوات.
6. إنتاج المنتجات المطابقة للوثائق العلمية والفنية.
7. المراقبة الفنية واختبار المنتجات. تقييم جودة الصنعة.
8. مبيعات المنتجات النهائية. الحفاظ على الجودة أثناء تخزين المنتجات ونقلها وبيعها.
9. تركيب وتشغيل المنتجات النهائية. ضمان جودة الخدمة والإصلاحات. تقييم درجة رضا المستهلك عن جودة المنتج.
10. التخلص. الاستخدام الأقصى للمواد القابلة لإعادة التدوير.
مراحل دورة حياة المنتج:
1) البحث والتصميم.
2) التصنيع.
3) الاستئناف والتنفيذ.
4) التشغيل والاستهلاك.
من تعريف المفهوم " إدارة الجودة "(راجع الفقرة 1) من الواضح أن المستوى المطلوب من جودة المنتج يجب أن يكون تم تثبيتها وتقديمها ودعمها.
المثبتةمستوى الجودة المطلوب بناءً على تحليل أفضل الإنجازات العلمية والتكنولوجية في بلادنا وخارجها لتلبية الاحتياجات بأقل تكلفة.
تعتبر إدارة الجودة في هذه المرحلة ذات أهمية خاصة لأن هنا يتم تشكيلها ويتم حساب المؤشرات الفنية والاقتصادية والتشغيلية الرئيسية للمنتجات المستقبلية، والتي يتم تضمينها في التصميم والوثائق التكنولوجية.
الغرض من الإدارة في مرحلة البحث والتصميميكون تشكيل مستوى الجودة يتوافق مع أعلى فئة من الجودة والإنجازات الحديثة والتنبؤ بالاحتياجات الاجتماعية لفترة الإنتاج، وكذلك إعداد مجموعة من الوثائق العلمية والفنية للإنتاج والتداول والاستهلاك والتشغيل، مع مراعاة المؤشرات الاقتصادية المحددة.
معيار تقييم الجودةمنتجات في مرحلة البحث والتصميمهي درجة امتثال المعايير الفنية والاقتصادية المضمنة في المنتج مع معاييره المماثلة لأفضل الإنجازات العلمية والتقنية في بلدنا وخارجها.
متاحجودة المنتج في مرحلة التصنيع. يتم تحديد جودة المنتجات في هذه المرحلة من خلال جودة الوثائق التنظيمية والفنية لتصنيع المنتجات وجودة المعدات والمعدات والأدوات والمواد الخام والمواد والمكونات المستلمة.
الغرض من الإدارة في مرحلة التصنيعهو إنتاج المنتجات وفقًا للخطة ومع مستوى الجودة المتكون في مرحلة البحث والتصميم، وكذلك تحسين جودة المنتجات بناءً على الخبرة أو التشغيل من خلال تحسين خصائص المنتج وتحسين تكنولوجيا الإنتاج مع مراعاة المؤشرات الاقتصادية المقررة .
معيار التقييمجودة المنتج في مرحلة التصنيعهي درجة امتثال المعايير الفنية والاقتصادية الفعلية للمنتج المصنّع مع معاييره المماثلة المنصوص عليها في وثائق التصميم.
صيانةيتم إنتاج جودة المنتجات المصنعة في مراحل التداول والبيع والتشغيل والاستهلاك.
جودة المناولة والمبيعات تتكون من جودة التخزين والنقل. من المهم هنا الحفاظ على مستوى الجودة الذي تم ضمانه في الإنتاج.
الغرض من الإدارة في مرحلة الاستئنافهو تهيئة الظروف اللازمة للحفاظ على خصائص المنتجات أثناء تخزينها ونقلها وبيعها، وفقاً للخطط والمعايير والشروط الفنية الموضوعة.
معيار التقييمجودة في مرحلة التعميم والتنفيذيعمل على التأكد من أن مؤشرات جودة المنتج تتوافق مع المؤشرات المسجلة في الوثائق الفنية المصاحبة للمنتج.
في مرحلة التشغيل، يتم إجراء التقييم النهائي والأكثر اكتمالًا للمستوى الفعلي لجودة المنتج.
يعتمد الحفاظ على الجودة في التشغيل على جودة وثائق التشغيل والإصلاح ومعدات التشغيل والإصلاح وقطع الغيار وجودة العمالة لدى موظفي التشغيل والصيانة.
الغرض من الإدارة في المرحلة التشغيليةهو الاهتمام بالتشغيل الخالي من المتاعب والفعال للمنتجات المصنعة أثناء التشغيل.
معيار التقييمجودة في عمليةيعمل على التأكد من أن مؤشرات جودة المنتج تتوافق مع المؤشرات المسجلة في الوثائق الفنية المصاحبة للمنتج، أي. الاحتياجات الحقيقية التي أنشئت من أجلها.
إنتاج
للحصول على منتجات بالجودة المطلوبة، يجب إجراء العمليات التكنولوجية وفقًا للوائح الصناعية والتعليمات ذات الصلة ومتطلبات هذا المعيار والوثائق التنظيمية والمتطلبات المحددة أثناء تسجيل المنتج الطبي.
الأحكام العامة
5.1. يجب أن تتم عملية الإنتاج ومراقبتها من قبل موظفين مؤهلين.
5.2. يجب تنفيذ جميع العمليات التي تتضمن المواد والمنتجات (مثل الاستلام والحجر الصحي وأخذ العينات والتخزين ووضع العلامات والتحضير والطهي والتعبئة والشحن) وفقًا للتعليمات أو الإجراءات المكتوبة، وتسجيلها إذا لزم الأمر.
5.3. يجب فحص جميع المواد الواردة للتأكد من مطابقتها للطلب. يجب تنظيف الحاويات والتغليف ووضع العلامات عليها.
5.4. ينبغي التحقيق في حقائق الأضرار التي لحقت بالحاويات والتغليف والتي قد يكون لها تأثير سلبي على جودة المواد وتسجيلها ثم إبلاغ قسم مراقبة الجودة بها.
5.5. يجب عزل المواد الواردة والمنتجات النهائية المنتجة على الفور، إما عن طريق التخزين المنفصل أو من خلال التدابير التنظيمية، حتى يتم الحصول على إذن للاستخدام أو الشحن.
5.6. يتم قبول المنتجات الوسيطة والسائبة وفقًا للقواعد المعمول بها بالنسبة للمواد الأولية.
5.7. يجب تخزين جميع المواد والمنتجات في الظروف المناسبة التي تحددها الشركة المصنعة، وبما يضمن فصل دفعات المنتجات وتداولها في المستودع.
5.8. ولضمان عدم وجود انحرافات تتجاوز الحدود المقبولة، من الضروري التأكد من التحكم في إنتاج (إطلاق) المنتجات ومقارنتها الكمية ببيانات اللوائح الصناعية.
5.9. لا يُسمح بالعمليات المتزامنة أو المتتابعة لمنتجات مختلفة في نفس المنطقة دون الحماية من مخاطر الخلط أو التلوث المتبادل.
5.10. يجب حماية المنتجات والمواد من التلوث الميكروبي وأنواع التلوث الأخرى في جميع مراحل الإنتاج.
5.11. عند العمل مع المواد والمنتجات الجافة، يجب اتخاذ احتياطات خاصة لمنع تكون وانتشار الغبار، وخاصة عند العمل مع المواد القوية والمحسسة.
5.12. أثناء العملية التكنولوجية، يجب وضع علامة (مُلصقة) على جميع المواد والعبوات التي تحتوي على المنتجات السائبة والمعدات الرئيسية والمباني التي تشير إلى المنتج أو المادة التي يتم تصنيعها، وجرعتها (إذا لزم الأمر) ورقم الدفعة. إذا لزم الأمر، ينبغي الإشارة إلى مرحلة العملية التكنولوجية.
5.13. يجب أن تكون التسميات (الملصقات) الموجودة على العبوات أو المعدات أو المباني واضحة ولا لبس فيها وفي شكل محدد. بالإضافة إلى استخدام تسميات الحروف، يوصى باستخدام الترميز اللوني للإشارة إلى حالة المنتج (على سبيل المثال، "الحجر الصحي"، "مقبول"، "مرفوض"، "نظيف"، وما إلى ذلك).
5.14. يجب مراقبة التوصيلات الصحيحة لخطوط الأنابيب والمعدات الأخرى المخصصة لنقل المنتجات من منطقة إلى أخرى.
5.15. لا يجوز الانحراف عن التعليمات. إذا لزم الأمر، يجب الحصول على إذن كتابي للخروج عن التعليمات من الأشخاص المختصين وقسم مراقبة الجودة.
5.16. ولا يجوز دخول أماكن الإنتاج إلا للموظفين المصرح لهم بدخولها.
5.17. كقاعدة عامة، لا يُسمح بتصنيع المنتجات غير الطبية في المباني والمعدات المخصصة لإنتاج المنتجات الطبية.
منع التلوث المتبادل في التصنيع
5.18. وينبغي تجنب احتمال تلوث المواد أو المنتجات الأولية بمواد أو منتجات أخرى. أثناء الإنتاج، ينشأ خطر التلوث المتبادل العرضي من الإطلاق غير المنضبط للغبار أو الغازات أو الأبخرة أو الهباء الجوي أو الكائنات الحية الدقيقة من المواد (المنتجات) ومن الملوثات المتبقية على المعدات وملابس الأشخاص. تعتمد درجة الخطورة على نوع التلوث والمنتج المتأثر بالتلوث.
وتشمل أخطر الملوثات المواد المسببة للحساسية والمستحضرات البيولوجية التي تحتوي على كائنات حية دقيقة وبعض الهرمونات والسموم الخلوية وغيرها من المواد القوية. يعد تلوث الأدوية القابلة للحقن، وكذلك الأدوية التي يتم تناولها بجرعات كبيرة و/أو على مدى فترة طويلة من الزمن، أمرًا خطيرًا بشكل خاص.
5.19. لمنع التلوث المتبادل، ينبغي اتخاذ التدابير الفنية والتنظيمية اللازمة، على سبيل المثال:
أ) الإنتاج في مناطق مخصصة (إلزامية لمنتجات مثل البنسلين واللقاحات الحية والمستحضرات البكتيرية من الكائنات الحية الدقيقة وبعض المنتجات الطبية البيولوجية الأخرى) أو فصل دورات الإنتاج مع مرور الوقت مع التنظيف المناسب للمباني والمعدات بين الدورات؛
ب) تنظيم غرف معادلة الضغط وأجهزة العادم؛
ج) التقليل إلى أدنى حد من مخاطر التلوث الناجم عن إعادة تدوير أو إعادة إدخال الهواء غير المعالج أو المعالج بشكل غير كاف؛
د) تخزين الملابس الواقية (الخاصة) داخل مناطق إنتاج المنتجات ذات المخاطر العالية للتلوث المتبادل؛
هـ) استخدام طرق تنظيف ومعالجة عالية الكفاءة للتخلص من التنظيف غير الكافي، والذي غالبًا ما يسبب التلوث المتبادل؛
و) استخدام "أنظمة الإنتاج المغلقة"؛
و) مراقبة بقايا المنتج السابق أو عوامل التنظيف ومعدات وضع العلامات التي تشير إلى حالة النظافة.
5.20. وينبغي مراجعة فعالية التدابير الرامية إلى منع التلوث المتبادل بشكل دوري وفقا للمبادئ التوجيهية المعتمدة.
الشهادات (الاختبارات)
5.21. تهدف الشهادة (الاختبار) إلى زيادة الكفاءة التشغيلية ويتم إجراؤها وفقًا للطرق المعتمدة. ويجب توثيق نتائجها.
5.22. عند الموافقة على تنظيم صناعي أو طريقة إنتاج جديدة، يجب التحقق من مدى ملاءمتها للإنتاج الضخم. يجب إثبات أن العملية والمواد والمعدات المستخدمة يمكن أن تنتج باستمرار منتجات بالجودة المطلوبة.
5.23. مع التغيرات الكبيرة في التكنولوجيا، بما في ذلك. يجب أن تخضع أي تغييرات في المعدات أو المواد التي قد تؤثر على جودة المنتج أو إمكانية تكرار العملية لتأهيل (اختبار) العمليات ذات الصلة.
5.24. وللتأكيد المستمر على تحقيق النتائج المطلوبة، ينبغي إجراء إعادة اعتماد (اختبار) للعمليات والأساليب التكنولوجية.
المواد المصدرية
5.25. يعد توفير المواد الخام عملية بالغة الأهمية تتطلب معلومات كاملة عن الموردين.
5.26. يجب شراء المواد الأولية فقط من الموردين المعتمدين (كما هو محدد في المواصفات)، وحيثما أمكن، مباشرة من الشركات المصنعة لهذه المواد. ويجب تحديد المتطلبات الخاصة بها في مواصفات المواد الأولية المعتمدة من قبل الشركة المصنعة للدواء والمتفق عليها مع المورد. جميع القضايا المتعلقة بإنتاج ومراقبة المواد الأولية، بما في ذلك. العمل معهم، ووضع العلامات، والتعبئة والتغليف، ويجب الاتفاق على إجراءات تقديم الشكاوى والرفض بين الشركة المصنعة والمورد.
5.27. لكل عملية تسليم، يجب التحقق من سلامة الحاوية والتغليف والأختام، ومدى امتثالها لإشعار التسليم الموجود على الحاوية (العبوة).
5.28. عندما يتم توفير دفعات متعددة من المواد الأولية، يجب معاملة كل دفعة على أنها مستقلة فيما يتعلق بأخذ العينات والاختبار والموافقة على الاستخدام.
5.29. يجب وضع العلامات على المواد الخام المخزنة وفقًا لذلك (5.13). يجب أن تحتوي العلامة على المعلومات التالية على الأقل:
تعيين المنتج الأصلي ورمز المصنع؛
رقم السلسلة المخصص عند القبول؛
الحالة المادية (على سبيل المثال، "الحجر الصحي"، "الاختبار"، "مسموح به"، "مرفوض"، وما إلى ذلك)؛
تاريخ انتهاء الصلاحية أو التاريخ الذي يجب بعده إعادة الفحص.
إذا كان المستودع مجهزًا بالكامل بأجهزة الكمبيوتر، فليس من الضروري الإشارة إلى كل هذه المعلومات في الملصق.
5.30. يتم التحكم في صحة محتويات كل حزمة مع المواد المصدرية من خلال التعليمات والأساليب المناسبة. يجب وضع علامة مناسبة على عبوات المنتجات السائبة التي تم أخذ العينات منها (6.13).
5.31. في إنتاج الأدوية، يمكن استخدام المواد الخام التي لها مدة صلاحية غير منتهية الصلاحية والمعتمدة من قبل قسم مراقبة الجودة.
5.32. يجب أن يتم إصدار المواد الأولية فقط من قبل أشخاص معينين خصيصًا وفقًا لتعليمات مكتوبة، كما يجب استيفاء متطلبات دقة وزن وقياس المواد في حاويات نظيفة وملصقة عليها علامات.
5.33. يجب التحقق بشكل مستقل من كل مادة يتم صرفها، من كتلتها وحجمها. ويجب توثيق نتائج التفتيش.
5.34. يجب تخزين المواد التي تم الحصول عليها لكل سلسلة في مكان واحد، ويجب وضع علامة واضحة عليه.
المنتجات المتوسطة والسائبة
5.35. قبل البدء في أي عملية عملية، ينبغي اتخاذ التدابير للتأكد من أن منطقة الإنتاج والمعدات نظيفة وخالية من أي مواد أولية أو منتجات أو بقايا المنتج أو وثائق لا تتعلق بالعملية.
5.36. يجب تخزين المنتجات المتوسطة والسائبة في ظل الظروف المناسبة.
5.37. يجب أن تكون العمليات الحرجة معتمدة (5.21 - 5.24).
5.38. يجب توثيق تنفيذ جميع العمليات اللازمة للرقابة أثناء العملية والبيئة.
5.39. يجب تسجيل وفحص أي دليل على وجود انحرافات كبيرة في إنتاجية المنتج (الكمية) عن القيم المتوقعة.
مواد التعبئة والتغليف
5.40. يجب أن يحظى شراء وتخزين ومراقبة مواد التعبئة والتغليف البكر والمطبوعة بنفس الاهتمام الذي تحظى به المواد الخام.
5.41. ينبغي إيلاء اهتمام خاص للمواد المطبوعة. وينبغي أن يتم تخزينها في ظروف آمنة تمنع الوصول إليها من قبل أشخاص غير مصرح لهم. يجب تخزين الملصقات المقطوعة والمواد السائبة الأخرى ونقلها بشكل منفصل في حاويات مغلقة لمنع اختلاطها. يجب أن يتم إصدار إذن استخدام مواد التعبئة والتغليف فقط من قبل أشخاص معينين خصيصًا وفقًا للتعليمات المعتمدة.
5.42. يجب تعيين رقم أو علامة تعريف لكل شحنة أو دفعة من مواد التعبئة والتغليف الأولية أو المطبوعة.
5.43. يجب تدمير مواد التغليف المطبوعة أو الأولية منتهية الصلاحية أو غير الصالحة للاستخدام وتسجيل البروتوكول.
عمليات التعبئة والتغليف
5.44. يجب أن تقلل تعبئة المنتج من مخاطر التلوث المتبادل أو الخلط أو الاستبدال. لا يجوز تعبئة المنتجات من أنواع مختلفة على مقربة من بعضها البعض في حالة عدم وجود فصل مادي للمناطق.
5.45. قبل البدء بعمليات التعبئة والتغليف، يجب التأكد من أن منطقة العمل وخطوط التغليف وآلات الطباعة وغيرها من المعدات في حالة نظيفة وخالية من المواد أو المنتجات أو المستندات المتعلقة بالعمل السابق وعدم استخدامها في العملية الحالية. يجب أن يتم تنظيف خط تعبئة المنتج وفقًا لتعليمات محددة. يجب الإشارة إلى اسم المنتج المعبأ ورقم تشغيلته في كل سطر أو عملية تثبيت.
5.46. عند وصول المنتجات ومواد التعبئة والتغليف إلى منطقة التعبئة والتغليف، يجب التحقق من كميتها وصحتها ومطابقتها لتعليمات التعبئة والتغليف.
5.47. يجب أن تكون العبوة الأولية نظيفة قبل البدء بعملية التعبئة. وينبغي إيلاء اهتمام خاص لإزالة أي ملوثات (شظايا الزجاج، والجزيئات المعدنية، وما إلى ذلك).
5.48. بمجرد تعبئة المنتجات وإغلاقها، يجب أن يتم وضع العلامات في أسرع وقت ممكن. إذا لم يكن ذلك ممكنا، فيجب اتخاذ التدابير اللازمة لمنع خلط المنتج أو وضع العلامات الخاطئة عليه.
5.49. يجب مراقبة وتوثيق صحة أي عمليات طباعة (على سبيل المثال، تطبيق الرموز أو تواريخ انتهاء الصلاحية) أثناء وبعد التعبئة والتغليف. وينبغي إيلاء اهتمام خاص للعلامات اليدوية، التي ينبغي مراقبتها على فترات منتظمة.
5.50. يجب اتخاذ احتياطات خاصة عند استخدام الملصقات المقطوعة والطباعة دون اتصال بالإنترنت. لمنع تشابك المواد المطبوعة، يوصى باستخدام الملصقات الملفوفة بدلاً من الملصقات المقطوعة.
5.51. يجب مراقبة التشغيل الصحيح لقارئات الرموز الإلكترونية وعدادات الملصقات وغيرها من الأجهزة المماثلة.
5.52. يجب أن تكون العلامات على مواد التعبئة والتغليف، التي يتم تطبيقها عن طريق الطباعة أو النقش، واضحة ومقاومة للضوء (البهتان) والإزالة.
5.53. عند مراقبة عملية تعبئة المنتج عبر الإنترنت، يجب التحقق مما يلي كحد أدنى:
أ) المظهر العام للعبوة؛
ب) اكتمال العبوة؛
ج) الاستخدام الصحيح لمواد التعبئة والتغليف وفقًا لمتطلبات الوثائق الخاصة بهذا المنتج؛
د) صحة النقوش المطبوعة؛
ه) التشغيل الصحيح لأجهزة مراقبة الخط.
لا يتم إرجاع عينات المنتج المأخوذة من خط التعبئة والتغليف إلى الخط.
5.55. إذا نشأت ظروف غير متوقعة أثناء تعبئة المنتجات، فلا يمكن إعادتها إلى الإنتاج إلا بعد إجراء فحص خاص وتحقيق وبإذن من شخص لديه السلطة المناسبة. ويجب توثيق هذه الإجراءات في شكل بروتوكولات، ويجب تخزينها بالطريقة المحددة.
5.56. إذا تم تحديد تناقض كبير أو غير عادي عند مقارنة كميات المنتج السائب ومواد التعبئة والتغليف المطبوعة وعدد وحدات المنتج النهائي المستلمة، فيجب إجراء تحقيق لتحديد سبب التناقض قبل منح الإذن بتسويق المنتج.
5.57. بعد الانتهاء من عمليات التعبئة والتغليف، يجب إتلاف أي مواد تعبئة متبقية مطبوع عليها رقم التشغيلة وإعداد تقرير بذلك. يتم إرجاع مواد التغليف غير المميزة إلى المستودع وفقاً للتعليمات المعتمدة.
المنتجات النهائية
5.58. قبل إصدار تصريح البيع، يجب الاحتفاظ بالمنتجات النهائية في الحجر الصحي وفقًا للشروط التي تحددها الشركة المصنعة.
5.59. إجراءات تقييم جودة المنتجات النهائية ومتطلبات الوثائق اللازمة للحصول على إذن البيع موضحة في القسم 6.
5.60. بعد إصدار تصريح البيع، يجب تخزين المنتجات النهائية في مستودع المنتجات النهائية وفقًا للشروط التي تحددها الشركة المصنعة.
المواد المرفوضة والمعاد استخدامها والمرتجعة
5.61. يجب وضع علامات واضحة على المواد والمنتجات المرفوضة وتخزينها بشكل منفصل في المناطق المحظورة. ويجب إعادتها إلى المورد، أو إعادة تدويرها (إذا كان مسموحًا بذلك) أو تدميرها. يجب توثيق أي إجراءات يتم تنفيذها والموافقة عليها من قبل الأشخاص ذوي السلطة المناسبة.
5.62. يُسمح بإعادة معالجة المنتجات المرفوضة في حالات استثنائية، بشرط عدم وجود تدهور في جودة المنتج النهائي واستيفاء جميع متطلبات المواصفات. تتم المعالجة وفقًا للتعليمات المعتمدة بعد تقييم المخاطر المحتملة مع الوثائق اللاحقة.
5.63. لا يُسمح بإعادة استخدام كامل (أو جزء) سلسلة المنتجات التي تم إنتاجها مسبقًا بالجودة المطلوبة من خلال دمجها مع سلسلة أخرى من نفس المنتجات في مرحلة معينة من الإنتاج إلا بعد الحصول على إذن مسبق موقع من الأشخاص المسؤولين. لا يُسمح بإعادة استخدام المنتجات إلا بعد تقييم المخاطر المحتملة (بما في ذلك تأثيرها على العمر الافتراضي للدفعة) وفقًا للتعليمات المعتمدة مع تنفيذ البروتوكول.
5.64. يتم تحديد الحاجة إلى مراقبة إضافية للمنتجات النهائية التي خضعت للمعالجة، أو المنتجات التي تتضمن منتجات مصنعة مسبقًا، من قبل قسم مراقبة الجودة.
5.65. يجب تدمير المنتجات المعادة من السوق والتي فقدت الشركة المصنعة السيطرة عليها ما لم يتم التأكد من جودتها لتلبية المتطلبات المحددة. لا يمكن اتخاذ قرار إعادة البيع أو إعادة التسمية أو إعادة الاستخدام إلا بعد إجراء تحليل محدد من قبل قسم مراقبة الجودة وفقًا للتعليمات المكتوبة. في هذه الحالة، من الضروري مراعاة طبيعة المنتج وخلفيته وحالته والامتثال لشروط التخزين الخاصة والوقت الذي انقضى منذ تاريخ الإصدار. إذا كان هناك أي شك حول جودة المنتج، فلا يجوز إعادة استخدامه أو إعادة إطلاقه، ولكن يُسمح بالمعالجة الكيميائية لاستعادة المكونات النشطة. يجب توثيق جميع الإجراءات التي تم تنفيذها.
إن العامل الأكثر أهمية والذي يحدد أحيانًا عند اختيار متطلبات جودة المنتج هو شروط استخدامه أو تشغيله. ولذلك، فإن الدراسة المستمرة لهذه الظروف هي بدورها جزء مهم من التصميم والتطوير. إن معرفة شروط استخدام المنتج أو تشغيله تجعل من الممكن تحديد شروط اختباره بشكل صحيح.
في ممارسة الاختبار، في الوثائق التنظيمية والتقنية والتصميمية، يتم استخدام مفهوم عوامل التأثير الخارجي (EIF)، والتي تُفهم على أنها "ظواهر أو عمليات أو بيئات خارجية للمنتج أو مكوناته، تتميز بكميات فيزيائية تسبب أو يمكن أن تسبب التسبب في تقييد أو فقدان الحالة التشغيلية للمنتج أو انتقاله إلى الحالة المقيدة أثناء التشغيل."
إن وضع مؤشرات الجودة في تطوير وتصميم المنتجات يتم، كما هو معروف، على عدة مراحل.
الأول هو وضع متطلبات التصميم الأولية للمنتجات، والتي يتم اختيارها بناءً على نتائج تحليل المعلومات وتشمل في المقام الأول نوع (نوع، طراز) المنتج الذي يتم تطويره والمتطلبات الأساسية له - الجودة القياسية المؤشرات.
في هذه الحالة، يتم عادةً تحديد المواد والمكونات الرئيسية المستخدمة، ومبادئ تصميم التشغيل، والرسوم البيانية، والوصفات، وكذلك في بعض الحالات، الحلول التكنولوجية الأساسية. تم تحديد المتطلبات الأولية لشروط الاستخدام (التشغيل). يتم إجراء تقديرات التكلفة ووضع مبرر اقتصادي للمشروع.
يمكن تطوير المتطلبات الأولية على عدة مراحل ومن ثم تحسينها بعد الاتفاق عليها مع العميل أو عند تطويرها بمزيد من التفصيل (مشروع متقدم). ويتم توثيقها في شكل مقترحات فنية ومواصفات التصميم والتطوير والمتطلبات الفنية والمستندات المماثلة، وكذلك عند إبرام عقد التصنيع والتوريد.
إن اختيار المتطلبات الأولية هو أول وأهم قرار تصميمي في سلسلة القرارات التي تضمن في نهاية المطاف الجودة المطلوبة والسليمة للمنتجات، حيث أن الأخطاء في اختيار مؤشرات الجودة، مثل أي أخطاء في التصميم، هي الأشد خطورة والأصعب تصحيحها. صحيح. قد تضيع كل الجهود الفكرية والتكاليف الإنتاجية والمالية لضمان الجودة إذا حدث خطأ في اختيار مؤشرات الجودة وكان من المستحيل حل المشكلة. عادةً ما يؤدي تصحيح هذا الخطأ إلى تكاليف أعلى بعدة مرات من التكاليف اللازمة للاختيار الصحيح.
المرحلة الثانية هي تحديد مؤشرات الجودة الموضوعية - الخصائص المحددة لمنتج معين (الأبعاد والتصميم والتكوين وما إلى ذلك)، والتي تم تحديدها في التصميم والوثائق التكنولوجية.
المرحلة الثالثة هي فحص وضبط المؤشرات المختارة باستخدام اختبارات مختلفة.
في الختام، يمكن الإشارة إلى أن كل ما ذكر أعلاه فيما يتعلق بالتحليل عند اختيار مؤشرات الجودة ينطبق بشكل كامل ليس فقط على أي منتج مادي - المواد والمواد والآلات والسلع الاستهلاكية، وما إلى ذلك، ولكن أيضًا على المنتجات والخدمات الفكرية.
في النظرية والممارسة الحديثة لإدارة الجودة، يتم التمييز بين المراحل الخمس الرئيسية التالية:
1. اتخاذ القرارات "ماذا ننتج؟" وإعداد المواصفات الفنية. على سبيل المثال، عند إطلاق سيارة من علامة تجارية معينة، من المهم أن تقرر: "لمن هي السيارة" (لدائرة ضيقة من الأثرياء جدًا أو للمستهلك الشامل).
2. التحقق من جاهزية الإنتاج وتوزيع المسؤولية التنظيمية.
3. عملية تصنيع المنتجات أو تقديم الخدمات.
4. إزالة العيوب وتوفير معلومات التغذية الراجعة من أجل إجراء التغييرات والتحكم فيها في عملية الإنتاج لتجنب العيوب المحددة في المستقبل.
5. تطوير خطط الجودة طويلة المدى.
إن تنفيذ المراحل المذكورة مستحيل دون تفاعل جميع الإدارات والهيئات الإدارية للشركة. ويسمى هذا التفاعل بنظام إدارة الجودة الموحد. وهذا يوفر نهجا منظما لإدارة الجودة.
دعونا نفكر بمزيد من التفصيل في محتوى مراحل إدارة الجودة.
في هذه المرحلة، تعني الجودة الدرجة التي تتوافق بها منتجات أو خدمات الشركة مع مواصفاتها الداخلية. ويسمى هذا الجانب من الجودة بجودة المطابقة.
في المرحلة الثانية، يتم تقييم جودة التصميم. قد تلبي الجودة المتطلبات الفنية للشركة لتصميم المنتج، إلا أن التصميم نفسه يمكن أن يكون بجودة عالية أو منخفضة.
وفي المرحلة الثالثة تعني الجودة الدرجة التي يلبي بها عمل أو أداء خدمات (منتجات) الشركة الاحتياجات الحقيقية للمستهلكين.
أن تكون منتجات الشركة مطابقة للمواصفات الداخلية (المرحلة الأولى)؛ يمكن أن يكون تصميم المنتج نفسه متميزًا (المرحلة الثانية)؛ قد لا تكون الخدمة أو المنتج مناسبًا لتلبية الاحتياجات المحددة للمستهلك. لقد نظرنا إلى محتوى ثلاث مراحل أساسية، وهي على نفس القدر من الأهمية. أي خلل في أي منها يمكن أن يخلق مشاكل في الجودة.
يعتمد نظام إدارة جودة المنتج على فئات الإدارة المترابطة التالية: الكائن، الأهداف، العوامل، الموضوع، الأساليب، الوظائف، الوسائل، المبدأ، النوع، نوع المعايير، إلخ.
تُفهم إدارة جودة المنتج على أنها عملية ثابتة ومنهجية وهادفة للتأثير على العوامل والظروف على جميع المستويات، مما يضمن إنشاء منتجات ذات جودة مثالية واستخدامها الكامل.
يتضمن نظام إدارة جودة المنتج الوظائف التالية:
1. وظائف الإدارة الإستراتيجية والتكتيكية والتشغيلية.
2. وظائف اتخاذ القرار، وإجراءات الرقابة، والتحليل والمحاسبة، ووظائف المعلومات والرقابة.
3. الوظائف متخصصة ومشتركة لجميع مراحل دورة حياة المنتج.
4. وظائف الإدارة وفقا للعوامل والظروف العلمية والفنية والإنتاجية والاقتصادية والاجتماعية.
تشمل الوظائف الإستراتيجية ما يلي:
التنبؤ وتحليل مؤشرات الجودة الأساسية؛
تحديد اتجاهات التصميم والعمل الهندسي؛
تحليل النتائج المحققة لجودة الإنتاج؛
تحليل المعلومات عن طلب المستهلك.
الميزات التكتيكية:
إدارة الانتاج؛
الحفاظ على مستوى مؤشرات الجودة المحددة؛
التفاعل مع الأشياء الخاضعة للرقابة والبيئة الخارجية.
نظام إدارة جودة المنتج عبارة عن مجموعة من هيئات الإدارة والأشياء الإدارية والأنشطة والأساليب والوسائل التي تهدف إلى إنشاء وضمان والحفاظ على مستوى عالٍ من جودة المنتج.
تكاليف الجودة وتصنيفها
تقليديا، تُفهم تكاليف الجودة على أنها تكاليف ضمان جودة المنتج أو الخدمات المصنعة المقدمة لتلبية رغبات المستهلك المحددة، والتي يجب عليه دفعها. لذلك، لا يزال هناك رأي واسع النطاق مفاده أن المستهلك "يجب أن يدفع مقابل الجودة"، وبالتالي تعويض التكاليف الإضافية التي تتحملها الشركة المصنعة لضمان هذه الجودة. تعتمد وجهة النظر هذه على النهج التقليدي لمشكلة الجودة.
يتم عرض هيكل الدخل وتكاليف الشركة المصنعة للمنتج ومكان تكاليف الجودة فيها في الشكل. 5.2.
أرز. 5.2. الهيكل العام لإيرادات الشركة وتكاليفها تم تجميعها من: [Gludkin et al., 1999, p. 284].
استنادا إلى المفاهيم النظرية التي تم عرضها بإيجاز أعلاه، عند تحليل تكاليف الجودة، من المعتاد تقسيم إجمالي التكاليف المرتبطة بالجودة إلى تكاليف الامتثالو الخسائر الناجمة عن عدم الامتثال(الشكل 5.3). ويقدم أوماشونو وروس التصنيف التالي لهذه التكاليف.
تكاليف الإجراءات الوقائية (ج1) (تكلفة الوقاية)- هي تكاليف الشركة المصنعة عن أي إجراءات لمنع حدوث التناقضات والعيوب، بما في ذلك تكاليف تطوير وتنفيذ وصيانة نظام الجودة الذي يقلل من مخاطر حصول المستهلك على منتج أو خدمة لا تلبي توقعاته.
تكاليف التفتيش(ج2) (تكلفة تقييم)- هي التكاليف التي يتحملها المصنع لاكتشاف التناقضات والعيوب التي تنشأ أثناء عملية التصميم والإنتاج أو تقديم الخدمات، بهدف التخلص منها قبل وصول المنتج إلى المستهلك أو اكتمال الخدمات المقدمة له. من الواضح أن الأخطاء في إنتاج المنتجات أو تقديم الخدمات تحدث مع كل مصنع. من أجل تقليل عدد الأخطاء التي تمثل عدم الامتثال للمواصفات (العيوب) أو متطلبات المستهلك، تضطر الشركة المصنعة إلى إنشاء نظام للكشف عنها، وإنفاق جزء من أموالها على التحكم في الوارد والتيار والمخرجات للمنتجات، بما في ذلك وكذلك تكاليف شراء وصيانة الأجهزة ومعدات الاختبار اللازمة. هذه تكاليف التشغيل أي مصنع(وأكثر من ذلك في سياق نظام إدارة الجودة الحالي القائم على أفكار إدارة الجودة الشاملة) هي حتمي.غالبًا ما يطلق عليها تكاليف تقييم الجودة، لأنها تتضمن أيضًا اختبارات قبول المنتجات النهائية، والتي تكون إلزامية لكل مصنع لتقييم موثوقيتها قبل تسليم المنتج إلى المستهلك.
وفيما يلي سوف نسمي هذا النوع من التكلفة تكاليف التفتيش أو مراقبة الجودة،بما في ذلك تكاليف تطوير وتنفيذ نظام التحكم، والمدفوعات للمفتشين والمشغلين الذين يقومون بالمراقبة، وسعر أدوات القياس أو استهلاكها، أي تكاليف الشركة المصنعة للفحص في أي مرحلة من مراحل دورة حياة المنتج.
المجموعتان التاليتان من التكاليف هما بالأحرى خسائر للشركة المصنعة. العيب الداخلي هو العيب الذي تكتشفه الشركة المصنعة (قبل طرح المنتج في السوق)؛ العيب الخارجي هو العيب الذي يكتشفه المستهلك بعد شراء المنتج.
التكاليف المرتبطة بالعيوب الداخلية(ج3)، - تكاليف الشركة المصنعة لإزالة العيوب التي اكتشفها أثناء الإنتاج أو تقديم الخدمة، مع مراعاة تكاليف إنتاج منتجات عالية الجودة لتحل محل المنتجات المرفوضة. وتشمل هذه، على سبيل المثال، تكاليف إنتاج المنتجات أو تقديم الخدمات التي تبين، نتيجة للتفتيش، أنها غير مطابقة (العيوب المكتشفة)؛ تكاليف المعالجة اللاحقة وتصحيح العيوب، وتعديل التصميم أو التصميم، وإعادة فحص التصحيحات التي تم إجراؤها، وتكاليف فرز 100٪ لمجموعة من المنتجات في حالة وجود نتائج سلبية لمراقبة الجودة العشوائية، والخسائر الناجمة عن تخفيض سعر منتجات منخفضة الجودة، وما إلى ذلك. هذه التكاليف التي يتحملها المصنع هي تكاليفه الفردية، أي التكاليف التي لن يتمكن من إعادتها في المستقبل على حساب المستهلك إذا كانت هناك منافسة عالية بما فيه الكفاية في السوق. ويعتمد مستوى هذه التكاليف على الشركة المصنعة على عدد حالات عدم المطابقة التي حددها المستهلك والمرحلة من دورة حياة المنتج التي تم فيها اكتشاف حالات عدم المطابقة (العيوب)، وتزداد تكلفة التصحيح وفقا لمبدأ زيادة عشرة أضعاف في التكاليف.
التكاليف المرتبطة بالعيوب الخارجية(ج4)، - التكاليف الإضافية التي تتحملها الشركة المصنعة لتصحيح التناقضات في المنتج المحول إلى المستهلك أو الخدمات المقدمة له مقارنة بما وعدت به الشركة المصنعة (مضمونة).
وتشمل هذه التكاليف، على سبيل المثال، ما يلي: تكاليف إصلاحات الضمان؛ للتحقيق في أسباب الفشل؛ لاستبدال المنتجات التي لا تعمل خلال فترة الضمان؛ خسارة في السعر بسبب المنتجات ذات الجودة المنخفضة المكتشفة خارج المؤسسة، وما إلى ذلك.
يتم تحديد هذا العيب من قبل المستهلك نفسه، وبالتالي، بالإضافة إلى التأثير المباشر على مستوى تكاليف الشركة المصنعة، فإنه لا يشمل فقط الاستبدال المجاني للمنتجات والخدمات منخفضة الجودة بمعادلاتها عالية الجودة، تليها مراقبة إضافية من أجل التعرف على أسباب عدم الامتثال، ولكن أيضا العقوبات. بالإضافة إلى ذلك، في نظر المستهلك، يعاني المورد من ضرر غير متناسب في الصورة، والذي، وفقًا لـ "تأثير جبل الجليد"، يمكن أن يجلب له خسائر لا يمكن التنبؤ بها، بما في ذلك خسارة السوق. ولذلك فإن وجود التكاليف المرتبطة بالعيوب الخارجية ومستوىها المرتفع نسبيا يشكل خطورة خاصة على الشركة.
أرز. 5.3. المكونات الرئيسية لتكاليف الجودة المصدر: [Gludkin et al., 1999, p. 285].
في الجدول يوضح الشكل 5.1 تقريبًا الأجزاء "المرئية" و"غير المرئية" من التكاليف المرتبطة بالجودة. طاولة يوضح الشكل 5.2 المجموعات التقريبية من الفوائد التي حصلت عليها الشركة التي تمكنت من تنظيم الرقابة الفعالة على التكاليف المتعلقة بالجودة. في الوقت نفسه، وفقا لمؤلفي المخطط، فإن الجزء المرئي يمثل حوالي 10٪ فقط من التكاليف المقابلة، و 90٪ هو الجزء غير المرئي، وهو أمر أكثر صعوبة في تقديره.
هذا هو الشكل المناسب لعرض هيكل التكلفة. ويعتقد العديد من المسؤولين التنفيذيين في الشركات أن الجزء المرئي من جبل الجليد هو الذي يحدد التكاليف الإجمالية والخسائر المرتبطة بالجودة الرديئة. وهذا مفهوم خاطئ عميق. إذا تم تقييم التكاليف الخفية والتحكم فيها وخفضها، فيمكن للشركة الحصول على فوائد كبيرة، كما هو موضح في الجدول. 5.2.
من بين أنواع التكاليف المذكورة أعلاه، يجب أن تحظى التكاليف الوقائية (C1) بالأولوية القصوى، حيث أن منع العيوب والأخطاء أرخص بكثير من تصحيحها. ترتبط تكاليف منع الأخطاء وتصحيح عواقبها والاستجابة للعيوب التي حددها المستهلك وفقًا لـ "قاعدة 1:10:100" وهي موضحة في الشكل. 5.4.
الجدول 5.1-فيض من تكاليف الجودة
الجزء المرئي من تكلفة جبل الجليد | |
العيوب (العيوب) التي تم تحديدها النفايات الإضافية تكاليف إعادة صياغة المنتجات المعيبة عمليات التفتيش (المراقبة) للنتائج العوائد من العملاء الوفاء بالتزامات الضمان ضمان الجودة | |
الجزء غير المرئي من تكلفة جبل الجليد | |
منع حالات عدم المطابقة | رقابة جودة |
مراجعة وتحليل المشاريع | مراقبة الموردين |
برامج عيب صفر | السيطرة الواردة |
تدريب الموردين | قبول المنتج |
تقييم الموردين | تحكم العملية |
مراجعة المواصفات | التفتيش على ظروف العمل |
عمليات تدقيق الجودة | مراقبة جودة العمل |
فنية وقائية | اختبار المنتج |
خدمة المعدات | السيطرة على التكاليف |
التغييرات الهندسية | معدات |
المسؤولية عن المنتجات | |
زيادة التكاليف العامة | |
زواج داخلي | الزواج الخارجي |
التوقف | علاقات المستهلك |
التغييرات الهندسية | التغيير في المستهلك |
لوازم إضافية | سلوك |
تكاليف وضعهم | خدمة اضافية |
عمليات التفتيش المتكررة | المسؤولية عن المنتجات |
فقدان حصة السوق | |
تأخير التسليم |
جمعتها: .
وهذا يعني أنه يمكن منع خسارة 100 وحدة بسبب المنتجات المعيبة التي يتم توفيرها للعملاء إذا تم اكتشافها وتصحيحها داخليًا، بتكلفة 10 وحدات فقط. ومع ذلك، من خلال إنفاق 1 فقط على التدابير الوقائية، يمكن للشركة تجنب العيوب، وبالتالي تكاليف تصحيحها والخسائر المرتبطة بشكاوى المستهلكين.
العائد على تكاليف الجودة.لا أحد يشك حاليًا في أنه من بين جميع مكونات تكاليف الجودة يتم أخذها بعين الاعتبار
سيتم إرجاع تكاليف الشركة المصنعة للإجراءات الوقائية ج 1، المدرجة في تكلفة المنتج كجزء من التكلفة الإجمالية ج، إلى الشركة المصنعة بعد بيع منتج عالي الجودة. وفي الوقت نفسه، لا يوجد ضمان لسداد تكاليف فحص C 2. وجهة النظر التقليدية هي أن تكاليف الفحص هي أيضًا تكلفة على الشركة المصنعة، على الرغم من إمكانية تجنبها. إذا تمكن المنافسون من تنظيم العملية التكنولوجية بحيث لا تكون هذه التكاليف إلزامية بالنسبة لهم، فستضطر الشركة إلى تعويض التكاليف ج 2 وليس من السعر.
الجدول 5.2 -الفوائد المرتبطة بالتحكم في تكاليف الجودة
فوائد | ||
يتم تخفيضها | تتزايد | تتحسن |
زمن دوران المخزون | العائد على الأصول | العلاقات مع الموردين |
مهلة | العائد على الاستثمار | علاقات المستهلك |
حان الوقت لجلب المنتج إلى السوق | مقياس اقتصادي | منحنى التعلم |
وقت دوران رأس المال | أداء | الجدولة |
مدة عمليات العمل | ||
حجم المنتجات النهائية | ||
مساحة في المستودعات لتخزين الإمدادات | ||
حجم الإخراج المطلوب | ||
تنظيم وقت العمليات | ||
نقل المنتجات النهائية | ||
مواصلات |
جمعتها:
أرز. 5.4. "القاعدة 1:10:100" فيما يتعلق بالتكاليف المرتبطة بالجودة
تكنولوجيا نشر وظائف الجودة (QFD - نشر وظيفة الجودة) -هذا هو اتجاه تطوير رغبات المستهلك بناءً على وظائف وعمليات أنشطة ضمان الجودة للشركة في كل مرحلة من مراحل دورة حياة المنتج الذي تم إنشاؤه حديثًا.
الفكرة الأساسية للتكنولوجيا QFDيكمن في فهم أن هناك فرقًا كبيرًا بين خصائص المستهلك ("مؤشرات الجودة الفعلية" في مصطلحات ك. إيشيكاوا) ومعلمات المنتج المقيسة في المعايير والمواصفات الفنية ("مؤشرات الجودة المساعدة" في مصطلحات ك. إيشيكاوا). تعد مؤشرات الجودة المساعدة مهمة بالنسبة للشركة المصنعة، ولكنها ليست مهمة دائمًا بالنسبة للمستهلك. تكنولوجيا QFDيسمح لك بتحويل مؤشرات جودة المنتج الفعلية إلى متطلبات فنية للمنتجات والعمليات والمعدات.
في الصميم QFD يكمن "ملف تعريف الجودة" - وهو النموذج الذي اقترحه ن. كانو، والذي يعتمد على ثلاثة مكونات:
- 1) الجودة الأساسية؛
- 2) الجودة المطلوبة.
- 3) الجودة المطلوبة.
ملف الجودة الأساسي - مجموعة من معايير جودة المنتج التي يعتبر وجودها إلزاميًا من قبل المستهلك.
ملف الجودة المطلوب - مجموعة من المؤشرات التي تمثل الخصائص التقنية والوظيفية للمنتج (على سبيل المثال، مستوى استهلاك البنزين في السيارة)؛ عادة ما يتماشى مع متوسط السوق.
ملف الجودة المطلوب - هذه مجموعة من معلمات الجودة التي تمثل قيمًا غير متوقعة للمنتج المقترح للمستهلك.
العناصر والأدوات الأساسية كفد:
- o توضيح متطلبات المستهلك؛
- o ترجمة متطلبات المستهلك إلى خصائص المنتج العامة (معلمات الجودة)؛
- o إبراز العلاقة بين "ماذا" و"كيف"، أي. ما هي المساهمة التي تقدمها خاصية (كيف) هذا المنتج أو تلك في تلبية رغبات المستهلك (ماذا)؛
- o اختيار الهدف، أي. ومعايير الجودة التي تحدد القدرة التنافسية؛
- o إنشاء (استنادًا إلى نتائج استطلاع رأي المستهلكين) تصنيف لأهمية مكون "ماذا"، وبناءً على هذه البيانات، تحديد تصنيف أهمية مكون "كيف".
المكونات الرئيسية QFDتظهر في الشكل. 8.7, يطلق عليه اسم "بيت الجودة" ("بيت الجودة").
أرز. 8.7. أداةQFD ""بيت الجودة""
"بيت الجودة" يعرض العلاقة بين مؤشرات الجودة الفعلية (خصائص المستهلك) والمؤشرات المساعدة (المتطلبات الفنية).
تكنولوجيا QFD يسمح لك بتطوير خطط الجودة التي تركز على تلبية متطلبات العملاء.
تحليل FMEA
تحليل FMEA(تحليلات تأثير وضع الفشل) هي تقنية لتحليل إمكانية حدوث العيوب وتأثيرها على المستهلك. يتم إجراء تحليل FMEA بشكل أساسي للمنتجات والعمليات قيد التطوير من أجل تقليل المخاطر التي يتعرض لها المستهلك من العيوب المحتملة.
يعد تحليل FMEA أحد التقنيات القياسية لتحليل جودة المنتجات والعمليات باستخدام النماذج القياسية لعرض نتائج التحليل وقواعد تنفيذها.
يتيح لك هذا النوع من التحليل الوظيفي تقليل التكاليف وتقليل مخاطر العيوب، ويجعل من الممكن تحديد العيوب التي تشكل أكبر خطر على المستهلك بالضبط، وتحديد أسبابها المحتملة، وتطوير الإجراءات التصحيحية للقضاء على العيوب حتى قبل ظهورها و وبالتالي منع تكاليف تصحيح العيوب.
عادةً ما يتم إجراء تحليل FMEA لعملية الإنتاج في الشركة المصنعة من خلال تخطيط الإنتاج أو خدمات إدارة الجودة بمشاركة الأقسام المتخصصة المقابلة للشركة المصنعة، وإذا لزم الأمر، المستهلك. يبدأ إجراء تحليل FMEA لعملية الإنتاج في مرحلة الإعداد الفني للإنتاج وينتهي قبل تركيب معدات الإنتاج. هدف FMEA-تحليل عملية التصنيع - ضمان تلبية جميع متطلبات الجودة لعملية التصنيع والتجميع عن طريق إجراء تغييرات على خطة العملية لأنشطة العملية عالية المخاطر.
مراحل تحليل FMEA:
- 1) بناء النماذج المكونة والهيكلية والوظيفية والتدفقية لموضوع التحليل؛
- 2) دراسة النماذج، ويتم خلالها تحديد ما يلي:
- س العيوب المحتملةلكل عنصر من عناصر نموذج الكائن المكون. وترتبط هذه العيوب عادة إما بفشل عنصر وظيفي (تدميره، كسره، الخ)، أو بأداء العنصر غير الصحيح لوظائفه المفيدة (فشل في الدقة، الأداء، الخ) أو بوظائف العنصر الضارة. كخطوة أولى، يوصى بإعادة فحص تحليل FMEA السابق أو تحليل المشكلات التي نشأت خلال فترة الضمان. ومن الضروري أيضًا مراعاة العيوب المحتملة التي قد تنشأ أثناء النقل والتخزين، وكذلك التغيرات في الظروف الخارجية (الرطوبة، الضغط، درجة الحرارة)،
- س الأسباب المحتملة للعيوب ،
- س العواقب المحتملة للعيوب بالنسبة للمستهلك؛نظرًا لأن كل العيوب قيد النظر يمكن أن تسبب سلسلة من الإخفاقات في الكائن، عند تحليل العواقب، يتم استخدام النماذج الهيكلية ونماذج التدفق للكائن،
- س إمكانية مراقبة حدوث العيوب.يتم تحديد ما إذا كان من الممكن تحديد الخلل قبل ظهور العواقب نتيجة لإجراءات المراقبة والتشخيص وما إلى ذلك المنصوص عليها في الكائن.
لتقييم كل من العيوب التي تم تحديدها، يتم استخدام ما يلي: خوارزمية الحساب:
- 1) بناءً على تقييمات الخبراء، يتم تحديد المعلمات التالية التي تميز الخلل:
- أ) معلمة شدة العواقب على المستهلك (ب).وعادة ما يتم تصنيفها على مقياس من 10 نقاط؛ يتم إعطاء أعلى الدرجات للحالات التي تستلزم فيها عواقب الخلل مسؤولية قانونية،
- ب) معلمة تكرار حدوث الخلل (A).يشار إليها على مقياس من 10 نقاط؛ يتم إعطاء أعلى الدرجات عندما يكون تكرار حدوث النتيجة 1 / 4 وما فوق،
- الخامس) معلمة احتمال عدم اكتشاف الخلل (E).مبينة على مقياس الخبراء المكون من 10 نقاط؛ وتعطى أعلى الدرجات للعيوب "الخفية" التي لا يمكن تحديدها قبل حدوث العواقب؛
- 2) محسوبة معلمة أولوية مخاطر المستهلك (CR2)كمنتج للمعلمات L، الخامس، إي.معامل ص>2من الناحية النظرية يمكن أن يكون في النطاق من 1 إلى 1000؛ وبناء على ذلك، كلما زاد ارتفاعه، كلما كان الفشل أكثر خطورة. توضح هذه المعلمة العلاقات بين أسباب العيوب؛ العيوب ذات أعلى معامل خطورة (RPZ> 100...120) يجب التخلص منها أولاً.
يتم إدخال نتائج التحليل في "جدول تحليل FMEA للكائن"، والذي يظهر في شكل رسم تخطيطي في الشكل. 8.8.
أرز. 8.8.
لمكونات الكائن مع المعلمة PP1 يتم وضع أكثر من 100...120 خطة عمل تصحيحية، تشمل:
- o التسلسل والتوقيت والفعالية من حيث التكلفة لتنفيذ هذه الأنشطة؛
- o المسؤولون عن تنفيذ كل حدث ومؤديه المحددين؛
- o موقع الأحداث (الوحدة الهيكلية)؛
- o مصدر تمويل الحدث. يتم تنفيذ التدابير التصحيحية في تسلسل معين. ضروري:
- 1) استبعاد سبب العيب، أي. عن طريق تغيير التصميم أو العملية، تقليل احتمال حدوث خلل (تنخفض المعلمة L)؛
- 2) منع حدوث الخلل، أي. باستخدام التحكم الإحصائي، منع حدوث خلل (في هذه الحالة، يتم تقليل المعلمة L)؛
- 3) تقليل تأثير الخلل على العميل أو العملية اللاحقة، مع مراعاة التغيرات في التوقيت والتكاليف (في نفس الوقت، يتم تقليل المعلمة ب)؛
- 4) زيادة موثوقية اكتشاف الخلل، وتسهيل تحديد الخلل والإصلاح اللاحق (في نفس الوقت المعلمة ه).
لتحسين جودة العملية أو المنتج، قد تشمل التدابير التصحيحية ما يلي: تغيير هيكل الكائن (التصميم، الرسم التخطيطي، وما إلى ذلك)؛ تغيير عملية عمل الكائن (تسلسل العمليات والانتقالات، محتواها، وما إلى ذلك)؛ تحسين نظام إدارة الجودة في المؤسسة.
وبعد اتخاذ التدابير التصحيحية، تتم إعادة حساب المعلمة R.P.Z.إذا لم يكن من الممكن تخفيضها إلى الحدود المقبولة (منخفضة المخاطر). (RPZ< 40) أو متوسطة الخطورة (RPZ< 100)))، ويتم وضع إجراءات تصحيحية إضافية وتكرار الخطوات السابقة.
تحليل FMEAيمكن استخدامها في مختلف الصناعات. على وجه الخصوص، يتم استخدامه على نطاق واسع في صناعة السيارات، حيث يتم تضمينه كملحق في المعايير إدارة الجودة 9000.
أساس جميع أنظمة إدارة الجودة هو "حلقة الجودة". وفقًا لمعيار ISO 8402، تعد "حلقة الجودة" نموذجًا مفاهيميًا للأنشطة المترابطة التي تؤثر على الجودة في مراحل مختلفة بدءًا من تقييم الاحتياجات وحتى تقييم الرضا. وتتضمن 11 مرحلة أو مرحلة من دورة حياة المنتج (الأرز)، ويجب إجراء تقييم الجودة في كل منها.
ومن الناحية العملية، يتم أخذ المراحل التالية من دورة حياة المنتج (LPC) في الاعتبار، والتي يتم من خلالها ضمان جودته:
1. ضمان جودة التسويق.
ينبغي للتسويق:
أ) إنشاء نظام للبحث ومعالجة وتحليل المعلومات حول المتطلبات التي تفرضها البيئة الخارجية (المستهلكون والمجتمع) على المنتجات والمنظمات. يجب أن تكون المؤشرات الرئيسية لجودة المعلومات التسويقية هي اكتمالها وموثوقيتها وأهميتها.
ب) تحديد وجود حاجة حالية أو مستقبلية يمكن أن تكون وسائلها منتجًا (خدمة) محددة وصياغة متطلبات المستهلك.
يمكن أن يكون أساس تنفيذ المرحلة التالية من دورة الحياة هو الوصف العام للمنتج، بما في ذلك الجوانب التالية:
· معلمات التشغيل (شروط الاستخدام، والموثوقية، وما إلى ذلك)؛
· تفضيلات المستهلك فيما يتعلق بالتصميم والخصائص الحسية للمنتجات؛
· متطلبات التعبئة والتغليف.
· إجراءات ضمان جودة المنتج أثناء التشغيل.
· القيود والمعايير القانونية القائمة.
يتم ضمان المستوى المناسب لجودة العمل المذكور أعلاه من خلال:
1) تطوير نظام الإجراءات الموثقة لجمع ومعالجة وتحليل البيانات؛
2) تخطيط العمل مع المراجعة الدورية للخطط وتعديلها (إذا لزم الأمر)؛
3) إسناد أداء العمل إلى موظفين مؤهلين تتوفر لديهم الوسائل اللازمة تحت تصرفهم.
2. الجودة في تطوير المنتجات.
يجب أن تضمن مرحلة تطوير المنتج من دورة الحياة ترجمة معلمات المنتج الأولية الواردة في الوصف المقدم من المسوقين إلى لغة المتطلبات الفنية للمواد والتصميم والعمليات التكنولوجية.
يتم ضمان جودة التصميم من خلال:
1) تطوير وتنفيذ برنامج التصميم، بما في ذلك معالم تقييم التصميم في كل مرحلة من مراحل البرنامج. تخضع نتائج التقييم والتحليل للتسجيل والتفكير في المواصفات والرسومات الفنية؛
2) إشراك ممثلي مختلف أقسام المنظمة في تحليل المشروع؛
3) الموافقة على جميع الوثائق التي تشكل أساس المشروع على مستويات الإدارة المناسبة المسؤولة عن إنتاج المنتجات.
3. جودة الخدمات اللوجستية
المواد الخام واللوازم والمكونات المشتراة لها تأثير مباشر على جودة المنتج.
يتم ضمان جودة العرض من خلال التدابير التالية:
1) تطوير وتنفيذ برنامج التوريد الذي يحتوي على:
· متطلبات أوامر الشراء.
· اتفاق ضمان الجودة؛
· الاتفاق على طرق التحقق.
· خطط مراقبة القبول.
· إجراءات مراقبة الوارد.
2) إجراءات حل المنازعات المتعلقة بجودة التوريدات.
3) تنظيم العمل على استلام وتخزين وإصدار وضمان سلامة المواد.
4. ضمان الجودة أثناء الإنتاج.
يتم ضمان جودة الإنتاج من خلال التدابير التالية:
1) تخطيط عمليات الإنتاج، موثقة بالتفصيل في تعليمات العمل.
2) الرقابة الفنية على عمليات الإنتاج.
3) خلق الظروف التي تستبعد إمكانية تلف المواد والمنتجات شبه المصنعة والمنتجات أثناء الإنتاج (التخزين المناسب والحماية والحركة).
4) فحص ومعايرة واختبار المعدات والأدوات والملحقات.
5. ضمان الجودة بعد إنتاج المنتجات.
بادئ ذي بدء، نحن نتحدث عن التعبئة والتغليف والتركيب والصيانة.
يتم ضمان الجودة في هذه المراحل من دورة الحياة من خلال:
1) التخطيط لجميع العمليات.
2) تهيئة الظروف التي تستبعد إمكانية تلف المنتجات قبل شحنها إلى المستهلك أو إلى شبكة التوزيع وأثناء عمليات التحميل والتفريغ.
3) الوثائق المصاحبة للمنتجات مكتوبة بشكل جيد.
4) فحص واختبار الأجهزة والمعدات الأخرى المستخدمة أثناء التثبيت.
5) تنسيق الالتزامات المتبادلة بين البائعين والمستهلكين.
هيكلة وظيفة الجودة (QF) هي منهج منظم لتطوير متطلبات ورغبات المستهلكين من خلال تحسين الأنشطة وأداء المسؤوليات في المنظمة من خلال نشر وظائفها وعملياتها لضمان إنشاء المؤسسة في كل مرحلة من دورة حياة المشروع منتجات بهذه الجودة التي من شأنها ضمان النتيجة النهائية، وتلبية توقعات المستهلك. يضمن التطوير التوفير المستمر لمنتجات عالية الجودة.
تم استخدام طريقة SFC لأول مرة في أحواض بناء السفن ميتسوبيشي كوبي في عام 1972، وفي الولايات المتحدة الأمريكية تم استخدامها من قبل فورد وزيروكس. وقد تم اعتماد هذا النهج لاحقًا من قبل العديد من الشركات المعروفة. اسم QFD (نشر وظائف الجودة)هي ترجمة من اليابانية وتعني تطوير خصائص المنتج. تعتمد هذه الطريقة إلى حد كبير على الحدس وتركز على تطوير قائمة أولويات لأهداف تطوير المنتج. الأداة الرئيسية لـ QFK هي نظام المصفوفات الذي يسمى "بيت الجودة" QH (دار الجودة).في التين. يوضح الشكل 2.15 منزلًا عالي الجودة "مفككًا" إلى مصفوفات منفصلة.
يعرض "بيت الجودة" العلاقة بين مؤشرات جودة المستهلك والمؤشرات الفنية (المتطلبات) للمنتجات.
تحتوي مصفوفة "بيت الجودة" على إجابات للأسئلة التالية:
- من هو المستهلك؟ (المصفوفة 1).
- ما هي متطلبات العملاء؟ (المصفوفة 1).
- كيف سيتم تلبية متطلبات المستهلك؟ (المصفوفة 2).
من؟من المفيد أن نجيب أولاً على السؤال التالي: "من سيستفيد من التطوير الناجح لمنتج أو خدمة أو عملية؟"
بمجرد تحديد المستهلك، السؤال التالي هو "ماذا؟".ويمكن الحصول على الإجابة من خلال إجراء مقابلة أو استبيان، وكذلك بناءً على معارف وتصورات أعضاء فريق مؤسسة قطر. أسئلة "ماذا؟" يجب أن يتم تنظيمها بطريقة تحدد أولاً الاحتياجات الرئيسية.
كيفيتعلق هذا السؤال بمؤشرات المنتجات والخدمات والعمليات الجاري تطويرها. المصفوفات التي تجيب على الأسئلة "ماذا؟" وكيف؟" (المصفوفة 4) يتم الحصول عليها باستخدام أدوات الجودة، وكذلك الإجابة على السؤال: “ما هو مستوى المتطلبات الفنية لتحقيق رضا العملاء؟”
سؤال "لماذا؟"يسمح لنا بتحديد موقف المستهلكين تجاه هذه المنتجات والخدمات والعمليات مقارنة بتلك المماثلة التي يمثلها المنافسون. تحدد المصفوفة المركزية 3 العلاقات بين متطلبات العملاء وأهداف المؤسسة.
باستخدام الأسئلة "ماذا؟" و لماذا؟" مقارنة احتياجات المستهلكين وأنشطة المنافسين (المصفوفة 5). تعكس مصفوفات "بيت الجودة" الموجودة أدناه التكاليف ومعايير المستوى لمقارنة خصائص هذا المنتج ومنتجات المنافسين (المصفوفتان 6 و 7). الجدول النهائي محدد للغاية بشأن الإجراءات التي يجب اتخاذها وكم ستكلف (المصفوفة 8).
الجانب المركزي لـ "بيت الجودة" هو متطلبات المستهلك. المعلومات حول المنافسين الواردة في المنزل
أرز. 2.15. يمكن لمصفوفة "بيت الجودة" تحديد أولويات الموارد وتلخيص الخبرات والمعلومات الموجودة (المصفوفة 9). هذا يسمح لك بتحديد الأنشطة. إذا تم التعامل مع "بيت الجودة" بشكل منهجي، فسوف يقوم بتنظيم المعلومات، وتوفير أساس لتحليل الحساسية، وتوفير الوثائق التي تسهل تنفيذ التغييرات.
دعونا نفكر في عملية نشر وظيفة الجودة باستخدام مثال إنشاء مطحنة منضدية بمحرك كهربائي للطحن الخشن لمواد الحبوب وإنتاج الأعلاف المختلطة. وفقًا لطريقة SFC، يجب تطوير متطلبات المستهلك وتحديدها على مراحل - بدءًا من أبحاث ما قبل الاستثمار وحتى إعداد ما قبل البيع.
المرحلة الأولى - توضيح وتوضيح متطلبات المستهلك. يقوم المستهلك بصياغة رغباته، كقاعدة عامة، في شكل مجرد، على سبيل المثال، "أثاث مريح" أو "هاتف خفيف". بالنسبة له، هذه الطريقة للتعبير عن احتياجاته أمر طبيعي تماما. ولكن هذا لا يكفي للمهندسين والمصممين والمصممين، بل يحتاجون إلى تحديد الأبعاد والمواد ومتطلبات معالجة السطح والوزن المسموح به بوضوح، وما إلى ذلك.
تتمثل مهمة الشركة المصنعة في ترجمة متطلبات العميل ("الصوت") إلى خصائص هندسية للمنتج باستخدام طرق مختلفة. وبالتالي، يتم توسيع متطلبات "المطحنة عالية الجودة" إلى متطلبات "التشغيل متعدد الأوضاع"، و"مدة خدمة الضمان"، ومن ثم إلى مؤشرات محددة، على سبيل المثال، "وضعان للتشغيل"، و"مدة خدمة الضمان للمنتج". أربع سنوات على الأقل"، وما إلى ذلك. بعد ذلك، يمكن للشركة المصنعة الإجابة على السؤال، ما الذي يجب القيام به لتلبية توقعات المستهلك؟
ترد قائمة متطلبات المستهلك للمطحنة في المصفوفة 1 (انظر الشكل 2.15).
المرحلة 2 - تصنيف متطلبات المستهلك. بالنسبة للتصنيف، من الضروري تقييم تقييمات متطلبات المستهلك، والتي يتم تحديدها في المرحلة 1. متطلبات المستهلك دائمًا متناقضة، لذلك من المستحيل إنشاء منتجات تلبي جميع متطلبات المستهلك. من الضروري أن تكون لديك فكرة واضحة عن المتطلبات التي يجب استيفائها وأيها يمكن التضحية بها إلى حد ما. للقيام بذلك، يجب عليك تنظيم قائمة متطلبات المستهلك وفقا لأهميتها. ونتيجة لذلك، يتم تقديم عمود آخر، والذي يشير إلى درجة أهمية كل من المتطلبات على مقياس من عشر نقاط.
المرحلة 3 - تطوير الخصائص الهندسية. يتم حل هذه المشكلة بواسطة فريق تطوير المنتج الذي يتم إنشاؤه. في هذه المرحلة، يجب عليها إعداد قائمة بالخصائص الهندسية للمنتج المستقبلي (نظرة على المنتج من وجهة نظر المهندس). وبطبيعة الحال، يجب أن تكون الخصائص محددة وواضحة بما فيه الكفاية، أي. موصوفة باللغة المعتمدة من قبل المطورين. ترد قائمة متطلبات المستهلك في المصفوفة 1 من "بيت الجودة" الموسع في الشكل. 2.16.
المرحلة 4 - حساب التبعيات بين متطلبات المستهلك والخصائص الهندسية. ونتيجة للمراحل السابقة، حصل المصممون على قائمة مرتبة لمتطلبات المستهلك، مجمعة بلغة المستهلك، والخصائص الهندسية، مصاغة بلغة المطورين.
في التحليل، تكفي المفاهيم الغامضة مثل "الاقتران القوي" و"الاقتران المتوسط" و"الاقتران الضعيف". لأنواع مختلفة من الاتصالات نستخدم الرموز الموضحة في الشكل. 2.16. في هذه الحالة سنفترض أن الاتصال القوي يساوي عدديا 9، والاتصال المتوسط 3، والاتصال الضعيف 1. وستكون هذه الأرقام مفيدة في المستقبل لحساب قيم الخصائص الهندسية.
بعد ذلك، عليك أن تقرر ما إذا كنت ستترك في المنتج المصمم تلك الخصائص الهندسية التي لا يحتاجها المستهلك. بعض الخصائص، حتى لو لم يكن المستهلك بحاجة إليها، قد تكون ضرورية للتشغيل الطبيعي للمنتج - في هذه الحالة، المطحنة. ولذلك، يجب الاحتفاظ بعدد من خصائص المنتج التي لا قيمة لها للمستهلك، ولكنها في نفس الوقت مهمة لعمله.
المرحلة الخامسة - بناء سقف "بيت الجودة". قد تكون الخصائص الهندسية متعددة الاتجاهات، مما يعني أنها قد لا تكون مترابطة أو متناقضة مع بعضها البعض. على سبيل المثال، لا ترتبط "مدة خدمة الضمان" المميزة بـ "التصميم" المميز. يتم الإشارة إلى الخصائص التي لا ترتبط مع بعضها البعض بعلامة "ناقص"، وتلك المرتبطة بعلامة "زائد". يجب أن يؤخذ هذا الاعتماد في الاعتبار عند تحسين النظام بأكمله. تحدد هذه الخصائص الطريقة والظروف والأنماط التي يجب أن تتم بها عملية الإنتاج من أجل الحصول في النهاية على المنتجات التي تلبي متطلبات المستهلك على أفضل وجه. لتطوير المنتجات الناجحة، ومتطلبات العملاء

أرز. 2.1 فولت. "بيت الجودة" للمنتج "المطحنة" يجب أن يترجم إلى خصائص هندسية تظهر على شكل خصائص (أهداف) للمنتج وتظهر في أعلى بيت الجودة (انظر الشكل 2.16) .
من الضروري الإجابة على السؤال، إلى أي مدى ترتبط متطلبات المستهلك بالخصائص المقبولة للمنتج؟ لنأخذ، على سبيل المثال، متطلبات مستهلك المطحنة - "تعدد استخدامات" المنتج. وهي مترابطة بخصائص مثل "كمية المواد المعالجة" و"عدد أوضاع التشغيل" و"مدة خدمة الضمان" و"سهولة الاستخدام". هذه المتطلبات المميزة للاتصالات تختلف في القوة.
سقف "بيت الجودة"عبارة عن مصفوفة ارتباط مليئة بالرموز التي تشير إلى وجود علاقة إيجابية أو سلبية بين الخصائص التقنية ذات الصلة بالمنتج من منظور اهتمامات المستهلك. باستخدام مصفوفة الارتباط 4 (انظر الشكل 2.15)، يمكنك توضيح العلاقة بين المؤشرات الرئيسية للجودة والتكلفة والوقت (انظر الشكل 2.16).
المرحلة السادسة - تحديد القيم الوزنية للخصائص الهندسية مع مراعاة تصنيف متطلبات المستهلك وكذلك العلاقة بين متطلبات المستهلك والخصائص الهندسية. وبضرب الوزن النسبي لمتطلبات المستهلك (التصنيف) في المؤشر العددي للعلاقة بين متطلبات المستهلك والخصائص الهندسية، المحدد في المرحلة الرابعة، نحصل على الأهمية التكاملية لكل خاصية هندسية. من خلال جمع النتائج عبر العمود بأكمله من الخاصية الهندسية المقابلة، نحصل على قيمة الهدف. وينبغي إيلاء الاهتمام الأساسي للخاصية الهندسية ذات القيمة الموضوعية الأعلى. في هذا المثال، هذه الخاصية الهندسية هي عدد أوضاع التشغيل (انظر الشكل 2.16).
المرحلة 7 - مع مراعاة القيود الفنية. ليست كل قيم الأداء الهندسي قابلة للتحقيق. تنشأ بعض الصعوبات التسويقية أو الإنتاجية أو الاقتصادية في طريق دعمهم العملي. لذلك، في السطر التالي من المصفوفة، تتم الإشارة إلى تقييمات الخبراء لصعوبة توفير قيم الخصائص الهندسية التي يطلبها المستهلكون بشكل أكبر. مع أخذ ذلك في الاعتبار، نحدد مدى صعوبة تحقيق الأهداف المحددة (انظر الشكل 2.16).

أرز. 2.17.
المرحلة 8 - مع مراعاة تأثير المنافسين. ومن الواضح أن هناك منافسة في السوق الحقيقية ويمكن أن تكون درجة المنافسة كبيرة. من خلال تقييم المواقف التنافسية لمؤسستك والمؤسسات المنافسة، يمكنك تحديد أولئك الذين يشكلون أكبر تهديد. يعد تحليل القوى التنافسية وفقًا لـ M. Porter مفيدًا، مما يسمح لك بتقييم قوة الرد المضاد من البيئة الخارجية بشكل واقعي. يتيح لك تصنيف المنافسين تحديد حدود تقييم المنافسين، مما يبسط مهمة الحصول على المعلومات. يتم التقييم التنافسي من موقعين: تقييم قدرة المنافسين على تلبية متطلبات المستهلك (أولوية للمستهلك) وتقييم قدرة المنافسين على تحقيق الأهداف الفنية والاستهلاكية التي حددتها المؤسسة (أولوية للشركة المصنعة) ). لتصور الوضع مع المنافسين، عادة ما يستخدمون المخططات التي يتم وضعها على يمين وأسفل "بيت الجودة" (انظر الشكل 2.16).
ونتيجة لتنفيذ الإجراءات المذكورة أعلاه، يتم الحصول على البيانات الأولية للمواصفات الفنية لتصميم وتطوير المنتجات الجديدة. إن بناء مصفوفة SFC والحصول على الخصائص الهندسية ليس سوى المرحلة الأولى من أربع مراحل "لتوزيع" متطلبات المستهلك ليس فقط في الخصائص الهندسية، ولكن أيضًا في مؤشرات العملية والإنتاج بأكمله. يظهر هيكل مراحل SFC في الشكل. 2.17.
المرحلة 1 - تخطيط المنتج. تمت مناقشة هذه العملية بالتفصيل أعلاه. في هذه المرحلة، تقوم الشركة المصنعة بتحديد وتوضيح متطلبات المستهلك. ونتيجة لبناء المصفوفة الأولى يتم الحصول على القيم الدقيقة للخصائص الهندسية، أي. أهداف الشركة المصنعة.
المرحلة الثانية - تخطيط مكونات المنتج. وكجزء من هذه المرحلة، يتم تحديد أهم مكونات المنتج الذي سيتم إنشاؤه، والتي تضمن تنفيذ الخصائص الهندسية التي تم تحديدها نتيجة بناء المصفوفة الأولى. في هذه الحالة، تعتبر قيم معينة من الخصائص الهندسية "مدخلات" (متطلبات) عند إنشاء المصفوفة الثانية (في المصفوفة الأولى كانت هذه "المدخلات" هي متطلبات المستهلك). تتأثر جودة تخطيط مكونات المنتج بشكل كبير بالتصميم المفاهيمي.
التطور المفاهيمييعتمد المنتج على الاتجاهات الرئيسية في تطوير الإنتاج الحديث. في هذه الحالة، من الضروري العثور على إجابات لعدد من الأسئلة الرئيسية التي تحددها حالة البيئة الخارجية والداخلية للمؤسسة. وترد أهمها في الجدول. 2.1.
القضايا الرئيسية في خلق منتجات جديدة
الأسئلة الرئيسية |
|
1. هل العوامل الداخلية للمؤسسة تتوافق استراتيجيا مع متطلبات "الاقتصاد الجديد"؟ نموذج "المؤسسة. كما هو؟" |
متطلبات المنتج:
|
2. هل تعرف ما هي المنتجات التي يريدها المستهلكون منك؟ نموذج "المنتجات. كيف ينبغي أن يكون مثل؟ |
تحديد متطلبات العملاء وتوقعاتهم:
تطوير نماذج المنتج لتحديد المواقع:
تكنولوجيا تجزئة المستهلك:
|
الأسئلة الرئيسية |
القضايا الرئيسية التي يتعين معالجتها |
تحديد مواقع السلع (الخدمات):
|
|
3. كيف يجب أن تكون المؤسسة لتلبية المتطلبات الخارجية؟ نموذج "المؤسسة. كيف ينبغي أن يكون مثل؟ |
|
4. ما الذي يجب فعله لضمان تلبية المؤسسة لمتطلبات البيئة الخارجية؟ استراتيجية التنمية: من نموذج "كما هو؟" إلى النموذج "كيف ينبغي أن يكون؟" |
تخطيط استراتيجي:
تنفيذ الاستراتيجيات:
|
الأسئلة الرئيسية |
القضايا الرئيسية التي يتعين معالجتها |
5. كيف ينبغي أن تتصرف المؤسسة في بيئة تنافسية قاسية؟ الإستراتيجية التنافسية: ما الذي يجب على المنشأة فعله لتعزيز مركزها التنافسي؟ |
|
يمكن إجراء التطوير الفعال لوثائق التصميم على مستوى مكونات المنتج باستخدام نظام التصميم المتكامل بمساعدة الكمبيوتر (CAD)، والذي يظهر الرسم التخطيطي العام له في الشكل. 2.18. ومن الناحية العملية، يتم استخدام نماذج تصميم المنتجات بشكل متزايد، مع التحول التدريجي بعيدًا عن التصميم المسطح.
تتضمن النمذجة تطوير نموذج رياضي للرسم في شكل أنظمة المعادلات. من الصعب القيام بهذا العمل يدويًا. لذلك، كان من الضروري تطوير أنظمة برمجية معقدة - المعلمات، والتي كان من الممكن إنشاء مثل هذه النماذج الرياضية. حاليًا، تشكل النوى البارامترية الأساس للعديد من SKPs. من خلال تحديد نوع النموذج (المشار إليه فيما بعد بنوع الجزء أو المنتج) وتعيين معلماته، يمكنك بسهولة الحصول على الرسومات المقابلة. هكذا ظهرت الرسومات البارامترية، أولاً مسطحة (ثنائية الأبعاد - 2D)،ثم الحجمي (ثلاثي الأبعاد - 3D).الميزة الكبيرة للنماذج البارامترية هي إمكانية النمذجة الحاسوبية بناءً عليها، عندما يتم إنشاء عائلات نماذج من نفس نوع المنتج أو الجزء ويتم تحديد الخيار الأفضل من خلال التحسين.
المرحلة 3 - تصميم العملية. في هذه المرحلة، يتم تحويل خصائص (معلمات الجودة) للمنتج المصمم إلى عمليات تكنولوجية محددة تضمن إنتاج منتج بخصائص محددة. في هذه المرحلة، يتم تحديد المعالم الرئيسية لكل عملية واختيار طرق التحكم بها. أثناء تطوير العملية التكنولوجية لتصنيع المنتج، يجب تحديد نظام التحكم في العملية وتوفير طرق لتحسين العملية بشكل أكبر.

أرز. 2.18.
اختيار المعدات الآلي
يركز الإنتاج الحديث على استخدام SKP، والذي، بالإضافة إلى حل مشاكل تطوير المنتج، يحل بشكل شامل مشاكل إعداد الوثائق التكنولوجية. كما يظهر في الشكل. 2.19، الخيار الأفضل هو SKP المعقد، حيث العنصر الأول هو نظام التصميم، ويتم نقل مخرجاته تلقائيًا إلى النظام التكنولوجي. كيف يتم تجميع حزمة البرامج هذه في شكل UPC تحت علامة تجارية؟ تي فليكسيظهر في الشكل. 2.19. يسمح لك بأتمتة كل من التصميم والعمل التكنولوجي. يوفر المجمع الفرصة للحصول على الوثائق التكنولوجية المتعلقة بالتصنيع والتجميع والختم وإنتاج الأجزاء البلاستيكية. العمل الآلي على إعداد برامج التحكم لماكينات CNC مع التصور الرسومي شبه

أرز. 2.19. هيكل مجمع أتمتة التصميم تي فليكس
النتائج المحسوبة على أساس برامج الوسائط المتعددة. يجب أن تدرك أن استخدام هذه الأنظمة لا يؤدي فقط إلى زيادة حادة في الإنتاجية عند أداء العمل المعقد، ولكن أيضًا إلى زيادة كبيرة في جودتها. وفقا للمعهد الدولي للمعايير والتكنولوجيا (المعهد الوطني للمعايير والتكنولوجيا)يتيح لك استخدام التصميم المتوازي من طرف إلى طرف تحقيق النتائج التالية:
- وإجراء التغييرات بشكل أسرع بنسبة 65-90%؛
- وقت التطوير أقل بنسبة 30-70%؛
- دخول المنتج إلى السوق بشكل أسرع بنسبة 20-90%؛
- جودة المنتج أعلى بنسبة 200-600%؛
- التكاليف أقل بنسبة 5-50%؛
- الاسترداد أسرع بنسبة 20-120٪.
المرحلة الرابعة - تصميم الإنتاج. تتضمن هذه المرحلة تطوير تعليمات الإنتاج واختيار أدوات مراقبة الجودة لإنتاج المنتج، بحيث يكون لدى كل مشغل فهم واضح لما يجب التحكم فيه وكيف يجب التحكم فيه أثناء العملية. ويجب أن تنص التعليمات أيضًا على إمكانية تحسين عمل المشغل، اعتمادًا على عدد القياسات وعدد المرات التي ينبغي إجراؤها، وأدوات القياس التي ينبغي استخدامها. يعتمد نجاح تصميم الإنتاج على مدى نجاح إدارة الشركة ومدى مراعاة الاتجاهات الحديثة في تطوير الإنتاج. يجب على الإدارة العليا التأكد من أن حالة البيئة الداخلية للمؤسسة تتوافق مع اتجاهات وطبيعة تطور البيئة الخارجية. يتم تحديد "حكمة" إدارة الشركات من خلال قدرتها على توقع التغييرات المستقبلية من أجل الاستعداد لصد الهجمات غير المواتية من البيئة الخارجية أو الاستخدام الفعال للظروف المواتية المتوفرة. وبالتالي، فإن تركيز الاقتصاد الوطني الروسي على التطوير المبتكر للإنتاج الصناعي سيقلل من اعتماده على حالة قطاع المواد الخام.
إن وجهات النظر حول بناء آلية اقتصادية وهياكل الإدارة التنظيمية وإضفاء الطابع الديمقراطي على الإدارة تتغير بشكل جذري. وهكذا، في اليابان، يتم لفت الانتباه إلى الجودة العالية للمنتجات وتكلفتها المنخفضة. وبطبيعة الحال، يطرح السؤال: "كيف تم ذلك؟" . الإجابة: المحرك عبارة عن نظامين مستقلين إلى حد ما - نظام شامل لإدارة جودة المنتج ونظام تكلفة الإنتاج يعتمد على أفضل تنظيم له. لقد تم تسليط الضوء أعلاه على أساليب إدارة الجودة في اليابان. ولذلك، سوف نركز فقط على النظام الثاني. ومن الناحية الاستراتيجية، يركز تنظيم الإنتاج في الصناعة اليابانية على تنفيذ فكرة “القضاء على كل ما هو غير ضروري” في الإنتاج. يتم تفسير مفهوم "إضافي" على نطاق واسع. تشمل هذه الفئة كل ما لا يدر دخلاً. ينطلق المديرون اليابانيون من حقيقة أنه ليس أولئك الذين يكسبون الكثير هم من يصبحون أثرياء، ولكن أولئك الذين ينفقون القليل. لقد ركزوا جهودهم على القضاء على جميع الأنشطة التي يمكن للمؤسسة القيام بها دون الإضرار بالأعمال. في حل هذه المشكلة، قاموا باستمرار بدراسة أسباب التجاوزات المختلفة في عملية الإنتاج وتطوير طرق للقضاء عليها. وتعتمد هذه الأساليب المفاهيمية الرئيسية بدورها على النقاط الأربع التالية.
أولاً،بشأن التشكيل الإلزامي في نظام الإنتاج لوحدات إنتاج مستقلة ومستقلة بدرجة كافية SHE (وحدة اقتصادية مستقلة).
ثانيًا،على الأداء غير المشروط لكل وحدة من وظائفها الإنتاجية بدقة وفي الوقت المحدد.
ثالث،بشأن الاستخدام المرن للعمالة.
رابعا،على الإدخال المستمر للأفكار الإبداعية والمبتكرة في الإنتاج.
بشكل عام، تسمح طريقة SFC ليس فقط بإضفاء الطابع الرسمي على الإجراء الخاص بتحديد الخصائص الرئيسية للمنتج قيد التطوير، مع مراعاة رغبات المستهلك، ولكن أيضًا لاتخاذ قرارات مستنيرة بشأن إدارة جودة عمليات إنشائه. وبالتالي، من خلال "نشر" الجودة في المراحل الأولية من دورة حياة المنتج وفقًا لاحتياجات ورغبات المستهلك، من الممكن تجنب تعديلات معايير المنتج بعد ظهوره في السوق (أو على الأقل تقليل إلى الحد الأدنى)، وبالتالي توفير قيمة عالية وفي نفس الوقت تكلفة منخفضة نسبيًا للمنتج (عن طريق تقليل التكاليف غير الإنتاجية).
مميزات إدارة الجودة المبنية على النموذج إدارة الجودة الشاملةهو التركيز المستمر على التحسين المستمر. لذلك، يفترض هيكل وظيفة الجودة أنه بعد تصميم الإنتاج، يتم تطوير التدابير لتحسين العمليات، والتي تبدأ بالتخطيط (الشكل 2.20).

عند اختيار مستحضرات التجميل أو المكملات الغذائية، التي أصبحت شائعة جدًا مؤخرًا، يسترشد معظم المستهلكين بمعايير مثل فعاليتها وسلامتها. ولهذا السبب تعتبر مراقبة الجودة الداخلية لمنتجاتنا جانبًا أساسيًا من عملية الإنتاج.
الميزة التنافسية لشركة KorolevPharm هي القدرة على تقديم مجموعة واسعة من الخدمات عالية الجودة، بدءًا من تطوير الوصفة وحتى إصدار المنتجات النهائية، والتي تكون مصحوبة بالضرورة بالوثائق المناسبة ويتم إنتاجها في حاوية مناسبة عميل. وفي الوقت نفسه، توجد في كل مرحلة من مراحل الإنتاج معايير صارمة لمراقبة الجودة. ولهذا السبب حظيت منتجاتنا باستمرار بشعبية كبيرة لسنوات عديدة وحصلت على اعتراف وجوائز دولية، بما في ذلك علامة "الشهادة الذهبية للجودة" المميزة، والتي تعد أفضل تأكيد على أن شركتنا رائدة معترف بها في هذا المجال.
المكملات الغذائية للأغذية وكذلك مستحضرات التجميل لها تأثير مباشر على صحة الإنسان. تدرك شركة KorolevPharm تمامًا مسؤوليتها تجاه منتجاتها، وبالتالي فهي تمتثل تمامًا لجميع متطلبات مراقبة الجودة الدولية والمحلية. من أجل إجراء مراقبة جودة الصيدلة الداخلية مباشرة في المؤسسة، تم افتتاح مختبر حصل على اعتماد الدولة. وهي مجهزة بأجهزة الكمبيوتر الحديثة وأحدث جيل.
تتيح لنا مراقبة الجودة في المختبر إجراء الاختبارات السريرية اللازمة لإنتاج منتجات مفيدة وفعالة وآمنة. هنا، يتم فحص جميع المكونات التي تعتمد عليها جودة المنتج النهائي، بدءًا من عينات الهواء والماء والمواد الخام وحتى المنتج النهائي. يعد هذا ضمانًا موثوقًا بأن منتجاتنا تتوافق بالضرورة مع جميع المعايير الميكروبيولوجية والفيزيائية والكيميائية، مما يعني أنها ليست آمنة للاستهلاك فحسب، ولكنها ستحقق أيضًا التأثير المعلن.
مراحل مراقبة الجودة في كل مرحلة من مراحل الإنتاج
إن عملية الإنتاج بأكملها التي نقوم بها تمر بالضرورة بمراحل مختلفة من مراقبة الجودة. علاوة على ذلك، فهذه ليست مراقبة انتقائية للجودة، ولكنها إشراف صارم على جميع مراحل أنشطتنا. يتم تطبيق جميع معايير مراقبة الجودة المعتمدة من خلال الوثائق التنظيمية والمعايير الحالية في المقام الأول على قبول المواد الخام، والتي يجب أن تمتثل لها بشكل صارم. فقط بعد ذلك يحصل على حالة "الحجر الصحي". وفي هذه المرحلة، تخضع المواد الخام الناتجة لجميع الاختبارات المعملية اللازمة، وإذا أكدت التجارب السريرية استيفاء جميع متطلبات مراقبة الجودة، ففي هذه الحالة فقط تحصل على الموافقة للاستخدام لأغراض الإنتاج.
لا يتم تنفيذ مراقبة جودة المختبرات الداخلية الصارمة في مؤسستنا على المواد المساعدة ومواد التعبئة والتغليف الموردة. يتم تطوير المواصفات المخصصة بشكل ثنائي ومراقبتها من قبل مهندسي الجودة. وبناءً على ذلك، يُسمح بإنتاج المواد الآمنة فقط، مما يلغي تمامًا أي تأثير سلبي محتمل على جودة المنتج النهائي، والذي يتم إنتاجه فقط إذا كانت جميع المؤشرات الرئيسية متوافقة مع المعايير والقواعد المطلوبة.
يقوم فريق من المحترفين من شركة KorolevPharm بتنفيذ رقابة صارمة على جودة منتجاتها داخل الصيدلية، والتي تتوافق تمامًا مع العينة المرجعية في جميع المؤشرات الميكروبيولوجية والفيزيائية والكيميائية والحسية. ولهذا السبب لم تفقد مكانتها الرائدة لسنوات عديدة وتتمتع بالاعتراف والطلب المستحق بين المستهلكين.